Abstract
Waterborne coatings have gained more and more attention as a method to protect the environment. However, the application of waterborne coatings to metals, especially for sufficient long-term protection in harshly corrosive environments, is still limited. Here, we report a self-curing waterborne coating with good corrosion resistance. First, a self-curing waterborne epoxy resin (SWEP) was synthesized by a chemical reaction between the epoxy resin and titanium diisopropoxide bisacetylacetonate in water. The structural characterizations via Fourier transform infrared spectroscopy and 13C nuclear magnetic resonance spectrsocopy confirmed the successful preparation of the SWEP resin. Differential scanning calorimetry and thermogravimetric analysis showed that the SWEP resin could be cured by heating without the use of any curing agents, and the cured coating exhibited good thermal resistance. The mechanical properties of the cured coatings were discussed in the context of the corresponding standards. The results confirmed that the physical properties of the SWEP coating were as good as those of a traditional two-component waterborne epoxy resin (DCWEP) coating. The chemical resistance analysis revealed that the water, acid and alkaline resistances of the SWEP coating all have significant improvements compared to those of the DCWEP coating. The electrochemical impedance spectroscopy and potentiodynamic polarization test implied that the SWEP coating provided better corrosion protection for metal substances than the DCWEP coating.
Similar content being viewed by others
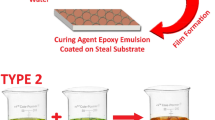
Explore related subjects
Discover the latest articles, news and stories from top researchers in related subjects.Avoid common mistakes on your manuscript.
Introduction
Metallic corrosion results in economic costs, technological delays and even structural failures of bridges, buildings, etc.1 Therefore, corrosion protection is necessary. The use of polymeric coatings on metal substrates is a smart and well-known strategy used to protect metals against corrosion.2
Epoxy resins, which are a very important class of thermosetting polymers, are widely used as protective coatings and adhesives due to their outstanding performances in terms of excellent corrosion resistance, stable chemical properties, outstanding adhesion, low curing shrinkage and high tensile strength.3,4,5,6,7,–8 Thus far, the majority of epoxy coatings are solvent-borne, containing high levels of volatile organic compounds (VOCs),3,4,–5,7,8 which cause serious environmental pollution and endanger human health. To protect the environment, worldwide environmental and ecological regulations require the development of new coating technologies that emit extremely low or no VOCs.9 Waterborne systems, using water as a diluting agent, have the advantage of easy cleaning of the formulation and equipment with water, which is harmless to the environment and human health. Therefore, studies on waterborne epoxy resins have received more attention in recent years, despite the somewhat higher cost and slightly reduced performance of these resins.6,10,11,12,13,14,15,–16
Currently, waterborne epoxy coatings are widely employed in building coatings and wood paints, but their application as anticorrosive coatings with sufficient long-term protection of metals, especially in harshly corrosive environments, is still limited.1,17 The water resistance of waterborne epoxy systems still cannot be enhanced to that of a solvent-based system, which limits their application.16 Many efforts have been made to improve the anticorrosive properties of waterborne coatings. One method is to improve their crosslinking property. Liu et al.18 reported that in a certain range, a moderate increase in the resin molecular weights and the carboxyl contents can improve the crosslinking property of the coatings, enhancing their water and corrosion resistance. Incorporation of nanoparticles in a coating is a modern approach to improve barrier and anticorrosive properties. For instance, Cui et al.16 developed waterborne epoxy coatings containing water-dispersible hexagonal boron nitride (h-BN) nanosheets. The homogeneously dispersed h-BN nanosheets improved the water barrier properties of the epoxy coating and remarkably improved the corrosion protection performance on a substrate. In addition, Wang et al.12,19,20 reported the incorporation of nanoparticles (e.g., mesoporous silica MCM-41 and MMT, mesoporous TiO2, and TiO2) into waterborne epoxy coatings, and possible chemical interactions between the polymeric matrix and nanoparticles caused high barrier properties and a high degree of crosslinking in the coatings.
