Abstract
AZ80-1.5 Vol.% SiC nanocomposite was produced by the stir-casting method. The cast specimens were annealed and subjected to multi-directional forging (MDF) for up to 8 passes at 250 °C. Shear punch test (SPT), Vickers microhardness test, and uniaxial tension test were employed to evaluate the mechanical properties of nanocomposite before and after MDF process. Microstructural studies showed that the average grain structure was refined and the grain size distribution became more uniform after all MDF passes. The most pronounced grain refinement was obtained after eighth passes of MDF, where the average grain size of the unprocessed material was reduced from 31.4 to 4.9 µm. Based on the results of shear punch test (SPT), both shear yield stress (SYS) and ultimate shear strength (USS) of the nanocomposite were significantly improved after eight passes of the MDF process. The values of SYS and USS in the unprocessed specimen were 123.7 and 158.9 MPa, respectively, which increased to 164.6 and 194.1 MPa after eight MDF passes. Processing by MDF resulted in the enhancement of microhardness, strength, and ductility of the nanocomposite. After 8 MDF passes, improvements of 22.4, 48.1, 45.2, and 8.5% were obtained for the microhardness, TYS, USS, and elongation, respectively. The mechanisms of these improvements were discussed based on the microstructural features of the material.
Similar content being viewed by others
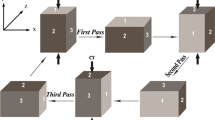
Explore related subjects
Discover the latest articles, news and stories from top researchers in related subjects.Avoid common mistakes on your manuscript.
1 Introduction
Magnesium alloys possess low density, high specific strength, good castability, and ease of machining and processing (Ref 1). Despite these great characteristics, they suffer from low workability caused by their HPC structure, which limits their application (Ref 2, 3). One of the common ways for improving the properties of magnesium is alloying with elements such as aluminum, zinc, manganese, calcium, and other similar elements. Even more enhanced properties can be achieved by composite reinforcements (Ref 4). It is generally believed that the ultimate tensile strength of Mg-based composites is much higher than that of the unreinforced alloys (Ref 5). In general, the use of ceramic strengthening particles can result in improvement of mechanical properties of Mg alloys (Ref 6). However, the selection of the proper processing method is essential for uniform distribution of strengthening particles and achieving favorable results. Among these methods, stir casing is known as an adaptable and cost-effective method, due to its simplicity, ability to produce complex structures, low production cost, and high production rate and is therefore preferred over other methods (Ref 7, 8).
Despite the high number of studies on fabrication of Mg nanocomposites, very few studies have investigated their thermomechanical processing (Ref 9). Studies have shown that using plastic deformation techniques such as extrusion, rolling, and forging can result in significant improvements in strength and ductility of composites. Currently, severe plastic deformation (SPD) processes such as equal-channel angular pressing (ECAP) (Ref 3), high-pressure torsion (HPT) (Ref 10), multi-directional forging (MDF) (Ref 11, 12), accumulative roll bonding (ARB) (Ref 13), and repeated upsetting (RU) (Ref 14) have been widely used for converting coarse-grained bulk Mg alloys into ultra-fined grain (UFG) materials. Among various SPD methods, MDF process has a relatively low cost and can be used for processing of voluminous pieces with ultra-fine grain structures (Ref 12, 15). This process is based on the repeated pressings along with change in the force axes, using the X→ Y→ Z→ X arrangement, which results in dynamic recrystallization and grain refinement in metallic alloys (Ref 16).
Although several studies have considered the SPD processing of Mg-based alloys, very few studies have focused on the Mg-based composites and nanocomposites. Qiao et al. (Ref 17) investigated the effect of extrusion and ECAP on the casted AZ91-SiC nanocomposite. In their study, the nanocomposite was extruded at the temperature of 350 °C before undergoing ECAP. The grain size decreased significantly after extrusion and ECAP, due to dynamic recrystallization. Although nanoparticles had formed clusters during casting process, a more uniform distribution of these particles emerged after extrusion and ECAP processes. Furthermore, YTS and UTS increased significantly after extrusion and ECAP processes. The microstructure and microhardness of the equal-channel angularly pressed AZ31 Mg alloy containing Al2O3 nanoparticles have also been investigated (Ref 18). The incorporation of Al2O3 nanoparticles in the base alloy refined the microstructure and improved the homogeneity of grain size distribution after ECAP. It was also shown that nanoparticles encouraged grain boundary pinning, resulting in enhanced microhardness of the nanocomposite. Nie et al. (Ref 9) studied the effects of MDF on AZ91 magnesium alloy and AZ91/SiC nanocomposite. They reported that after 6 passes of the MDF process, the decrease in grain size of nanocomposite was significantly higher than that of AZ91 alloy. This was accompanied by the improvement in tensile properties.
