Abstract
The mechanism of coal and gas outbursts tends to be more complex after entering the deep part of a coal mine from the shallow ground. As deep coal roadway outbursts change from gas-dominated to geostress-dominated, it is imperative to explore how to prevent outbursts of deep geostress-dominated coal roadways. Because the fracture zone of surrounding rocks in deep roadways is far larger than that in shallow roadways, this research considered the pressure relief field for a deep roadway. The first pressure relief field in the horizontal and vertical directions was 1.3 times and 2.05 times, respectively, greater than the roadway diameter based on data analysis, while the second pressure relief field in the horizontal and vertical directions was 1.8 and 2.8 times, respectively, greater than the roadway diameter. The range of the pressure relief of the second pressure relief field was 1.4 times greater than that of the first one in both the horizontal and vertical directions. With the action of the pressure relief field, the strip of the overlying coal roadway would produce a pressure relief area, a stress concentration area and the original coalbed area. Then, we proposed a dual pressure relief and outburst prevention model and applied it in the Qujiang Coal Mine. With the supplementation of hydraulic technology, this model released pressure from the floor rock roadway and drilled boreholes across beds to extract gas. The application showed that releasing pressure in the strip zone of the coal roadway was very effective in preventing an outburst. The hazards produced by both the geostress of the roof and floor rocks and the coalbed gas were removed so that the coal roadway could be excavated in a safe and rapid manner.
Similar content being viewed by others
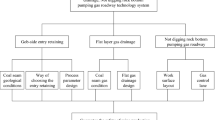
Avoid common mistakes on your manuscript.
Introduction
According to statistics, during the process of excavating coal roadways, coal and gas outbursts (outbursts) account for more than 75% of all accidents. Therefore, outburst prevention and control (outburst prevention) are key priorities for coal mines. Shallow coal seams have low geostress values. Outburst prevention in coal roadways mainly includes protective seam mining (Cheng et al. 2020; Ren et al. 2019; Yan et al. 2018; Li 2020) and regional outburst prevention, i.e. pre-drainage of coalbed gas. In most cases, pre-drainage happens through surface vertical wells (Hu and Sun 2014), surface horizontal wells (Chen et al. 2019a, b; Guo et al. 2019), boreholes drilled across layers (Lu et al. 2015; Qin et al. 2020a, b) and boreholes drilled along the seam (Karacan et al. 2007). To improve the effect of pre-drainage, scholars have proposed hydraulic flushing (Zou et al. 2014; Zhang et al. 2019a, b), hydraulic cutting (Zou et al. 2017; Zheng et al. 2018; Jun et al. 2019), hydraulic fracturing (Hu et al. 2020; Jiang et al. 2019; Liang et al. 2017; Bai et al. 2018), CO2 fracturing (Yang et al. 2019; Zhang et al. 2017a, b), high-pressure air blasting (Zhu et al. 2016) and other anti-reflection technologies. The gas permeability of the coal seam and the mining effect of coalbed gas, which are beneficial for safe excavation in coal roadways, have been improved. However, once the geostress and gas pressure in deep coal seams increase, the surrounding rocks will experience large deformations, fractured zones and sudden dynamic response changes (Xie et al. 2018; Wang et al. 2018a, b; Charles 2017; Tan et al. 2019), and the risk of an outburst in deep coal roadways will grow. In addition, the occurrence mechanism and type of outburst will become so complex that new characteristics different from those of the shallow portion will appear. To be specific, the outbursts in coal roadways will change from gas-dominated in shallow areas to geostress-dominated in deep areas, or they will be complex dynamic disasters (Kang et al. 2018; Pan 2016; Wei and Zhang 2020); further, the gas-dynamic phenomenon will occur, even when coalbed excavation meets the given standards, and the predictive indicators will be lower than the threshold values (Hu and Wen 2013).
