Abstract
A novel type of Epoxy Resin (EP)/Copper(II) acetylacetonate (Cu(acac)2) composites is developed and applied to improve electroless plating. This efficient and palladium-free process is based on the EP filled with various mass fractions of Cu(acac)2 via ball milling. The thermal stability of the composite of EP/Cu(acac)2 was performed with corresponding instruments. Moreover, the results of the viscosity and adhesion strength show that the viscosity of sample is positively correlated with the mass fraction of Cu(acac)2 in the composite. On the contrary, the shear strength of sample coated on FR-4 diminishes with the increasing fraction of Cu(acac)2. Results of parametrical optimizing reach the conclusion that under the condition of 50 °C for 15 min by electroless deposition (ELD) of copper, EP containing 40% Cu(acac)2 composites yields the best result.
Similar content being viewed by others
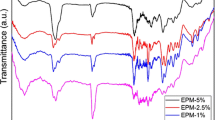
Explore related subjects
Discover the latest articles, news and stories from top researchers in related subjects.Avoid common mistakes on your manuscript.
1 Introduction
With the flourishing development of printed circuit board (PCB) industry, copper plating process has been playing an essential role in manufacturing conductive circuits for decades [1, 2]. Compared with the traditional electroless deposition (ELD) which is a complicated process involving palladium (Pd) as catalyst to initiate the electroless plating on PCB, this process with copper acetylacetone (Cu(acac)2) which is formed by simple stirring at a molar ratio of acetylacetone to copper acetate 2:1, is able to replace the expensive metals for catalysis [3, 4]. Therefore, it significantly cuts the cost of production. What’s more, acetylacetone (Hacac) whose pKa is about 8–9 [5, 6], is used as a coordination agent to chelate heavy metal ions [7], making the system stable. Choosing Cu(acac)2 instead of palladium as catalyst will certainly improve the electroless plating technique.
Epoxy Resin (EP) with good compatibility, high heat resistance, excellent mechanical performance and low cost is widely applied in the manufacture of PCB. Moreover, it is reported that the amount of the fiber-glass-epoxy-resin (FR-4) type copper clad is dominant (about 90%) in the manufacture of PCB [8]. In spite of various technological applications of EP composites [9,10,11,12], studies over EP composites prepared with Cu(acac)2 have not been reported in the literature. In this work, the aim is to modify the EP by doping with Cu(acac)2 to initiate the electroless plating on the FR-4. We prepared EP/Cu(acac)2 to form the composed material with various concentrations of Cu(acac)2 using a ball milling method. Hence, electroless plating on EP/Cu(acac)2 composite is operated in three steps: (1) heat curing EP/Cu(acac)2 on the FR-4; (2) the reduction of Cu2+ into Cu0 on the FR-4 surface by NaBH4, acting as catalysts of electroless plating; (3) the FR-4 metallization through electroless plating. Finally, the samples of EP/Cu(acac)2 were performed by thermogravimetric analysis (TGA) and differential scanning calorimetry (DSC). Furthermore, the formed layer of conductive copper on the FR-4 was evaluated by scanning electron microscopy (SEM), X-ray diffraction (XRD) and metallographic microscope.
2 Experimental
2.1 Materials
FR-4 was cut into 2 × 5 cm2 pieces and washed with regular detergents and deionized water before use. Bisphenol A diglycidyl ether (DGEBA, C18H17Br4ClO3) was selected as polymer matrix of the EP. And 1-cyanoethyl-2-ethyl-4-methylimidazole (2E4MZ-CN, C9H13N3) was employed as catalyst. Hexahydro-4-methylphthalic anhydride (MHHPA, C9H10O3) was corresponding hardener. Hacac (C5H8O2) and Copper(II) acetate monohydrate (Cu(CH3COO)2·H2O) were used for Cu(acac)2 synthesis. Sodium borohydride powder (NaBH4) was introduced for the copper reduction. Sulfuric acid (H2SO4), butanone (C4H8O) and sodium persulfate (Na2S2O8) were used as received. Then the plating bath was a homemade copper plating bath made of copper salt (CuSO4·5H2O), formaldehyde (HCHO), 2,2′-bipyridine (C10H8N2), sodium hydroxide (NaOH) and ethylene diamine tetraacetic acid (EDTA, C10H16N2O8). These materials used without undergoing any processing. In addition, all water in the experiment was deionized.
2.2 Preparation and treatment of EP/Cu(acac)2
Cu(CH3COO)2·H2O was dispersed in Hacac and stirred to form Cu(acac)2. 2.0 g DGEBA and 1.6 g MHHPA was mixed to synthesize EP. Then the catalyst 2E4MZ-CN was added to initialize the curing reaction [13]. EP containing 10–90% Cu(acac)2 was mixed with 10 mL butanone. A ball-milling in planetary ball-mill for 3 h was performed to enhance the compatibility between Cu(acac)2 with EP. At last, EP/Cu(acac)2 composites were coated on the FR-4 and cured for 30 min at 160 °C.
