Abstract
Superalloys are high-performance materials which combine high tensile, creep and fatigue strength, besides good ductility, toughness and resistance to corrosion, properties that are also responsible for their low machinability. The VAT 30® alloy contains an austenitic stainless steel base with additions of chromium, nickel, titanium and aluminum, and it is mainly applied on the manufacture of valves of combustion engines, due to its advantageous characteristics. This alloy exhibits both high ductility and abrasiveness, features that may promote both attrition and abrasion wear mechanisms on the tool used to cut it. This work contains some investigations about the effect of cooling condition, tool rake angle and cutting speed on the machinability of Ni-30 alloy in terms of cutting power consumption, surface roughness and tool life, besides the tool wear mechanisms. Conventional and high-pressure coolant injected toward the tool rake face was compared, as well as negative rake angle and neutral tooling, besides two different cutting speeds. Results show that high-pressure coolant may reduce cutting power consumption and even increase the volume of material removed during tool life up to 45% in some cases, but this same influence has not been verified regarding the workpiece arithmetical mean roughness value. Negative and neutral rake angle tools did not present very different results in terms of power and roughness, but negative tools provided considerably higher volume of material removed per tool life (up to 75% in one condition). Cutting speed showed strong effect on the cutting power, as expected, but no reasonable effect on workpiece surface roughness; regarding tool life, the cutting speed increase typically reduced the volume of material removed per tool life with conventional cooling, but when high-pressure coolant was used, this effect was attenuated. Abrasion and attrition were the main tool wear mechanisms in any tested condition.
Similar content being viewed by others
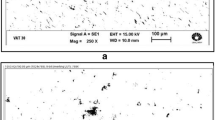
Avoid common mistakes on your manuscript.
1 Introduction
Superalloys are metallic materials that present outstanding mechanical properties even at high temperatures (above 540 °C); they can be divided into three categories: nickel based, cobalt based or iron based [1]. Besides fatigue strength and chemical stability, the addition of 10–25% of chromium provides high resistance to oxidation and corrosion [2]. Other alloying elements like nickel, titanium and aluminum help increasing mechanical and creep strength [3].
Although iron-based superalloys do not present such high properties as nickel- or cobalt-based superalloys, their cost is much lower than the others. VAT 30® alloy, also known as Ni-30 or NCF 3015, for example, is considerably cheaper than others of that kind, as it can be seen in Fig. 1 [4], which present the relative raw material cost of some superalloys. The main reason for the low cost of these alloys is their lower content of nickel, which is a very expensive alloying element. The nickel content inside Ni-30 alloy is close to 30%, which is typically lower than the nickel content of other superalloys. Sato et al. [5] asserted that using NCF 3015 instead of NCF 6018 (which features a nickel content of approximately 60 wt%) results in 20% cost reduction on the manufacturing of exhaust valves for combustion engines.
Relative raw material cost of some superalloys [4]
The Ni-30 alloy also presents, besides nickel, chromium, titanium and aluminum as the main alloying elements; these additions provide good mechanical, chemical and thermal properties which allow its application on turbine blades, high-temperature bolts, different parts for nuclear reactors and also valves for combustion engines. This alloy presents an austenitic gamma matrix with secondary phase constituted of Ni3Al and Ni3Ti intermetallics and precipitated carbides when it is not in the annealed condition [6]. This microstructure provides properties close to that of high-nickel alloys, at much lower cost [4]. Therefore, among other valve steels, it can withstand very high temperatures keeping its resistance to corrosion at a harmful environment created by the combined action of combustion gases and thermal and mechanical shocks [7].
Several material properties severely impair the machinability of metallic materials, such as: hardness, ultimate tensile strength, thermal conductivity, abrasiveness, strain hardening exponent, ductility and specific heat [8]. This means that tool wear, due to several mechanisms like abrasion, attrition, diffusion, oxidation or even built-up edge, may be accelerated by the combination of some of these properties.
Abrasion is related to the arisement of grooves on the flank face of the tool, at the same direction of the cutting speed, which removes tool coating and, consequently, increases the friction coefficient. It is accelerated by the increase of cutting temperature that reduces the hardness of the tool. The presence of hard particles inside the workpiece, like carbides, also stimulates abrasion. Attrition means the cyclical adhesion and removal of workpiece material on the tool cutting edge, pulling out also particles of the tool, especially on the machining of high ductility materials [9]. Abrasion is stimulated by these removed very hard tool particles because they scratch against the portion of the tool in front of them.
