Abstract
The tribocorrosion behavior of 304 stainless steel was studied through comparing the damage behavior of 304 stainless steel in dilute sulfuric acid to that in distilled water by a reciprocating tribotester. The re-passivation behavior, the surface and sectional morphological features, as well as the change of microhardness of samples were studied, and the tribocorrosion mechanism was also discussed. The experimental results reveal that the damage of stainless steel in dilute sulfuric acid was caused by the steel’s mechanical removal and electrochemical dissolution. The wear mechanism of stainless steel is abrasive wear, which mainly consists of micro-cutting and peeling. The synergetic action between corrosion and wear is notable. The corrosive environment leads to the embrittlement of the surface layer, and the wear destroys the passivation film and causes galvanic corrosion.
Similar content being viewed by others
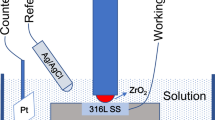
Avoid common mistakes on your manuscript.
1 Introduction
Generally, tribocorrosion refers to a phenomenon during which a solid suffers surface damage due to mechanical friction of other solids in a corrosive environment. In modern industry, many metallic parts, such as pumps, valves, turbines, engine cylinders and gears, are damaged early due to the combined effect of corrosion and wear in their service conditions [1, 2]. The issue of corrosion and wear has not only restricted the development of such industrial fields as marine industries, chemical engineering, bioengineering, mechanical processing, transportation and aerospace but has also caused a series of engineering problems for a long time. British scientists found that losses caused by corrosion of materials account for approximately 4–5% of the UK’s GDP, and that more than 70% of losses are related to the mechanical effect [3]. Accordingly, scholars have begun to pay attention to the tribocorrosion of materials, emphasizing the synergetic action between corrosion and wear to reduce the damage to materials.
In a corrosive and abrasive environment, the mutual activities of corrosion and wear can accelerate the damage to materials [4]. On the one hand, a metal starts to have its passivation film destroyed or undergo severe plastic deformation in corrosive media under the condition of mechanical wear, and the increased crystal defect density promotes a higher corrosive activity, thereby promoting corrosion [5]. On the other hand, corrosion has a certain role in promoting wear. During sliding contact, the soft surface first experiences plastic deformation; then, deformation accumulation brings low-cycle fatigue to the material, and the surface of the material starts to spall [6, 7], thus forming a large number of cracks on the worn surface. As a result, corrosion speeds up the expansion and propagation of cracks and promotes wear [8]. In addition, the surface and subsurface of a metal endure high strain and have a high strain gradient during the friction process [7], and plastic deformation decreases the size of surface grains, forming a nanocrystalline layer on the friction surface [9,10,11]. Therefore, corrosive media have a certain effect on the structure of a surface, as well as the subsurface, under friction [12].
The synergetic action between corrosion and wear has been recognized to some degree [13]. However, given that the tribocorrosion behavior of materials is closely related to the environment (temperature, composition of media and concentration), mechanical factors (e.g., load and speed), and material properties (composition, microstructure, and mechanical performance), the corrosive wear behavior of materials is highly complex, and much work should be done to understand the tribocorrosion mechanism. 304 stainless steel, characterized by low price, high corrosion resistance and good comprehensive mechanical performance, is widely used in some equipment exposed to corrosion. Nevertheless, its low hardness and poor wear resistance restrict its further use. In view of this, the current study intends to further understand the relationship between the tribocorrosion mechanism of metals and the metals’ service environment through studying the tribocorrosion behavior of 304 stainless steel affected by different environmental and mechanical factors.
2 Experimental
2.1 Material
304 stainless steel was used as the test material, and its main compositions are listed in Table 1.
The metallographic structure of 304 stainless steel, as presented in Fig. 1, was composed of polygonal equiaxed grains in which there were many twins inside the grains. The size of the grains was 10–30 μm.
2.2 Methodology
2.2.1 Tribocorrosion Tests
All tests were carried out by an MFW-05 reciprocating tribotester produced in Shunmao, Jinan, as presented in Fig. 2. The upper sample was a φ4 mm Si3N4 ball. The applied loads were 30 N, 60 N and 90 N, respectively. The reciprocating frequency was 0.5, 1 and 2 Hz, respectively. The reciprocation reached 3600 times. The one-way distance reached 10 mm. The test media were 0.5 mol/L H2SO4 and distilled water. The oxygen in both solutions was not removed during the tests. The samples with a size of 20 mm × 20 mm × 3 mm were ground to 1000# step by step by a SiC sand paper. Before tests, the samples were ultrasonically washed and dried by anhydrous ethanol and then weighed as W0 on the analytical balance with a precision of 0.1 mg. The samples were installed for tribocorrosion tests. After tests, the samples were again ultrasonically washed, dried and weighed as W1. The weight loss of corrosive wear was expressed by Wtotal= W0− W1. There were three repeated tests under each experimental condition, and the tribocorrosion resistance of the material was measured by the average of three Wtotal values.