In terms of the new characteristics of an outburst that occurs in a deep coal roadway, we can adopt traditional outburst prevention measures, such as pre-drainage of the coalbed gas in the deep floor rock roadway to reduce the gas hazard at the coal seams. However, this method can hardly reduce the geostress hazard of the roof and floor rock strata. This is why geostress-dominated outbursts occur even when the gas extraction in deep coal seams meets the given standards. Therefore, outburst prevention in deep coal roadways should be able to reduce the hazards produced by both the coalbed gas and the geostress of the roof and floor rock strata. Although current anti-reflection technologies can increase the gas permeability of coal seams and reduce the hazards of coalbed gas, they have poor performance in decreasing the geostress hazards of the roof and floor rock strata, and they still need to be improved. For example, deep-hole loosening blasting uses complex technologies, hydraulic fracturing often concentrates local stresses, and hydraulic cutting can only produce a small range of pressure relief. In recent years, scholars have conducted numerous studies on the characteristics of deep surrounding rock failures through field investigations (Zhang and Song 2020), theoretical analysis (Xie 2019), laboratory experiments (Wang et al. 2018a, b; Qin et al. 2020a, b) and numerical simulations (Gao et al. 2019). Their results show that zonal disintegration occurs in deep surrounding rocks (Zhang et al. 2017a, b; Chen et al. 2019a, b). In addition, some studies have shown that the scope of zonal disintegration in deep surrounding rocks was much larger than that in the shallow portion. The failures and deformations of the surrounding rocks in roadways should be reduced as much as possible. For outburst prevention in deep coal roadways, zonal disintegration in deep surrounding rocks can decrease the geostress and increase the deformation in coal seams, and it is helpful for drilling for outburst prevention, gas extraction and reduction in the outburst prevention workload. Therefore, we propose the use of the zonal disintegration in deep surrounding rocks to arrange the coal roadways to be excavated within the range of the pressure relief influences of zonal disintegration in floor rock roadways. We also propose the release of the geostress of overlying coal seams in advance to increase the deformation of coal seams and reduce the geostress hazard. If the pressure relief fails to meet expectations in some areas, hydraulic technology can be used to peel coal off and drain the seam. At the same time, we should drill boreholes across layers for gas extraction to remove geostress and gas hazards.
For outburst prevention in geostress-dominated deep coal roadways, this paper proposes three outburst prevention measures including pressure relief for floor rock roadways, hydraulic technology and gas extraction by drilling boreholes across layers based on several research methods, such as theoretical analysis, numerical simulation and field tests. We built a dual pressure and outburst prevention model for floor rock roadways and applied it on site to obtain new outburst prevention methods in the strip zones of deep coal roadways for future reference.
The pressure relief field of surrounding rocks in deep roadways
Based on the theory of loose surrounding rock circles, under the action of dynamic and static forces generated during the process of excavation, surrounding rocks in shallow roadways include a crushing zone, a plastic softening zone, plastic hardening zone and an elastic zone, as shown in Fig. 1a. With high geostress levels, surrounding rocks in deep roadways will produce a pressure relief zone (see Fig. 1a) once they are excavated. Then, the plastic zone will develop towards the deep portion (see Fig. 1b), and an extension fracture will occur when the elastic property transforms into the brittle property (see Fig. 1c). In the end, zonal disintegration alternatively occurs in the broken zone and the integrated zone (see Fig. 1d) (Chen et al. 2010). Therefore, the loose circle of the surrounding rock in shallow roadways is simply the first fracture zone of zonal disintegration in deep roadways, which means the scope of the fracture zone of the surrounding rocks in deep roadways is much larger than that in shallow roadways.
Generally, for the arrangement of traditional floor rock roadways, at 15~25 m (the difference between the internal and external horizontal distances is usually 10~30 m) under the coal seam, no pressure relief effect can be produced on the overlying coal seam. However, the fracture zone of the surrounding rocks in deep roadways is able to effectively release the pressure of overlying coal seams. Meanwhile, research has shown that in the floor rock roadway, an area in which the stress decreases by more than 5% has a better pressure relief effect on the surrounding rocks of the roadway (Lu et al. 2012). Generally, a range of 2–6 times the roadway diameter can be affected (Lan n.d.). An area of deformation of the surrounding rocks of more than 3‰ has a better pressure relief effect on the overlying coal seam (Wang 2016). Therefore, we refer to the area where the stress decreases by more than 5% and the surrounding rocks deform by more than 3‰ as the pressure relief field of the surrounding rocks in deep floor rock roadways, as shown in Fig. 2. We hope the pressure relief effect produced by the pressure relief field of the surrounding rocks in deep roadways can provide new outburst prevention methods for strip zones in coal roadways.
