Abstract
The Fe3O4–Fe2O3 nanocomposites were prepared by the co-precipitation method and followed by calcination process. The products were synthesized and characterized by X-ray diffraction, scanning electron microscopy, transmission electron microscopy and energy-dispersive X-ray analysis. The obtained Fe3O4–Fe2O3 nanocomposites were then applied to study the electrocatalytic reduction of hydrogen peroxide (H2O2) in 0.01 M pH 7.0 phosphate buffer medium. Then the Fe3O4–Fe2O3 nanocomposites were used as active electrode material of electrochemical sensors for H2O2 detection The detection sensitivity of the sensor was 20.325 μA mM −1, and the detection limit was estimated to be about 0.2 mM.
Similar content being viewed by others
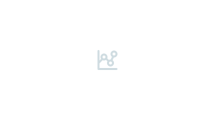
Explore related subjects
Discover the latest articles, news and stories from top researchers in related subjects.Avoid common mistakes on your manuscript.
1 Introduction
Owing to its strong oxidizing property, hydrogen peroxide (H2O2) is widely used in many fields. For example, H2O2 is useful for food production, sterilization, clinical applications and environmental analyses.[1–4] Further, H2O2 has emerged as an important by-product of enzymatic reactions in the field of biosensing. Thus, accurate and reliable determination of H2O2 has been widely investigated using spectrometry, chemiluminescence and electrochemistry technologies.[5–7] Among these methods, electrochemical method has been extensively applied due to its simple, accurate and fast analytical process. Many enzyme-based electrochemical biosensors towards H2O2 reduction have been made. However, the immobilized enzyme/protein on the surface of the electrode is facilitated to denature, which leads to such modified electrodes that suffer from a poor enzyme/protein activity, a low reproducibility and stability.[8] Nanomaterials can play an important role in improving sensor performance, due to their large specific surface areas, excellent conductivities and compatibilities. In recent years, nanomaterials have been regarded as excellent substitutes for enzymes. Single crystal and vertically aligned Co3O4 nanowalls were synthesized, and the Co3O4 nanowall electrode was applied for the amperometric detection of H2O2 and showed a fast response and high sensitivity.[9] Gu et al[10] have synthesized Cu–Ni(OH)2 nanocomposites and applied it as the fast and sensitive H2O2 sensor material. Ag nanoparticles were synthesized on indium tin oxide conducting glass substrate using the electrochemical deposition method, and the developed Ag nanoparticles sensor had excellent electrocatalytic activity for H2O2 detection.[11] The electrocatalytic activity of CuO flower-like nanostructured electrode was investigated in terms of its application to enzymeless amperometric H2O2 sensors.[12]
Transition metal oxide nanomaterials are one of the promising candidates for the active electrode material of non-enzymatic electrochemical sensors. Magnetite (Fe3O4), which is chemically stable, non-toxic and non-carcinogenic, has a high magnetic saturation value.[13–15] Hematite (α-Fe2O3), the most stable iron oxide under ambient condition with low-cost, non-toxicity and environmental-friendly features, is of great scientific and technology importance.[16] Fe3O4 and Fe2O3 have been widely fabricated as gas sensor because of its good stability, lower cost and easy availability. Yu et al[17] reported the application of chitosan–Fe3O4 nanocomposite-modified glassy carbon electrodes for the amperometric determination of bisphenol A. A novel imprinted sol–gel electrochemical sensor based on multi-walled carbon nanotubes doped with chitosan film on a carbon electrode has been developed.[18] La-doped Fe2O3 nanotubes are synthesized by an electrospinning method and followed by calcination, and the nanotubesshow a good selectivity to acetone.[19] To the best of our knowledge, H2O2 electrochemical sensor based on the Fe3O4–Fe2O3 nanocomposites has never been reported before. In this study, Fe3O4–Fe2O3 nanocomposites are synthesized by the co-precipitation method and followed by calcination process. The Fe3O4–Fe2O3 nanocomposites were applied for the sensitive amperometric detection of H2O2. The proposed sensor possesses high sensitivity and high stability.
2 Experimental
2.1 Sample preparation
Fe3O4–Fe2O3 nanocomposites were synthesized by the co-precipitation method and followed by calcination. Typically, 2.2 g of FeCl3⋅6H2O and 2.3 g of FeSO4⋅7H2O were dissolved in 30 ml of 0.01 M HCl to form a transparent solution. When the solution became clear, the mixture was then added drop-wise to 40 ml of 3 M NH3⋅H2O with the reaction mixture vigorously stirred at 80∘C for 150 min. The final products were collected, followed by calcination at 350–500∘C for 4 h.
2.2 Electrode preparation
Glassy carbon (GC) disks were polished with 0.03 mm Al2O3 powders. A typical suspension of the Fe3O4–Fe2O3 nanocomposites was prepared by suspending 6 mg Fe3O4–Fe2O3 nanocomposites in 3 ml 0.5% Nafion solution, and sonicated for 15 min. The suspension was transferred to the surface of the polished GC disk and dried at 80∘C for 5 min.