Almost all the mechanical work related to chip formation turns on thermal energy, that is heat. There are several sources for this heat, like chip strain, primary and secondary shear, friction between tool and chip and between tool and workpiece. This thermal energy may be dissipated through chip, workpiece, tool or even cutting fluid. For the tool, the contact region with either chip or workpiece is quite small and approximately fixed (do not change with time), making tool high temperatures to be reached. The higher the machining parameters, cutting speed, feed and depth of cut, the higher the amount of heat generated, and so the temperature on the tool. Therefore, tool wear is accelerated and coefficient of friction and cutting force is increased. Most of the tool wear mechanisms cited above are stimulated by the increase of temperature. Therefore, the increase of tool temperature shortens tool life. The use of coolant and lubricant cutting fluids may reduce the cutting temperature [10].
There are some features that strongly affect the specific cutting pressure and, consequently, cutting power: workpiece material, tool material and geometry, cutting section, cooling/lubrication conditions and sharpness of the tool [11]. Some alloying elements can increase the ultimate tensile strength of the workpiece material, and so its shear strength, what means increase of the specific cutting pressure. Regarding tool geometry, negative rake angles increase specific cutting pressure because chips are subjected to a higher strain [12]. Specific cutting pressure is reduced by the increase of cutting speed when low cutting speeds are applied, because chips became softer; additionally, a built-up edge may be formed at low cutting speeds and change the specific cutting pressure because it currently changes the rake angle of the tool; at higher speeds, its influence may be considered negligible. The higher the effectiveness of the penetration of the cutting fluid on the interfaces, tool flank face with workpiece and tool rake face with chip, the higher the lubrication effect, and so the lower the specific cutting pressure, because the cutting fluid changes the friction conditions between tool rake face and chip and between tool flank face and workpiece. However, this effect is less relevant at higher speeds, as the cutting fluid encounters more difficulties to reach those interfaces [12]. Moreover, in the machining of ductile materials, a lot of seizure of the chip happens on the tool rake face, what makes the contact between these two elements very intense and make the fluid penetration very unlikely.
During the cutting processes, some regions of the workpiece are compressed by the rake face of the tool. The portion of the workpiece in the vicinity of the portion of material which becomes chip may endure both elastic deformation (with consequent recovery) and plastic deformation without fracture. This condition generates burrs and grooves which harm surface finishing [13]. Therefore, the more ductile the workpiece material is, the more difficult is to obtain low surface roughness on it. Other features which strongly affect surface roughness are the combination of tool nose radius and feed (which has a geometrical contribution to the roughness) and vibration.
Ni-30 hot hardness that is around 300 HV from 400 to 600 °C is slightly inferior to that of Inconel 751® (a very expensive material whose nickel content is approximately 72 wt%) but is much greater when compared with 21-4N (or SUH 35, a high Cr–Mn, heat-resistant steel). Regarding the yield strength, Ni-30 maintains 700 MPa until 700 °C, a little bit lower than that of Inconel 751® but much higher than 21-4N. Charpy impact test showed excellent values around 180 J/cm2, outperforming both competitor alloys. Finally, the mean coefficient of thermal expansion for Ni-30 is lower than that presented by the others, as well as thermal conductivity [5].
When it comes to tensile properties, according to Carpenter Technology [14], Ni-30 alloy presents 1124 MPa ultimate strength, 35% elongation and 54% reduction of area at room temperature. Stainless steel type 304/304L, for example, presents 517 MPa ultimate strength, 60% elongation and 70% reduction of area [15]. This means Ni-30 is more than twice more resistant than 304 stainless steel with 3/5 of its elongation and 3/4 of its reduction of area. Pyromet alloy 718®, on the other side, presents 1250 MPa ultimate strength, 16% elongation and 23% reduction of area [16]. This means Ni-30 is almost as stronger as Pyromet, but two times more ductile than it, considering both elongation and reduction of area.