The waterborne epoxy resin is an inhomogeneous two-phase system consisting of water as a continuous phase with dissolved hardener and epoxy resin emulsion droplets as a dispersed phase. Film formation of a waterborne coating includes coalescence of the emulsion droplets, penetration of the hardener molecules and reaction with the resin in the emulsion droplets. However, the degree of coalescence is limited, and a completely homogeneous film is extremely difficult or even impossible to obtain. For a waterborne epoxy/amine resin system, Wegmann21 reported that the diffusion rates and pathways of the hardener molecules cannot be controlled. Therefore, the cured film consists of domains of the original epoxy emulsion droplets or hexagons, and the former phase boundaries are still present in the coating. He found that the main reason for the poor resistance of these coatings to chemicals is their inhomogeneous film structure due to insufficient coalescence during the curing process. In a solvent-based film, the resin and hardener react chemically to form a three-dimensional network in a homogeneous phase. Therefore, the properties of a water-dispersed system are inferior to those of a solvent-based system.
Titanium diisopropoxide bisacetylacetonate (TIAA) is a special kind of titanium chelate. TIAA is more hydrolytically stable than other titanium ligands, e.g., ethylacetoacetate. A combination of TIAA and a diol solvent has been used to prepare sols with higher stability against hydrolysis and lower toxicity than those prepared by the predominantly used sol–gel routes.22,23,–24 TIAA can reduce shrinkage stress during drying and permits an increase in the thickness of ferroelectric thin films of lead titanate and lead zirconate titanate prepared from sols.22 In addition, TIAA is useful as a binder and can be used as a crosslinker for –OH functional polymers and other binders in paints, as well as adhesion promoters. In our previous study, a self-curing thermosetting bisphenol A epoxy resin/diisopropoxy bisethylacetoacetato titanate (EP-SG) resin was synthesized via a reaction between the hydroxyl or epoxy groups of EP and the isopropoxy groups of SG. The cured EP-SG coatings exhibit good thermal and chemical resistances as well as good physical properties.25
The goal of this study is to prepare a waterborne epoxy resin with improved corrosion resistance for the prevention of heat exchanger corrosion in petrochemical refineries. TIAA was chosen to chemically react with the epoxy resin in a waterborne system to obtain a self-curing waterborne epoxy (SWEP) resin. This SWEP resin contains free hydroxyl, epoxy, isopropoxy and titanium chelate groups and stably disperses in water. Therefore, the SWEP resin emulsion droplets are homogeneous, and the SWEP resin can be thermally crosslinked without the addition of a curing agent or catalyst, avoiding insufficient coalescence during the curing process. Structural characterizations of the SWEP resin during the polymerization and curing processes were performed via Fourier transform infrared spectroscopy (FTIR) and 13C nuclear magnetic resonance (NMR) spectroscopy. The curing behavior and thermal resistance were investigated by differential scanning calorimetry and thermogravimetric analysis. The corrosion protection properties of the coating were evaluated by an immersion test and electrochemical impedance spectroscopy. A double-component waterborne epoxy resin coating created by curing the waterborne epoxy resin with 25 wt% methyl-etherified melamine resin, marked as DCWEP coating, was chosen for comparison to characterize the physical and corrosion resistance properties of the cured SWEP coating.
Materials and methods
Materials
Waterborne epoxy resin (WE-20) was supplied by Guangzhou Feiyue New Materials Technology Co., Ltd., China. Titanium diisopropoxide bisacetylacetonate (TIAA) was purchased from E.I. Du Pont Company, USA. Methyl-etherified melamine resin (5386-60) was purchased from Shanghai New Resin Factory, China. Wetting agent (W-469) was provided by Elementis Specialties, UK. Acetone, ethanol, isopropanol and other chemicals were supplied by Tianjin Kemiou Chemical Reagent Co., Ltd., China, and used as received. Distilled water was prepared using an Ai Kepu (Aquapro) ultrapure water system.
Preparation of the self-curing waterborne epoxy resin
First, a certain amount of waterborne epoxy resin was added to a three-necked, round-bottomed flask equipped with a mechanical stirrer, thermometer, and circulating water condenser. Then, 15 wt.% of diisopropoxy bis(acetylacetone) titanate with respect to the epoxy resin was added dropwise into the above round-bottomed flask under vigorous stirring. Finally, the above mixture was stirred vigorously for 2 h at room temperature. The resulting self-curing waterborne epoxy resin before curing was marked as SWEP resin.
