Abstract
The authors report effects of placing a very thin metallic interlayer, such as W and Ni, in between the Cu film and the Si substrate on cyclic thermal stress-induced interfacial sliding and hillock growth in Cu. Cu-Si samples with no interlayer were the most prone to both interfacial sliding and hillock growth, whereas samples with the Ni interlayer were the most resistant against these deleterious phenomena. While the rate of interfacial sliding decreased with each consecutive thermal cycle, hillocks continued to grow undeterred. The obtained experimental results are discussed, considering the compressive stress field generated in the Cu film.
Similar content being viewed by others
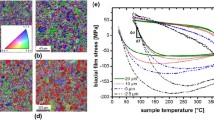
Explore related subjects
Discover the latest articles, news and stories from top researchers in related subjects.Avoid common mistakes on your manuscript.
Introduction
The mechanical integrity of “thin metallic film–elastic substrate” systems, such as the Cu–Si system, is critical for determining short- and long-term reliability of a myriad of devices, such as micro- and nano-electro-mechanical systems, and device-level interconnects in microelectronic devices. Much of the mechanical reliability issues that arise during the fabrication and the operation of these devices are attributed to the thermal stresses, which are generated due to the mismatch in the coefficients of thermal expansion (CTE) of the adjoining components, such as the Si substrate, low-k dielectric, and metallic film.[1,2] In addition, thermal excursions also lead to the generation of large shear stresses, especially near the edges of thin films, and significant stress gradients in the film, which in tandem with very large thermal stresses can lead to device failures via creep, interfacial sliding, interfacial debonding, voiding, and whiskering.[3–9]
In particular, interfacial sliding is a stress-directed diffusion-controlled phenomenon, which does not involve breaking of bonds and leads to stress relaxation in the system. Interfacial sliding between two adjoining components leads to dimensional incompatibility due to differential straining of the components, which may result in a malfunction of the device. Hence, interfacial sliding is a major reliability issue, which is getting exacerbated with a rapid increase in the fraction of hetero-interfaces in ever-shrinking microelectronic devices. Although mechanical stress-driven interfacial sliding between a metal thin film and the Si substrate is widely studied,[10–14] there is a scarcity of studies devoted to understanding the role of thermal excursions on interfacial sliding and stress relaxation in thin film systems. Notably, Chen and Dutta[10] studied interfacial sliding-assisted plastic deformation in the patterned Al thin films deposited on the Si substrate during thermal cycling by measuring the change in the width of the films using an atomic force microscope (AFM). The authors proposed that large shear stresses were developed at the extremities of the sample during thermal cycling, which were subsequently relaxed via interfacial sliding.[10] Since the kinetics of the interfacial sliding is governed by diffusion,[12,14] which is faster at higher temperatures, the interfacial sliding during the heating segment of the thermal cycle could not be fully recovered during the cooling segment.[10] This resulted in a residual interfacial sliding, which could be determined by measuring the finite change in the width of the Al film.
Another mechanism for stress relaxation in thin films can be hillock formation, which is identified as a wide-filament type of material growth. Hillock formation (and whiskering) in Al films deposited on Si, Sn coatings on Cu or brass, etc. are widely reported.[15–18] Alike interfacial sliding, hillock formation is also a stress-directed diffusion-controlled phenomenon that leads to stress relaxation in the metal film. Hillock growth may lead to short-circuiting, and hence, it is also a major long-term reliability issue associated with microelectronic devices. Interestingly, interfacial sliding and hillock formation in the Cu–Si system, which is widely used in microelectronic devices, due to the cyclic thermal stresses have not been satisfactorily explored; these form the central goals of this study.