Ni-30 iron-based superalloy also presents considerably abrasiveness, especially due to the presence of Ni3(Ti, Al) precipitates, which answer for 25% in terms of atomic composition, and also due to the carbide phase [5]. Indeed, niobium is an element that promotes precipitation hardening, so its presence may be effective to improve this phase strength. For example, stainless steel type 304/304L presents no Nb content [15], while Ni-30 present almost 1 wt% niobium [20] and Pyromet almost 5 wt% [16]. Then, Ni-30 must exhibit both high ductility and abrasiveness, features that may promote both attrition and abrasion tool wear mechanisms.
Using low-pressure cutting fluids is quite simple, because it does not need any special device. In this case, cutting fluid is applied abundantly on the workpiece, chip and tool, without any specific direction [17]. The use of high-pressure coolant injected toward either tool flank face or tool rake face usually makes the fluid cooling and lubrication effects more efficient. When directed toward tool rake face, high-pressure coolant strongly helps chip breaking. This way of using fluid is especially interesting when machining materials which exhibit high strain hardening coefficients, good heat resistance, low thermal conductivity and high ductility, since high-pressure cutting fluid may facilitate heat dissipation, chip removal and, consequently, increase of tool life [18].
Magri et al. [19] concluded that the use of high-pressure coolant directed either to the flank face or to the rake face of the tool could extend tool life compared with the use of the conventional application of cutting fluid, when turning a nickel-based superalloy. This cooling condition was able to avoid notch wear caused by the furrowing effect of the hard burr (the nickel-based alloy has a high hardening ratio, what made the burr created by the plastic deformation of the chip to be very hard) that was formed near the end of the depth of cut. Regarding surface roughness, high-pressure coolant could guarantee better finishing from the beginning to the end of tool life.
Diniz and Micaroni [20] compared dry machining with the usage of vegetable water-based flood coolant (6% brix) applied both conventionally and using high pressure on flank and rake surfaces of the tool during a turning operation of a SAE 1045 carbon steel. The best results for tool life were obtained with high-pressure coolant injected toward both flank and rake faces or only toward rake face. When the coolant was directed only to flank face, the attrition mechanism led to a huge crater wear. Conventional cooling provided similar results to that of dry cutting.
Diniz et al. [21] also compared dry and vegetable water-based flood coolant applied on turning of SAE 1045 steel using two different coolant flow rates: 2.5 and 11 l/min and two different cutting speeds: 490 and 570 m/min. For the lowest speed, best results regarding tool life were obtained with the lowest coolant flow rate, but they were not much better than dry cutting. Cooling influence on tool life was more pronounced with the highest speed; nonetheless, the coolant flow rate seemed not to affect considerably tool life. Regarding power consumption, the different cooling conditions apparently did not affect lubricity, because no variation was noticed. This means that the coolant was not able to effectively reach the cutting interfaces; however, it was capable of reducing the cutting temperature and so increase tool life. So, the fluid effectively cooled the process, but it was not able to lubricate it.
Sharman et al. [22] tested three different cutting speeds, five different pressures for the semi-synthetic cutting fluid with three different coolant directions (flank face, rake face and both) on finishing turning of Inconel 718®. Results showed that even ultra-high-pressure coolant (450 bar) was not able to increase tool life significantly comparing to conventional cooling probably because temperatures generated were not too high so that high pressure could reduce them. Surface roughness and microhardness profile below the machined surface also did not show the effect of high-pressure coolant, even when tools close to their end of life were employed. Regarding residual stress, a compression-induced state was gotten when using sharp tools with ultra-high-pressure coolant directed only to the rake face of the tool. On the other side, a tensile-induced state was verified when conventional cooling was applied, especially when turning with extensively worn tools. High-pressure coolant reduced tensile stress. These results show that it is possible to induce compressive stress on machined parts during machining, with no need of further treatments like shoot peening.
Cica and Kramar [23] led an experimental investigation of the effect of machining parameters on high-pressure jet-assisted turning of Inconel 718 (a nickel-based superalloy) with coated carbide tools. A Taguchi L27 orthogonal array was used for the experimental design, in which diameter of the nozzle, distance between the impact point of the jet and the cutting edge, pressure of the jet, cutting speed and feed were considered as input factors. Their results showed that feed, pressure of the jet and diameter of the nozzle were the most important factors as far as cutting tool temperature is concerned. Besides other discussions, they concluded that cutting power was mainly influenced by the cutting speed, followed by the feed and the pressure of the jet.