Preparation of SWEP coatings
Carbon steel substrates were prepared using sandpaper with a grit size of 800 and rinsed thoroughly with acetone and ethanol and air-dried prior to use. To decrease the surface tension of the SWEP resin, a certain amount of wetting agent was added to the SWEP resin and mixed thoroughly. The above SWEP resin solution was coated on the treated carbon steel substrates and dried at room temperature for 1–3 h until the surfaces of the coatings were dry. In our previous study,25 it was found that the chelate bonds can be broken at temperatures above 150°C. Therefore, all coated samples were cured at 160°C for 2 h in an air circulating oven. The SWEP resin after curing was marked as SWEP coating. The thicknesses of the SWEP coatings were determined using a ferromagnetic coating thickness meter (FMP20, Helmut Fischer, Germany).
Characterization
FTIR spectra were recorded on a Spectrum 100 FTIR spectrometer (FTS3000, Bio-Rad, USA) in the range of 4000–400 cm−1. A potassium bromide pellet was used to support the IR sample. The sample was spread thinly on a potassium bromide pellet with a spatula, and a potassium bromide pellet was used as a blank. The solid-state 13C NMR spectra were recorded on a JNM-ECA400 instrument (JEOLCo. Ltd., 100 MHz). The SWEP resin and SWEP coating were pulverized into powder with a mortar and pestle and placed into zirconium sample tubes. The 13C NMR spectra were characterized using the CP/MAS method.26
To observe the reaction process, determine the thermal stability of the coating and find an ideal curing temperature, the curing behavior and thermal stability of the SWEP resin were assessed via differential scanning calorimetry (DSC) and thermogravimetric (TG) analysis with simultaneous thermal analysis (DSC/DTA-TG, NETZSCH, STA 409 PC Luxx®, Germany) under a nitrogen atmosphere at a heating rate of 10°C min−1 in the range of 30–500°C.
To characterize the physical and corrosion resistance properties of the SWEP coatings, a double-component waterborne epoxy resin coating was chosen for comparison and created by curing a waterborne epoxy resin with a methylated melamine resin, which was marked as the DCWEP coating.
Carbon steel substrates with dimensions of 120 mm × 35 mm × 0.2 mm were used as the substrates for the physical and mechanical tests of the SWEP and DCWEP coatings. Flexibility was tested using the GB/T1731-1993 standard. Impact strength was measured using an impact tester according to the GB1732-93 standard. The samples were tested using a cantilever beam impact testing machine (Chengde Precision Tester XC-22, China). The adhesive force was measured using the GB/T1720-1979 standard.
Water resistance was measured in boiling ultrapure water and 80°C ultrapure water. Carbon steel bars 100 mm long and 10 mm wide were polished with successively finer grades of sandpaper and then washed thoroughly with acetone before further use. Following the GB/T1727-1992 standard, the SWEP and DCWEP resins were coated onto treated carbon steel bars. All samples were approximately 180 µm thick. The samples were immersed in boiling ultrapure water and 80°C ultrapure water at atmospheric pressure for 8 h, and after this period, the temperature was reduced to room temperature and maintained for 16 h. The acid and alkali resistances of the SWEP coatings were determined via an immersion test. Coated carbon steel bars were placed into a glass container with a 5 wt.% sulfuric acid (H2SO4) solution for the acid resistance test and into another glass container with a 10 wt.% sodium hydroxide (NaOH) solution for the alkali resistance test. After immersion for a predetermined time, a visual examination was performed to detect deterioration, such as blistering, cracking or spoiling.
The anticorrosive efficiency of the SWEP and DCWEP coatings with a thickness of 30 ± 3 µm was investigated by electrochemical methods including electrochemical impedance spectroscopy (EIS) and potentiodynamic polarization test. All electrochemical measurements were recorded by an electrochemical workstation (PARSTAT 2273, Princeton Applied Research, USA) with ZSimpwin software. A conventional three-electrode cell arrangement was used in the experiments18: Carbon steel substrates coated with SWEP and DCWEP coatings were set as the working electrodes with a circular testing area of 1 cm2; a saturated calomel electrode (SCE) was used as the reference electrode; and a platinum wire electrode was the counter electrode. After being immersed in a 3.5% NaCl solution for 5 h at room temperature, 3 h at 80°C, and 24 h at 80°C, the EIS data of the samples were recorded over a frequency range from 10−2 to 105 Hz. A sinusoidal signal of 10 mV in amplitude was applied near the open circuit potential. The polarization curves were plotted by sweeping the applied potential from –0.25 to +0.25 V with respect to OCP at scan rate of 0.167 mV/s on 1 cm2 anode.
