Abstract
Porous transparent films of TiO2 (anatase) were obtained by controlled hydrolysis of titanium tetraisopropoxide (sol-gel method) in the presence of a polyethylene glycol as a template agent with molar masses of 300, 600 and 1000 g/mol and α-terpineol as a high viscosity agent. The efficiency of the films in the photocatalytic degradation of Rhodamine 6G is correlated with their porosity and films’ thickness. Higher photoactivity of the obtained films compared with a non-porous TiO2 film was observed for TiO2(300) and TiO2(600) whereas the lower activity was noted for TiO2(1000). The size of anatase crystals is increased proportionally to the precursor’ gelation time and is accompanied by a decrease of the specific surface area and porosity of the film. The presence of polyethylene glycol slowed down TIPT’s hydrolysis rate. It is shown that the viscosity of the precursor is the key factor in the preparation of titania films with certain crystal size, thickness and high photocatalytic activity.
Similar content being viewed by others
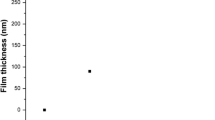
Explore related subjects
Discover the latest articles, news and stories from top researchers in related subjects.Avoid common mistakes on your manuscript.
Introduction
Nanosized titanium dioxide in the form of powders or films is widely used to create photocatalysts, superhydrophilic coatings, sensors, solar cells, electrochromic lightening windows, as well as mineralization of many environmental pollutants [1,2,3]. The use of TiO2 in the form of a film has a number of advantages over its powder form (convenience in removing from the solution, the ability to apply on the glass or ceramic surfaces etc), but the specific surface area of film is much smaller than that in the powder, which affects the efficiency of photocatalysis. To increase the photocatalytic activity of the film, the titanium dioxide can be modified by metal ions and/or non-metals [4]. The synthesis of porous films with a developed surface is also an extremely promising method for their photocatalytic activity improvement [5,6,7]. In this case, the pore-formation substance is added to the precursor at the stage of the sol-gel transition using the template agent. Polyethylene glycol (PEG) is one of the best templates for the morphological alteration of titania-based films [8]. The use of viscous agents in precursors allows the films’ production of controlled thickness [9].
Despite the large number of publications, investigation of the effect of the molecular weight of PEG on the photocatalytic activity of the TiO2 films is controversial. The authors [8] claimed that the activity of TiO2 films synthesized by the spray-pyrolysis method in the presence of PEG was influenced by the ratio of TIPT: PEG rather than the molecular weight of the polymer. It is noted [10] that the activity of the photocatalyst is increased with the increase of molar mass of the pore forming agent. However, our preliminary data [11] and results [12] indicated a decrease in photoactivity when PEG molar mass was increased.
Controlled synthesis of mechanically stable TiO2 films of high optical quality and high photocatalytic activity is still actual. In this paper, the effects of the initial precursor composition, the molecular weight of PEG and the structuring processes in the sol on the stability of the precursor, the thickness and porosity of the films and their photocatalytic activity were investigated.
It is known that the variation of the photocatalytic activity of films obtained from viscous precursors is attributed to the initial conditions of synthesis, such as the ratio of components in the precursor [13], and the different length of the oligomer of the porous former [7, 14]. In this work, the films and powders of titanium dioxide were obtained using polyethylene glycol (PEG) pore forming agent with different molar masses of 300, 600 and 1000 and α-terpineol as a viscous agent. The films were deposited on glass substrates by dip-coating technique with the following calcination at 500 °C. For comparison, TiO2 powders from the same precursors were also synthesized: the corresponding gels were left for 1 month in air and then calcined at 500 °C. The resulting nanosized porous TiO2 films and powders have a crystalline structure of anatase. It is shown that photocatalytic activity of the films of the same composition and conditions of synthesis obtained from viscous initial sols is related to the processes of structure formation in the precursor.