2.2.2 Electrochemical Measurement
A Gamry Interface 1000 electrochemical workstation was applied to the electrochemical measurement based on a three-electrode system. The media were distilled water and 0.5 mol/L sulfuric acid. A saturated calomel electrode was used as the reference electrode, and a platinum sheet was used as the auxiliary electrode. The area of the working electrode was 1 cm2. The scanning range of the polarization curve measurement varied from − 0.5 to 1.5 V relative to the open-circuit potential, and the scanning rate was 0.166 mV/s.
Re-passivation curve measurement: First, the system potential was set at − 0.5 V relative to the open-circuit potential. After 5 min, the passivation film was removed. Then, the system’s potential was immediately adjusted to 0.2 V relative to the open-circuit potential. Current changes were recorded at the interval of 0.01 s. The measurement lasted 100 s.
The microstructure of the cross section: The samples tested underwent electroless nickel plating with the coating thickness of approximately 5 μm. Then, the samples were cut by a wire cutting machine from the middle of wear scars along frictional direction. After hot mounting, the samples were polished by a 1000# sand paper and diamond polishing paste and then electrochemically etched in 10 vol% oxalic acid (at 6 V for 50 s). Finally, the samples were observed through a Philips XL30 scanning electron microscope (SEM).
The surface morphology of wear scars was observed by the Philips XL30 SEM, and the distribution of elements on the surface of wear scars was measured by energy-dispersive X-ray spectroscopy (EDX).
A Leco LM 247 AT microhardness tester produced in the USA was used to measure the microhardness of the surface of samples and the cross section of wear scars. The load was set at 25 N, and the pressure-holding time was 15 s. The cross-sectional microhardness was first measured at 20 μm away from the surface of wear scars and then measured at intervals of 20 μm along the vertical wear direction inside the material. Eight points were measured in total.
3 Results
The weight loss data of the stainless steel in sulfuric acid and water are illustrated in Fig. 3. The following rules could be deduced from Fig. 3.
-
1.
The effect of the load: with the increase in the load, the weight loss of 304 stainless steel increased in different media and frequencies.
-
2.
The effect of the reciprocating frequency: with the increase in the reciprocating frequency, the weight loss of 304 stainless steel decreased in 0.5 mol/L H2SO4 under the same load; the trend was not obvious in distilled water, as the reciprocating frequency had little effect on the weight loss.
-
3.
The effect of environmental media: under the same load and frequency condition, the weight loss of 304 stainless steel in 0.5 mol/L H2SO4 was obviously higher than that in distilled water. The weight loss increased nearly 20 times under the condition of 30 N and 0.5 Hz, whereas it increased 2.5 times under the condition of 90 N and 2 Hz. Comparatively, the weight loss grew significantly under the condition of a light load and low frequency.
Figure 4 presents the friction factor of frictional pairs under different experimental conditions. As can be seen, the frictional pairs went through a running-in period at the beginning, and the friction factor started to be stable (a, b, c) when the reciprocating frequency reached approximately 200 times. Furthermore, the load and frequency had little influence on the friction factor, while experimental media had a great influence on the friction factor. For example, the friction factor of stainless steel in 0.5 mol/L sulfuric acid was smaller than that in distilled water (c). The friction factor varied from 0.30 to 0.35 and from 0.50 to 0.57 in 0.5 mol/L sulfuric acid and distilled water, respectively.
The surface morphology of the wear scars in 304 stainless steel is illustrated in Fig. 5. As shown in Fig. 5a, c, e, there was obvious plastic deformation on the surface of the wear scars in distilled water. As observed, irregular furrows appeared along the frictional direction. A small amount of the wear debris resulting from micro-cutting was repeatedly ground, and it remained on the worn surface. These were typical abrasive wear. With a growing load, the furrows became deeper and the plastic deformation got severer. The wear mechanism of the stainless steel in water mainly consisted of cutting, ploughing and plastic deformation. Judging from Fig. 5b, d, f, there were obvious signs of cutting and a large number of pits on the worn surface in the 0.5 mol/L sulfuric acid solution, with few shallow furrows. With increasing load, spalling became more serious. This indicated that the wear of stainless steel in the 0.5 mol/L sulfuric acid solution also belonged to abrasive wear, but the wear mechanism mainly consisted of cutting and brittle spalling.