Results and discussion
Synthesis of the SWEP coating
The synthesis route used to make the SWEP resin is shown in Fig. 1. The synthesis of the SWEP resin was carried out by the reaction between epoxy resins (EP) in the waterborne epoxy resin system and TIAA. After TIAA was added into the waterborne epoxy resin system, the isopropoxy groups of TIAA could react with the hydroxyl or epoxy groups of the dispersed EP particles in the system because alkoxy groups are known to rapidly attach. Finally, a uniform and stable brown solution was obtained, which indicated the formation of the SWEP resin.
The structures of the SWEP resin and SWEP coating were confirmed via 13C NMR, as shown in Fig. 2. The peaks above 110 ppm are assigned to the carbon atoms of the benzene rings, and those below 110 ppm are assigned to the aliphatic carbon atoms. In the case of the SWEP resin (Fig. 2a), the signal observed at 50 ppm is due to the epoxy groups. The peak from the epoxy groups disappears completely in the spectrum of the SWEP coating (Fig. 2b), suggesting that the epoxy groups participate in the crosslinking process. However, the reactions of the hydroxyl, isopropoxy and acetylacetonate groups cannot be observed from the 13C NMR spectra.
To investigate the reaction mechanism during the synthesis of the SWEP resin and the crosslinking process of the SWEP coating, the structures of the EP, SWEP resin and SWEP coating were further characterized by FTIR. The results are shown in Fig. 3. For the FTIR spectrum of EP in Fig. 3a, characteristic peaks at approximately 3420 and 914 cm−1 are assigned to the hydroxyl and epoxy groups, respectively. In addition, there is a small peak at 1735 cm−1 due to the ester emulsifying and dispersing agents in the waterborne epoxy resin system. In the spectrum of the SWEP resin (Fig. 3b), the characteristic peak at 914 cm−1 decreases, suggesting that the epoxy groups react with the isopropoxy groups of TIAA. Although there are no obvious changes in the peaks of the hydroxyl groups from that observed in the spectra of EP and the SWEP resin, it is proposed that the hydroxyl groups may also participate in the reaction with the isopropoxy groups because of their higher reactivity compared to that of EP.25 In addition, the intensity of the band at 1735 cm−1 is stronger in comparison with that of EP (Fig. 3a) due to the ketone groups in the SWEP resin, which also indicates that the chelating ligands, i.e., the acetylacetonate groups, do not participate in the reaction between EP and TIAA. After the SWEP resin was cured (Fig. 3c), the epoxy group peak disappeared. Additionally, the hydroxyl group and acetylacetonate group peaks became much weaker. This result suggests that a reaction occurs between the remaining hydroxyl and epoxy groups in the EP structure and the acetylacetonate group in the TIAA structure, leading to crosslinking of the SWEP resin.
In conclusion, the epoxy and hydroxyl groups in EP reacted with the isopropoxy group in TIAA to produce the SWEP resin, while the chelating ligands in TIAA did not react and remained stable in the structure of the SWEP resin. During the crosslinking process, the bonds of the chelating ligands were broken at high temperature (e.g., 160°C), and new reactive groups were formed. The new reactive groups could react further with the epoxy and hydroxyl groups that did not react during the synthesis, leading to crosslinking of the SWEP resin.
Thermal properties
It is necessary to study curing behavior to obtain coatings with excellent properties. DSC is a convenient tool for examining the curing behavior of resins. Figure 4a shows the TG–DTA curves of the SWEP resin. A broad exothermic peak appears in the DSC curve from 80 to 200°C and may be regarded as the onset of the curing of the SWEP resin. In the TG curve, little weight loss occurs below 100°C. The losses decrease slowly due to volatilization of water as the temperature increases. During the curing process, some small molecules are generated and volatilized, leading to further weight loss. However, the weight decreases rapidly as the resin decomposes above 340°C. The thermal degradation of the SWEP coating is shown in Fig. 4b. The SWEP coating maintains a constant weight of 100% until 340°C. The thermal degradation temperature is defined as the temperature at which the samples lose 5% of their initial weight. It can be seen that a 5 wt.% loss occurs at approximately 360°C. In summary, the thermal degradation temperature is approximately 360°C, which indicates that the coatings exhibit good thermal resistance.