Experimental
Two initial solutions (A and B) as precursors for the preparation of porous TiO2 films contained α-terpineol to significantly increase the viscosity of the solution [9], and PEG300, PEG600 or PEG1000 (Loba feinchemie) as pore formers and acetic acid as an acid catalyst have been used. Solution A was prepared by mixing of titanium tetraisopropoxide 97% (TIPT) (Aldrich) in iso-propanol (IPA) (UkrReAChem), α-terpineol (Aldrich) and the corresponding template agent (PEG). Solution B consisted of the following components: IPA, distilled water and acetic acid. After stirring, solution B was added dropwise to solution A. The concentration of TiO2 in the precursor was 4% by weight. The components of solution A were taken in the following quantities: TIPT—0.34 mol, α-Terpineol—2.12 mol, isopropanol—4.57 mol, PEG300, PEG600 and PEG1000—0.19 mol. The components of solution B were iso-propanol—0.78 mol, CH3COOH—0.37 mol, H2O—1.11 mol. The films are marked as TiO2(300), TiO2(600) and TiO2(1000) indicating the type of the template agent used in the synthesis procedure, as namely PEG300, PEG600 and PEG1000, respectively.
The precursors of the films were coated on the glass substrates by dip-coating procedure at a constant rate of 9 cm/min. The substrates were carefully washed with hydrochloric acid and distilled water beforehand and, then, dried in an oven at 150 °C. Dip-coated TiO2 films were calcined at 500 °C for 1 h. In the case of multi-layer films, the heat treatment was repeated for every layer.
The thickness and refractive index of thin films were measured by the method of polygonal ellipsometry on an LEF-3 M (λ = 632.8 nm) ellipsometer. The transmission spectra of the films were recorded on a Perkin Elmer Lambda 35 UV/VIS spectrophotometer. The porosity of the films is calculated using the equation:
where n is the refractive index of the porous film, nd is the refractive index of non-porous film.
The viscosity of the initial solutions was measured on a cylindrical rotational viscometer at a constant temperature. The viscosity measurement error is ± 1%.
The photocatalytic procedure was carried out in a quartz reactor containing a mixture of anatase nanocomposite and 20 ml of Rhodamine 6G aqueous solution (2.5 × 10−5 mol L−1). The open reactor enabled a continuos inflow of oxygen which supported the reaction; the solution was continuously mixed during the experiments. The reaction system was irradiated by an UV light lamp PRK-1000 (power 1000 W). The distance between the reactor and lamp was 50 cm. During the experiments, a certain amount of Rhodamine 6G solution was periodically taken out from the reactor to obtain the absorption spectra (an UV-VIS spectrometer Lambda-35) and the concentration of the dye solution was calculated.
Results and discussion
The obtained optically transparent TiO2 films exhibit high adhesion to glass substrate. As seen from Fig. 1a, the film thickness affects the optical properties of the films where the interference maxima and minima are observed in the transmission spectra. This feature can be used to determine the thickness of the films by spectral method. To compare the accuracy of the proposed method of thickness determination, the data obtained using ellipsometry are also used. The thickness of the coating depends on the number of applied layers. However, to obtain the films with high transparency and satisfied mechanical properties, not more than seven layers were dip-coated with the calcination of every layer at 500°. Due to the multi-layered coatings, the films of thickness in the range of 600–1100 nm can be obtained. Figure 1b shows that the film thickness depends on the presence of the template agent as well as on its molar mass.
The obtained films crystallized to anatase without traces of other crystalline phases. The crystal size of anatase in most samples is detected to be less than 25 nm, wherein, the TiO2(300) films contained a fraction of crystals of size up to 5 nm similar to that published in [1].