One possible conduit for the dominant mass transport, required for both interfacial sliding and hillocking, in metal–Si systems can be the hetero-interfacial region formed at the interface of the metal film and the substrate.[19–21] This is because such hetero-interfaces are often more “open” as compared to the lattice or grain boundaries and hence they provide the least resistive path for atoms or vacancies to migrate. Now, since the interfacial region in the metal–Si system can be easily manipulated with the addition of an interlayer between the metal film and the substrate, it is imperative to study the effect of the interlayer on thermal excursion induced mass transport, resulting in interfacial sliding, hillocking, and whis-kering in the Cu–Si system. Accordingly, we have studied the effect of the chemistry of the interlayer placed in between Cu and Si on the overall interfacial sliding as well as hillock formation during thermal cycling. We demonstrate that the interlayer dramatically affects these two phenomena, such that it is always advantageous to place a metallic interlayer and, moreover, an optimum interlayer, such as Ni, can greatly diminish the propensity of the occurrence of the both of these deleterious phenomena. It should be noted that an interlayer is always placed in between the metal film and the substrate for a myriad of reasons, such as adhesion, diffusion barrier, and reaction barrier. Our work, now, adds an additional purpose for placing the interlayer, as it also determines the overall mass transport through the interfacial region in the Cu film and hence affects the stress relaxation mechanisms of hillocking and interfacial sliding during thermal excursion.
Procedures for experiments and finite element analysis
Experimental procedure
In this study, Cu thin films were deposited on the Si substrate with the following three types of interlayers: Ni, W, and no interlayer. These choices of interlayers were made because, as revealed by the respective binary phase diagrams,[22] one can expect widely different interactions between the selected interlayer and the metal film in these three systems. For example, the interaction between Ni and Cu is of an unlimited solid solution type, while several compounds form in between Cu and Si. On the other hand, W and Cu show insignificant interaction,[22] with little mutual solid solubility and no stable intermetallic compound.[23] Therefore, selecting these three different interlayer–metal film systems allowed the nature of the interface between the interlayer and the Cu film to vary the widest and hence understanding the effect of the interlayer on the stress relaxation during thermal cycling could be easier.
As shown in Fig. 1, small square islands of Cu films were deposited on the (100)-oriented Si substrate (with or without any interlayer). Firstly, the Si substrate was cleaned with piranha solution using the standard protocol. Subsequently, a 25 nm thick film of either W or Ni was deposited on the entire Si substrate using direct current (DC) magnetron sputtering. After depositing W or Ni blanket thin films, a square island pattern on the substrate was created using photolithography. Since the work involved studying the effect of the metallic interlayer on the interfacial sliding, leaving any residue of the polymer photoresist on the substrate following the photolithography process was considered as a major contamination. Therefore, the plasma descumming process was used for removing the photoresist residue from the patterned region. After descumming, the 100 nm thick Cu film was deposited using DC magnetron sputtering on the patterned substrate. A scanning electron micrograph of the Cu islands is shown in Fig. 1(b). After the deposition of the Cu film, the square islands were scanned using an AFM.
(a) A schematic illustration of the Cu square islands deposited on the Si substrate with various types of interlayers: (i) no interlayer, (ii) Ni, and (iii) W. (b) A micrograph showing the top view of the Cu–Si sample, comprising Cu islands, at the end of the sample fabrication procedure. (c) Geometry, along with the boundary conditions, of a Cu island and the Si substrate prepared to obtain the stress field in the sample during thermal cycling using finite element analysis (FEA), and (d) the thermal cycle profile imposed as a boundary condition in the FEA study.
Fabricated samples were vacuum sealed in a borosilicate glass tube with better than 10−3 Pa vacuum. Subsequently, the vacuum-sealed samples were thermally cycled, by placing the glass tubes in an environmental chamber, in between −50 and 150 °C with a constant heating and cooling rate of 1 K/min and a 10 min dwell at both the minimum and the maximum temperatures. Following a thermal excursion, the topography of each Cu island was again measured using an AFM. The obtained topography was compared with the same island before the previous stage of the thermal cycling to ascertain the effect of thermal cycling on the dimensional changes of Cu islands and hence sliding at the interface of the Cu islands. The interfacial sliding was measured as the difference in the width of the film before and after the thermal cycling, i.e., Δw.