4 Discussion
4.1 The Influence of Corrosive Media on the Subsurface Structure and Mechanical Performance of 304 Stainless Steel
The surface microhardness of the original stainless steel sample was 2.2 GPa. After 0.5 h of 0.5 mol/L H2SO4 corrosion, the surface microhardness was 2.0 GPa. The test results of the cross-sectional hardness of wear scars are illustrated in Fig. 6. Regardless of whether they were in 0.5 mol/L H2SO4 or distilled H2O, the subsurface hardness of samples was obviously improved after the wear test, and the material was work-hardened [14, 15]. With increasing distance from the surface of the wear scars, the hardness of the samples decreased gradually, and the influence of friction on the subsurface of the material exceeded 100 μm. On the near surface (20–40 μm), the average cross-sectional hardness of the samples was 3.3 GPa in 0.5 mol/L H2SO4 and 3.7 GPa in distilled water. It could be inferred that the sulfuric acid medium could reduce not only the surface strength of stainless steel but also the subsurface strength of the wear scars.
Figure 7 presents the cross-sectional microstructure of the wear scars in 304 stainless steel. It could be seen that the material on the near surface of wear scars underwent strong plastic deformation and formed a banded structure at 1 μm intervals. Mishra [16] and Meyers et al. [17, 18] proposed a model in which the material in a shear band structure undergoes grain refinement: homogeneous distribution of dislocation, elongated cell formation, dislocations blocked by subgrain boundaries, breakup of elongated subgrains, reorientation of subgrain boundaries, and formation of ultrafine grain sizes. As many studies [9,10,11,12] indicated, wear can cause significant changes in the subsurface structure of the materials. Typical three-layer structures were found near the subsurface: a nanoscale mechanical mixing layer, a gradient plastic deformation layer and a matrix layer. In addition, the stainless steel had a lamellar stripe in 0.5 mol/L H2SO4, and a number of submicron-grade peeling craters appeared in each layer (Fig. 8). According to the existing research and the results of this experiment, it was inferred that grain refinement occurred on the subsurface of stainless steel under the experimental conditions.
Based on the comparison between Fig. 7a, b and c, d, the banded texture of the wear scars in distilled water (approximately 10–15 μm) was thicker than that in the sulfuric acid solution (approximately 5–10 μm), which might be related to the release of certain stress during material spalling in the sulfuric acid solution. There were some defects on the subsurface, as indicated by red rings in Fig. 7a, b. Zavieh et al. [19, 20] studied the tribocorrosion behavior of austenitic stainless steel in a NaCl solution and also found holes on the subsurface of wear scars. They believed that a thicker passive film could impede the plastic flow of subsurface materials, and more materials superimposed each other to form a dislocation matrix, which eventually resulted in discontinuities of materials as well as voids and pits. According to the classic theory of delamination wear proposed by Suh [21], cracks were formed at the subsurface during the cyclic loading of a hard surface on a soft surface, and crack propagation caused exfoliation. Therefore, the subsurface defects were highly harmful to wear resistance. According to the results of microhardness, the surface morphology of the wear mark and the structure of the cross section, the corrosive medium embrittled the surface and subsurface of the stainless steel.
Jiang et al. [22, 23] proposed two ways of reducing surface strength of a material by corrosive media under corrosive and abrasive conditions: (1) Wear makes the material surface deformed and uneven, thus promoting local corrosion and increasing the amount of micro-crack initiation; (2) the reaction between crack-tip atoms and corrosive media reduces the bonding strength at the crack tip, which is advantageous to the expansion of cracks. In addition, hydrogen diffusion in the stainless steel would decrease the mechanical properties of the steel [24, 25]. Jiang et al. [26] studied the tribocorrosion behavior of a high-strength steel in 0.02 mol/L H2SO4 under a load of 50 N at the sliding speed of 0.15 m/s. They found that hydrogen penetrates into the subsurface of wear scars, resulting in a large increase in the material damage loss. Hydrogen embrittlement often occurs in the process of corrosion fatigue and stress corrosion cracking. Hydrogen atoms penetrate into the material along grain boundaries, which reduces the material strength and accelerates the fracture of the material. After grains on the worn surface are refined in a sulfuric acid solution, many defects are formed. Hydrogen atoms generated by corrosion reaction can be easily concentrated on grain boundaries and defects and penetrate into the worn subsurface along the grain boundaries and gather around the subsurface defects, thus resulting in decreased material strength. Therefore, it was inferred that hydrogen is the cause of embrittlement of the stainless steel in the sulfuric acid solution.
