Abstract
The microstructures and tension properties of Fe50Mn20Cr20Ni10 medium entropy alloy (MEA) were investigated, which was produced by vacuum induction melting and subsequently was homogenized at 1200 °C for 6 h. Microstructure characterization shows the single-phase solid solution with face-centered cubic structure by means of transmission electron microscopy and scanning electron microscopy combined with energy disperse spectroscopy. Our Fe-MEA has an ultimate tensile strength of 550 ± 10 MPa and a high strain hardening exponent, n, of 0.41 as well as a higher ductility (60%) than those of CrMnFeCoNi alloy. The single-phase solid solution deforms plastically via dislocations and twins. Twin boundaries associated with deformation twinning impede dislocation motion, enhancing the strain hardening capacity. This article focuses on the insights into the concept of Fe-MEAs and provides a potential direction for the future development of high entropy alloys and MEAs.
Similar content being viewed by others
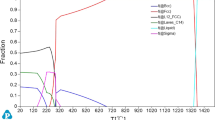
Avoid common mistakes on your manuscript.
1 Introduction
Conventional alloys usually contain only one or two primary elements, with small amounts of alloying elements added to enhance specific physical and/or mechanical properties. In contrast, medium and high entropy alloys (MEAs and HEAs) consist of at least four principal elements with approximately equal proportions [1,2,3]. The increased number of elements not only greatly expands possible alloy composition spaces and potential for promising new alloys [4] but also leads to excellent mechanical properties [5,6,7,8,9] with a good combination of strength, ductility and toughness at room temperature and cryogenic temperatures.
A representative example is the equiatomic FeCoCrMnNi HEA, and under quasi-static uniaxial tensile loading, the room-temperature mechanical performances of FeCoCrMnNi HEA are super to those of simple binary Fe–Mn alloys [10]. On the other hand, Gludovatz et al. [11] recently reported that the mechanical performance of equiatomic FeCoCrMnNi alloy is better than that of all conventional alloys under cryogenic conditions. The fracture toughness values measured by compact tension test at cryogenic temperatures down to 77 K were found to exceed 200 MPa m1/2 at crack initiation and 300 MPa m1/2 for stable crack growth. The potential deformation mechanism that is associated with these excellent properties is owing to nano-twins, which is absent at ambient temperatures [12]. Generally, the deformation mechanisms and stacking fault energy (SFE) have the following relationships in high manganese twinning induced plasticity (TWIP) steels: (i) the dislocation slip with SFEs larger than 60 mJ m−2; (ii) the twinning with SFEs between 20 and 60 mJ m−2; and (iii) transformation from face-centered cubic (FCC) to hexagonal close-packed phase, i.e., transformation induced plasticity (TRIP), with SFEs lower than 20 mJ m−2 [13,14,15,16].
In this study, we purposefully designed non-equiatomic FCC-based MEAs with four principle elements (i.e., Fe, Mn, Cr and Ni) and successfully developed a non-equiatomic FCC Fe50Mn20Cr20Ni10 MEA using an appropriate adjustment of composition ratio to decrease SFE in order to promote twinning and reduce the cost of alloy. The designed Fe50Mn20Cr20Ni10 MEA shows dislocation and twinning co-dominated deformation mechanism. The effect of SFE on the deformation mode is discussed in detail. This work provides a guide for the design of high-performance and low-cost second-generation Fe-MEAs or HEAs for extensive applications.
2 Experimental
An Fe50Mn20Cr20Ni10 MEA was fabricated using a vacuum induction melting equipment under an argon atmosphere using commercial pure elements (the purity of each raw material was 99.9% at least). Raw materials were alloyed in a boron nitride crucible to make a master alloy of 350 g in weight. Additional 5 wt.% Mn was added to compensate for the loss of Mn by evaporation during melting. The master alloy was molten and poured into rectangular copper molds (length of 30 mm, width of 30 mm, and thickness of 100 mm). The alloys were re-melted twice to ensure chemical homogeneity and were homogenized at 1200 °C for 6 h. The phase structure was characterized by X-ray diffraction (XRD) using a Rigaku UltimalV diffractometer. Transmission electron microscopy (TEM) observations were performed using a JEM-F200 microscope operating at 200 kV. Scanning electron microscope (SEM) was operated at 20 kV and a sample tilt of 70°. The tensile samples with gauge length of 10 mm and width of 3 mm were cut into a dog-bone shape using the electrical discharge machine. Tensile tests were carried out at a strain rate of 1 × 10–3 s−1 using an Instron 5969 materials testing machine at room temperature (293 K).