2.3 Characterization
Scanning electron microscopy (SEM, Hitachi S-4700) was used to characterize the morphology of the Fe3O4–Fe2O3 nanocomposites. The chemical compositions of the products were detected using an energy-dispersive X-ray spectrometry (EDS, Thermo Noran VANTAG-ESI). The obtained samples were characterized by X-ray powder diffraction (XRD) using a Rigaku D/max- γB X-ray diffractometer with graphite monochromatized Cu K α radiation (λ = 1.54178 Å) operated at 40 kV and 80 mA. Electrochemical measurements were performed using a computer-controlled CHI 660C electrochemical workstation in a standard three-electrode configuration, including Fe3O4–Fe2O3 nanocomposite electrodes as the working electrode, an Ag/AgCl reference electrode and a platinum counter electrode. H2O2 measurement was carried out in 0.01 M, pH 7.0, phosphate buffer containing 0.2–1.8 mM H2O2.
3 Results and discussion
In our study, the calcination temperature is varied from 350 to 450∘C to investigate its influence on the structure. Figure 1a shows the XRD patterns of the as-obtained products at 350∘C. All the diffraction peaks in figure 1a can be readily indexed to Fe3O4 of spinel structure (JCPDS Card no. 19-0629). Figure 1b shows the XRD pattern of the as-obtained product at 400∘C. All of the peaks of the XRD pattern in figure 1b can be indexed to a mixed phase of Fe3O4 (JCPDS Card no. 19-0629) and α-Fe2O3 (JCPDS Card no. 39-1346). This reveals that Fe3O4–Fe2O3 composites were obtained at 400∘C. When calcination temperatures are above 450∘C, it can be easily found from figure 1c that besides the diffraction peaks of Fe3O4, strong diffraction peaks of α-Fe2O3 are observed. Figure 1d shows the XRD patterns of the as-synthesized samples at 500∘C, all the reflection peaks can be readily indexed to α-Fe2O3 (JCPDS Card no. 39-1346). The XRD patterns indicate that Fe3O4–Fe2O3 composites were obtained in the calcination temperature range under investigation (350–450∘C).
The morphologies of the as-obtained products were examined by SEM microscopy. Figure 2a shows the pattern of the Fe3O4–Fe2O3 composites prepared at 400∘C. The SEM image displayed much smaller nanoparticles with diameters of about 40–50 nm. Figure 2b is the SEM image of the sample prepared at 450∘C. SEM images revealed that the morphologies of the Fe3O4–Fe2O3 nanocomposites prepared at 450∘C were similar to the sample prepared at 350∘C.
HRTEM analysis provides more detail structural information about the Fe3O4–Fe2O3 nanocomposites, showing the apparent lattice fringes of the crystal. Figure 3 is an HRTEM image taken from the Fe3O4–Fe2O3 nanocomposites. The observed interplanar spacing is 0.309 and 0.205 nm, which correspond to the (012) atomic spacing of Fe3O4 and the (400) atomic spacing of Fe2O3, respectively.
The EDS patterns of the Fe3O4–Fe2O3 nanocomposites prepared at 400 and 450∘C are shown in figure 4. It can be seen that the main elements in the samples are O and Fe and the peak intensity of Fe decreases with the increasing calcination temperature. Fe and O elements existed in the Fe3O4–Fe2O3 nanocomposites prepared at 400 and 450∘C have the molar ratio of 72.9:100 and 70.6:100, respectively. By calculation, the Fe3O4–Fe2O3 molar ratios in the Fe3O4–Fe2O3 nanocomposites are 2.22:1 and 0.67:1.
The electrocatalytic activity of the as-obtained products at different calcination temperature was studied. All samples exhibited the reduction of H2O2 starting around −0.5 V. The Fe3O4–Fe2O3 nanocomposites prepared at 400∘C exhibited the strongest electrocatalytic ability towards the reduction of H2O2. The electro-reduction mechanism of H2O2 on the Fe3O4–Fe2O3 nanocomposites can be illustrated by the equations below
Based on the XRD, HRTEM and FDS analysis, it is obvious that the strongest electrocatalytic activity of the Fe3O4–Fe2O3 nanocomposites may be attributed to its structure with the interface of Fe3O4–Fe2O3. According to the mechanism above, the reaction exists in Fe3O4 and Fe2O3. In Fe3O4–Fe2O3 nanocomposites, there are many Fe3O4–Fe2O3 interfaces, which is favourable for increasing diffusion rate and accelerating electrode kinetics. It is believed that the structure and Fe2O3 content have played an important role in controlling the reduction of H2O2.