Numerical analysis of the distribution characteristics of the pressure relief field
Engineering background and 2
The software FLAC3D was used for this simulation test and the constitutive relationship of the surrounding rocks followed the Mohr–Coulomb criterion. A schematic diagram of the 3D model is shown in Fig. 3. Floor rock roadway 213 was arranged under coal roadway 213. The fault surface of floor rock roadway 213 was a vertical wall with a semi-circular arch. The roadway was 4 m wide, the vertical wall was 1 m tall, and the radius of the circular arch was 2 m. Shaped in a rectangle, the fault surface of coal roadway 213 was 4 m wide and 3 m tall. The inclination of the coalbed was 15°. The burial depth and the thickness of the coal seam were 1000 m and 3 m, respectively. For the 3D numerical model in Fig. 4, the X-axis was the strike of the coal seam, while the Y-axis was the dip of the coal seam. With the length, width and height all being 100 m, the mesh was 2 × 2 × 2 m. Both the coal roadway and the floor rock roadway were simulated with null units. A tetrahedron mesh cells and a bottom constraint were applied to the displacement of the model. All surfaces were free surfaces with a uniformly distributed load. The physical and mechanical parameters of the coal seams were measured (Table 1).
According to the requirement of outburst prevention, the coal roadway cannot be excavated until it reaches the standard. Thus, we simulated and analysed the distribution characteristics of the pressure relief field in the floor rock roadway after the floor rock road, and the coal roadway were sequentially excavated (first pressure relief and second pressure relief). Through theoretical analysis, we found that pressure relief performed best when the coal roadway was directly under the floor rock roadway. To analyse the pressure relief effect at different distances between the two, we simulated, monitored and analysed changes in the horizontal and vertical stresses and displacements of the surrounding rocks of the overlying rock seam in the floor rock roadway after the floor rock roadway, and the coal roadway were sequentially excavated; the coal roadway was 8, 10, 15 and 25 m under the floor rock roadway. Finally, we obtained the distribution characteristics of the pressure relief field in the floor rock roadway (first pressure relief field and second pressure relief field), and the results provide a theoretical basis for how to select a reasonable spatial location for floor rock roadways. The monitoring line settings are shown in Fig. 5.
Results and analysis
First pressure relief field
After excavation of the floor rock roadway began, by calculating the horizontal and vertical (monitoring lines 1 and 2) stresses and displacements of the overlying surrounding rocks, we drew curves with decreasing amplitudes of the vertical stress and deformation of the surrounding rocks for the first pressure relief field of the floor rock roadway (Figs. 6 and 7). Because the deformation 3 m above the surrounding rock and within 3 m on both sides of the centreline was far more than 3‰, which had no impact on the analysis, the deformation within this range is not reflected in the figure.
Figure 6a indicates that the decrease in the vertical stress within 15 m of the upper and lower portions of the floor rock roadway gradually lessened and was finally steady from the centreline of the roadway to both sides, with the largest decreasing amplitude being 27% and the decreasing amplitude at 5.4 m and 5.7 m of the upper and lower portions being 5%. The stress increased at 5.4~15 m of the upper portion and 5.7~15 m of the lower portion, with the largest increasing amplitude being 4%. Figure 6b shows that the decrease in the vertical stress of the rock seam within 15 m above the floor rock roadway gradually lessened, with the decreasing amplitude being 6%~73%. As shown in Fig. 7a, the deformation of the surrounding rocks at the upper and lower portions of the floor rock roadway decreased gradually from the centreline of the roadway to both sides. In particular, the surrounding rocks deformed by 3‰ at 5.2 and 5.5 m of the upper and lower portions, respectively. Figure 7b shows that the surrounding rocks above the roadway deformed less and less, with the deformation at 8.2 m being 3‰. Upon analysis, we knew that the first pressure relief field was at 5.2 and 8.2 m of the two portions and above the floor rock roadway, 1.3 and 2.05 times greater than the roadway diameter, respectively.