4.2 The Influence of Corrosive Media on the Surface State of Wear Scars
The electrochemical behavior of stainless steels was studied widely, which is strongly related to chemical compositions and microstructures of stainless steels and corrosive media [27, 28]. Figure 9 illustrates the polarization curves of samples in water and sulfuric acid. The open-circuit potential of stainless steel in water was − 0.18 VSCE, and three open-circuit potentials in sulfuric acid were − 0.37 VSCE, − 0.25 VSCE and − 0.02 VSCE, which meant that both samples were in the passivation state. The corresponding corrosion current density was 0.34 μA/cm2 for the stainless steel in water and 126, 17 and 1.8 μA/cm2 for the stainless steel in sulfuric acid.
Studies have demonstrated that the passivation behavior had an important effect on corrosion resistance of steels [29, 30]. Hu et al. [31] studied the effect of solution pH on electrochemical behavior of an ultra-high-strength steel in acidic environments. At pH 0–2, the reduction of H+ was the primary cathodic reaction. At pH 4, the reduction of oxygen dominated the cathodic process. At pH ≥ 4.2, the steel was passivated. In Fig. 9, although the samples were passivated both in water and sulfuric acid, the corrosion currents were very different; that was mainly caused by different depolarization reactions in the corrosion system.
The electrochemical corrosion mechanism of 304 stainless steel in sulfuric acid was as follows:
which is different from that in sulfuric acid. The anode reaction was the same, and the reaction of the cathode in water was as follows:
Being of excellent corrosion resistance, 304 stainless steel could spontaneously produce a thin and compact passivation film in the atmosphere as well as in the distilled water and 0.5 mol/L sulfuric acid environments. Its main component was Cr2O3 that reduced the corrosion rate. The passivation film experienced the process of continuous removal and regeneration during reciprocating wear. Therefore, the re-passivation of the metal was bound to affect the surface state of wear scars.
According to the model of the slip dissolution mechanism, the passivation film was broken down by the stress, which made the fresh metal expose in the corrosive environment. The fresh metal was continuously anodized, and the passivation film was reformed. The process that the fresh metal was continuously anodized and the passivation film reformed was called the re-passivation of the metal. In the Ford model [32], the process of re-passivation was typically characterized by the decay curve of the current density:
In formula (4), m is the slope of the passivation curve, i0 refers to the initial current density of a fresh metal’s surface dissolved in the environment, and t0 refers to the passivation time of the fresh metal. Because the passivation time of fresh metals was very short, it was considered to be close to 0. The greater the slope of the passivation curve was, the more the ability of the passivation film to form was. The result of the experiment was converted into the logarithmic coordinate curve of the current density and time, and the characteristic parameters m and i0 could be obtained [33].
Figure 10 is the re-passivation curves of the stainless steel in water and in sulfuric acid. The initial current density of re-passivation of the stainless steel in water was 0.032 mA/cm2 in water and 14.2 mA/cm2 in sulfuric acid, respectively. The slopes of the re-passivation curves were − 0.35 and − 1.38, respectively. The i0 of the stainless steel in sulfuric acid was very large, which indicated that the steel was corroded during the process of re-passivation. The i0 of the stainless steel in water was very small, indicating that the corrosion of the stainless steel in the process of re-passivation in water could be ignored. However, the re-passivation speed of stainless steel in sulfuric acid was higher than that in water, indicating that a passivation film could be formed quickly in sulfuric acid and that a relatively complete passivation film could be formed quickly on the surface of wear scars during reciprocating wear.
Generally, the factors that affect friction mainly include the physical properties of the contact surface, the chemical interaction of the sliding surface and the external environmental factors, and so on [34]. According to the results of the EDX analysis on the surface of wear scars (Table 2), the oxygen content of the worn surface of 304 stainless steel in 0.5 mol/L sulfuric acid is smaller than that in water, indicating that the passive film formed in sulfuric acid was easy to remove. The passivation film had a certain antifriction effect. Besides, in the acidic environment of the 0.5 mol/L H2SO4 solution, a large number of sulfate ions and hydrogen ions might have a tribochemical reaction with stainless steel, thereby forming a friction layer that could be easily sheared on the contact surface, separating the frictional pairs, and making the friction factor in 0.5 mol/L H2SO4 solution lower than that in distilled water.