Waterborne epoxy resins are usually cured by adding amine curing agents. However, their long-term chemical resistance, particularly toward acids, is rather poor. A waterborne epoxy/amine coating (DCWEP coating) was prepared by curing a waterborne epoxy resin with a methylated melamine resin. Then, the physical and corrosion resistance properties of the SWEP coating and DCWEP coating were evaluated. The results are shown and discussed as follows.
Physical properties
For industrial applications, protective coatings should be able to increase the lifetime of a metal substrate in abrasive and corrosive environments and ensure that film detachment, scratch or wear failure does not occur to prevent electrolytes from accessing the underlying metal surface.27 The physical properties of the SWEP and DCWEP coatings are shown in Table 1. Flexibility was determined by the minimum diameter of the bar flexibility tester that does not cause damage to the coating. The results show less than 1 mm of flexibility for both samples. Moreover, for both samples, the adhesion was scratch tested and determined to be first grade, and the impact resistance was above 50 cm for a hammer with a weight of 1000 g. In other words, both the SWEP and DCWEP coatings possess excellent flexibility and adhesion and impact resistances, and these properties meet the requirements for anticorrosive coatings.
Chemical resistance
Chemical resistance tests were carried out to determine the ability of the coatings to withstand specific conditions (Table 2). First, water resistance was measured in boiling ultrapure water and 80°C ultrapure water. The SWEP coating maintained its integrity without cracking, spots or blisters for 6 h and 7 days in boiling ultrapure water and 80°C ultrapure water, respectively. However, the DCWEP coating could only resist water for 3 h and 1 day in boiling ultrapure water and 80°C ultrapure water, respectively, suggesting that the DCWEP coating can be easily attacked by water, especially at high temperatures. Examinations of the chemical resistance were also performed by immersing the coatings in an acid solution (5 wt.% H2SO4 solution) and alkaline solution (10 wt.% NaOH solution). After 7 days of immersion, there were no signs of cracking, spots, blisters or other indications of solvent attack on the SWEP coating. However, the DCWEP coating could only resist 5 wt.% H2SO4 for 2 days and 10 wt.% NaOH solution for 6 days. Compared to those of the DCWEP coating, the water, acid and alkaline resistances of the SWEP coating were significantly improved.
Electrochemical impedance spectroscopy (EIS)
EIS was further employed to investigate the deterioration processes of the SWEP and DCWEP coatings. The impedance behaviors of coatings with a thickness of approximately 30 µm were measured in a 3.5 wt.% NaCl solution for different times and at different temperatures. After 5 h of immersion at room temperature, the same electrode was then immersed in a 3.5 wt.% NaCl solution at 80°C to accelerate the corrosion rate. The EIS measurements were performed in the salt solution at room temperature. The barrier effect of a coating is directly proportional to the coating thickness. In our experience, the polymeric coatings used for corrosion protection usually have a thickness ranging from one hundred to several hundreds of micrometers. In this study, the thickness of the SWEP and DCWEP coatings was 30 ± 5 µm, ensuring the accuracy of the EIS results.
The Bode, Nyquist and phase angle plots are shown in Fig. 5. The impedance modulus at the lowest frequency (Zf=0.01 Hz) in the Bode plot can be used as a semiquantitative indicator of a coating’s barrier performance.12 The EIS data clearly indicate that both the SWEP and DCWEP coatings provided excellent barrier protection for the steel surface at the initial immersion time with high Zf=0.01 Hz values of approximately 8.5 × 1010 and 7.9 × 1010 Ω cm2, respectively. With increasing immersion time, the Zf=0.01 Hz values of both samples presented a decreasing trend because water diffused through the coatings and created conducting pathways at various depths within the coatings.14 After 5 h of immersion at room temperature, the Zf=0.01 Hz value of the SWEP coating decreased to 3.6 × 109 Ω cm2. However, in the case of the DCWEP coating, the Zf=0.01 Hz value decreased dramatically to 1.0 × 107 Ω cm2. The phase angle plot (Fig. 5f) shows two time constants, which are related to the corrosion activity due to the ion dissolution and oxygen reduction.28 The time constant at high frequencies concerning the organic layer describes the dielectric and barrier properties of the organic coating. The time constant at lower frequencies concerning the substrate represents the corrosion reactions at the metal/organic film interface. When the immersion temperature increased to 80°C, after 3 h of immersion, the Zf=0.01 Hz value of the DCWEP coating decreased to 5.3 × 104 Ω cm2, which implied failure of the corrosive protection and delamination of the coating layer.29 At this stage, diffusion of the electrolyte inside the DCWEP coating was complete, and the electrolyte phase was in contact with the metal/oxide interface. Thus, corrosion reactions occurred on the metal surface. However, the SWEP coating maintained a high Zf=0.01 Hz value of 4.8 × 107 Ω cm2. With additional immersion time up to 24 h at 80°C, the Zf=0.01 Hz values of the SWEP and DCWEP coatings were 3.0 × 104 and 1.9 × 104 Ω cm2, respectively, suggesting that the SWEP coating also lost corrosive protection. From the EIS results, it could be preliminarily ascertained that the SWEP coating provided better corrosion protection for metal substances than the DCWEP coating.