Second pressure relief field
After excavation of the floor rock roadway began, by calculating the horizontal and vertical (monitoring lines 3 and 4) stresses and displacements of the overlying surrounding rocks, we drew curves with decreasing amplitudes of the vertical stress and deformation of the surrounding rocks for the second pressure relief field of the floor rock roadway when the floor rock road was 8, 10, 15 and 25 m away from the coal roadway (Figs. 8 and 9).
The vertical stress of the surrounding rocks 15 m from both sides of the middle point of the centreline of the coal roadway floor decreased by 51~80%, as shown by the “notching” curve (Fig. 8a). The affected scope was 8.5 and 10 m. The stress within 7.5 m from both sides decreased by 5%. The vertical stress of the surrounding rocks at the centrelines of the coal roadway and the floor rock roadway declined to produce a “convex” curve (Fig. 8b). This means that the vertical stress in the middle dropped less, while that on both sides decreased more, between 39 and 100%. As shown in Fig. 9a, the deformation of the surrounding rocks within 15 m of the upper and lower portions above the centreline of the coal roadway floor decreased gradually from the middle to both sides. In particular, the surrounding rocks deformed by 3‰ at 7.1 m and 7.2 m of the upper and lower portions. Figure 9b shows that the surrounding rocks directly below the centreline of the coal roadway floor deformed less and less. When the vertical distance between seams was 8, 10 or 15 m, the surrounding rocks deformed by more than 3‰; when the vertical distance between the seams was 25 m, the surrounding rocks within 14 m of the centreline of the coal roadway floor deformed by more than 3‰. We found that the second pressure relief field was 7.1 and 14 m below the floor rock roadway and the two portions 1.8 and 2.8 times greater than the roadway diameter, respectively.
Construction of the dual pressure relief and outburst prevention model and analysis on the effect and application of pressure relief on site
Construction of the dual pressure relief and outburst prevention model for floor rock roadways
Based on the research mentioned above, in the vertical direction, we arranged the coal roadway to be excavated within the range of the pressure relief zone of the surrounding rocks in the floor rock roadway (the vertical distance between the two h was generally 2–6 times the roadway diameter R), to reduce the geostress hazard of the roof and floor rock strata in the coal roadway to be excavated. In the horizontal direction, we divided the overlying coal seams into a pressure relief zone, a stress concentration zone and the original coal seam zone. For the stress concentration zone and the original coal seam zone, we used hydraulic technology to drain some coal from the seam to further reduce the geostress hazard. For soft coal seams (firmness coefficient of coal f ≤ 0.5) and hard coal (firmness coefficient of coal f > 0.5) seams, hydraulic reaming technology and hydraulic cutting seam technology were, respectively, adopted (Yuan 2018). In addition, we excavated gas from the strip zone of the coal roadway by drilling holes across layers to reduce the gas hazard of the coal seam, which could remove both geostress and gas hazards of the strip zone in the coal roadway (Fig. 10).
(1) Safe excavation of the floor rock roadway. Before excavating, based on the principle of “exploration first”, the geological conditions and the occurrence of the coal seam should be explored by drilling and geophysical prospecting to ensure that the distance between the floor rock roadway and the coal seam is reasonable. During the process of excavation, an acoustic emission detector, roof abscission layer monitor and other instruments are used to monitor the stability of the surrounding rocks in the floor rock roadway, and a gas monitoring system is used to monitor the gas concentration of the return current in the floor rock roadway. Then, the three aspects mentioned above are comprehensively analysed to determine if they are normal. Safety measures are performed if necessary to ensure safe excavation of the floor rock roadway.
(2) Evaluation of the effect of preventing and controlling gas and geostress hazards. To evaluate the gas hazard, we should test the residual gas content. The critical value of the residual gas content in normal areas is 8 m3/t, while that in geologic structure zones is 6 m3/t. For the geostress hazard, the mass of the coal drained on site and the deformation of the coal seam are calculated, and the values are compared with the critical values of the indicator. The critical value of deformation in the original coal seam zone is 3‰, while the critical values in the pressure relief and stress concentration zones are the respective stress coefficients times 3‰. The outburst prevention effect in the strip zone of the coal roadway can be determined effective only when both the geostress and gas indexes reach the standard.