As-cured EP and EP/Cu(acac)2 on FR-4 were soaked in solution with 50 g/L Na2S2O8 and 20 mL/L H2SO4. Then, the treated substrate was immersed in 2 mol/L NaBH4 solution until Cu2+ was reduced to Cu0. Both of the two steps above were reacted under room temperature for 5 min. Finally, the surface-activated FR-4 substrates were placed in the electroless copper plating bath at 50 °C under ambient conditions. The homemade electroless copper plating bath contained CuSO4·5H2O as a source of Cu2+ (7.86 g/L), 10.5 g/L NaOH, 2 mg/L 2,2′-bipyridine, 30 g/L EDTA as complexing agent and 10 mL/L HCHO as a reducing agent, with a pH of 12–13.
3 Results and discussion
3.1 EP/Cu(acac)2 composite for ELD
EP consists of DGEBA monomer, the monomer contains a –COO–CO– structure and O which include lone pair electrons that interact with Cu2+. Moreover, the N atom in –C=N–C– group of the 2E4MZ-CN can also coordinate with the Cu2+ by the lone pair electrons. When EP is mixed with Cu(acac)2, the Cu2+ in the copper-containing EP exists in the coordination state. What’s more, Cu2+ is subsequently reduced by NaBH4 into Cu0 to serves as a catalyst for ELD. Finally, a copper layer is electroless deposition on the substrate. The rate of ELD of copper as well as the plated copper density is both proportional to the weight fraction of catalyst (Cu2+ in this case). Thus a high weight fraction of Cu(acac)2 is preferred. On the other hand, the viscosity test is necessary because the viscosity of the EP/Cu(acac)2 affects the resolution of the pattern formed on the substrate [14]. The corresponding results are shown in Table 1 (ƞ stands for viscosity).
Table 1 shows the viscosity of EP/Cu(acac)2 obviously increases with the rising weight fraction of Cu(acac)2. In order to ensure the coating thickness and smoothness, we chose EP/Cu(acac)2 with 10–50% Cu(acac)2 for ELD. Figure 3 displays the deposition results of patterns printed with EP/Cu(acac)2 in different weight fraction of Cu(acac)2. The FR-4 was taken out of the deposition solution after ELD. Then, the color of the FR-4 substrate changed in different degrees. In Fig. 3a, group 1# shows no sign of copper layer deposited by ELD and the other groups’ surface were changed by copper deposit (Fig. 3b–e).
As the reaction progresses, CuSO4 and HCHO are both persistently consumed until the deposition gradually stops. Cu2+ in EP/Cu(acac)2 is reduced by NaBH4, which initiates the electroless copper plating. Subsequently the reduced copper, the catalyst keeps the reaction going. The activity of copper can be maintained by controlling the deposition rate [15]. The EP/Cu(acac)2 with low weight fraction of Cu(acac)2 leads to attenuated activity of the reduced copper, which provides an explanation for the incomplete coating of groups 1#, 2# and 3#. In contrast to the three groups of experiments, the electroless copper layer in groups 4# and 5# completely covered the substrate. Moreover, the different concentration of Cu2+ in the two groups leads to different coating roughness. All the results are shown in Fig. 1.
As shown in Fig. 2, with the reduced electroless plating time, the EP containing 40 and 50% Cu(acac)2 is capable to deposit sufficient copper covering the substrate. In order to observe the morphology of the chemical deposited copper layer, the samples were examined by SEM (Fig. 3). The images of Fig. 3 display the pattern with some pores and clusters which contribute to the rough surface to further improve the electromigration reliability of Cu inter-connects. However, the clusters of Fig. 3a is obviously larger than (b), the surface of 7# is smoother than the one of 6# because of the higher content and distribution of Cu2+, which was consistent with the ones shown in Fig. 2a, b [16].
In XRD spectra, the peaks of the samples 6# and 7# are found around 43.3°, 50.4° and 74.1°, corresponding to the (111), (200) and (220) planes of the cubic copper structure (Fig. 4), respectively. Due to the lower surface energy of the [111] planes aligned parallel to the surface, the intensity of [111] orientation peak is stronger than that of [200] [17, 18]. Moreover, the preference of (111) copper crystal plane can be achieved directly without annealing treatment [19].
In respect of adhesion, the copper coating on the substrate was tested against scraping with a Cross-Cut Tester. Scotch tape test [20] was performed on freshly prepared samples (the results are shown in Fig. 5). According to the standard (ISO2409-1992), the sample 6# and 7# were qualified. However, in order to save the copper source cost, 40% Cu(acac)2 is selected to be mixed with EP.