4.3 Synergetic Action Between Corrosion and Wear
The total mass loss W total of corrosive wear could be divided into pure corrosion WC, pure wear WW and interaction between corrosion and wear ΔW [26]. The interaction amount ΔW can be divided into the increment of corrosion to wear ΔWW and the increment of wear to corrosion ΔWC.
In the static corrosion tests of 304 stainless steel, the weight loss caused by corrosion can be ignored. The current density of re-passivation of stainless steel in water was very low, and its dynamic corrosion in water could be ignored. The results could be concluded as follows:
The calculation results are illustrated in Fig. 11. It was obvious that the amount of interaction was very high, which accounted for the total weight loss of 56–95%.
According to the theoretical model of Archard abrasive wear, the wear amounts were related to the normal load and the hardness of the soft material. The formula was as follows:
where Wv is wear volume, Ka is abrasive wear factor, N is normal load, and H is hardness of soft materials.
According to formula (9), it was found that the weight loss of material wear was proportional to the load and inversely proportional to the hardness of the material. The hardness of the material’s surface and subsurface in 0.5 mol/L sulfuric acid was approximately 10% lower than that in water. Except for different environmental media, other experimental conditions were the same, and Ka was similar. It was inferred that the wear loss of stainless steel in 0.5 mol/L sulfuric acid was increased by approximately 10%. The total amount of interaction of 304 stainless steel was not obvious with the change of load, which meant that the increment of corrosion to wear was not significant (Fig. 11).
However, the amount of interaction between corrosion and wear of 304 stainless steel due to the change of frequency was quite obvious. With decreasing frequency, the interaction amount increased. Because the number of reciprocation is consistent, higher frequency leads to a shorter test time. With increasing time of the experiment, the amount of damage increased; this was the characteristic of corrosion. It was indicated that wear had an obvious promoting effect on corrosion, and the interaction mainly resulted from the promotion of wear on corrosion. On the one hand, the effect of wear on corrosion was caused by the electrochemical dissolution of the material during the process of re-passivation. On the other hand, the non-worn area as well as the non-peeling and peeling areas in the grinding mark was damaged by galvanic corrosion, which also accelerated the electrochemical dissolution of the material.
5 Conclusions
-
1.
In distilled water, the friction factor was within the range of 0.50–0.57, and the wear mechanism was abrasive, which mainly consisted of cutting, ploughing and plastic deformation. In the sulfuric acid solution, the friction factor was within the range of 0.30–0.35, and the wear mechanism was abrasive wear that mainly consisted of cutting and peeling.
-
2.
There was a strong plastic deformation zone in the near surface of the wear scar that formed a strip structure under all experimental conditions. Compared with distilled water, there was a thinner strip district on which a void and defects appeared, and the microhardness of the surface and subsurface of the grinding mark decreased in the sulfuric acid solution. The embrittlement of stainless steel in the sulfuric acid environment was the main reason that decreased its strength and wear resistance.
-
3.
The damage of stainless steel in the sulfuric acid solution was higher than that in the aqueous solution, and there was an obvious interaction between corrosion and wear. This interaction accounted for 56–95% of total damage, and it was mainly caused by the effect of wear to corrosion. The promotion of wear to corrosion was characterized by electrochemical dissolution and galvanic corrosion of the sample during the process of re-passivation.