D’Addona and Raykar [24] developed a finite-element modeling of tool temperature distribution during high-pressure coolant-assisted turning of Inconel 718 comparing four machining conditions: dry, conventional wet, high-pressure coolant at 50 bar and high-pressure coolant at 80 bar. They found out that the high-pressure jet was able to partially penetrate into the cutting interface, providing an efficient cooling and lubricating action, creating a coolant liquid wedge at the tool–chip interface which reduced the tool–chip contact length, decreased the coefficient of friction and, consequently, lowered the temperature during machining, what affected positively tool life.
Finally, Zahoor et al. [25] attempted to replace conventional fluids with a synthetic vegetable ester-based biodegradable oil to investigate the machinability aspects of Inconel 718, also studying cutting speed, feed per tooth and axial depth of cut as control variables on milling. They concluded that low cutting speeds were suitable to obtain smaller values of tool wear (as well as we found in this work) and also low surface roughness (which however was not statistically proved here). Besides that, with respect to tool wear, abrasion and adhesion wear were observed as the prominent types of wear on the carbide inserts, the same mechanisms found in our investigation.
This work contains a study of the machinability of the Ni-30 iron-based superalloy for engine valves manufacturing based on cutting power consumption, workpiece arithmetical mean roughness value, tool life and tool wear mechanisms. Cutting speed, cooling condition and tool geometry were chosen as input variables. Considering that mechanical and thermal properties may severely impair the alloy machinability, it is interesting to highlight some of its features in comparison with other heat-resistant alloys, as it follows.
2 Materials and methods
Experimental procedures were held in a 15-kW power and maximum 4500 rpm CNC lathe. They were external longitudinal turning tests on specimens of Ni-30 high-temperature iron-based superalloy using PVD triple-layered (TiAlN/(Al,Cr)2O3/TiAlN)-coated carbide inserts, ISO grade HC M15 and Blaser Swisslube vegetal-based emulsion (6% brix). Feed (f) and depth of cut (ap) were always kept as 0.1 mm and 0.5 mm, respectively.
The workpiece material was a Ni-30 superalloy, also known as VAT 30® or NCF 3015. It is recommended for valve manufacture for internal combustion engines, in which high-temperature strength and corrosion resistance are imperative. It is considerably cheaper than other alloys that present higher nickel content and may be used for the same purpose. So, it is very reasonable to present a study of machinability focused on this kind of material. Table 1 presents chemical composition of Ni-30 alloy, while Table 2 presents its mechanical properties at room temperature.
Figure 2 contains a micrography of Ni-30 alloy made in a scanning electron microscope (SEM) Zeiss EVO MA15 with an energy-dispersive X-ray spectroscopy (EDS) resource; the overview (Fig. 2a) shows carbide inclusions (dark regions) on the matrix (white background) and the EDS analysis (Fig. 2b) was capable of identifying that the main carbides (points 1, 2, 3 and 4) are rich in Nb and Ti, as inclusions on the austenitic matrix with Fe, Ni and Cr (points 5 and 6). Finally, using ImageJ, a freeware software on image processing, it was possible to infer that approximately 0.50% of the analyzed surface is full of carbides, whose average size is typically lower than 2.5 μm.
A full 23 factorial experimental planning was applied. This means that three input variables were studied, each one applied at two different levels. The first variable was the cooling condition: conventional coolant versus high-pressure coolant, injected toward the tool rake face at approximately 70 bar. The second variable was the tool geometry, as shown in Fig. 3: one was a negative rake angle (γo = − 6°) PCLNR 2525 M12 HP with CNMG 120404 MF inserts (Fig. 3a), and the other one was a neutral rake angle (γo = 0°) SCLCR 2525 M09 HP with CCMT 09T304 MF inserts (Fig. 3b). For the third variable, cutting speed was tested at two levels: 70 m/min and 85 m/min. Every experiment was replied in order to make possible the analysis of variance on the results.
