Abstract
This paper presents a framework for designing a closed-loop green supply chain network (CLGSCN) that incorporates a redundancy strategy for maximum reliability and eco-friendliness. The network consists of production centers, repairs, and spare parts, with maintenance outsourced to ensure that spare parts circulate within the network for as long as possible. The proposed multi-objective mixed-integer program considers environmental considerations, service costs, routing decisions, cycle times, and assignments, with active and cold standby strategies for maximum reliability. A hybrid heuristics algorithm and multi-choice meta-goal programming with utility function are applied to solve the multi-objective model. The case study demonstrates the applicability of the model in real-world scenarios, offering valuable insights for optimized spare-part supply for maintenance and delivery. Sensitivity analyses show that the objectives are highly sensitive to the parameters, including the failure rate, demand, and reliability of the components, and results show an approximate decrease of 15.3% in the total cost and an increase of 2.83% in eco-friendly parts and finally increase of 11.25% in reliability with active standby strategy. Overall, this paper contributes to the field of supply chain management for advanced manufacturing systems both theoretically and practically, with potential benefits for businesses and society.
Similar content being viewed by others
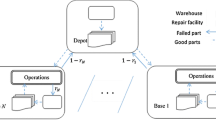
Explore related subjects
Discover the latest articles, news and stories from top researchers in related subjects.Avoid common mistakes on your manuscript.
1 Introduction
Effective management of manufacturing supply chains requires attention to system and parts reliability to ensure optimal efficiency [9, 39]. Achieving this reliability entails optimizing system and parts reliability based on operational objectives such as cost, availability, and serviceability [35]. The literature is rich in studies on reliability optimization, with two popular models standing out.
The first model is the Redundancy Allocation Problem (RAP), which considers discrete component choices along with attributes such as cost and reliability to maximize system reliability [44]. The second model is the Reliability-Redundancy Allocation Problem (RRAP), which is a non-linear mixed-integer programming problem. RRAP involves non-linear constraints that specify the number of redundant components and reliability levels of each component to achieve optimal system reliability [40]. While RRAP is a more complex model than RAP, it provides a realistic solution to the problem, especially when the specifications of the components and reliability are unknown [32]. However, classical mathematical approaches have been unable to provide optimal or near-optimal solutions [68].
In summary, the literature on reliability optimization offers useful insights into how manufacturing supply chains can achieve optimal system and parts reliability. The RAP and RRAP models are particularly relevant for this purpose. However, the complexity of the RRAP model means that classical mathematical approaches may not provide satisfactory solutions. Therefore, more research is needed to refine these models and develop alternative optimization techniques.
Redundancy strategies and outsourcing decisions are essential aspects of maintenance operations in many manufacturing supply chains. The goal of this study is to provide a framework of different redundancy strategies and outsourcing decisions to help ensure efficient and reliable system operations.
Redundancy strategies involve the deployment of redundant components in a subsystem to minimize the impact of component failures on the system's overall reliability. Two primary redundancy strategies are commonly used: active and standby. Active redundancy involves deploying all redundant components simultaneously, with only one used at a time. Standby redundancy, on the other hand, is based on the failure characteristics of a component when on standby. Standby redundancy can be further categorized as warm, cold, and hot standby, where cold and hot standby models are special cases of the warm standby model [5]. The cold-standby strategy involves protecting redundant components from stresses arising from system operations, resulting in a low probability of failure until the component stands in for a failed component [42].
Outsourcing maintenance operations is a common strategy employed by firms to improve production planning, decrease costs, and increase flexibility [4]. Outsourcing involves collaboration between firms to achieve maintenance goals [7, 36]. However, the decision to outsource involves various aspects of the maintenance, production, and logistics processes that should be carefully considered [27]. Every maintenance operation is conducted to maintain and rebuild a system to a high degree of quality. Maintenance can be either corrective or preventive, with corrective maintenance being implemented after a failure has occurred, and preventive maintenance being routinely applied to prevent failures. The goal of maintenance is to restore the system to an as good as new condition or a minimal repair to an as bad as old condition [62]. In terms of academic research, machine repair can be modeled as a renewal process, with successive times to failure that are independently and identically distributed [47]. Some studies have proposed mathematical approaches for optimizing redundancy strategies and outsourcing decisions, such as the Redundancy Allocation Problem (RAP) and the Reliability-Redundancy Allocation Problem (RRAP) [63].