3 Results and discussion
3.1 Design strategy of a novel Fe-MEA
The alloy design strategy is based on the following considerations: (i) as reported elsewhere [17], SFE of the equiatomic FeMnNiCoCr HEA was determined to be 25 mJ/m2 using a combination of density functional theory calculations and XRD experiments. Reducing Ni and Co contents would lower SFE and alloying costs and increase the potential industrial applicability of the alloys. (ii) It is well known that stainless steels have good corrosion resistance because of the addition of a large number of alloying elements including Cr [18]. And (iii) as recently reported in Ref. [19], Fe40Mn20Cr20Ni20 MEA exhibits deformation nano-twins at cryogenic temperatures. Nevertheless, it is absent at ambient temperature. Thus, to avoid the brittle sigma phase, reduce cost and achieve TWIP effect in a single FCC phase microstructure, Fe50Mn20Cr20Ni10 alloy with reduced Ni content and Co totally removed is developed.
As shown in Table 1, some thermodynamic parameters of the present alloy have been calculated, including the mixed entropy (ΔSmix), mixing enthalpy (ΔHmix), misfit of atomic radius (δ), electronegativity difference (Δχ) and valance electron concentration (VEC). Table 1 suggests that these parameters all meet the phase formation criterion and are beneficial to obtaining simple FCC solid solutions.
3.2 Microstructure
Figure 1a shows SEM image of the homogenized Fe50Mn20Cr20Ni10 MEA, which was composed of fully recrystallized equiaxed grains with an average grain size of ~ 100 μm. And it can be concluded that the crystal orientations were random without any texture. A region containing a normal grain boundary (GB) of the homogenized alloy was prepared for compositional homogeneity analysis by energy-dispersive spectrum (EDS), as shown in Fig. 1b. The accurate composition of the homogenized alloy was obtained by conducting a comprehensive chemical analysis and the results are listed in Table 2. All the alloying elements (Fe, Mn, Cr and Ni) were homogenously distributed without apparent elemental segregation or secondary phases, indicating that Fe-based MEA has a uniform microstructure and is a random solid solution. This is different from FeMn- and FeMnNi-based alloys in which Mn segregation at GBs is usually found [20,21,22]. Figure 2 exhibits XRD patterns of the homogenized sample, which indicates that the present alloy has single-phase FCC structure, i.e., an austenite-type structure. Moreover, aγ is the austenite lattice parameter that can be calculated as to be 0.365 nm by the following equation:
where dhkl is the inter-planar spacing at austenite reflections {hkl}. dhkl is related to the angular position (θhkl) and X-ray wavelength (λ) as follows:
3.3 Mechanical properties at room temperature
Figure 3 shows the tensile stress–strain and strain hardening rate curves of Fe50Mn20Cr20Ni10 MEA at room temperature. The alloy has a yield strength of 300 ± 10 MPa, an ultimate tensile strength of 550 ± 10 MPa and tensile ductility of 60% ± 5%, which are comparable to those of CrMnFeCoNi [11, 23], CrMnFeCo [6, 24,25,26] and CrFeCoNi HEAs [27], all of which include the element of Co. Figure 3b shows the corresponding strain hardening rate. Another parameter used for evaluating strain hardening capability is the strain hardening exponent n, whose value could be simulated by the Hollomon and Ludwick equations, respectively, as shown below [28]:
where σ is true stress; σ0 is the yield strength; εp is true strain; and K is a strength coefficient representing the true stress when εp = 1. Figure 3 shows engineering and true stress–strain curves of Fe50Mn20Cr20Ni10 MEA and Fig. 4 is the simulated curves by Hollomon and Ludwick equations. Table 3 lists the simulated values of n, K and σ0 from Hollomon and Ludwick equations. The overall n of Fe50Mn20Cr20Ni10 MEA is 0.41 by the Hollomon equation and 0.63 by the Ludwick equation. The high value of n indicates a high strain hardening ability for the current Fe50Mn20Cr20Ni10 MEA, which are superior values among HEAs as well as TWIP and TRIP alloys [29,30,31]. It is reasonable that the flow stress will remarkably increase, since the newly formed twins refine the grain size and introduce new interface obstacles. Therefore, the strain hardening behavior from twinning is known as a dynamic Hall–Petch effect. Based on Hart’s theory [32] and the Considère criterion [33], strain hardening rate \(\left( {\varTheta = \frac{{\text{d}}\sigma }{{\text{d}}\varepsilon }} \right)\) contributed to high ductility, as it can help delay necking and maintain elongation. Consequently, the uniform elongation of Fe50Mn20Cr20Ni10 alloy is comparable to that of other alloys and MEAs/HEAs [2, 19, 24, 25].