Cutting power consumption was monitored all along the machining tests using an energy analyzer connected to a portable computer. The arithmetical mean roughness value (Ra) of the machined surface of the workpiece was evaluated after each machining pass using Mitutoyo Surftest SJ-201P portable surface roughness tester adjusted for a 0.8-mm cutoff. The roughness measurements were taken three times on each surface, each one at 120° distance from the other. An Olympus MX51-M optical microscope with a 1.3 megapixels Motic Moticam 1000 optical camera connected to a portable computer along with the image processing software Motic Images Plus was used to measure the evolution of the maximum flank wear of the tools. The tool life criterion was set as tool flank wear equal or above 0.3 mm. Considering the difference of material removal rates between combinations with different cutting speeds, tool life results are presented, rather than in cutting time, in terms of volume of material removed (V), which can be calculated as the product of feed (f), depth of cut (ap) and machining length (lf), as shown in Eq. 1.
All these response variables were submitted to analysis of variance (ANOVA) in order to infer if the factors cooling, tooling and cutting speed were significant on the results considering a 95% confidence level. Additionally, after the experiments, each cutting edge used was also taken to the SEM to have its wear analyzed using EDS, in order to investigate the wear mechanisms which led to the end of each tool life.
3 Results and discussion
Results for cutting power consumption at both, the beginning and the end of tool life, are presented in Fig. 4. Horizontal bars present the average power between replicas and the error bar, the standard deviation. It can be easily seen that tool wear increased cutting power in all conditions, as expected, because the growth of flank wear caused the enlargement of the contact area between tool and workpiece, increasing friction and, consequently, cutting force and cutting power. It is also clear that this difference was more significant when high-pressure coolant was employed. Moreover, this cooling condition provided lower cutting power in comparison with conventional cooling in all experiments, except for negative tool and 85 m/min, where the average power results were very similar. This pattern may be associated either to the improvement of lubrication on the tool–chip interface or to the reduction of the contact area between tool and chip provided by the wedge effect of the high-pressure coolant. The exception occurred in the test in which chip probably experienced the highest strain on the shear plane because of the negative rake angle of the tool and the highest cutting speed (what means both high temperature and ductility); the hypothesis to explain this result is that high-pressure cooling promoted a kind of quenching of the chip after the stick–slip zone, increasing its hardness and so cutting force and cutting power.
It is interesting to highlight that the use of a neutral tool provided considerably lower cutting power consumption than the negative rake angle tool, as it was expected, only at the condition in which cutting speed was 85 m/min and high-pressure coolant was used. At all the other conditions, in which conventional cooling and/or lower cutting speed were employed, this variation was not large; this means that the influence of cooling condition and cutting speed on cutting power was more significant than the cutting tool geometry. It may be observed that higher cutting speed provided higher cutting power in any combination of variables, what was very likely to happen. This result is quite similar to that of Cica and Kramar [23], which concluded that cutting power was mainly influenced by the cutting speed on turning Inconel 718.
On the analysis of variance (ANOVA) approach using F test (critical value for 95% confidence level is 5.32), cutting speed (130.74), cooling condition (54.20) and tool geometry (6.76) showed significant effects in this order of relevance, as well as the interactions between cooling and rake angle and between cooling and cutting speed.
Results for arithmetical mean roughness value (Ra) of the machined surface in each experiment measured at both, the beginning and the end of tool life, are shown in Fig. 5. Regarding the influence of tool wear on surface roughness, it seems that there is no consistent tendency; in some experiments, roughness was higher at the end of tool life; in other experiments, it was similar to that verified at the beginning of tool life. This result showed that flank wear, which has been used to establish the end of tool life criterion, has been probably not accompanied by the variation of the tool nose shape, what would provide roughness increase. In terms of cooling condition influence, in general, when high-pressure cooling was used, workpiece roughness was lower than when conventional cooling was used, very likely due to the higher lubrication provided by the former one. This was observed in any condition except for neutral tool and 85 m/min.
In terms of the influence of tool geometry, it seems that the tool rake angle did not affect surface roughness in a consistent way. The same can be said about the influence of cutting speed, since for some experiments with 70 m/min, roughness was lower and, for other experiments, the roughness value was lower when 85 m/min was used.