Procedure for FEA
FEA was performed using ANSYS®, a commercial software package, for evaluating the role of stress in the interfacial sliding and the hillock growth in the Cu–Si system when subjected to thermal cyclic loading. A 3D geometry of the Cu–Si system without an interlayer, as shown in Fig. 1(c), was prepared and discretized using 10-node tetrahedral elements (Solid 187 in ANSYS® terminology) that are suitable for a thermomechanical analysis. As shown in Fig. 1(c), only one-fourth of the entire island sample was modeled in FEA due to the prevalent symmetry of the problem. While keeping the size of the Si substrate the same, the following two different size Cu islands were modeled to assess the effects of the island size on the stress distribution in the Cu films during thermal cycling: (i) 6×6 and (ii) 3×3 μm2. The thicknesses of the Cu film and Si substrate were 100 nm and 100 μm, respectively, to mimic the dimensions of the samples used in the experiments. Since the goal of this FEA study was to obtain only qualitative insights into the stress distribution in the Cu film during thermal cycling, temperature insensitive bulk material properties were taken for both the Cu film and Si substrate, and the Cu–Si interface was assumed to be perfectly bonded (i.e., interfacial sliding was not allowed). The Si substrate was modeled as an elastic material with an isotropic Young’s modulus of 180 GPa, while the Cu film was modeled as a bilinear elastic-plastic material having Young’s modulus of 124 GPa, yield strength of 70 MPa and a tangent modulus of 125 MPa. Poisson’s ratio of Cu was taken as 0.34 and for Si as 0.18. Thermal expansion coefficients of Si and Cu were taken as 2.6 and 17 ppm/K, respectively. Thermal loading was applied on all the nodes in the form of a temperature cycle, as shown in Fig. 1(d) and as used in the experiments. The simulation was run using a transient solver, and the stress profiles were plotted along various paths at the maximum temperature during the thermal cycle, i.e., 150 °C, to understand the most severe condition. It should be noted that the effect of the interlayer on the stress–strain distribution was not determined using FEA, and it is assumed that placing an interlayer would qualitatively not affect the stress distribution in the Cu film. This assumption is reasonable as the thickness of the interlayers was much smaller as compared to the thickness of the Si substrate (as well as the Cu thin film), and hence, it is not expected that the interlayer, which is strongly bonded to Si, will affect the qualitative description of the stress field in Cu during thermal cycling.
Results and discussion
Interfacial sliding
Figure 2 shows the effect of thermal cycling on the topography of the Cu islands deposited directly on the Si substrate. A comparison of Figs. 2(a) and 2(b) reveals that the shape of the sample remained unchanged during thermal cycling. However, careful observation of Fig. 2(c) clearly reveals that the footprint of the Cu island along a fixed median changed after three thermal cycles. As a matter of fact, the Cu island shrank by 250 ±25 nm after three cycles. This shrinkage of the Cu film occurred without any other damage to the film, such as debonding and cavitation. Interestingly, the thickness of the film also increased slightly (≈3 nm) after thermal cycling, which can be attributed to the accommodation required for the mass conservation. Furthermore, Fig. 2(c) also reveals that the differential change in the dimension of the Cu island occurred without any significant change in the profile of its vertical face. Finally, as shown in Fig. 2(d), the overall change in the width of the Cu island, Δw, increased with the number of thermal cycles. However, the rate of change of Δw decreased quite dramatically beyond the first a few thermal cycles, finally showing a saturation. This observation of rapid change in Δw during the first a few thermal cycles, followed by subsequent saturation can be attributed to saturation in the built-up of the maximum residual stress during a thermal cycle. Such a behavior has also been observed in the studies that discuss interfacial sliding between the Al film and the Si substrate.[10]
AFM scan showing the topography of a Cu island deposited directly on Si (i.e., without an interlayer): (a) before and (b) after three thermal cycles between −50 and 150 °C. (c) Representative line profiles along one of the medians of one of Cu–Si islands before and after three thermal cycles. The selected median is shown by a broken line in (a) and (b). The two graphs in the inset show the zoomed view of the edges of the Cu film. (d) Variation in the extent of interfacial sliding, measured in terms of change in the width of Cu island (Δw), as a function of the number of thermal cycles for Cu–Si samples comprising various types of interlayers. FEA results showing the variation of (e) σyy and (f) plastic εyy in the Cu film at 150 °C as a function of the distance from the interface, z. The distance, y =3 μm, represents one of the vertical surfaces of the Cu film.