Model verification and measurement analysis of pressure relief in floor rock roadways
Test scheme
The test was conducted in coal roadway 213 of the Qujiang Coal Mine, Fengcheng, Jiangxi, China. The test zone was arranged 10 m above floor rock roadway 213, and the length was 370 m. The distance between the boreholes drilled across layers was 4 m. For the original coal seam, the gas pressure was 9.0 MPa, the gas content was 15.3 m3/t, the coal permeability coefficient was 0.004 m2/(MPa2·d), and the coal firmness coefficient was 0.23. The purpose of this test was to evaluate the effect of geostress pressure relief and outburst prevention for gas extraction in the coal seams within 15 m of the upper and lower portions of the overlying coal and rock mass of floor rock roadway 213. The test content and test method are listed in Table 2. Each parameter included five test holes (Fig. 11).
Results and analysis
(1) Effect of geostress pressure relief
Figure 12 shows the results of the geostress pressure relief parameters. The complete rock and the broken rock are shown in Figs. 12a and b, respectively. As shown in Fig. 12c, there were four fracture zones for the surrounding rocks within 6.8 m of the roadway, which is 1.7 times greater than the roadway diameter. Figure 12d indicates that different test points of the same drill hole showed wave crests and troughs from outside to inside. In particular, the crest with the largest displacement was the fracture zone, and the trough with the least displacement was the integration zone, which is consistent with the law based on physical simulations in the laboratory (Zhang et al. 2009; Xu and Yuan 2015). These results indicated zonal disintegration inside the surrounding rocks after excavation of the roadway began. The cumulative deformations of test holes 1~5# on the surrounding rocks of the roadway were 4.1, 7.7, 9.3, 10.3 and 6.1‰, respectively, which were all greater than 3‰. These results indicated that the geostress hazard of the coal seam within 15 m of the upper and lower portions of the overlying coal seam in the floor rock roadway had been removed. By comparing with the numerical simulation results mentioned above, we found that the area with surrounding rocks that had deformed by more than 3‰ was larger than the numerical simulation result. This was because the blasting driving technique was used in the floor rock roadway, which produced shock waves in the surrounding rocks, increasing the deformation of these surrounding rocks. In addition, the deformation test lasted for 3 months. The rheological effect over time also increased the deformation of the surrounding rocks in the roadway. Thus, the measured deformation of the surrounding rocks was larger than the numerical simulation result. These factors improved the effect of pressure relief in the floor rock roadway. Therefore, it is unnecessary to use the hydraulic technology in this area.
(2) Effect of outburst prevention for gas extraction
Figure 13 presents the results of the outburst prevention parameters for gas extraction. Figure 13a and b shows that the coal permeability coefficient and gas extraction radius increased less and less from directly above to both sides within 15 m above the floor rock roadway. In particular, the coal permeability coefficient increased by 9.1~55.7 times, and when the process lasted for 15, 30, 60 and 90 days, the gas extraction radius increased by 52~84%, 47~76%, 44~69% and 43~67%, respectively, with the average increasing being more than 50%, which could reduce the drilling workload by 50% on average. As shown in Fig. 13c, 11 drill holes contained residual gas after excavation, for a total of approximately 4.05~5.31 m3/t, which is less than the critical value of 8 m3/t. As shown in Fig. 13d, when 370 m of the roadway was excavated, the gas desorption index of drill cuttings K1 was 0.08~0.38 mL/g·min1/2, which is less than the critical value of 0.5 mL/g·min1/2, and the amount of drill cuttings S was 2.5~4.2 kg/m, which is less than the critical value of 6 kg/m. The results of comprehensive analysis indicated that the gas hazard had been removed. At the same time, the excavation speed was significantly improved from 45 to 105 m/month.