According to the ANOVA, neither cooling condition (F = 4.82), tool geometry (F = 0.54) or cutting speed (F = 0.77), or their interactions, presented reasonable effect on the arithmetical mean roughness on a 95% confidence level.
Results for volume of material removed per tool life (V) for each experiment are shown in Fig. 6. The vertical bars present the average volume between replicas and the error bar the standard deviation. High-pressure coolant did not always provide longer tool life when compared to conventional cooling. In two experiments, negative tool with the lowest speed and neutral tool with the highest speed, results were quite similar on both cooling conditions. For the experiment with rake angle equal to zero and cutting speed 70 m/min, high-pressure coolant actually reduced tool life to less than half of material removed when conventional cooling was used. Indeed, only with tool rake angle equal to − 6° and cutting speed of 85 m/min high-pressure coolant was useful for increasing tool life (around 45%) compared to the volume of material removed with conventional cooling. This indicates that, due to the seizure conditions on the tool–chip interface, even the high pressure of the fluid could not efficiently cool down the cutting edge and, therefore, its cooling effect was similar to the conventional system. Moreover, since the fluid injection when high pressure was used was made directed to chip-tool rake interface, the fluid did not reach flank face in a way to efficiently decrease its temperature. Therefore, the use of high-pressure cooling did not influence the flank wear rate and, consequently, did not cause tool life to increase consistently. This is not similar to what was verified by D’Addona and Raykar [24], whose work indicates that high-pressure jet could always be able to affect tool life in respect of Inconel 718, even when directed toward tool rake face.
In most of the conditions, neutral tool provided shorter tool lives than negative rake angle tool. This is because negative tools present bigger wedge angle, and then more volume to distribute cutting heat input, so that the temperature on the tool may be lower than when neutral tool was applied. Moreover, when the edge angle is smaller (which is the case of the neutral tool compared to the negative tool), the volume of tool material removed to obtain the same flank wear height is also smaller. Therefore, the volume of material removed from the tool to reach the same flank wear value (in the case of these experiments this value was 0.3 mm) was smaller for the neutral tool. These effects were probably more remarkable than the higher heat generation due to the increase of chip strain and friction contact area between tool and chip provided by the negative rake angle in comparison with neutral tooling. When conventional cooling was used, the increase of cutting speed caused the decrease of tool life. This effect of cutting speed on tool life is extensively reported in the literature [10]. The increase of cutting speed provides higher thermal input, but the area of the tool which is exposed to this heat is the same, so that the temperature on the tool increases and then tool life decreases. This effect can be clearly seen for the tests in which conventional cooling was used. Nonetheless, with high-pressure coolant, this influence was not evident. Probably, the improvement of cooling lubrication somehow overcame the negative effect of the increase of cutting speed on tool life. This means that the cross-effect between cooling condition and cutting speed was significant on tool life, although cooling condition itself was not, as it was cited before in this work.
Considering the ANOVA approach for tool life, every factor and each one of their interactions showed out to be statistically significant: cutting speed (F = 46.86), tool geometry (F = 46.68) and cooling condition (F = 11.51). Remember that the critical value of the F test for 95% confidence level is 5.32. It is quite interesting to point out that the interactions between cooling condition and cutting speed (F = 108.38) and between cooling condition and tooling (F = 96.33) showed considerably high effects, presenting F values even higher than those presented by each individual factor.
Figure 7 shows the worn flank face (with the flank wear obtained in the end of tool life) of one of the tools used in the experiments. It is a SEM picture of the tool after one of the tests in which conventional cooling, neutral tool and 70 m/min cutting speed were employed. No images of other experiments are presented because all of them seemed quite similar to each other.