Quite interestingly, Fig. 2(d) also reveals that Δw was significantly altered by changing the interlayer placed in between the Cu film and the Si substrate. Placing metallic interlayers resulted in a better performance against residual differential strain or footprint shift as compared to the case of no interlayer. Moreover, placing Ni between Cu and Si, which forms a strong bond with Cu, made the Cu film slightly more resistant against dimensional changes as compared to the W interlayer, which does not interact very strongly with Cu.[22,23] In summary, Fig. 2 reveals that the footprint of the Cu islands, which decreases with thermal cycling while maintaining the overall shape of the vertical face, can be altered by placing a very thin layer of a metal in between the Cu film and the Si substrate. This suggests interfacial sliding, which is a diffusion-driven phenomenon, as the mechanism responsible for the change in the footprint of Cu islands, resulting in the observed differential strain. This inference is further corroborated with the FEA , as described below.
Now, as shown in Fig. 2, since Cu islands contracted in all cases, the prevalence of compressive stress in Cu films at high temperatures during thermal cycling can be inferred. This is consistent with the stress profile at 150 °C, as shown in Fig. 2(e). It should be noted that, here, all discussions related to FEA results have been done with respect to the stress field established at 150 °C, which was the highest temperature during thermal cycling. At this temperature, not only the stresses were the highest but also the kinetics of the interfacial sliding (i.e., diffusion) would be the maximum. Hence, the highest temperature represents a case when the drive for the occurrence of the observed phenomenon of stress relaxation will be the highest. As shown in Fig. 2(e), irrespective of the distance from the outer corner of the Cu island [i.e., for an x at y = 3 μm in Fig. 1(c)], the normal stress on the vertical face of the Cu island [i.e., σyy for the coordinate system shown in Fig. 1(c)], especially near the Cu-Si interface, was highly compressive. Furthermore, the highest compressive stress was established at the Cu–Si interface and the stress decreased, albeit linearly, away from the interface toward the free surface of the Cu film becoming zero at about one-fifth of the thickness of the Cu film. This suggests that the highest driving force for the contraction of the island at the most conducive temperature during thermal cycling (i.e., at the highest temperature) was available at the interface of the Cu film and the Si substrate. However, as shown in Fig. 2(f), the (time independent) plastic strain in the Cu island would produce a kink (i.e., the change in the slope) in the vertical face of the Cu island. This is in contrast to the shape of the island experimentally observed in this study [see Fig. 2(c)], and hence, the role of plastic deformation in determining the final shape of the Cu island cannot be dominant. In such a scenario, an accommodation of the compressive strain (and subsequent stress relaxation) in the Cu film at the highest temperature by the interfacial sliding can be inferred as the most dominant mechanism responsible for the differential strains, as shown in Figs. 2(a)–2(d). Since the maximum compressive stress was generated near the Cu–Si interface, it will further make the interfacial sliding in the system more conducive. It should be noted that the stress state in the thin Cu film was tri-axial, with all stress components being compressive, and hence the εyy profile shown in Fig. 2(f) does not show a direct correlation to the profile of σyy shown in Fig. 2(e).