The corrosion protection efficiency of the SWEP and DCWEP coatings was characterized by the potentiodynamic polarization test after stabilization for 30 min in 3.5 wt% NaCl solution. The values of the potentiodynamic polarization curves after Tafel fit are presented in Fig. 6 and Table 3. Corrosion rate (C.R) in mm/year is calculated according to equation (1):
In equation (1), ρ is the density of the carbon steel (7.87 g/cm3) and Ew is the equivalent weight of the carbon steel (27.92 g).30 According to the results, the SWEP coating shows more positive Ecorr and significantly lower icorr than the DCWEP coating. It means that the SWEP coating had more effective corrosion protection performance than the DCWEP coating.
The lower chemical resistance of waterborne epoxy coatings is often blamed on the fact that hydrophilic surfactants and hardeners must be used, and these components remain in the coating, which makes the coatings less resistant to attacks from water, solvents and other chemicals. However, Wegmann21 found that the main reasons for the poor resistance of these coatings to other chemicals, especially acids, are the unreacted amine curing agents and/or water trapped inside the coating and, most importantly, the inhomogeneous film structure due to insufficient coalescence during the curing process. In this work, a self-curing waterborne epoxy resin (SWEP resin) was synthesized via a chemical reaction between an epoxy resin and TIAA. In a waterborne epoxy resin system, the obtained SWEP resin containing free epoxy groups, hydroxyl groups and organic titanium chelate bonds could stably disperse in water. Therefore, only one component is present in water, which avoids the harmful effect of unreacted amine curing agent. During the curing process, the organic titanium chelate bonds in the epoxy resin break at high temperature and form new reactive groups that can react with epoxy and hydroxyl groups to form a homogeneous coating with improved chemical and corrosion resistances. A high temperature can drive the reaction to completion and improve the coalescence. Therefore, compared to those of the DCWEP coating, the SWEP coating has significantly better water, acid and alkaline resistances and corrosion protection properties.
Conclusions
In this study, a self-curing waterborne epoxy resin (SWEP) was synthesized by a chemical reaction between the hydroxyl groups or epoxy groups of an epoxy resin and the isopropoxy groups of titanium diisopropoxide bisacetylacetonate in water and structurally characterized via Fourier transform infrared spectroscopy and 13C nuclear magnetic resonance spectroscopy. This SWEP resin contains free hydroxyl, epoxy and titanium chelate groups, stably disperses in water and can be self-cured via heating. The cured SWEP coating exhibited good physical and thermal resistance properties. In particular, the chemical resistance analysis, EIS and potentiodynamic polarization test revealed that the SWEP coating provided better corrosion resistance for metal substances than a traditional two-component waterborne epoxy resin.