In conclusion, optimizing the reliability of the system and its parts is necessary for efficient and reliable system operations. Redundancy strategies and outsourcing decisions are essential aspects of maintenance operations that should be carefully considered to ensure the highest quality of maintenance while minimizing costs and maximizing system reliability. Further research is needed to develop more effective mathematical approaches for optimizing redundancy strategies and outsourcing decisions. When considering a closed-loop green supply chain network (CLGSCN), the maintenance scheme for advanced production systems involving production centers, repairs, and spare parts centers can become complex. A critical aspect of designing such a network is ensuring that spare parts circulate within the CLGSCN for as long as possible, making access to nodes containing spare parts imperative. To address this problem, this paper presents a framework for designing a CLGSCN under a redundancy strategy (active and standby) that minimizes total cost while maximizing the reliability of parts, demand coverage for parts, and use of eco-friendly parts. Specifically, this paper addresses a multi-objective mixed-integer linear programming (MOMILP) problem with time windows for a focal firm involved in CLGSCN in Iran. The proposed hybrid algorithm, based on Heuristics and Multi-Choice Meta-Goal Programming with Utility Function (MCMGP-UF), aims to find near-optimal solutions to this complex and multi-objective problem. The contribution of this paper is presented from both theoretical and practical aspects of the following.
From a theoretical standpoint, this paper contributes to the literature on supply chain management for advanced manufacturing systems by proposing a novel design for an outsourced maintenance supply network that takes into account the unique requirements of such systems. This includes addressing the challenge of machine reliability by developing a redundancy strategy for repairs, as well as formulating a four-objective location-routing model to optimize the performance of the supply network in industrial plants. Additionally, this paper incorporates environmental considerations into the selection of spare parts, using the concept of "eco-friendly" parts to reduce the environmental impact of the supply network.
From a practical perspective, the proposed model and optimization techniques provide managers with a tool to optimize machine availability, reduce the cost of spares in the network, and ensure a stable line of spares re-supply. Furthermore, the incorporation of environmental considerations into the model allows managers to make more sustainable and socially responsible decisions. The application of the proposed model and optimization techniques to a case firm from Iran demonstrates the applicability of the model in real-world scenarios, offering valuable insights for optimized spare-part supply for maintenance and delivery.
Overall, this paper makes significant contributions to the field of supply chain management for advanced manufacturing systems both theoretically and practically. The proposed model and optimization techniques have the potential to improve the performance and sustainability of maintenance supply networks for industrial machinery, providing benefits for both businesses and society.
The paper is set as follows. Section 2 provides a comprehensive review of existing literature on CLGSCN design and redundancy strategies. The review highlights the importance of addressing the circulation of spare parts in the network and the need for access to spare part nodes. The section also discusses the types of redundancy strategies, such as active and standby, and their applications in CLGSCN maintenance schemes. Section 3 presents the methodology used to develop the MOMILP model. The objectives of the model, including minimizing total costs and maximizing reliability and demand coverage, are clearly stated. The section also provides an explanation of the time window constraints and the constraints of the eco-friendly parts used in the model. Section 4 outlines the hybrid approach used to solve the MOMILP model. The HA and MCMGP-UF algorithms are explained in detail, highlighting their strengths and limitations in solving multi-objective optimization problems. Section 5 introduces the case study firm and presents an analysis of the model and solution method. The section provides a detailed explanation of the data used in the study, including the demand, inventory, and transportation costs. The results of the study are presented and discussed, highlighting the effectiveness of the hybrid approach in solving the MOMILP model. Section 6 concludes the study with suggestions for future research. The conclusion summarizes the key findings of the study, including the importance of designing a CLGSCN with a redundancy strategy to minimize costs and maximize reliability. The limitations of the study are also acknowledged, and recommendations for further research are provided.