3.4 Prediction of yield strength
According to classical Labush model [36] for concentrated solid solutions, already successfully applied to HEAs [37], solid solution strengthening (SSS) caused by the atoms of i element (\(\Delta \sigma_{{{\text{SS}}i}}\)) can be described as:
where G is the shear modulus of the alloy, 81.8 GPa; Z is a fitting constant; Ci is the concentration of element i; ri and Gi are i-atomic size and shear modulus; and fi is the mismatch parameter, which can be calculated using the following formula:
where \(\updelta r_{i} = \left( \frac{1}{r} \right){\text{d}}r/{\text{d}}C_{i}\) and \(\updelta G_{i} = \frac{1}{G}{\text{d}}G/{\text{d}}C_{i}\) are atomic size and the atomic modulus mismatch parameters, respectively; and α is a constant dependent on the type of the mobile dislocations. Generally, α is 2–4 for the screw dislocations and α ≥ 16 for edge dislocations [38].
The mismatch parameters \(\updelta G_{i}\) and \(\updelta r_{i}\) can be estimated in accordance with the method proposed in Refs. [38, 39]. In an FCC lattice, each element has 12 nearest-neighbor atoms, thus forming a 13-atom cluster. If the local environment around the alloying element i is assumed to be equal to the average composition of the alloy, element i has Nj = 13Cj of j-atom and Ni = 13 Ci − 1 of i-atom neighbors (j ≠ i). Then, \(\updelta r_{i}\) and \(\updelta G_{i}\) mismatches in the vicinity of the element i are estimated as an average of the atomic size difference, \(\updelta r_{ij} = 2\left( {r_{i} - r_{j} } \right)/\left( {r_{i} + r_{j} } \right)\) and shear modulus difference, \(\updelta G_{ij} = 2\left( {G_{i} - G_{j} } \right)/\left( {G_{i} + G_{j} } \right)\), respectively, of this element with its neighbors:
The calculated values of \(\updelta r_{i}\) and \(\updelta G_{i}\) for different constituent elements of Fe50Mn20Cr20Ni10 alloy calculated using Eqs. (7) and (8) are given in Table 4. Apparently, the highest (absolute) atomic size mismatches, \(\updelta r_{i}\), in the Fe50Mn20Cr20Ni10 alloy are around Cr and Ni atoms of 0.0520 and − 0.0650, respectively. Likewise, the highest atomic modulus mismatches in Fe50Mn20Cr20Ni10 alloy are around Cr and Ni atoms of 0.3009 and − 0.1434, respectively. It should be noted that the absolute value of δGCr is more than twice higher than the value of δGNi.
fi values are calculated using Eq. (6) with α value of 2. Calculations were performed with an assumption that Fe50Mn20Cr20Ni10 alloy is single solid solution phase with a composition corresponding to nominal composition of the alloy. Obviously, the mismatch parameter for Cr is significantly higher than those for other constitutive elements.