Discussion
Because removing gas hazards cannot effectively prevent geostress-dominated outbursts in deep coal roadways, we proposed simultaneously removing the geostress and gas hazards, which provides a new method for outburst prevention in deep coal roadways. Because the zonal disintegration of surrounding rocks in deep roadways is characterized by a large scope of fracture and effective pressure relief, we defined the area with a deformation of more than 3‰ and a stress decrease of more than 5% of the surrounding rocks as the pressure relief field of the floor rock roadway. This technique was successfully applied in preventing outbursts in the strip zone of a coal roadway, and it can effectively remove the geostress hazard generated by the roof and floor rock strata and the coalbed gas hazard to achieve safe and rapid excavation of coal roadways. However, the research still needs to be improved. First, the pressure relief field of the floor rock roadway has a rheological effect over time (Cao 2020). Further research on the effect of pressure relief on the overlying coal roadway is required. Second, this model only considers the test effect under certain conditions. It is necessary to further explore the effect of pressure relief for outburst prevention given changes in the gas geological conditions (such as the inclination of the coal seam, the lithology, the thickness of the coal seam, the lateral pressure coefficient, the burial depth and the geological structure). Third, in addition to the effect of pressure relief for outburst prevention in terms of the single factors of geostress and gas, the coupling effect of these two factors needs to be explored.
Conclusion
(1) By analysing the differences between the fracture zones of deep and shallow surrounding rocks, we found zonal disintegration among the surrounding rocks in deep roadways, and the range of the fracture zone was much larger than that in shallow roadways. The stress of the floor rock roadways decreased by more than 5%. We defined the area where the surrounding rocks deformed by more than 3‰ as the pressure relief field of the surrounding rocks in the deep floor rock roadway. This provides a new method for outburst prevention in deep coal roadways.
(2) By conducting numerical analysis on the stress decrease and deformation of the surrounding rocks in the floor rock roadway, we obtained the range of pressure relief in both the horizontal and vertical directions of the first pressure relief field as 5.2 m and 8.2 m, respectively; this range is 1.3 and 2.05 times greater than the roadway diameter, respectively. The range of the pressure relief in both the horizontal and vertical directions of the second pressure relief field was 7 m and 14 m, respectively; this range is 1.8 and 2.8 times greater than the roadway diameter, respectively. Thus, the range of pressure relief in both the horizontal and vertical directions of the second pressure relief field was 1.4 times that of the first pressure relief field. These results provide a theoretical basis for how to select a reasonable location for the floor rock roadway.
(3) We utilized the pressure relief effect of the zonal disintegration in deep roadways as well as hydraulic technology and the method of excavating by drilling holes across layers to build the dual pressure relief and outburst prevention model for deep floor rock roadways. The application of this model, which was successful, indicated that there was zonal disintegration among the surrounding rocks in the floor rock roadway. The surrounding rocks deformed by 4.1~10.3‰. The excavation radius within 15 m of the upper and lower portion of the coal roadway increased by more than 50% on average, which reduced the drilling workload by 50%. Both the gas desorption index K1 and the S value were less than the critical values. The excavation speed was improved 1.3 times, and the geostress and gas hazards in the strip zone of the coal roadway were removed to achieve safe and rapid excavation of the coal roadway.
References
Bai X, Wu C, Liu X, et al(2018). Analysis of the tempo-spatial effects of hydraulic fracturing by drilling through underground coal mine strata on desorption characteristics. Energy Science & Engineering.
Cao JJ (2020) Research on the method of coal and gas outburst prevention by floor roadway pressure relief and gas drainage in deep coal seam roadway strip. Anhui University of Sci Technol
Chen J, Zhu C, Zhang Y (2010) Elastic-plastic-brittle analysis of zonal disintegration within rock mass in deep tunnel. J China Coal Soc 35:541–545
Chen S, Tang D, Tao S et al (2019a) Current status and key factors for coalbed methane development with multibranched horizontal wells in the southern qinshui basin of china. Energy Sci Eng 5:1572–1587
Chen H, Qi C, Wang S et al (2019b) A simple gradient model for zonal disintegration of the surrounding rock around a deep circular tunnel. Tunn Undergr Space Technol 91:38–47
Cheng X, Zhao GM, Li YM et al (2020) Evolution of overburden mining-induced fractured zone and pressure-relief gas drainage in soft rock protective seam. J Mining and Safety Eng 37(3):533–542
Charles F (2017) Some challenges of deep mining. Engineering 3(4):210–232
Gao Q, Zhang Q, Xiang W (2019) Mechanism of zonal disintegration phenomenon (zdp) around deep roadway under dynamic excavation. Geotech Geol Eng 37:25–41
Guo X, Deng C, Fan Y et al (2019) Experimental research on leaf vein geometric characteristics of multibranch horizontal well for coalbed methane recovery. Energy Sci Eng:1–15
Hu Q, Sun H (2014) Graded optimization design method on surface gas drainage borehole. J China Coal Soc 39:1907–1913
Hu Q, Wen G (2013) The mechanical mechanism of coal and gas outburst. Science Press, Beijing, pp 32–37
Hu QT, Liu L, Li QG et al (2020) Experimental investigation on crack competitive extension during hydraulic fracturing in coal measures strata. Fuel.