2 Literature review
Reliability Redundancy Allocation Problem (RRAP) has been widely studied in the literature. The problem involves finding the optimal allocation of redundancy resources to minimize the system's failure probability. Most existing studies assume an active redundancy strategy and use exact optimization methods, such as branch-and-bound and dynamic programming [23]. However, the NP-hard nature of RRAP [25, 32] makes it challenging to solve and optimize, especially for large problems. Therefore, meta-heuristic algorithms have been proposed to address this issue. These include artificial immune systems [10, 32], artificial neural networks [13], particle swarm optimization [14, 28, 29, 71, 77, 78], memetic algorithm [51], artificial bee colony algorithm [31, 76], genetic algorithm (GA) [37, 56, 79, 80], and ant colony optimization [3, 48]. The redundancy allocation problem has received recent attention from several researchers, as highlighted by Bhattacharya and Roychowdhury [6], Chambari et al. [8], Guilani et al. [22], Guo et al. [24], He et al. [28], Valaei and Behnamian [67], Hadipour et al. [26], and Hsieh [30].
Several studies have combined these algorithms to develop new optimization methods for RRAP. For example, Talafuse & Pohl [66] proposed the bat algorithm (BA), which has been found to be effective for optimal active and cold standby redundancy strategies [41]. For more information on cold-standby redundancy strategy, Abouei Ardakan & Hamadani [1], Wang et al. [69], and Feizollahi et al. [12] are recommended sources. Several studies have investigated the application of both active and cold-standby redundancy strategies to optimize system reliability. For instance, the use of warm standby strategies has been examined in power plants and wireless sensor networks, where the ability to switch to a primary component is crucial [43, 26, 59, 65]. Meanwhile, the active and cold-standby redundancy strategies have been used to improve the reliability of systems with faulty detectors and components [33, 46]. In conclusion, this review highlights the challenges associated with solving the RRAP and the various meta-heuristic algorithms proposed to overcome them. While many of these algorithms have been found to be effective, there is still a need for further research to develop more efficient and effective optimization methods for RRAP. Reliability engineering is a field that has been gaining increasing attention in recent years, particularly with the rise of complex systems and the need for high reliability in critical systems. In this regard, various studies have explored different strategies to optimize system reliability, including mixed redundancy, cold-standby, and active and cold-standby strategies. Abouei Ardakan et al. [2] investigated the effectiveness of mixed redundancy strategy on a multi-objective optimization RAP, and found that this strategy can improve system reliability without necessarily increasing costs or compromising other system features. Similarly, Wang et al. [70] introduced an RAP model for cold-standby systems with degraded components, and used GA with dual mutation to find an optimal configuration of components to increase system reliability under resource constraints. Xu & Liao [72] studied the reliability of a one-shot system with multifunctional components, and proposed an RAP to improve system reliability. They used a heuristic containing a two-stage GA and tabu search (TS) to solve the RAP. Kayedpour et al. [38] conducted an RAP over a finite time horizon, utilizing Markov processes and the NSGA-II algorithm to solve the reliability problem.
Pourkarim et al. [52] examined the RAP for a series–parallel system with component failure rates following a Weibull distribution. They utilized simulation and GA to optimize the system reliability. Finally, Sadjadi & Soltani [58] developed an RAP model for a series–parallel system using active and cold standby strategies. To formulate robust solutions, they employed the min–max regret criterion. Due to the complex constraints, Benders' decomposition method was used to solve the RAP. In conclusion, the studies mentioned in this text provide valuable insights into different strategies that can be employed to optimize system reliability. The use of various optimization techniques and algorithms, including GA, tabu search, and Markov processes, has proven effective in solving the RAP problem. Overall, these studies make significant contributions to the field of reliability engineering and demonstrate the importance of considering different strategies to achieve high system reliability.
Several researchers have recently focused on designing green and sustainable closed-loop supply chains, as highlighted by Sazvar et al. [64], Ebrahimi and Tavakkoli-Moghaddam [11], Samuel et al. [61], Ghahremani-Nahr et al. [15], Ghomi-Avili et al. [16], and Sahebjamnia et al. [60].