ΔσSSi is calculated using Eq. (5), Z value is 0.04 and G value is 81.8 GPa. ΔσSSCr is distinctly higher than solid solution strengthening by other elements: ΔσSSNi is 79.92 MPa, while ΔσSSFe and ΔσSSMn are 18.18 and 41.62 MPa, respectively. It should be noted that ΔσSSCr = 246.30 MPa, and ΔσSSNi is only approximately 32% of ΔσSSCr, whereas ΔσSSFe and ΔσSSMn are about 7% and about 17% of ΔσSSCr, respectively. This analysis reveals that SSS by single element (Cr) with atomic fraction of 20% is about 1.8 times higher than strengthening by other elements. Therefore, the conclusion can be applied to complexly concentrated multi-component alloys, in which, only certain elements can produce strong SSS effect, while other constitutive elements only slightly strengthen alloys.
SSS effect in multi-component alloys can be calculated using the Gypen and Deruyttere methods [40] that have been successfully applied to HEA [37]. In this way, overall solid solution strengthening of alloy, ΔσSS, can be calculated using the following formula by summarizing the ΔσSSi of each component in the alloy:
The calculated values of ΔσSS of Fe50Mn20Cr20Ni10 MEA are plotted against the experimental values of the corresponding alloys in Fig. 5. A good fit between the calculated values of ΔσSS and experimentally determined yield strength (YS) of the alloys is reached. The reason for the slight difference between the predicted yield strength and experimental value is that the mechanical behavior of MEAs is directly correlated with the degree of local chemical order [42, 43]. The correlation between the predicted SSS and experimental yield strength illustrates two following facts: (i) the methodology developed for predicting SSS in conventional alloys, i.e., Labush approach and Gypen and Deruyttere approach, is working for MEAs or HEAs if contributions from each constitutive element of the alloys are estimated and summarized; (ii) the yield strength of the solid solution alloys can be primarily attributed to SSS.
3.5 Deformation mechanisms
The deformation behavior of metals mainly includes dislocation multiplication and interactions between dislocations and other crystal defects as well as themselves. According to the classic Taylor hardening model [44], the quantitative forest hardening effect of dislocations in Fe50Mn20Cr20Ni10 MEA is given by:
where Δσ is the corresponding increase in the tensile stress; M is the Taylor factor, 3.06; b is the magnitude of the Burgers vector (0.253 nm); and ρ is the dislocation density. α is 0.2 in Eq. (10). The actual value of α is determined by the geometrical arrangement of the dislocation, and it decreases continuously with plastic deformation. However, the variations are in a 10% range [45], and thus it is approximated as a stable constant during the plastic deformation. Here, it is assumed that if no accumulation of dislocations occurs when yields, then, σ can be obtained by the corresponding ρ at different tensile strains as σ = Δσ + YS. The difference between the calculated and experimental flow stress is increased with straining, since the contribution of stacking faults and twins is not considered. In general, the forest dislocation hardening effect is the major mechanism in the initial deformation stage in Fe50Mn20Cr20Ni10 MEA.
The variation in strength, ductility and strain hardening with Mn content is closely related to the deformation mechanisms. An essential novelty of the current finding is the fact that the newly designed Fe50Mn20Cr20Ni10 alloy shows deformation-induced nano-twins at room temperature. It has been reported that the equiatomic Fe20Mn20Ni20Co20Cr20 HEA exhibited deformation twinning only at 77 K [11]. For FCC HEAs, it has been reported that the main deformation mechanism is the dislocation slip at room temperature, although it changes to the deformation twinning at cryogenic temperature as the resolved shear stress is sufficient to reach the critical stress for twinning [46]. In order to explore the deformation mechanisms at room temperature, the presence of the deformation twins is further confirmed by TEM analysis, as shown in Fig. 6a. The high-density dislocations accumulated within deformation twin and the corresponding selected area electron diffraction (SAED) pattern are presented in Fig. 6b–d, where the activated twin system was indexed as \(\left[ {\overline{1}12} \right]\left( {1\overline{1}1} \right)\), similar to a compound FCC twin commonly observed in FCC crystalline alloys [47].