Finally, the cross-sectional area of the coating was observed and the thickness of the coating was measured to be 4.90 µm by the metallographic microscope for 6# (Fig. 6). Therefore, the electroless plating rate of copper reached 19.6 µm/h, which is a promisingly high deposition rate [19].
3.2 Cured EP and EP/Cu(acac)2 on the FR-4 by the shear bond strength testing
Shear bond strength testing was conducted to evaluate the pure EP and EP/Cu(acac)2 fused to the FR-4. According to the standard GB/T7124-2008, an automatic digital universal tensile testing machine (LYWN-Z10000N) was selected for testing, and the shear area was 12.5 × 25 mm2. With the increase of the content of Cu(acac)2, the shear strength of the composites and the FR-4 was getting smaller. Namely, with the increase of the weight of Cu(acac)2, the composite material coated on the FR-4 became easier fall off. Figure 7 shows that the samples with mass fraction of the EP/Cu(acac)2 less than 50% yielded the shear force between composite material and the FR-4 greater than 20 MPa, which sufficiently meets the requirement of subsequent processing.
3.3 The thermal stability of cured EP and EP/Cu(acac)2
The thermal stability of cured EP and EP/Cu(acac)2 were analyzed by TGA in a nitrogen atmosphere at the heating rate of 10 °C/min. As shown in Fig. 8a, the weight of the EP and EP/Cu(acac)2 started to decrease at 50 °C due to the volatility of butanone. The curve shows that a 70 wt% loss occurred at the temperature of 440 °C. During this period, Hacac, MHHPA and Cu(acac)2 were all decomposed by heat. Decomposition temperature for EP was around 420 °C, which is consistent with the performance of DGEBA and MHHPA cured polymer. The operating temperature for PCB is around 260 °C in reflow-soldering process, which is much lower than 350 °C [13]. Therefore, the EP and EP/Cu(acac)2 are competitive candidates to interconnect the isolated layers even under reflowing operation at higher temperature. Moreover, the thermal stability of EP and EP/Cu(acac)2 qualities lost around 490 °C [21, 22].
DSC was used to monitor the curing behavior in Fig. 8b. Comparatively, the curves of cured EP and EP containing 40% Cu(acac)2 show the similar exothermic behavior. It is well known that the peak temperature of the DSC exothermic curve is often taken to evaluate the reactivity of the compound in curing reactions. The lower the temperature of the peak is, the higher the reactivity is [23]. Obviously, the exothermic peak for the ring-opening reaction of the epoxy group is about 160 °C, so the curing reaction of DGEBA and MHHPA under the condition of 160 °C. The Cu(acac)2 begins to decompose at about 250 °C. But the pure EP did not change at that temperature. As a result, the DSC and TGA curves show that an excellent thermal stability of EP/Cu(acac)2 composites will survive the heating processes in industrial PCB manufacture.
4 Conclusion
The developed composite of EP/Cu(acac)2 to apply ELD on FR-4 substrate shows excellent performance of the copper coating. The percolation region for EP/Cu(acac)2 falling in the region of Cu(acac)2 filler with 40 and 50 wt% is able to electroless deposit a layer of copper covering the entire area of the coated composite under water-bath heating at 50 °C for 15 min. However, according to production costs and the shear force analyses, the best fraction is 40% for Cu(acac)2 in composite. Moreover, the results of the EP/Cu(acac)2 composite of TGA and DSC confirm that the full reaction between DGEBA and HMMPA form epoxy polymer as the adhesive between Cu(acac)2 and the FR-4. In the future, the EP/Cu(acac)2 composite material should be applied to functional printing, flexible electronics and other device manufacturing field [24].