Since the maximum temperature during thermal cycling was very small (e.g., 150 °C, ~0.3 Tm, where Tm is the melting temperature of Cu), significant diffusion through the lattice of Cu can be ruled out. Moreover, diffusion through grain boundaries is expected to be sluggish at such low temperatures.[24] Hence, as mentioned earlier, hetero-interfaces may provide the fastest conduit for mass transport required for interfacial sliding, which, as mentioned earlier, is a diffusion-controlled phenomenon. Now, since the diffusivity through a hetero-interface often decreases with the adhesion strength between the adjoining components and it is known that Cu–Si adhesion is weaker than the adhesion between Cu and a metal (e.g., Ni and W), the diffusivity through the Cu/Si interface would be much faster than that through the Cu/Ni or Cu/W interface. This is consistent with the observation of a faster rate of interfacial sliding in the Cu/Si system as compared to Cu/W/Si and Cu/Ni/Si systems [see Fig. 2(d)]. Since the intermixing zone between Ni and Cu is very large (due to unlimited solid solubility of Cu in Ni and vice versa) as compared to Cu and W, the adhesion between Cu and Ni at the interface would be relatively stronger.[25] Such a difference between the adhesion at Cu–Ni and Cu–W hetero-interfaces may explain a slightly faster rate of interfacial sliding in the weakly bonded Cu/W/Si system as compared to the strongly bonded Cu/Ni/Si system. Therefore, placing a strongly interacting interlayer below a film may reduce the interfacial sliding and hence alleviate the related reliability concerns. It should be noted that the value of stress and stress gradient in the Cu film will change with the placement of an interlayer, and hence, the force driving the interfacial sliding may also change due to the placement of an interlayer. Nevertheless, as mentioned earlier, due to very small thickness of the interlayer, the qualitative description of the stress state inside the Cu film may not change significantly, and hence, the control of kinetics (i.e., interfacial diffusion) by placing an interlayer appears to be the dominant cause for the variations, as shown in Fig. 2(d).
Hillock growth
Figure 3 shows AFM images of a few representative Cu islands after a large number of thermal cycling. The surface of the Cu islands after 10 thermal cycles became significantly rougher, as the material started to protrude out at a few locations in the island. On the other hand, well-defined hillocks started to grow in the samples after 20 thermal cycles [see Figs. 3(b) and 3(c)]. Figure 3(d) reveals that the width and the height of the hillocks were approximately 1 μm and a few hundred nanometers, respectively. Interestingly, the grains of the Cu films deposited here were columnar with a width of a few tens of nanometers and a height of approximately 100 nm. Therefore, the hillock grew over several grains and attained a height significantly more than the thickness of the Cu film. Finally, Fig. 3(e) shows that the height of the tallest hillock in the Cu film continuously increased with the number of cycles. It should be noted that hillocking was not observed in samples with the metallic interlayer even after 50 thermal cycles, which was the maximum number of thermal cycles used in this work. As mentioned before, hillock and whisker formation has been reported in Al thin films on Si[15,16] and Sn coatings on Cu or brass[26]; however, there has been a scarcity of studies providing the direct evidence of hillock formation in Cu thin films deposited on the Si substrate under a thermal cycling condition. Hence, these results provide useful insights into the non-fracture-based stress relaxation mechanisms, such as interfacial sliding and hillock formation, operative in the commercially quite important Cu–Si system during thermal cycling.
Topography of various square Cu islands on the Si substrate after (a) 10 and (b) 20 thermal cycles. (c) High magnification SEM micrograph showing a Cu island with several hillocks after 20 thermal cycles. (d) Line profile of a hillock formed in a Cu island after 20 thermal cycles. (e) Variation in the height of the tallest hillock in a Cu island as a function of the number of thermal cycles. The islands shown in (a)–(c) are different; however, all of them were deposited simultaneously.
Since hillock (or whisker) formation is a stress relaxation mechanism that releases buildup of the compressive stresses by transporting atoms along the compressive stress gradient in the film,[15,18] observations of hillocks in Cu islands clearly suggest the generation of very high compressive stresses in the Cu film during thermal cycling. As mentioned before, large compressive stresses in Cu films will build up during the heating segment of the thermal cycling, as the CTE of Cu is significantly higher than that of Si. Interestingly, alike interfacial sliding, the mass transport responsible for hillock formation also occurs through diffusion, which is more likely to occur during the heating segment, near the highest temperature, of a thermal cycle. Therefore, the formation of hillocks and the shrinkage of Cu islands due to the interfacial sliding are mutually consistent. However, there is one fundamental difference between the stress profile needed for interfacial sliding and that needed for hillock formation: while an in-plane stress (i.e., σyy and σxy) is needed for interfacial sliding, a gradient in the out-of-plane stress (i.e., σzz) is needed for hillock formation. Quite interestingly, as shown in Fig. 4(a), an out-of-plane stress gradient was readily established in the Cu film during thermal cycling, wherein the material near the Cu–Si interface was at the maximum compressive stress and the top (traction free) surface was stress free. Therefore, a chemical potential for driving mass transport from the bottom of the thin Cu film toward its free surface could be readily established, resulting in the growth of hillocks in these films.