In the present study, 1.5 vol.% SiC nanoparticles were added to AZ80 magnesium alloy by stir-casting method. The nanocomposite specimens were processed by MDF for up to 8 passes. The effect of MDF on the microstructure, hardness and mechanical properties of the specimens was investigated in the tensile and shear deformation modes.
2 Materials and Methods
The AZ80 alloy was used as the matrix material, and 1.5 vol.% of SiC ceramic nanoparticles with the average particle size of 38 nm was used as the reinforcement. Mg, Al, Zn, and Mn with high purity (99.9% wt.%) were used to manufacture the initial AZ80 alloy with the chemical composition of Mg-8.03Al-0.5Zn-0.02Mn. Stir-casting method was used to fabricate the AZ80/SiC nanocomposites. In this method, after melting of the base alloy, the reinforcing SiC nanoparticles are added during magnetic stirring of the molten alloy. This leads to better distribution of nanoparticles during solidification of the melt in the mold. The base AZ80 alloy was melted in a graphite crucible at the temperature of 750 °C. The molten alloy was kept at this temperature for 30 min and was then stirred for 2 min using a magnetic stirrer before addition of reinforcing particles in order to create eddy current. Then, reinforcing particles were added to the molten alloy without any preheating. Stirring was continued for a few minutes after the addition of the last batch of nanoparticles. Finally, the composite was transferred to a metal mold preheated to 300 °C.
In order to produce a more uniform microstructure with less structural defects for MDF processing, nanocomposites were coated with a solution of magnesium oxide in ethanol to prevent surface oxidation before homogenization at 400 °C for 6 h. The annealed specimens were then cut into 13 mm × 13 mm × 20 mm samples using electro-discharge machining (EDM). During MDF, the specimen is placed inside a die cavity and pressed by the applied load. The specimen size is preserved during the process and no recognizable changes take place. This process can be repeated in several passes from different directions in order to achieve ultra-fine grain structures. Figure 1 shows the schematics of two subsequent passes of MDF process. MDF was carried out using an MTS universal testing machine at the constant temperature of 220 °C with compression rate of 1 mm/min. The die assembly was heated to the desired temperature by heating elements incorporated close to the die cavity. It was kept constant by using a temperature controller unit, and specimens were placed in the die 15 min before the process in order to reach thermal equilibrium. Teflon tapes were used as lubricants. In order to investigate the effects of MDF processing on the microstructural features and mechanical properties, two specimens after every two MDF passes (2, 4, 6, and 8 passes) were studied. The effective strain after each MDF pass in the die cavity is about 0.5 (Ref 16). The aspect ratio of the specimens during MDF process was preserved at 1:1:1.54, while the loading direction changed by 90 degrees between two subsequent passes.
For microstructural studies, 3-mm-thick samples were cut from the cross section perpendicular to the flow direction of each specimen. After polishing, specimens were etched for 6 to 10 s in a solution containing 4.2 g picric acid, 10 mL acetic acid, 10 mL distilled water, and 70 mL ethanol. The microstructural images were then prepared using optical microscopy (OM). Digimizer software was used for calculating the average grain size and size distribution in the annealed and MDFed nanocomposite specimens. The EDS analysis was used to examine the distribution of nanoparticles through elemental maps. XRD analysis was performed to identify the phases present in the nanocomposite.