Figure 5 shows the CVs of the Fe3O4–Fe2O3 nanocomposites prepared at 400∘C in 0.01 M phosphate buffer containing H2O2 with different concentrations. The current sensitivity increases with increasing H2O2 concentration (from the top: 0, 0.2, 0.6, 1.0 mM), which may be applied as the quantitative analysis. Figure 6a displays a typical current–time plot of the Fe3O4–Fe2O3 nanocomposites on the successive addition of H2O2 with various concentrations into stirring phosphate buffer (0.01 M, pH 7.0) at the applied potential of −1.0 V. These Fe3O4–Fe2O3 nanocomposite sensors show a very fast response, as the response reaches 100% of the steady-state value within 2.5 s. The calibration curves of the Fe3O4–Fe2O3 nanocomposites sensor are shown in figure 6b. The sensor has a wide linear range from 0.2 to 1.8 mM with a correlation coefficient of 0.997, and the sensitivity is determined to be as 20.325 μA mM −1. The selectivity of the sensor was also evaluated with four species: SO\(_{\mathrm {4}}^{\mathrm {\,\,\,2-}}\), Cl −, ClO\(_{\mathrm {3}}^{\mathrm {-}}\) and CO\(_{\mathrm {3}}^{\mathrm {~2-}}\). When SO\(_{\mathrm {4}}^{\mathrm {~2-}}\), Cl −, ClO\(_{\mathrm {3}}^{\mathrm {-}}\) and CO\(_{\mathrm {3}}^{\mathrm {\,\,\,2-}}\) were injected into the phosphate buffer, no obvious current was observed as shown in figure 7. This suggests that these species have no obvious interference in the reduction of H2O2.
4 Conclusion
In conclusion, the Fe3O4–Fe2O3 nanocomposites have been successfully synthesized by the co-precipitation method and followed by calcination process. The electrocatalytic activity of the as-obtained products at different calcination temperatures was studied by CV. It was found that the Fe3O4–Fe2O3 nanocomposites obtained at 400∘C showed maximal electrocatalytic ability for the reduction of H2O2. The amperometric response of the electrode was rapid (within 2.5 s), and had high sensitivity (20.325 μA mM −1). The proposed electrochemical sensor based on Fe3O4–Fe2O3 nanocomposites is thus expected to generate new opportunities for monitoring H2O2 concentrations in industry analyses fields.
References
Klassen N V, Marchington D and Mcgowan H C E 1994 Anal. Chem. 66 2921
Salimi A, Hallaj R, Soltanian S and Mamkhezri H 2007 Anal. Chim. Acta 594 24
Yang Y J and Hu S 2010 Electrochim. Acta 55 3471
Song X C, Wang X, Zheng Y F, Ma R and Yin H Y 2011a J. Nanopart. Res. 13 1319
Diaz A N, Peinado M C R and Minguez M C T 1998 Anal. Chim. Acta 363 221
Tanner P A and Wong A Y S 1998 Anal. Chim. Acta 370 279
Cui K, Song Y H, Yao Y, Huang Z Z and Wang L 2008 Electrochem. Commun. 10 663
Miao X, Yuan R, Chai Y, Shi Y and Yuan Y 2008 J. Electroanal. Chem. 612 157
Jia W, Guo M, Zheng Z, Yu T, Rodriguez E G, Wang Y and Lei Y 2009 J. Electroanal. Chem. 625 27
Gu A, Wang G, Gua J, Zhang X and Fang B 2010 Electrochim. Acta 55 7182
Song X C, Wang X, Zheng Y F, Ma R and Yin H Y 2011b J. Nanopart. Res. 13 5449
Song M, Hwang S W and Whang D 2010 Talanta 80 1648
Tural B, Ozkan N and Volkan M 2009 J. Phys. Chem. Solids 70 860
Wang N, Zhu L, Wang M, Wang D and Tang H 2010 Ultrasonics Sonochem. 17 78
Song X C, Zheng Y F and Yin H Y 2013 J. Nanopart. Res. 15 1856
Wang Y, Cao J, Yu M, Sun G, Wang X, Bala H and Zhang Z 2013 Mater. Lett. 100 102
Yu C, Gou L, Zhou X, Bao N and Gu H 2011 Electrochim. Acta 56 9056
Hu Y, Li J, Zhang Z, Zhang H, Luo L and Yao S 2011 Anal. Chim. Acta 698 61
Shan H, Liu C, Liu L, Li S, Wang L, Zhang X, Bo X and Chi X 2013 Sens. Actuators B 184 243
Author information
Authors and Affiliations
Corresponding author
Rights and permissions
About this article
Cite this article
CAO, G.S., WANG, P., LI, X. et al. A sensitive nonenzymatic hydrogen peroxide sensor based on Fe3O4–Fe2O3 nanocomposites. Bull Mater Sci 38, 163–167 (2015). https://doi.org/10.1007/s12034-014-0803-x
Received:
Revised:
Published:
Issue Date:
DOI: https://doi.org/10.1007/s12034-014-0803-x