It was observed that the thickness of the films coated on the substrate from the same precursor after different aging periods is varied. Thus, the thickness of TiO2(600) films coated on the substrate immediately after the precursor preparation and aging for 140 min was changed from 126 to 222 nm, respectively (Table 1). The refractive index is also nonlinearly increased from 2.07 to 2.37 while the calculated porosity of the coating is reduced. The increase in the refractive index occurs without changing of the crystalline structure of the films and, therefore, the change in the effective density of the film is suggested. The films density and specific masses (g/cm2) are increased from 1.39 g/cm3 and 1.75 g/cm2 to 1.74 g/cm3 and 3.88 g/cm2, respectively (Table 1). Thus, the ripening period of sol and its content influenced the structural parameters of the resulting films. The longer the maturing time of the sol, the greater the length of the oligomer and, consequently, the size of the titania crystals in the coating is increased. Such significant changes in properties can often exceed the changes made by the variety of used pore-formation agents and affect the effectiveness of films in photocatalytic reactions. It must be stressed that the freshly prepared sol (within 5 min after adding of all components) was used for every layer coating in the case of the films involved in the determination of the dependence of film thickness on the number of layers (Fig. 1b).
The similar changes in the physical properties have been also observed for TiO2, TiO2(300) and TiO2(1000) films due to the processes of structuring taking place in a viscous initial solution until a bulk polymer network is formed. It is accompanied by a change of the precursor’ viscosity with time (Fig. 2a), which is significantly dependent on the temperature as well (Fig. 2b).
The increase of the precursor viscosity leads to the formation of thicker film and increases the maturation time of the initial solution. The change in viscosity also affects the rate of hydrolysis, which may vary depending on a number of parameters: the water content, temperature, etc. (Fig. 2b). The change in the specific mass of films (mass of 1 cm2) over time is similar to the dependence of viscosity on time (Fig. 3).
It is known that TIPT reacts rapidly with water molecules in the precursor (reactions 1, 2 and 3), whereas the process of hydrolysis of alkoxides can be much more complicated in the presence of stabilizers (acids) [15]. The introduction of acid to the initial TIPT solution allows controlling the rate of hydrolysis [15]:
The film morphology is determined by several main factors: surface tension of the film precursor, oligomer polycondensation, presence of PEG, and solvent. Hydrolysis is a gradual process, the C3H7O groups are hydrolyzed sequentially. This is followed by dehydratation and polycondensation processes. The molecule of PEG is exothermically adsorbed on an oligomer –Ti–O–Ti– forming a hydrogen bond [15].
The further process of structuring and polymerization consists in the formation of an oligomer/PEG composite, where PEG determines the size of the crystals. PEG with smaller length of the oligomer forms a denser net in the precursor, thereby limiting the growth of the oligomer –Ti–O–Ti– and vice versa. PEG with higher molar mass and length of the oligomer leads to the increase of TiO2 crystals. As a result, the films obtained from freshly prepared precursors differ in refractive indexes. Thus, TiO2, TiO2(300), TiO2(600) and TiO2(1000) films have refractive indexes of 2.40, 2.15, 2.20, and 2.30, respectively. The highest value of the refractive index obtained for nonporous TiO2 film is explained by the lowest porosity. All films exhibited a secondary porosity due to polycrystallinity and the presence of voids between the crystals (Fig. 4).
The described above processes affect the photocatalytic activity of the obtained films. Photocatalytic oxidation of a dye rhodamine 6G has been studied. The reaction was carried out in the presence of TiO2 films under UV irradiation with a mercury lamp PRK-1000 on air under vigorous stirring. As seen from Fig. 5, the photocatalytic reaction rate (r) depends on the thickness of the film leading to the suggestion that total film volume is responsible for the efficient photocatalytic decomposition.
The photocatalytic activity is estimated as a relative change of R6G concentration per 1 g (∆C/C0m) of the film after 20 min. of irradiation. The photocatalytic activity crucially depends on the time of the gelation of the precursor (Fig. 6).
The nonlinear change in the precursor viscosity is observed: the longer the maturing time of the sol, the larger the size of the crystals is formed and, hence, the decrease in the specific surface area and porosity of the film occurs. This leads to a decrease in the photoactivity of the films (Fig. 6). However, a significant increase of the precursor viscosity provides an increase in film thickness. It can be concluded that the processes of crystals growth and the thickness of the coating determine the activity of TiO2 films. The film obtained from the precursor after 10 min of gelation exhibited a maximal photocatalytic activity. The photocatalytic activity of the films is decreased as follows: TiO2(300) > TiO2(600) > TiO2 > TiO2(1000) (Fig. 6).