Shear punch test (SPT) is a miniature testing method for determining shear properties, which can provide shear yield stress (SYS) and ultimate shear strength (USS). The schematic presentation of this test is exhibited in Fig. 2(a). The 0.7-mm-thick SPT specimens were prepared from the sections cut perpendicular to the axial direction (Ref 19). The diameter of the punch used in this test was 3.21 mm, and speed of the punch was 0.25 mm/min. Figure 2(b) shows a schematic illustration of the location of the microstructure and SPT specimens. SPT was carried out using an MTS universal testing machine at room temperature, where each test was repeated at least three times in order to ensure the validity of the results.
(a) Schematic image of the shear punch test template (Ref 3), geometrical position of (b) shear punch, microhardness, and (c) tensile test specimens
The initial data obtained from SPT include the variation of force with punch displacement, which can be converted into a shear stress versus dimensionless displacement data, using the equations \(\uptau =\frac{\mathrm{P}}{2\mathrm{\pi rt}}\) and \(\updelta =\frac{{\mathrm{d}}_{\mathrm{c}}}{\mathrm{t}}\), where \(\tau \) is the shear stress, \(P\) is the applied force, \(r\) is the mean radius of punch and die, and t is the specimen thickness, \(\delta \) is the dimensionless displacement, and \({d}_{c}\) is the measured displacement (Ref 17, 20).
Tensile tests at room temperature would provide yield stress, ultimate tensile strength, and elongation of AZ80/SiC nanocomposite before and after various passes of MDF process. The small dog-bone specimens for tensile test were prepared using ASTM E8 standard with the gauge length, width, and thickness of 2.6, 2 and 1.3 mm, respectively. As shown in Fig. 2(c), test specimens were prepared using EDM from the plane parallel to the flow direction. In order to validate the results, three tensile test specimens were tested for each condition. Uniaxial tensile test was carried out at room temperature and an initial constant strain rate of \(1\times {10}^{-3}{s}^{-1}\) using an MTS universal testing machine.
Microhardness of the processed material was measured on the specimens with a thickness of 3 mm (Fig. 2(b)), according to the ASTM E384 standard, using a NEXUS 4000 microhardness tester under a load of 200 g and time of 30 s. At least three separate locations were tested on the surface of each specimen, and the average hardness value of all points was reported.
3 Results and Discussion
3.1 Microstructural Studies
Figure 3 shows the microstructures of the AZ80/SiC nanocomposite in the annealed condition and after different MDF passes. As can be seen, after two MDF passes (Fig. 3b), distribution of grains is more uniform compared to the unprocessed specimen. This enhanced microstructural uniformity is accompanied by grain size refinement. The average grain size of the nanocomposite before MDF is about 36.7 μm, which reduces to 20 μm after 2 passes of MDF. Variation of grain size distribution is shown in Fig. 4. Comparing the results in Fig. 4(a) and (b) shows that grain size distribution has improved after MDF process compared to the unprocessed nanocomposite. One of the main goals in the post-processing of metal–matrix nanocomposites is creating a more uniform distribution of nanoparticles, which can result in finer and more uniform microstructures. According to Fig. 3(c) and 4(c), the average grain size has decreased to 12.6 μm with a standard deviation of 3.6 μm after four MDF passes, indicating a finer grain structure with a more uniform distribution. Furthermore, Fig. 3(d) and 4(d) show that after six MDF passes, further dynamic recrystallization has resulted in the average grain size of 7.8 μm with a standard deviation of 3 μm, while Fig. 3(e) and 4(e) indicate that the average grain size and standard deviation are 4.9 and 2.9 μm, respectively, after eight passes of MDF process. This means that after 8 MDF passes the material exhibits the most uniform grain structure. Table 1 shows the changes in the average grain size of the nanocomposite before and after different passes of MDF process.
During all MDF passes, average grain size decreases compared to the unprocessed nanocomposite, and a more uniform grain size distribution is achieved. Furthermore, nanoparticles can prevent grain growth through pinning of grain boundaries and thus create a fine-grained structure during MDF at a constant temperature (Ref 21). The results have shown that average grain size decreases with the increase in the number of MDF passes. It can be said that with increase in the number of MDF passes or equivalent strain, dynamic recrystallization takes place in a more advanced state and decreases the fraction of the microstructure that has not undergone recrystallization. Furthermore, grain size distribution is more uniform, and finer grains are obtained after the MDF process compared to the unprocessed nanocomposites. In a study by Nie et al. (Ref 20) on microstructure and mechanical properties of magnesium-based AZ91/SiCp nanocomposite at different processing temperatures, the results indicated that increasing the number of MDF passes at the temperature of 370 °C resulted in a decrease in grain size. Their results showed that dynamic recrystallization (DRX) was the reason for the observed change in grain size, indicating that DRX progresses with increasing the number of MDF passes.