Jiang Z Z, Li Q G, Hu Q T, et al(2019). Underground micro-seismic monitoring of a hydraulic fracturing operation for coalbed methane (CBM) reservoirs in a coal mine. Energy Science & Engineering.
Jun X, Yun PL, Zou Q et al (2019) Elimination of coal and gas outburst risk of low-permeability coal seam using high-pressure water jet slotting technology: a case study in shihuatian coal mine in guizhou province, china. Energy Sci Eng 7:1394–1404
Kang H, Wang G, Jiang P et al (2018) Conception for strata control and intelligent mining technology in deep coal mines with depth more than 1000m. J China Coal Soc 43:1789–1800
Karacan C, Diamond WP, Schatzel SJ (2007) Numerical analysis of the influence of in-seam horizontal methane drainage boreholes on longwall face emission rates. Int J Coal Geol 72:15–32
Lan T W(2012). Research on the geodynamic condition and prevention technology of rockburst in Datai Mine. Liaoning Technical University
Li JG (2020) Acoustic emission monitoring and early warning method for stress-dominated coal-gas dynamic disasters in deep mines. J Shandong University of Sci Technol (Nat Sci) 39(4):20–27
Liang YP, Cheng YH, Zou QL et al (2017) Response characteristics of coal subjected to hydraulic fracturing: an evaluation based on real-time monitoring of borehole strain and acoustic emission. J Nat Gas Sci Eng 38:402–411
Lu SQ, Cheng YP, Wang HF et al (2012) Numerical simulation research on the Hongling Coal Mine’s minimum mining thickness of upper protective layer. J China Coal Soc 37(S1):43–47
Lu TK, W Z, Yang HM et al (2015) Improvement of coal seam gas drainage by under-panel cross-strata stimulation using highly pressurized gas. Int J Rock Mech Min Sci 77:300–312
Pan Y (2016) Integrated study on compound dynamic disaster of coal-gas outburst and rockburst. J China Coal Soc 41:105–112
Qin B, Wei G, Lou Z, et al(2020a). A new cross-borehole hydraulic caving technique in the coal seam with a soft layer for preventing coal and gas outbursts during coal roadway excavation. Energy Science & Engineering.