References
A. Iwabuchi, J.W. Lee, M. Uchidate, Wear 263, 492 (2007)
J. Stojadinovic, L. Mendia, D. Bouvet, M. Declercq, S. Mischler, Wear 267, 186 (2009)
P. Ponthiaux, J. Celis, Tribo-Corrosion: Research, Testing, and Applications (ASTM International, West Conshohocken, 2013), p. 203
D. Landolt, S. Mischler, M. Stemp, S. Barril, Wear 256, 517 (2004)
Y.S. Yang, J.X. Qu, H.S. Shao, Tribology 16, 47 (1996)
A. Kapoor, F.J. Franklin, Wear 245, 204 (2000)
J. Chen, Q.N. Li, Q. Zhang, J. Chin. Soc. Corros. Prot. 34, 433 (2014). (in Chinese)
D.A. Rigney, X.Y. Fu, J.E. Hammerberg, B.L. Holian, M.L. Falk, Scr. Mater. 49, 977 (2003)
D.A. Rigney, M.G.S. Naylor, R. Divakar, L.K. Ives, Mater. Sci. Eng. 81, 409 (1986)
P. Heilmann, J. Don, T.C. Sun, D.A. Rignye, W.A. Glaeser, Wear 91, 171 (1983)
P. Heilmann, W.A.T. Clark, D.A. Rigney, Acta Metall. 31, 1293 (1983)
M. Favero, P. Stadelmann, S. Mischler, J. Phys. D Appl. Phys. 39, 3175 (2006)
Q. Zhang, The Influence of Heat Treatment on Corrosive Wear Behavior of AISI 310s Stainless Steel in Different Media. MS Dissertation, Jiangsu University, 2016 (in Chinese)
H. Zhao, Y. Ren, J. Dong, X. Fan, K. Yang, Acta Metall. Sin. (Engl. Lett.) 29, 217 (2016)
F. Dong, P. Zhang, J. Pang, Acta Metall. Sin. (Engl. Lett.) 29, 140 (2016)
A. Mishra, V. Richard, F. Gregori, R.J. Asaro, M.A. Meyers, Mater. Sci. Eng. A 410–411, 290 (2005)
V.F. Nesterenko, M.A. Meyers, J.C. Lasalvia, M.P. Bondar, Y.J. Chen, Y.L. Lukyanov, Mater. Sci. Eng. A 229, 23 (1997)
M.A. Meyers, V.F. Nasterenko, J.C. Lasalvia, Q. Xue, Mater. Sci. Eng. A 317, 204 (2001)
A.H. Zavieh, N. Espallargas, Tribol. Int. 103, 368 (2016)
A.H. Zavieh, N. Espallargas, Tribol. Int. 99, 96 (2016)
N.P. Shu, Wear 25, 111 (1973)
J. Jiang, M.M. Stack, Wear 261, 954 (2006)
J. Jiang, M.M. Stack, Tribol. Int. 35, 669 (2002)
Z. Zheng, Y. Yu, W. Zhang, Acta Metall. Sin. (Engl. Lett.) 30, 89 (2017)
Z. Huang, Q. Shi, F. Chen, Acta Metall. Sin. (Engl. Lett.) 27, 416 (2014)
X.X. Jiang, S.Z. Li, S. Li, Corrosive Wear of Metals (Beijing Chemical Industry Press, Beijing, 2003), pp. 241–246. (in Chinese)
L. Fan, Z. Liu, W. Guo, J. Hou, C. Du, X. Li, Acta Metall. Sin. (Engl. Lett.) 28, 866 (2015)
M. Sun, K. Xiao, C. Dong, X. Li, Acta Metall. Sin. 47, 442 (2011). (in Chinese)
L. Xu, J. Zhu, B. Wang, Acta Metall. Sin. 53, 677 (2017). (in Chinese)
R. Blair, B. Pesic, J. Kline, I. Ehrsam, K. Raja, Acta Metall. Sin. (Engl. Lett.) 30, 376 (2017)
Y. Hu, C. Dong, M. Sun, K. Xiao, P. Zhong, X.G. Li, Corros. Sci. 53, 4159 (2011)
F. Ford, Corrosion 52, 375 (1996)
B.C. Chen, A Study on Electrochemical and Mechanical Properties in Stress Corrosion Cracking Predication Model for Austenitic Stainless Steel Used in Nuclear Power Plants. MS Dissertation, Shanghai Institute of Materials (2009) (in Chinese)
D. Rigney, S. Karthikeyan, Tribol. Lett. 39, 3 (2010)
Acknowledgements
This work was supported by the National Natural Science Foundation of China (Grant No. 51275506).
Author information
Authors and Affiliations
Corresponding author
Additional information
Available online at http://springerlink.bibliotecabuap.elogim.com/journal/40195
Rights and permissions
About this article
Cite this article
Liu, M., Duan, DL., Jiang, SL. et al. Tribocorrosion Behavior of 304 Stainless Steel in 0.5 mol/L Sulfuric Acid. Acta Metall. Sin. (Engl. Lett.) 31, 1049–1058 (2018). https://doi.org/10.1007/s40195-018-0773-x
Received:
Revised:
Published:
Issue Date:
DOI: https://doi.org/10.1007/s40195-018-0773-x