Figure 5 shows the EDX-MAP analysis of the AZ80/SiC nanocomposite. As a result of strong van der Waals forces, nanoparticles tend to agglomerate around each other and create nanoparticle clusters. These clusters, due to the lack of proper bonding between them and the matrix, act as weak points in the nanocomposite structure and provide suitable locations for crack nucleation. Furthermore, stress concentration in these areas increases the probability of brittle fracture. As a result, the characteristics of nanocomposites highly depend on uniform and suitable distribution of strengthening nanoparticles in the alloy matrix. The uniform distribution of nanoparticles and lack of cluster formation after the annealing process can be seen in Fig. 5. According to these results, it can be stated that SiC nanoparticles have a proper distribution in the matrix, and therefore, it can be concluded that stir casting is a suitable method for producing AZ80/SiC nanocomposite. In addition to the nanoparticles, the elemental maps are indicative of the presence of Mg17Al12 phase. The observed cluster of Al atoms in Fig. 5(c) implies that the gray coarse particles shown in Fig. 5(a) are mainly Mg17Al12 intermetallics.
Figure 6 shows the XRD pattern of the material after 8 MDF passes. As can be seen, Mg, Mg17Al12, and SiC are the only constitutive phases in the material. The weak peaks of the Mg17Al12 intermetallic compound show that this phase has been partially dissolved in the matrix after the initial annealing process, the fact that had already been demonstrated in Fig. 5(a). The only observable weak peak for SiC, which is detected at the 2θ of about 40°, is attributed to the low volume fraction of the added nanoparticles.
3.2 Shear Behavior
The shear stress-normalized displacement graph of the AZ80/SiC nanocomposite specimens after annealing and various passes of MDF process is presented in Fig. 7. As can be seen, SYS and USS of the AZ80/SiC nanocomposite are improved significantly due to the MDF processing. The graph of shear stress versus dimensionless displacement includes an elastic linear section, after which the specimen diverges from linear behavior before reaching a maximum point, similar to the tensile engineering stress–strain graph. The point of deviation from linear behavior is known as SYS, while the maximum point of the graph is known as USS of the specimen. The results indicate that after the second pass of MDF, SYS and USS increase from 123.7 and 158.9 MPa in the unprocessed condition to 132 and 176.2 MPa, respectively. This trend continues after the fourth pass of MDF by increasing the SYS and USS to 137.8 and 176.8 MPa, respectively. These quantities finally reach their maximum values of 164.6 and 194.1 MPa after the eighth MDF pass. This trend can be due to better distribution of nanoparticles and decrease in grain size (Ref 11), because grain size refinement plays an important role in improving the strength of materials (Ref 3). Table 2 shows SYS and USS values of annealed and MDFed nanocomposite specimens.
3.3 Tensile Properties
The engineering stress–strain curves obtained using uniaxial tensile test of AZ80/SiC nanocomposites, before and after 2, 4, 6, and 8 MDF passes, are shown in Fig. 8. As can be seen from the results, the yield stress and ultimate tensile strength of AZ80/SiC nanocomposites increase from 135 and 213.2 MPa to 150.8 and 241.2 MPa after 2 MDF passes, respectively. In general, improvement of tensile strength as a result of nanoparticle addition is often accompanied by decrease in other characteristics such as ductility. However, this decrease is not observed in magnesium-based nanocomposites reinforced with ceramic particles. This can be due to finer grain size, more uniform grain structure, activation of other slip planes and changes in crystalline structure (Ref 22). The YS and UTS values as well as elongation obtained from engineering stress–strain curves are presented in Table 3. According to these results, the second pass of MDF leads to an increase in tensile strength of the nanocomposite and trivial decrease in ductility compared to the unprocessed nanocomposite. After the fourth pass, elongation also shows an increasing trend along with YS and UTS values, due to smaller grain size and decrease in the number of larger grains. The highest YS value is observed after the eight pass of MDF process, which is equal to 200 MPa. UTS values of 241.2, 263.0, 290.4, and 309.5 MPa and elongations of 10.0, 10.9, 11.2, and 11.5% are obtained after 2, 4, 6, and 8 MDF passes, respectively. Therefore, highest tensile strength and ductility is observed after the eight pass of MDF. The YS, UTS and elongation values after eighth pass of MDF are 48.1, 45.2, and 8.5% higher than that of the unprocessed nanocomposite, respectively.