References
L. Ji, C. Wang, S. Wang et al., Multiphysics coupling simulation of RDE for PCB manufacturing. Circuit World 41(1), 20–28 (2015)
Y. Chen, W. He, X. Chen et al., Plating uniformity of bottom-up copper pillars and patterns for IC substrates with additive-assisted electrodeposition. Electrochim. Acta 120, 293–301 (2014)
D. Nicolas-Debarnot, M. Pascu, C. Vasile et al., Influence of the polymer pre-treatment before its electroless metallization. Surf. Coat. Technol. 200(14–15), 4257–4265 (2006)
N.A. Malvadkar, G. Demirel, M. Poss et al., Fabrication and use of electroless plated polymer surface-enhanced Raman spectroscopy substrates for viral gene detection. J. Phys. Chem. C 114(24), 10730–10738 (2010)
S. Coussan, Y. Ferro, A. Trivella et al., Experimental and theoretical UV characterizations of acetylacetone and its isomers. J. Phys. Chem. A 110(11), 3920–3926 (2006)
R.R. Lozada-Garcia, J. Ceponkus, W. Chin et al., Acetylacetone in hydrogen solids: IR signatures of the enol and keto tautomers and UV induced tautomerization. Chem. Phys. Lett. 504(4–6), 142–147 (2011)
H.W. Peng, M.S. Kuo, Determination of trace amounts of beryllium (II) in drinking water and of beryllium vapor in air by graphite-furnace atomic absorption spectrophotometry using acetylacetone as a chelating agent. Anal. Sci. 16(2), 157–161 (2000)
Y. Chen, Q. Gao, X. He et al., Enhancing adhesion performance of no-flow prepreg to form multilayer structure of printed circuit boards with plasma-induced surface modification. Surf. Coat. Technol. 333, 24–31 (2018)
S. Wang, Y. Tu, S. Xu et al., Electrical performance of TGPAP and DGEBF-based epoxy resin insulation materials for superconducting magnets. Fusion Eng. Des. 125, 118–122 (2017)
F.H. Gojny, M.H.G. Wichmann, U. Köpke et al., Carbon nanotube-reinforced epoxy-composites: enhanced stiffness and fracture toughness at low nanotube content. Compos. Sci. Technol. 64(15), 2363–2371 (2004)
H. Pihtili, An experimental investigation of wear of glass fibre–epoxy resin and glass fibre–polyester resin composite materials. Eur. Polym. J. 45(1), 149–154 (2009)
T. Prasse, J.Y. Cavaille, W. Bauhofer, Electric anisotropy of carbon nanofibre/epoxy resin composites due to electric field induced alignment. Compos. Sci. Technol. 63(13), 1835–1841 (2003)
G. Zhou, Y. Mao, C. Wang et al., Fabrication of silver electrically conductive adhesive to apply in through-hole filling for PCB interconnection. J. Mater. Sci.: Mater. Electron. 27(9), 9186–9190 (2016)
M. Kuang, L. Wang, Y. Song, Controllable printing droplets for high-resolution patterns. Adv. Mater. 26(40), 6950 (2014)
T. Zhang, X. Wang, T. Li et al., Fabrication of flexible copper-based electronics with high-resolution and high-conductivity on paper via inkjet printing. J. Mater. Chem. C 2(2), 286–294 (2013)
J.N. Balaraju, K.S. Rajam, Influence of particle size on the microstructure, hardness and corrosion resistance of electroless Ni–P–Al2O3 composite coatings. Surf. Coat. Technol. 200(12–13), 3933–3941 (2006)
L.E.E. Chang-Min, L.I.M. Jun-Hyung, S.M. Hwang et al., Characterization of flexible copper laminates fabricated by Cu electro-plating process. Trans. Nonferr. Met. Soc. China 19(4), 965–969 (2009)
V.A. Vas’ Ko, I. Tabakovic, S.C. Riemer et al., Effect of organic additives on structure, resistivity, and room-temperature recrystallization of electrodeposited copper. Microelectron. Eng. 75(1), 71–77 (2004)
Y. Sung, Y.H. Chou, W.H. Hwu et al., Electroless copper deposition by non-isothermal deposition technology. Mater. Chem. Phys. 113(1), 303–308 (2009)
C.M. Madl, P.N. Kariuki, J. Gendron et al., Vapor phase polymerization of poly (3, 4-ethylenedioxythiophene) on flexible substrates for enhanced transparent electrodes. Synth. Met. 161(13), 1159–1165 (2011)
F. Liu, Z. Wang, Y. Wang et al., Copolymer networks from carboxyl-containing polyaryletherketone and diglycidyl ether of bisphenol-A: preparation and properties. J. Polym. Sci. B 48(23), 2424–2431 (2010)
C. Luo, J. Zuo, Y. Yuan et al., Synthesis and characterization of high refractive epoxy prepolymers with different molecular structures. High Perform. Polym. 26(4), 477–482 (2014)
Z. Tao, S. Yang, J. Chen et al., Synthesis and characterization of imide ring and siloxane-containing cycloaliphatic epoxy resins. Eur. Polymer J. 43(4), 1470–1479 (2007)
Y. Shacham-Diamand, T. Osaka, Y. Okinaka et al., 30 years of electroless plating for semiconductor and polymer micro-systems. Microelectron. Eng. 132, 35–45 (2015)
Acknowledgements
This work is supported by Guangdong Application Technology Program (No. 2015B010127012) and National Science Foundation of China (Nos. 61474019 and 21603027).
Author information
Authors and Affiliations
Corresponding authors
Rights and permissions
About this article
Cite this article
Li, J., Zhou, G., Hong, Y. et al. A composite of epoxy resin/copper(II) acetylacetonae as catalyst of copper addition on insulated substrate. J Mater Sci: Mater Electron 29, 9460–9465 (2018). https://doi.org/10.1007/s10854-018-8979-2
Received:
Accepted:
Published:
Issue Date:
DOI: https://doi.org/10.1007/s10854-018-8979-2