EDS analysis taken in the points shown with numbers in Fig. 7a showed elements from tool coating, that are Ti, Al and Cr (points 1 and 2), from substrate, that are W and Co (point 5), and from workpiece material adhered, that are Fe, Ni and Cr (points 3 and 4). The detail shown in Fig. 7b also indicates the presence of parallel abrasive scratches on the tool flank face. Then, abrasion wear was probably the main mechanism that led to the removal of the tool coating, which facilitated the adhesion of the workpiece material on the flank wear. Without coating, some Ni-30 particles could adhere on the flank face and provided an even worse tool wear by attrition. Although cooling condition, tool geometry or cutting speed could accelerate or slow down tool wear, the same tool wear mechanisms were found in every experiment probably because of the high ductility and abrasiveness presented by this alloy. In other words, the high abrasiveness of the workpiece material (as it was seen in Fig. 2) caused an initial removal of the tool coating, which increased the friction coefficient of the tool. Besides that, the high ductility of the workpiece material (shown in Table 2) made possible the extrusion of some of the chip material (or material of the workpiece in the moment it was becoming chip) between tool and workpiece and the adhesion of it on the flank face, which was facilitated by the higher tool friction coefficient. After that, the relative movement between tool and workpiece promoted the cyclical removal and adhesion of this adhered material, which also removed tool particles, causing tool wear. The presence of abrasive particles on the tool stimulated this process and caused the abrasive scratches shown in Fig. 7b. Abrasion and adhesion wear were also observed as the prominent types of wear on the carbide inserts by Zahoor et al. [25] when machining Inconel 718.
Based on this tool wear phenomenon, in order to increase the productivity of turning process of alloys with thermal and mechanical properties similar to those of the Ni-30 alloy, it would be necessary to develop some tool material with a harder tool coating, in order to hinder the removal of it by the hard particles of the material, and with lower friction coefficient, in order to hinder the material adhesion on the tool flank face.
Moreover, it is important to emphasize that not only tensile strength, strain hardening ratio and thermal conductivity are important to establish the machinability of a given material, but also properties like ductility and abrasiveness must be considered, since they are very important in the definition of the tool wear mechanism.
4 Conclusions
Based on the results shown in this work, it can be concluded for the machining of the Ni-30 alloy in conditions similar to those used here that:
-
The use of high pressure cutting fluid provided lower cutting power than the use of conventional fluid injection. In most of the conditions tried, the use of a tool with neutral rake angle did not cause the cutting power to be lower than when negative rake angle tool was used.
-
The increase of flank wear did not always cause surface roughness to increase since it was not always followed by the variation of tool nose shape. When high pressure cooling was used, workpiece roughness was lower than when conventional cooling was used. Neither tool geometry nor cutting speed significantly influenced surface roughness.
-
The use of high pressure cooling did not influence the flank wear rate and, consequently, did not cause tool life to increase consistently. In most of the conditions, neutral tool provided shorter tool lives than negative rake angle tool. When conventional cooling was used, the increase of cutting speed caused tool life to decrease, but when high pressure cooling was used this influence was not significant.
-
Based on these results, the best set of conditions to be used in turning operations of Ni-30 alloys is high pressure cooling (to provide better surface roughness and lower cutting power), negative tool rake angle (to provide longer tool life) and high cutting speed (since when high pressure fluid was used, cutting speed did not influence tool life).
-
The main tool wear mechanism seen in these experiments were abrasion and attrition due to the high abrasiveness and ductility of the Ni-30 alloys. Therefore, a tool material to be used efficiently in the turning operation of this kind of alloy must have a hard tool coating, in order to hinder the removal of coating particles by the hard particles of the material, and low friction coefficient, in order to hinder the material adhesion on the tool flank face.