In general, mechanical properties in magnesium-based nanocomposites are highly dependent on grain size and microstructural changes. According to the Hall–Petch equation presented in Eq. (1), a decrease in grain size results in increase in yield stress and overall strength of the material.
In this equation, \({\upsigma }_{\mathrm{y}}\) is the yield stress, \({\upsigma }_{0}\) is initial yield stress, K is a constant coefficient and \(d\) is the average grain size. Based on this equation, decrease in average grain size results in increase in yield stress of the material. This means that more uniform grain structure with smaller average grain size results in more improvement in material’s yield stress based on the Hall–Petch mechanism (Ref 23).
However, the strength of nanocomposites is not only a function of their grain size. Other than Hall–Petch mechanism, other strengthening mechanisms such as Orowan, effective load transfer, and thermal mismatch can affect the final strength of nanocomposites (Ref 24). According to the results of tensile test, it can be said that increase in tensile strength is accompanied with increase in ductility, which is desirable for magnesium nanocomposites. It should also be noted that Hall–Petch equation and the inverse relation between yield stress and square root of mean grain size is more important in HCP metals due to their limited number of slip planes (Ref 2). Therefore, decrease in grain size and increase in the uniformity of microstructure, which starts with the addition of nanoparticles and continues until eighth pass of MDF, are the cause of improvement in tensile strength of nanocomposite specimens. The study by Nie et al. (Ref 9) has shown that in AZ91/SiC nanocomposite, increase in the number of MDF passes at 370 °C results to increase in yield stress and ultimate tensile strength. They concluded that the improvement in mechanical properties is due to dynamic recrystallization (DRX) and stated that increase in the number of MDF passes enhances the DRX process.
3.4 Microhardness Behavior
Figure 9 shows the variation of microhardness with the number of MDF passes, superimposed on the tensile and shear behaviors. According to these results, the trend of changes in yield stress after different MDF passes is similar to the changes in microhardness. This is due to the fact that decrease in grain size and increase in microstructure uniformity at higher number of MDF passes result in increase in both yield stress and microhardness. This trend can be explained based on the optical micrographs and Hall–Petch equation (Fig. 10). Our results are in agreement with those on the same composite processed by DECLE at constant temperature of 300 °C (Ref 25). The results of that study have shown that with increasing the number of passes and equivalent strain, a significant decrease in grain size occurred, and therefore, a substantial increase in strength and hardness was achieved. In another study by Guo et al. (Ref 26), the effect of continuous extrusion–compression (CEC) process on Mg-1wt.%SiC nanocomposite was investigated. Their results indicated that increasing the number of CEC passes results in a more uniform microstructure and decrease in grain size, leading to significant increase in hardness.
According to Fig. 10, we found the equation \({\upsigma }_{\mathrm{y}}=96.2+223.5{d}^{-0.5}\) (MPa) for the tested nanocomposite. It is of some interest to compare the obtained Hall–Petch coefficient with those reported for some other Mg composites. Lee et al. (Ref 27) found k = 140 MPa µm0.5 for AZ91-10 vo l%SiC composites. The smaller Hall–Petch parameter could be initiated from coarser particle size of 8-50 µm. In another study, Sahoo and Panigrahi (Ref 28) [28] examined mechanical properties of in situ (TiC-TiB2) reinforced AZ91 matrix composite. The sizes of the particles were in the range of 1-2 µm, and their volume fraction was 3.9%. They found k = 130 MPa µm0.5 for their processed composites. These comparisons clearly indicate that our composite containing nanoparticles and very fine-grained structures have significantly higher Hall–Petch parameter. This could stem from a more pronounced locking effect of the nanoscale particles and also higher density of grain boundary area in the processed composite. In contrast to the above cases, a study of AZ61/carbon nanotubes (CNTs) composites fabricated by the stir-casting method in the as-cast and aged conditions has shown relatively high k-values of 304.8 and 340.7 MPa µm0.5, respectively (Ref 29) [29 = Abbas]. This again emphasizes the significant effect of nanoparticles on the pinning of grain boundaries.