TEM images on [110] zone axis (Z.A.) of tensile-fractured Fe-MEA with ε = 60%. a Dark field image showing deformation nano-twinning system in Fe-MEA; b, c bright field images of high-density dislocations within twins; d corresponding SAED pattern of matrix (M) and twin (T); e high-density dislocations accumulated between dislocation walls; f schematic sketch illustrating deformation mechanism in Fe-MEA
Now, it is widely accepted that twinning during deformation continuously increases new interfaces that promote work hardening by decreasing the dislocation mean-free path [48]. It is commonly referred as the “dynamic Hall–Petch” effect. In addition, the triggered deformation twins at cryogenic temperature and/or high strain rate contain high-density dislocations that act as strong barriers to dislocation glides, which further primarily contributes to strain hardening [49,50,51,52,53]. Hence, the improvement in the strength mainly by the activation of nano-twins is quite significant. The formation of more complex planar dislocation configurations is available, such as dislocation walls and dislocation networks (Fig. 6e). It should be noted that the formation of dislocation networks enables the transformation of dislocation pile-up into planar dislocation structures in Ref. [24]. Figure 6f symbolically shows the deformation mechanisms of the alloy under the joint action of dislocation cells, dislocation walls and deformation twins. Therefore, the mechanical properties of the present Fe-based MEA are better than those in many other major HEA classes.
The design strategy, mechanical properties and deformation mechanism of Fe-based MEA are discussed in detail above. It can be found that the design concept of Fe-based MEA combines the advantages of TWIP steels and HEAs. Figure 7 shows that Fe-MEA concept is a potential guide for the development of low-cost, but high-performance HEAs or MEAs. It summarizes (UTS·TE/price) versus configurational entropy of Fe-MEAs in comparison with other previously developed HEAs and/or MEAs where R is gas constant, 8.314 J mol−1 K−1, UTS is ultimate tensile strength, GPa; and TE is total elongation to fracture, %. Obviously, compared to many Co-containing HEAs or MEAs, Fe-based MEAs have very broad development aspect and application prospects. The successful design of Fe-based MEAs greatly promoted the development of new alloys with low cost and excellent mechanical performance, which will be the critical point for alloy design and practical industry application in the future.
4 Conclusions
-
1.
The mechanical properties of Fe50Mn20Cr20Ni10 MEA were comparable to the equiatomic CoCrFeMnNi alloy due to the deformation twins. The average strain hardening exponents simulated by the Hollomon equation and the Ludwick equation were 0.41 and 0.63, respectively.
-
2.
The solid solution strengthening caused by different elements of Fe50Mn20Cr20Ni10 MEA was calculated using Labush approach. It shows that Cr produces strongest solid solution strengthening among the constitutive elements of the alloys. According to the Gypen and Deruyttere method, the contribution of each element of the alloy is summarized to evaluate the solid solution strengthening of Fe50Mn20Cr20Ni10 MEA. A good correlation between the experimental yield strength value and the predicted solid solution strengthening was observed.
-
3.
The forest dislocation hardening effect, calculated by the Taylor hardening model, and a dynamic Hall–Petch effect caused by deformation twins were the primary hardening contributor during the plastic deformation.
-
4.
Compared with other major HEA classes, the present Fe-MEA has outstanding combination mechanical properties and low cost, providing a new direction for future development of HEAs and MEAs.
References
J.W. Yeh, S.K. Chen, S.J. Lin, J.Y. Gan, T.S. Chin, T.T. Shun, C.H. Tsau, S.Y. Chang, Adv. Eng. Mater. 6 (2004) 299–303.
B. Cantor, I.T.H. Chang, P. Knight, A.J.B. Vincent, Mater. Sci. Eng. A 375–377 (2004) 213–218.
Y. Zhang, T.T. Zuo, Z. Tang, M.C. Gao, K.A. Dahmen, P.K. Liaw, Z.P. Lu, Prog. Mater. Sci. 61 (2014) 1–93.
Y. Ye, Q. Wang, J. Lu, C. Liu, Y. Yang, Mater. Today 19 (2016) 349–362.
M.H. Tsai, J.W. Yeh, Mater. Res. Lett. 2 (2014) 107–123.
Z. Li, K.G. Pradeep, Y. Deng, D. Raabe, C.C. Tasan, Nature 534 (2016) 227–230.
O.N. Senkov, G.B. Wilks, J.M. Scott, D.B. Miracle, Intermetallics 19 (2011) 698–706.