References
Choudhury IA, El-Baradie MA (1998) Machining nickel base superalloys: Inconel 718. Proc Inst Mech Eng B J Eng. https://doi.org/10.1243/0954405981515617
Baldan R (2009) Processamento e caracterização de rotores automotivos da superliga MAR-M247. Dissertation, Universidade de São Paulo
Yaedu AE (2003) Influência do substrato na deposição de Stellite 1 com plasma de arco transferido. Dissertation, Universidade Federal do Paraná
Frank RB (2005) Selection of age-hardenable superalloys. Adv Mater Process 163:37–42
Sato K et al (1998) Development of low-nickel superalloys for exhaust valves. SAE Tech Paper. https://doi.org/10.4271/980703
Nathal MV, Ebert LJ (1983) Gamma prime shape changes during creep of a nickel-base superalloy. Scr Metall Mater. https://doi.org/10.1016/0036-9748(83)90472-6
Ezugwu EO et al (2003) An overview of the machinability of aeroengine alloys. J Mater Process Technol. https://doi.org/10.1016/S0924-0136(02)01042-7
Stahl JE et al (2012) Metal cutting theories and models. Lund University Press, Lund
Trent EM, Wright PK (2000) Metal cutting. Butterworth-Heinemann, Woburn
Diniz AE et al (2014) Tecnologia da Usinagem dos Materiais. Artliber, São Paulo
Ferraresi D (1970) Fundamentos da Usinagem dos Metais. Blucher, São Paulo
Machado ÁR et al (2015) Teoria da Usinagem dos Materiais. Blucher, São Paulo
Buttery TC, Archard JF (1971) Some microscopical investigations of grinding and abrasive wear. J Microsc Oxf 94:13–24
Carpenter Technology (1987) NCF 3015 alloy. CRS Holdings Inc. https://www.carpentertechnology.com/en/product-solutions/cartech-ncf-3015-alloy/. Accessed 05 Nov 2019
Carpenter Technology (2000) 304/304L stainless. CRS Holdings Inc. https://www.carpentertechnology.com/en/product-solutions/cartech-304304l-stainless/. Accessed 05 Nov 2019
Carpenter Technology (2011) 718 alloy. CRS Holdings Inc. https://www.carpentertechnology.com/en/product-solutions/cartech-718-alloy/. Accessed 05 Nov 2019
Santos SC, Sales WF (2007) Aspectos Tribológicos da Usinagem dos Materiais. Artliber, São Paulo
SandvikCoromant (2019) NCF 3015 alloy. Sandvik Coromant do Brasil S.A. https://www.sandvik.coromant.com/pt-pt/knowledge/machine-tooling-solutions/tooling-considerations/pages/coolant.aspx. Accessed 05 Nov 2019
Magri A et al (2016) Evaluating the use of high-pressure coolant in turning process of Inconel 625 nickel-based alloy. Proc Inst Mech Eng B J Eng. https://doi.org/10.1177/0954405416664373
Diniz AE, Micaroni R (2007) Influence of the direction and flow rate of the cutting fluid on tool life in turning process of AISI 1045 steel. Int J Mach Tool Manuf. https://doi.org/10.1016/j.ijmachtools.2006.04.003
Diniz AE et al (2010) Evaluating the effect of coolant pressure and flow rate on tool wear and tool life in the steel turning operation. Int J Adv Manuf Technol. https://doi.org/10.1007/s00170-010-2570-1
Sharman ARC et al (2008) Surface integrity and tool life when turning Inconel 718 using ultra-high pressure and flood coolant systems. Proc Inst Mech Eng B J Eng. https://doi.org/10.1243/09544054JEM936
Cica D, Kramar D (2019) Multi-objective optimization of high-pressure jet-assisted turning of Inconel 718. Int J Adv Manuf Technol. https://doi.org/10.1007/s00170-019-04513-4
D’Addona DM, Raykar SJ (2020) Thermal modeling of tool temperature distribution during high pressure coolant assisted turning of Inconel 718. Materials. https://doi.org/10.3390/ma12030408
Zahoor S et al (2020) Environmentally conscious machining of Inconel 718: surface roughness, tool wear, and material removal rate assessment. Int J Adv Manuf Technol. https://doi.org/10.1007/s00170-019-04550-z
Acknowledgements
The authors would like to thank the Coordination of Superior Level Staff Improvement (Capes) for providing the scholarship, Villares Metals for providing the valve steels for the cutting tests and Sandvik Coromant, for providing the cutting tools.
Author information
Authors and Affiliations
Corresponding author
Additional information
Technical Editor: Lincoln Cardoso Brandao, Ph.D.
Publisher's Note
Springer Nature remains neutral with regard to jurisdictional claims in published maps and institutional affiliations.
Rights and permissions
About this article
Cite this article
Antonialli, A.Í.S., Carvalho, M.R.D.D. & Diniz, A.E. On the machinability of the Ni-30 high-temperature iron-based superalloy. J Braz. Soc. Mech. Sci. Eng. 42, 503 (2020). https://doi.org/10.1007/s40430-020-02588-9
Received:
Accepted:
Published:
DOI: https://doi.org/10.1007/s40430-020-02588-9