3.5 Fractography
The SEM images of the fracture surfaces of the tensile strength test samples are shown in Fig. 11. According to Fig. 11(a), due to the addition of SiC nanoparticles, the fracture surfaces contain both cleavage and dimples with various sizes. This bimodal structure of the fracture is also predictable due to the bimodal structure of AZ80/SiC nanocomposite. The dark and light parts of the image indicate the difference in depth, showing the plastic deformations of the surface and change of the fracture mechanism from brittle to ductile. Figure 11(b) shows the fracture surface of the sample after 2 passes of the MDF process, showing an increase in the number of the cleavage surfaces and a decrease in the ductility. According to Fig. 11(c), after the 8 passes, with the decrease in the grain size, the number of small dimples increases. Noticeable depth differences in different zones are observed, and compared to the other two samples, it has the highest ductile fracture effects. These results are very similar to the ductility results of the tensile test provided in Table 3.
4 Conclusions
In this study, the effect of multi-directional forging (MDF) process on microstructure and mechanical properties of AZ80/SiC nanocomposite, manufactured using the stir casting method, was investigated. The important results of the current study can be summarized as follows:
-
1.
By comparing the average grain size in different processing conditions, it can be concluded that at higher MDF passes, more uniform distribution of grains and their smaller size occurs compared to unprocessed specimen. The average grain size of the unprocessed nanocomposite after stir casting was equal to 36.7 μm, which decreased to 4.9 μm after 8 passes of MDF.
-
2.
After the eighth pass of MDF, shear yield stress and ultimate shear strength improved by 10.9 and 5.5%, respectively, compared to the un-MDFed specimen. This can be due to the strengthening effect of nanoparticles in the alloy matrix, better distribution of these particles at higher passes and decrease in grain size.
-
3.
Hardness increased significantly after the second pass of MDF, due to the decrease in grain size with the increase in the number of passes. The hardness of nanocomposite after the second MDF pass was 96.3 HV, which increased to its maximum value of 99.6 HV after eighth MDF pass.
-
4.
The YS, UTS, and elongation values of the nanocomposites after 8 MDF passes were 48.1, 45.2, and 8.5% higher than that of the unprocessed nanocomposite, respectively. During the MDF process, increase in mechanical strength is accompanied by increase in elongation, indicating improved ductility of the nanocomposite caused by the formation of a finer and more uniform grain structure.
-
5.
Microstructural examinations together with mechanical tests showed that the microstructure of AZ80/SiC nanocomposites becomes significantly finer and more uniform after 8 MDF passes, resulting in significant improvements in their mechanical properties.
References
F. Barati, M. Esfandiari, and S. Babaei, The Effect of 2% SiO2 Nanopowder on Mechanical Behavior of Mg AZ31, J. Stress. Anal., 2020, 5(1), p 69–76.
H.Z. Ye and X.Y. Liu, Review of Recent Studies in Magnesium Matrix Composites, J. Mater. Sci., 2004, 39(20), p 6153–6171.
S.M. Masoudpanah and R. Mahmudi, The Microstructure, Tensile, and Shear Deformation Behavior of an AZ31 Magnesium Alloy after Extrusion and Equal Channel Angular Pressing, Mater. Des., 2010, 31(7), p 3512–3517.
S. Aravindan, P.V. Rao, and K. Ponappa, Evaluation of Physical and Mechanical Properties of AZ91D/SiC Composites by Two Step Stir Casting Process, J. Magnes. Alloy., 2015, 3(1), p 52–62.