References
Sørensen, PA, Kiil, S, Dam-Johansen, K, Weinell, CE, “Anticorrosive Coatings: A Review.” J. Coat. Technol. Res., 6 135–176 (2009)
Qiu, S, Chen, C, Cui, M, Li, W, Zhao, H, Wang, L, “Corrosion Protection Performance of Waterborne Epoxy Coatings Containing Self-Doped Polyaniline Nanofiber.” Appl. Surf. Sci., 407 213–222 (2017)
Shau, M, Wang, T, “Syntheses, Structure, Reactivity, and Thermal Properties of New Cyclic Phosphine Oxide Epoxy Resins Cured by Diamines.” J. Polym. Sci. PartA: Polym. Chem., 34 387–396 (1996)
Conradi, M, Kocijan, A, Kek-Merl, D, Zorko, M, Verpoest, I, “Mechanical and Anticorrosion Properties of Nano Silica-Filled Epoxy Resin Composite Coatings.” Appl. Surf. Sci., 292 432–437 (2014)
Tomic, MD, Dunjic, B, Likic, V, Bajat, J, Rogan, J, Djonlagic, J, “The Use of Nanoclay in Preparation of Epoxy Anticorrosive Coatings.” Prog. Org. Coat., 77 518–527 (2014)
Yu, Z, Di, H, Ma, Y, Lv, L, Pan, Y, Zhang, C, He, Y, “Fabrication of Graphene Oxide-Alumina Hybrids to Reinforce the Anti-Corrosion Performance of Composite Epoxy Coatings.” Appl. Surf. Sci., 351 986–996 (2015)
Pourhashem, S, Rashidi, A, Vaezi, MR, Bagherzadeh, MR, “Excellent Corrosion Protection Performance of Epoxy Composite Coatings Filled with Amino-Silane Functionalized Graphene Oxide.” Surf. Coat. Technol., 317 1–9 (2017)
Kongparakul, S, Kornprasert, S, Suriya, P, Le, D, Samart, C, Chantarasiri, N, Prasassarakich, P, Guan, G, “Self-healing Hybrid Nanocomposite Anticorrosive Coating from Epoxy/Modified Nanosilica/Perfluorooctyl Triethoxysilane.” Prog. Org. Coat., 104 173–179 (2017)
Athawale, VD, Nimbalkar, RV, “Waterborne Coatings Based on Renewable Oil Resources: An Overview.” J. Am. Oil Chem. Soc., 88 159–185 (2011)
Han, SO, Drzal, LT, “Water Absorption Effects on Hydrophilic Polymer Matrix of Carboxyl Functionalized Glucose Resin and Epoxy Resin.” Eur. Polym. J., 39 1791–1799 (2003)
Liu, M, Mao, X, Zhu, H, Lin, A, Wang, D, “Water and Corrosion Resistance of Epoxy-Acrylic-Amine Waterborne Coatings: Effects of Resin Molecular Weight, Polar Group and Hydrophobic Segment.” Corros. Sci., 75 106–113 (2013)
Wang, N, Fu, W, Zhang, J, Li, X, Fang, Q, “Corrosion Performance of Waterborne Epoxy Coatings Containing Polyethylenimine Treated Mesoporous-TiO2 Nanoparticles on Mild Steel.” Prog. Org. Coat., 89 114–122 (2015)
Cai, K, Zuo, S, Luo, S, Yao, C, Liu, W, Ma, J, Mao, H, Li, Z, “Preparation of Polyaniline/Graphene Composites with Excellent Anti-Corrosion Properties and Their Application in Waterborne Polyurethane Anticorrosive Coatings.” RSC, 6 95965–95972 (2016)
Wang, N, Fu, W, Sun, M, Zhang, J, Fang, Q, “Effect of Different Structured TiO2 Particle on Anticorrosion Properties of Waterborne Epoxy Coatings.” Corros. Eng. Sci. Techn, 51 365–372 (2016)
Qiu, S, Chen, C, Cui, M, Li, W, Zhao, H, Wang, L, “Corrosion Protection Performance of Waterborne Epoxy Coatings Containing Self-Doped Polyaniline Nanofiber.” Appl. Surf. Sci., 407 213–222 (2017)
Cui, M, Ren, S, Chen, J, Liu, S, Zhang, G, Zhao, H, Wang, L, Xue, Q, “Anticorrosive Performance of Waterborne Epoxy Coatings Containing Water-Dispersible Hexagonal Boron Nitride (h-BN) Nanosheets.” Appl. Surf. Sci., 397 77–86 (2017)
Elmore, JD, Kincaid, DS, Komar, PC, Nielsen, JE, “Waterborne Epoxy Protective Coatings for Metal.” J. Coat. Technol., 74 63–72 (2002)