Z.Y. Ding, Q.F. He, Q. Wang, Y. Yang, Int. J. Plasticity 106 (2018) 57–72.
K.S. Ming, X.F. Bi, J. Wang, Int. J. Plasticity 100 (2018) 177–191.
C.C. Tasan, Y. Deng, K.G. Pradeep, M.J. Yao, H. Springer, D. Raabe, JOM 66 (2014) 1993–2001.
B. Gludovatz, A. Hohenwarter, D. Catoor, E.H. Chang, E.P. George, R.O. Ritchie, Science 345 (2014) 1153–1158.
F. Otto, A. Dlouhý, C. Somsen, H. Bei, G. Eggeler, E.P. George, Acta Mater. 61 (2013) 5743–5755.
A. Saeed-Akbari, L. Mosecker, A. Schwedt, W. Bleck, Metall. Mater. Trans. A 43 (2012) 1688–1704.
S. Allain, J.P. Chateau, O. Bouaziz, S. Migot, N. Guelton, Mater. Sci. Eng. A 387–389 (2004) 158–162.
V. Shterner, I.B. Timokhina, H. Beladi, Mater. Sci. Eng. A 669 (2016) 437–446.
S. Curtze, V.T. Kuokkala, Acta Mater. 58 (2010) 5129–5141.
A.J. Zaddach, C. Niu, C.C. Koch, D.L. Irving, JOM 65 (2013) 1780–1789.
K.H. Lo, C.H. Shek, J.K.L. Lai, Mater. Sci. Eng. R Rep. 65 (2009) 39–104.
B.B. Bian, N. Guo, H.J. Yang, R.P. Guo, L. Yang, Y.C. Wu, J.W. Qiao, J. Alloy. Compd. 827 (2020) 153981.
O. Dmitrieva, D. Ponge, G. Lnden, J. Millán, P. Choi, J. Sietsma, D. Raabe, Acta Mater. 59 (2011) 364–374.
D. Raabe, S. Sandlöbes, J. Millán, D. Ponge, H. Assadi, M. Herbig, P.P. Choi, Acta Mater. 61 (2013) 6132–6152.
M. Kuzmina, D. Ponge, D. Raabe, Acta Mater. 86 (2015) 182–192.
M.J. Yao, K.G. Pradeep, C.C. Tasan, D. Raabe, Scripta Mater. 72–73 (2014) 5–8.
Y. Deng, C.C. Tasan, K.G. Pradeep, H. Springer, A. Kostka, D. Raabe, Acta Mater. 94 (2015) 124–133.
Z.M. Li, F. Körmann, B. Grabowski, J. Neugebauer, D. Raabe, Acta Mater. 136 (2017) 262–270.
Z.M. Li, C.C. Tasan, H. Springer, B. Gault, D. Raabe, Sci. Rep. 7 (2017) 40704.
Z.G. Wu, Y.F. Gao, H.B. Bei, Acta Mater. 120 (2016) 108–119.
T.H. Courney, in: Mechanical Behavior of Materials, 2nd ed., McGraw-Hill, New York, USA, 2000.
X.L. Wu, M.X. Yang, F.P. Yuan, L. Chen, Y.T. Zhu, Acta Mater. 112 (2016) 337–346.
M.M. Wang, C.C. Tasan, D. Ponge, D. Raabe, Acta Mater. 111 (2016) 262–272.
Z.C. Li, R.D.K. Misra, Z.H. Cai, H.X. Li, H. Ding, Mater. Sci. Eng. A 673 (2016) 63–72.
E.W. Hart, Acta Metall. 15 (1967) 351–355.
Q. Wei, S. Cheng, K.T. Ramesh, E. Ma, Mater. Sci. Eng. A 381 (2004) 71–79.
X. Yang, Y. Zhang, Mater. Chem. Phys. 132 (2012) 233–238.
R.T. Chen, G. Qin, H.T. Zheng, L. Wang, Y.Q. Su, Y.L. Chiu, H.S. Ding, J.J. Guo, H.Z. Fu, Acta Mater. 144 (2018) 129–137.