M.Z. Rong, M.Q. Zhang, Y.X. Zheng, H.M. Zeng, R. Walter, and K. Friedrich, Structure-Property Relationships of Irradiation Grafted Nano-Inorganic Particle Filled Polypropylene Composites, Polymer. Guildf, 2001, 42(1), p 167–183.
G.H. Majzoobi, K. Rahmani, and M. Kashfi, The Effect of Pre-Compaction on Properties of Mg/SiC Nanocomposites Compacted at High Strain Rates, J. Stress. Anal., 2020, 4(2), p 19–28.
H. Mozafari and F. Akbaripanah, Changes in Grain Size, Texture, and Mechanical Properties of AZ31/(TiO2)p Nanocomposites Processed by Isothermal Multidirectional Forging, J. Stress. Anal., 2020, 4(2), p 45–53.
M.J. Shen, X.J. Wang, C.D. Li, M.F. Zhang, X.S. Hu, M.Y. Zheng, and K. Wu, Effect of Submicron Size SiC Particles on Microstructure and Mechanical Properties of AZ31B Magnesium Matrix Composites, Mater. Des., 2014, 54, p 436–442.
K.B. Nie, K.K. Deng, X.J. Wang, T. Wang, and K. Wu, Influence of SiC Nanoparticles Addition on the Microstructural Evolution and Mechanical Properties of AZ91 Alloy during Isothermal Multidirectional Forging, Mater. Charact., 2017, 124, p 14–24.
F. Akbaripanah, M. Sabbaghian, N. Fakhar, P. Minárik, J. Veselý, P.T. Hung, G. Kapoor, O. Renk, K. Máthis, J. Gubicza, and J. Eckert, Influence of High Pressure Torsion on Microstructure Evolution and Mechanical Properties of AZ80/SiC Magnesium Matrix Composites, Mater. Sci. Eng. A, 2021, 826, p 141916.
K.B. Nie, K. Wu, X. Wang, K. Deng, Y.W. Wu, and M. Zheng, Multidirectional Forging of Magnesium Matrix Composites: Effect on Microstructures and Tensile Properties, Mater. Sci. Eng., 2010, 527, p 7364–7368.
N. Azizi and R. Mahmudi, Microstructure, Texture, and Mechanical Properties of the Extruded and Multi-Directionally Forged Mg–XGd Alloys, Mater. Sci. Eng. A, 2021, 817, p 141385.
Q.F. Wang, X.P. Xiao, J. Hu, W.W. Xu, X.Q. Zhao, and S.J. Zhao, An Ultrafine-Grained AZ31 Magnesium Alloy Sheet With Enhanced Superplasticity Prepared by Accumulative Roll Bonding, J. Iron. Steel. Res. Int., 2007, 14(5), p 167–172.
M.A. Salevati, A. Imam, R. Seifi, and F. Akbaripanah, The Effect of Repeated Upsetting Process on Microstructure, Shear Strength, and Fracture Toughness of SiC/AZ80 Nanocomposite, J. Mater. Eng. Perform., 2021 https://doi.org/10.1007/s11665-021-06215-z
A. Jamali and R. Mahmudi, Evolution of Microstructure, Texture, and Mechanical Properties in a Multi-Directionally Forged ZK60 Mg Alloy, Mater. Sci. Eng. A, 2019, 752, p 55–62.
M.A. Salevati, F. Akbaripanah, and R. Mahmudi, Microstructure, Texture, and Mechanical Properties of AM60 Magnesium Alloy Processed by Extrusion and Multidirectional Forging, J. Mater. Eng. Perform., 2019, 28(5), p 3021–3030.
X.G. Qiao, T. Ying, M.Y. Zheng, E.D. Wei, K. Wu, X.S. Hu, W.M. Gan, H.G. Brokmeier, and I.S. Golovin, Microstructure Evolution and Mechanical Properties of Nano-SiCp/AZ91 Composite Processed by Extrusion and Equal Channel Angular Pressing (ECAP), Mater. Charact., 2016, 121, p 222–230.
Y. Radi and R. Mahmudi, Effect of Al2O3 Nano-Particles on the Microstructural Stability of AZ31 Mg Alloy after Equal Channel Angular Pressing, Mater. Sci. Eng. A., 2010, 527(10–11), p 2764–2771.