FEA results showing the variation of σzzat 150 °C as a function of distance away from the interface between Si and Cu at (a) the edge and (b) a location away from the edge toward the central region of the Cu island. Here, y =3 and 1.5 μm represent the distance from the center of the 6 × 6 μm2 Cu island. FEA results showing the variation of (c) σyy and (d) σzz at 150 °C as afunction of distance away from the interface between Si and Cu at the edge of Cu islands having 6 × 6 and 3 × 3 μm2 sizes. High-resolution transmission electron micrographs showing the interfacial region formed between Cu and Si: (e) in the as-deposited sample and (f) after 20 thermal cycles between −25 and 135 °C.
A high magnification micrograph of one of Cu islands is shown in Fig. 3(c), which clearly shows the formation of cavities or pores primarily at the edges of the Cu island. This explains the mass balance: the material from the regions showing cavities or pores has been transported to form the hillocks. Careful observation of Fig. 3(c) also reveals that the central region of the Cu islands was generally free from the hillocks, which suggests that the out-of-plane stress gradient should be insignificant in the central region of Cu islands. This is reasonable as the thermal strain decreases as the distance from the neutral point, which would be at the center of the Cu island, decreases. The same is also revealed by the FEA, as shown in Fig. 4(b), which shows almost zero σzz in the Cu islands at locations sufficiently far away from the edges of the Cu islands.
It should be noted that the new material is added at the bottom of the hillock, and hence, a significantly faster interfacial diffusion will be needed for the rapid growth of hillocks, as observed in this study. As mentioned earlier in the context of interfacial sliding, hetero-interfaces are known to provide a faster conduit for interfacial diffusion, especially as diffusion through lattice and grain boundaries at the temperatures used in this study was low. This explains the observed dramatic effect of the interfacial material, placed in between the Cu film and the Si substrate, on the hillock formation.
Careful observation of Figs. 2 and 3 suggests that hillock formation became aggravated only after a large number of thermal cycles, by when interfacial sliding had saturated. Since the occurrence of interfacial sliding relaxes the compressive stress built-up in the Cu–Si thin film system during thermal cycling, hillock growth may be suppressed due to the stress relaxation caused by the interfacial sliding, which occurs most significantly only during the initial thermal cycles. Nevertheless, it is possible that interfacial sliding, which precedes hillock formation, enables hillock formation by both reducing the dimensions of the Cu island and damaging the interfacial layer formed between Cu and Si. As shown in Figs. 4(c) and 4(d), a decrease in the size of the Cu islands may lead to an increase in both the in-plane compressive stress and the out-of-plane compressive stress gradient in the Cu island at the highest temperatures; this may enhance the rate of hillock growth. Furthermore, it can be speculated that interfacial sliding will lead to the evolution of the interfacial layer; for example, interfacial sliding between Al and Si interfaces was shown to not only reduce the expanse of the amorphous interfacial region but also increase in the solute atom concentration in the amorphous region.[14] Similarly, as shown in Figs. 4(e) and 4(f), the structure of the interfacial layer formed between the Cu film and Si significantly evolved due to thermal cycling between −25 and 135 °C (which is slightly different than those used to obtain other results in this study). As shown in Figs. 4(e) and 4(f), the interfacial region became more crystalline following the thermal cycle. This may not only change the diffusivity through the interfacial region, which is an important parameter also for hillock growth but also change the out-of-plane stress near the Cu-Si interface, which may then also affect the hillock growth. Hence, the occurrence of interfacial sliding can be speculated to aid to hillock formation after a large number of thermal cycling.