Conclusions
The photocatalytic activity of porous nanosized TiO2 films depends critically on the composition of the precursor and film formation conditions: the pore-forming and viscous agents as well as the dynamics of the structuring processes. Therefore, for each type of film, the optimal ratio of crystal size/thickness is found, which can be adjusted by controlling the rheological characteristics of the precursor. The highest photocatalytic activity is observed for TiO2(300) and TiO2(600) films obtained from the freshly prepared precursor. The effectiveness of photocatalytic degradation of R6G dye in the presence of TiO2(1000) films is achieved by increasing the thickness and mass of the films.
References
U.I. Gaya, J. Photochem. Photobiol. 9, 1 (2008)
M. Ibadurrohman, K. Hellgardt, A.C.S. Appl, Mater. Interfaces. 7, 9088 (2015)
A. Ebrahimi, M. Kitano, K. Iyatani, Y. Horiuchi, M. Takeuchi, M. Matsuoka, M. Anpo, Res. Chem. Intermed. 39, 4 (2013)
X. Chen, Y. Lou, S. Dayal, X. Qiu, R. Krolicki, C. Burda, C. Zhao, J. Becker, Nanosci. Nanotechnol. 5, 1408 (2005)
N. Negishi, K. Takeuchi, T. Ibusuki, Appl. Surf. Sci. 121/122, 417 (1997)
W.I. Nawawi, R. Zaharudin, M.A.M. Ishak, K. Ismail, A. Zuliahani, Appl. Sci. 7, 24 (2017)
J.M. Calderon-Moreno, S. Preda, L. Predoana, M. Zaharescua, M. Anastasescu, M. Nicolescu, M. Stoic, H. Stroescu, M. Gartner, O. Buiu, M. Mihaila, B. Serban, Ceram. Int. 40, 2209 (2014)
K. Kajihara, K. Nakanishi, K. Tanaka, K. Hirao, N. Soga, J. Am. Ceram. Soc. 81, 2670 (1998)
N. Negishi, K. Takeuchi, J. Sol-Gel. Sci. Technol. 22, 23 (2001)
B. Guo, Z. Liu, L. Hong, H. Jiang, Surf. Coat. Technol. 8, 24 (2005)
V. Gayvoronsky, V. Timoshenko, M. Brodyn, A. Galas, S.A. Nepijko, Th Dittrich, F. Koch, I. Petrik, N. Smirnova, A. Eremenko, M. Klimenkov, Phys. Stat. Sol. C. 2, 3303 (2005)
A.A. Santos, P.A. Pena, E.M. Cordoba, Quim. Nova 35, 1931 (2012)
S. Bu, Z. Jin, X. Liu, T. Yin, Z. Cheng, J. Mater. Sci. 41, 2067 (2006)
J. Yu, J.C. Yu, B. Cheng, X. Zhao, Z. Zheng, A.S.K. Li, J. Sol-Gel. Sci. Technol. 24, 229 (2002)
S. Bu, Z. Jin, X. Liu, H. Du, Z. Cheng, J. Sol-Gel. Sci. Technol. 30, 239 (2004)
Author information
Authors and Affiliations
Corresponding author
Additional information
Publisher's Note
Springer Nature remains neutral with regard to jurisdictional claims in published maps and institutional affiliations.
Rights and permissions
About this article
Cite this article
Petrik, I., Frolova, E., Turchin, A. et al. Design of titania porous films controlled by precursors’ viscosity for photocatalytic application. Res Chem Intermed 45, 4113–4120 (2019). https://doi.org/10.1007/s11164-019-03894-1
Received:
Accepted:
Published:
Issue Date:
DOI: https://doi.org/10.1007/s11164-019-03894-1