S. Goyal, V. Karthik, K.V. Kasiviswanathan, M. Valsan, K.B.S. Rao, and B. Raj, Finite Element Analysis of Shear Punch Testing and Experimental Validation, Mater. Des., 2010, 31(5), p 2546–2552.
K.B. Nie, X.J. Wang, X.S. Hu, Y.W. Wu, K.K. Deng, K. Wu, and M.Y. Zheng, Effect of Multidirectional Forging on Microstructures and Tensile Properties of a Particulate Reinforced Magnesium Matrix Composite, Mater. Sci. Eng. A, 2011, 528(24), p 7133–7139.
X. Xia, Q. Chen, Z. Zhao, M. Ma, X. Li, and K. Zhang, Microstructure, Texture and Mechanical Properties of Coarse-Grained Mg–Gd–Y–Nd–Zr Alloy Processed by Multidirectional Forging, J. Alloys. Compd., 2015, 623, p 62–68.
M.P. Reddy, V. Manakari, G. Parande, F. Ubaid, R.A. Shakoor, A.M. Mohamed, and M. Gupta, Enhancing Compressive, Tensile, Thermal and Damping Response of Pure Al Using BN Nanoparticles, J. Alloys. Compd., 2018, 762, p 398–408.
S.F. Hassan, M. Paramsothy, F. Patel, and M. Gupta, High Temperature Tensile Response of Nano-Al2O3 Reinforced AZ31 Nanocomposites, Mater. Sci. Eng. A, 2012, 558, p 278–284.
J.B. Correia, H.A. Davies, and C.M. Sellars, Strengthening in Rapidly Solidified Age Hardened Cu-Cr and Cu-Cr-Zr Alloys, Acta. Mater., 1997, 45(1), p 177–190.
M.A. Salevati, A. Imam, R. Seifi, and F. Akbaripanah, Investigating the Microstructure, Hardness and Tensile Behavior of Magnesium AZ80 Alloy and AZ80/SiC Nanocomposite Manufactured Through Dual Equal Channel Lateral Extrusion (DECLE), Met. Mater. Int., 2020, 9, p 3538–3549.
W. Guo, Q. Wang, B. Ye, X. Li, X. Liu, and H. Zhou, Microstructural Refinement and Homogenization of Mg–SiC Nanocomposites by Cyclic Extrusion Compression, Mater. Sci. Eng. A, 2012, 556, p 267–270.
D.M. Lee, B.K. Suh, B.G. Kim, J.S. Lee, and C.H. Lee, Fabrication, microstructures, and tensile properties of magnesium alloy AZ91/SiCp composites produced by powder metallurgy, Mater. Sci. Technol, 1997, 7, p 590–595.
B.N. Sahoo and S.K. Panigrahi, Synthesis, characterization and mechanical properties of in-situ (TiC-TiB2) reinforced magnesium matrix composite, Mater. Des, 2016, 109, p 300–313.
A. Abbas and S.-J. Huang, Investigating the Hall-Petch Constants for As-Cast and Aged AZ61/CNTs Metal Matrix Composites and Their Role on Superposition Law Exponent, J. Compos. Sci, 2021, 5(3), p 103–112.
Author information
Authors and Affiliations
Corresponding author
Additional information
Publisher's Note
Springer Nature remains neutral with regard to jurisdictional claims in published maps and institutional affiliations.
This invited article is part of a special topical focus in the Journal of Materials Engineering and Performance on Magnesium. The issue was organized by Prof. C. (Ravi) Ravindran, Dr. Raja Roy, Mr. Payam Emadi, and Mr. Bernoulli Andilab, Ryerson University.
Rights and permissions
About this article
Cite this article
Akbaripanah, F., Zarin, M., Salevati, M.A. et al. Effects of Multi-Directional Forging on the Microstructure and Mechanical Properties of an AZ80/SiC Nanocomposite. J. of Materi Eng and Perform 32, 2676–2687 (2023). https://doi.org/10.1007/s11665-022-07307-0
Received:
Revised:
Accepted:
Published:
Issue Date:
DOI: https://doi.org/10.1007/s11665-022-07307-0