Qin ZC, Nie W, Liu YL, Zhang YB, Liu LN (2020b) Location selection of lower layer mining roadway in thick coal seam bifurcation area. J Shandong University of Sci Technol (Nat Sci) 39(3):43–49
Ren WG, Zhou HW, Xue DJ et al (2019) Mechanical behavior and permeability of coal and rock under strong mining disturbance in protected coal seam mining. J China Coal Soc 44(5):1473–1481
Tan Y, Fan D, Liu X et al (2019) Numerical investigation of failure evolution for the surrounding rock of a super-large section chamber group in a deep coal mine. Energy Sci Eng:1–23
Wang ZH (2016) Methods of destressing and increasing penetration at pre-excavated rock roadway under floor. China Coal 42(6):101–104
Wang DY, Li XB, Peng K, Ma CD, Zhang ZY, Liu XQ (2018a) Geotechnical characterization of red shale and its indication for ground control in deep underground mining. J Cent South Univ 25(12):2979–2991
Wang MY, Chen HX, Li J et al (2018b) Theoretical research on zonal disintegration of rock masses around deep tunnels and comparisons with in-situ observations. Chin J Rock Mech Eng 37(10):2209–2218
Wei MR, Zhang SW (2020) Simulation study of maximum bolt supporting capacity during dynamic disaster. J Shandong University of Sci Technol (Nat Sci) 39(4):37–45
Xie HP (2019) Research review of the state key research development program of China: deep rock mechanics and mining theory. J China Coal Soc 44(5):1283–1305
Xie H, Gao M, Zhang R et al (2018) Study on the mechanical properties and mechanical response of coal mining at 1000 m or deeper. Rock Mech Rock Eng 6:1–16
Xu Y, Yuan P (2015) Model test of zonal disintegration in deep rock under blasting load. Chin J Rock Mech Eng 34:3844–3851
Yan H, Zhang JX, Ju Y et al (2018) Fracture development rules controlled by backfill body’s compression ratio and gas drainage technology under upper protective layer mining. J Mining and Safety Eng 35(6):1262–1268
Yang X, Wen G, Lu T et al (2019) Optimization and field application of co2 gas fracturing technique for enhancing cbm extraction. Nat Resour Res 7:3186–3203
Yuan BQ (2018) Application conditions and evaluation indexes of hydraulic permeability enhancement technology in coal Roadway strip mining. Coal Mine Safety 49(12):164–168
Zhang JW, Song ZX (2020) Mechanical response and failure characteristics of deep sandstone under triaxial loading and unloading. J Mining and Safety Eng 37(2):409–418+428
Zhang Q, Chen X, Lin B et al (2009) Study of 3d geomechanical model test of zonal disintegration of surrounding rock of deep tunnel. Chin J Rock Mech Eng 28:1757–1766
Zhang XW, Lu YY, Tang JR et al (2017a) Experimental study on fracture initiation and propagation in shale using supercritical carbon dioxide fracturing. Fuel 190:370–378
Zhang Q, Zhang X, Wang Z, Xiang W, Xue J (2017b) Failure mechanism and numerical simulation of zonal disintegration around a deep tunnel under high stress. Int J Rock Mech Min Sci 93:344–355
Zhang R, Cheng Y, Yuan L, Zhou H, Wang L, Zhao W (2019a) Enhancement of gas drainage efficiency in a special thick coal seam through hydraulic flushing. Int J Rock Mech Min Sci 124:104085
Zhang H, Cheng Y, Yuan L et al (2019b) Hydraulic flushing in soft coal sublayer: gas extraction enhancement mechanism and field application. Energy Sci Eng 7:1–24
Zheng C, Lin B, Kizil MS, Aminossadati SM, Li H, Chen Z (2018) Analysis on the multi-phase flow characterization in cross-measure borehole during coal hydraulic slotting. Int J Min Sci Technol 28:701–705
Zhu W, Gai D, Wei CH et al (2016) High-pressure air blasting experiments on concrete and implications for enhanced coal gas drainage. J Natl Gas Sci Eng 36:1253–1263
Zou QL, Lin BQ, Liu T, Zhou Y, Zhang Z, Yan FZ (2014) Variation of methane adsorption property of coal after the treatment of hydraulic slotting and methane pre-drainage: a case study. J Natl Gas Sci Eng 20:396–406
Zou QL, Li QG, Liu T et al (2017) Peak strength property of the pre-cracked similar material: implications for the application of hydraulic slotting in ECBM. J Nat Gas Sci Eng 37:106–115
Acknowledgements
This research was financially supported by the national key research and development programme of China (2017YFC0804206).
Author information
Authors and Affiliations
Corresponding author
Ethics declarations
Conflicts of interest
The authors declare no competing interests.
Additional information
Responsible Editor: Zeynal Abiddin Erguler
Rights and permissions
About this article
Cite this article
Wang, Z., Chen, B., Zhang, Y. et al. Research on dual pressure relief and outburst prevention model for deep floor rock roadways. Arab J Geosci 14, 845 (2021). https://doi.org/10.1007/s12517-021-07118-y
Received:
Accepted:
Published:
DOI: https://doi.org/10.1007/s12517-021-07118-y