The device-level interconnects in the next-generation microelectronic devices are densely packed with a distance of a few tens of nanometer between them. Hillocks of heights more than 1 μm can easily grow in 200 nm thick Cu films due to thermal cycling between −50 and 150 °C, which represents an accelerated test condition widely used to certify the reliability of the microelectronic packages. Such long hillocks can not only lead to short-circuiting of the device level interconnects but may also pose the significant structural integrity threat to the adjacent components in case of the embedded interconnects. Furthermore, interfacial sliding of thin film Cu interconnects will lead to dimensional incompatibility and result in an open circuit. However, a judicious selection of an interlayer placed in between the Cu film and the Si substrate may minimize the extent of both deleterious phenomena discussed here. Therefore, an ideal interlayer should not only be an excellent diffusion (and reaction) barrier and adhesion layer but also should minimize interfacial diffusion for controlling the phenomena of the interfacial sliding and the hillock growth.
Summary
After a few thermal cycles between −50 and 150 °C, the Cu islands deposited on the Si substrate shrunk, without significant changes in the shape and the height of the sample. Interfacial debonding was not observed; however, the surface roughness of the Cu films increased after thermal cycling. The extent of the interfacial sliding was maximum in the Cu/Si sample and minimum in the Cu/Ni/Si sample.
Hillocks formed in Cu films deposited directly on the Si substrate after several thermal cycles. However, they did not form in Cu films deposited with W or Ni as an interlayer. The height of the tallest hillock in a Cu island continuously increased with the number of thermal cycles, without showing any saturation.
FEA revealed the establishment of a compressive stress in the Cu film, with maximum compressive in-plane stress near the Cu–Si interface, and an out-of-plane compressive stress gradient. While the in-plane compressive stress drives the interfacial sliding, the out-of-plane compressive stress gradient is responsible for hillock growth. The severity of the compressive stress and stress gradient increases with a decrease in the width of the Cu islands.
References
Z. Suo: Reliability of interconnect structures. In Volume 8: Interfacial and Nanoscale Failure, Comprehensive Structural Integrity (I. Milne, R.O. Ritchie and B. Karihaloo, Editors-in-Chief), edited by W. Gerberich and W. Yang (Elsevier, Amsterdam, 2003) pp. 265–324.
D. Shamiryan, T. Abell, F. Iacopi, and K. Maex: Low-k dielectric materials. Mater. Today 7, 34–39 (2004).
M.F. Dorner and W.D. Nix: Stresses and deformation processes in thin films on substrates. CRC Crit. Rev. Solid State Mater. Sci. 14, 225–267 (1988).
D. Fridline: Finite element modeling of electromigration and stress voiding in microelectronic interconnects. Ph.D. thesis, Brown University, 2001.
M.A. Korhonen, C.A. Paszkiet, and C.Y. Li: Mechanisms of thermal stress relaxation and stress induced voiding in narrow aluminum based metallizations. J. Appl. Phys. 69, 8083–8095 (1991).
A.I. Sauter and W.D. Nix: Thermal stresses in Al lines bonded to substrates. IEEE Trans. Compd. Hybrids Manuf. Technol. 15, 594–600 (1992).
J.W. Hutchinson and Z. Suo: Mixed mode cracking in layered materials. Adv. Appl. Mech. 29, 163–191 (1992).
H. Tohmyoh, M. Yasuda, and M. Saka: Controlling Ag whisker growth using very thin metallic films. Scr. Mater. 63, 289–292 (2010).
A. Kosinova, D. Wang, P. Schaaf, A. Sharma, L. Klinger, and E. Rabkin: Whiskers growth in thin passivated Au films. Acta Mater. 149, 154–163 (2018).
M.W. Chen and I. Dutta: Atomic force microscopy study of plastic deformation and interfacial sliding in Al thin film: Si substrate systems due to thermal cycling. Appl. Phys. Lett. 77, 4298–4300 (2000).