R. Labusch, Phys. Status Solidi 41 (1970) 659–669.
I. Toda-Caraballo, P.E.J. Rivera-Díaz-del-Castillo, Acta Mater. 85 (2015) 14–23.
O.N. Senkov, J.M. Scott, S.V. Senkova, D.B. Miracle, C.F. Woodward, J. Alloy. Compd. 509 (2011) 6043–6048.
G.A. Salishchev, M.A. Tikhonovsky, D.G. Shaysultanov, N.D. Stepanov, A.V. Kuznetsov, I.V. Kolodiy, A.S. Tortika, O.N. Senkov, J. Alloy. Compd. 591 (2014) 11–21.
L.A. Gypen, A. Deryuttere, J. Mater. Sci. 12 (1977) 1028–1033.
N.D. Stepanov, D.G. Shaysultanov, M.A. Tikhonovsky, G.A. Salishchev, Mater. Des. 87 (2015) 60–65.
Y. Ma, Q. Wang, C. Li, L.J. Santodonato, M. Feygenson, C. Dong, P.K. Liaw, Scripta Mater. 144 (2018) 64–68.
R. Zhang, S. Zhao, J. Ding, Y. Chong, T. Jia, C. Ophus, M. Asta, R.O. Ritchie, A.M. Minor, Nature 581 (2020) 283–287.
J.K. Kim, B.C. De Cooman, Mater. Sci. Eng. A 676 (2016) 216–231.
W. Püschl, Prog. Mater. Sci. 47 (2002) 415–461.
G. Laplanche, A. Kostka, O.M. Horst, G. Eggeler, E.P. George, Acta Mater. 118 (2016) 152–163.
N.L. Okamoto, S. Fujimoto, Y. Kambara, M. Kawamura, Z.M.T. Chen, H. Matsunoshita, K. Tanaka, H. Inui, E.P. George, Sci. Rep. 6 (2016) 35863.
O. Bouaziz, S. Allain, C. Scott, Scripta Mater. 58 (2008) 484–487.
H. Idrissi, K. Renard, D. Schryvers, P.J. Jacques, Scripta Mater. 63 (2010) 961–964.
Z. Yang, M. Yang, Y. Ma, L. Zhou, W. Cheng, F. Yuan, X. Wu, Mater. Sci. Eng. A 793 (2020) 139854.
Y. Ma, F. Yuan, M. Yang, P. Jiang, E. Ma, X. Wu, Acta Mater. 148 (2018) 407–418.
Z. Li, S. Zhao, S.M. Alotaibi, Y. Liu, B. Wang, M.A. Meyers, Acta Mater. 151 (2018) 424–431.
Z. Li, S. Zhao, H. Diao, P.K. Liaw, M.A. Meyers, Sci. Rep. 7 (2017) 42742.
J.W. Bae, H.S. Kim, Scripta Mater. 186 (2020) 169–173.
J.W. Bae, J.B. Seol, J. Moon, S.S. Sohn, M.J. Jang, H.Y. Um, B.J. Lee, H.S. Kim, Acta Mater. 161 (2018) 388–399.
Acknowledgements
The authors would like to acknowledge the financial support of the Natural Science Foundation of Shanxi Province, China (Nos. 201901D111105 and 201901D111114), Transformation of Scientific and Technological Achievements Programs of Higher Education Institutions in Shanxi (2019), State Key Lab of Advanced Metals and Materials of China (Grant No. 2020-Z09), and the opening project of the State Key Laboratory of Explosion Science and Technology (Beijing Institute of Technology), and the opening project number is KFJJ20-13M.
Author information
Authors and Affiliations
Corresponding author
Rights and permissions
About this article
Cite this article
Qin, Mj., Jin, X., Zhang, M. et al. Twinning induced remarkable strain hardening in a novel Fe50Mn20Cr20Ni10 medium entropy alloy. J. Iron Steel Res. Int. 28, 1463–1470 (2021). https://doi.org/10.1007/s42243-021-00585-3
Received:
Revised:
Accepted:
Published:
Issue Date:
DOI: https://doi.org/10.1007/s42243-021-00585-3