Liu, M, Mao, X, Zhu, H, Lin, A, Wang, D, “Water and Corrosion Resistance of Epoxy-Acrylic-Amine Waterborne Coatings: Effects of Resin Molecular Weight, Polar Group and Hydrophobic Segment.” Corros. Sci., 75 106–113 (2013)
Wang, N, Cheng, K, Wu, H, Wang, C, Wang, Q, Wang, F, “Effect of Nano-Sized Mesoporous Silica MCM-41 and MMT on Corrosion Properties of Epoxy Coating.” Prog. Org. Coat., 75 386–391 (2012)
Wang, N, Fu, W, Sun, M, Zhang, J, Fang, Q, “Effect of Different Structured TiO2 Particle on Anticorrosion Properties of Waterborne Epoxy.” Corros. Eng. Sci. Techn, 51 365–372 (2016)
Wegmann, A, “Chemical Resistance of Waterborne Epoxy/Amine Coatings.” Prog. Org. Coat., 32 231–239 (1997)
Phillips, NJ, Milne, SJ, Ali, NJ, Kennedy, JD, “A Preliminary Nuclear Magnetic Resonance Investigation of the Titanium Diisopropoxide Bis(2,4-pentanedionate) Propanediol Sol-Gel Precursor System.” J. Mater. Sci. Lett., 13 1535–1537 (1994)
Calzada, ML, Bretos, I, Jimenez, R, Guillon, H, Pardo, L, “Low-Temperature Processing of Ferroelectric Thin Films Compatible with Silicon Integrated Circuit Technology.” Adv. Mater., 16 1620–1624 (2004)
Tangwiwat, S, Milne, SJ, “Barium Titanate Sols Prepared by A Diol-Based Sol-Gel Route.” J. Non-Cryst. Solids, 351 976–980 (2005)
Tang, G, Zhang, K, Yan, Z, Ma, L, Huang, X, “A Self-Curing, Thermosetting Resin Based on Epoxy and Organictitanium Chelate as an Anticorrosive Coating Matrix for Heatexchangers: Preparation and Properties.” Prog. Org. Coat., 102 225–230 (2017)
Huang, K, Liu, Z, Zhang, J, Li, S, Li, M, Xia, J, Zhou, Y, “A Self-Crosslinking Thermosetting Monomer with Both Epoxy and Anhydride Groups Derived from Tung Oil Fatty Acids: Synthesis and Properties.” Eur. Polym J., 70 45–54 (2015)
Harb, SV, Pulcinelli, SH, Santilli, CV, Knowles, KM, Hammer, P, “A Comparative Study on Graphene Oxide and Carbon Nanotube Reinforcement of PMMA-Siloxane-Silica Anticorrosive Coatings.” ACS Appl. Mater. Interfaces, 8 16339–16350 (2016)
Deyab, MA, “Effect of Carbon Nano-Tubes on the Corrosion Resistance of Alkyd Coating Immersed in Sodium Chloride Solution.” Prog. Org. Coat., 85 146–150 (2015)
Qiu, Z, Wang, R, Wu, J, Zhang, Y, Qu, Y, Wu, X, “Graphene Oxide as a Corrosion-Inhibitive Coating on Magnesium Alloys.” RSC Adv., 5 44149–44159 (2015)
Pourhashem, S, Vaezi, MR, Rashidi, A, “Investigating the Effect of SiO2-Graphene Oxide Hybrid as Inorganic Nanofiller on Corrosion Protection Properties of Epoxy Coatings.” Surf. Coat. Technol., 311 282–294 (2017)
Acknowledgments
This work was financially supported by a Team Project using the Fundamental Research Funds for Central Scientific Research Institutions (Nos. K-JBYWF-2016-T18 and K-JBYWF-2017-T17), Innovative talents project using the Fundamental Research Funds for Central Scientific Research Institutions (No. K-JBYWF-2018-CR03), the Tianjin Postdoctoral Innovation Projects Merit Funding Scheme, the Projects in the National Science and Technology Pillar Program during the Twelfth Five-year Plan Period (No. 2014BAB06B00) and the National Natural Science Foundation of China (No. 51401061).
Author information
Authors and Affiliations
Corresponding author
Rights and permissions
About this article
Cite this article
Tang, G., Ren, T., Yan, Z. et al. Corrosion resistance of a self-curing waterborne epoxy resin coating. J Coat Technol Res 16, 895–904 (2019). https://doi.org/10.1007/s11998-018-00166-2
Published:
Issue Date:
DOI: https://doi.org/10.1007/s11998-018-00166-2