I. Dutta, M.W. Chen, K.A. Peterson, and T. Shultz: Plastic deformation and interfacial sliding in Al and Cu thin film: Si substrate systems due to thermal cycling. J. Electron. Mater. 30, 1537–1548 (2001).
P. Kumar and I. Dutta: Influence of electric current on diffusionally accommodated sliding at hetero-interfaces. Acta Mater. 59, 2096–2108 (2011).
P. Kumar and I. Dutta: Effect of substrate surface on electromigration-induced sliding at hetero-interfaces. J. Phys. D Appl. Phys. 46, 155303 (2013).
K.A. Peterson, I. Dutta, and M.W. Chen: Diffusionally accommodated interfacial sliding in metal-silicon systems. Acta Mater. 51, 2831–2846 (2003).
D.K. Kim, W.D. Nix, R.P. Vinci, M.D. Deal, and J.D. Plumer: Study of the effect of grain boundary migration on hillock formation in Al thin films. J. Appl. Phys. 90, 781–788 (2001).
M. Burkhard, S. Kuwano, T. Fujita, I. Dutta, and M.W. Chen: Correlation between whisker growth, dissolution pitting and Si precipitation in an Al thin film on Si during heat treatment. J. Mater. Sci. 45, 3367–3374 (2010).
P. Jagtap, A. Chakraborty, P. Eisenlohr, and P. Kumar: Identification of whisker grain in Sn coatings by analyzing crystallographic micro-texture using electron back-scatter diffraction. Acta Mater. 134, 346–359 (2017).
P. Jagtap, V. Sethuraman, and P. Kumar: Critical evaluation of relative importance of stress and stress gradient in whisker growth in Sn coatings. J. Electron. Mater. 47, 5229–5242 (2018).
I. Dutta, P. Kumar, and M.S. Bakir: Interface-related reliability challenges in 3-D interconnect system with through-silicon vias. JOM 63, 70–77 (2011).
P. Kumar, I. Dutta, and M.S. Bakir: Interfacial effects during thermal cycling of Cu-filled through-silicon vias (TSV). J. Electron. Mater. 41, 322–335 (2012).
E. Zschech, H.J. Engelmann, M.A. Meyer, V. Kahlert, A.V. Vairagar, S.G. Mhaisalkar, K. Ahila, M.Y. Yan, K.N. Tu, and V. Sukharev: Effect of interface strength on electromigration-induced inlaid copper interconnect degradation: experiment and simulation. Z. Metallkd. 96, 966–971 (2005).
E.A. Brandes and G.B. Brook (Eds): Smithells Metals Reference Book. 7th ed. (Butterworth-Heinemann Ltd., Oxford, 1992).
M. Vijayakumar, A.M. Sriramamurthy, and S.V.N. Naidu: Calculated phase diagram of Cu–W, Ag–W and Au–W binary system. Calphad 12, 177–184 (1988).
D. Josell, T.P. Weihs, and H. Gao: Diffusional creep: stresses and strain rates in thin films and multilayers. MRS Bull. 27, 39–44 (2002).
N. Okamoto, F. Wang, and T. Watanabe: Adhesion of electrodeposited copper, nickel and silver films on copper, nickel and silver substrates. Mater. Trans. 45, 3330–3333 (2004).
P. Jagtap, P.R. Narayan, and P. Kumar: Effect of substrate composition on whisker growth in Sn coatings. J. Electron. Mater. 47, 4177–4189 (2018).
Acknowledgment
The authors thank the Department of Science and Technology (DST), Government of India for financial support (DSTO #1164 and #1526).
Author information
Authors and Affiliations
Corresponding author
Rights and permissions
About this article
Cite this article
Somaiah, N., Kanjilal, A. & Kumar, P. Effects of an interfacial layer on stress relaxation mechanisms active in the Cu-Si thin film system during thermal cycling. MRS Communications 10, 164–172 (2020). https://doi.org/10.1557/mrc.2020.6
Received:
Accepted:
Published:
Issue Date:
DOI: https://doi.org/10.1557/mrc.2020.6