In the context of the COVID-19 pandemic, Raeisi and Jafarzadeh Ghoushchi [57] investigated the development of waste management models during the infection, where a multi-objective mathematical model was optimized and compared using several meta-heuristics algorithms. Additionally, the impact of restrictions on public activities, such as visiting urban parks, on the mental and physical health of individuals was explored by Geng et al. [21]. Pietrzykowski et al. [53] studied carbon emissions in both above and below-ground biomass for green plantations. In disaster relief logistics, Ghasemi et al. [20] developed a stochastic program that considers multiple objectives, including cost, demand for relief staffs, and unsuccessful evacuation routes in a humanitarian relief logistics network. This approach helps decision-makers allocate resources more efficiently and ultimately provides better support for victims.
Overall, these studies contribute to a better understanding of the application of different strategies to improve system reliability, waste management, environmental impact, and disaster relief logistics in the context of the COVID-19 pandemic.
The negative impact of the ripple effect has led to the increased use of reverse supply chains in order to promote sustainability. In recent years, researchers have developed several approaches to handle uncertainty and reliability in such systems. For example, Yilmaz et al. [75] proposed a two-stage stochastic program that can handle the ripple effect and other sources of uncertainty in a reverse supply chain. Similarly, Özçelik et al. [50] developed a robust optimization model that can effectively address the ripple effect in real-world industrial applications.
Additive manufacturing technology has emerged as a promising approach for optimizing supply chains. For instance, Yilmaz [73] proposed a vehicle routing paradigm that included additive manufacturing technology in the production process. In another study, Yilmaz and Durmusoglu [74] investigated the scheduling of a manufacturing system that combined cell and functional areas and included walking workers.
To address the risk involved in reverse supply chains, researchers have also developed various models and algorithms. For example, Ji et al. [34] proposed a risk averse model based on a consensus model and adjustment cost, which was solved using the CPLEX solver. Qu et al. [54] developed a robust optimization model that considers both individual opinions and unit adjustment cost uncertainties to control the risk of decision making.
In addition to these studies, several optimization algorithms have been proposed to solve the reverse resource allocation problem (RRAP). Kanagaraj et al. [37] conducted a cuckoo search algorithm with genetic algorithms (CS-GA) to solve the RRAP. Huang [29] applied a particle-based simplified swarm optimization (PSSO) algorithm to solve four RRAP benchmarks, highlighting the effectiveness of PSSO over other swarm optimization algorithms. He et al. [28] proposed an artificial fish swarm algorithm (NAFSA) to solve large-scale RRAP problems. Liu [45] applied a modified particle swarm optimization (MPSO) to solve the RRAP model. A multi-objective particle swarm optimization (MOPSO) algorithm was also introduced to handle such problems. The MOPSO was validated through two examples and a case study of a supervisory control and data acquisition (SCADA) system.
This paper makes several contributions to the existing literature on supply chain management for advanced manufacturing systems. Firstly, we propose a novel design for an outsourced maintenance supply network, which takes into account the unique requirements of such systems. Secondly, we incorporate environmental considerations into the selection of spare parts, using a concept we refer to as "eco-friendly" parts, to reduce the environmental impact of the supply network. Thirdly, we address the challenge of machine reliability by developing a redundancy strategy for repairs. Fourthly, we formulate a four-objective location-routing model to optimize the performance of the supply network in industrial plants. Finally, we apply two optimization techniques, heuristics and Multi-Choice Meta-Goal Programming with Utility Function, to solve the model. By addressing these issues, our paper aims to make a significant contribution to the field of supply chain management for advanced manufacturing systems.
3 Problem formulation
This study proposes an outsourced maintenance supply network for manufacturing systems that includes manufacturing factories, repair centers, and spare parts centers. The aim of the network is to repair failed machines outside the production plant, and thereby avoid the need for maintenance and repair departments in small and medium-sized production systems. The network operates as follows: when machines break down, they are sent to repair centers for inspection and repair. Simultaneously, spare parts centers are alerted to supply the required parts. After repair, the machinery is shipped back to the factories.
The key objective of this study is to determine the optimal number and location of spare parts and repair centers, as well as the optimal routes and flows of machinery and parts between these centers. Figure 1 shows the proposed network, which includes bidirectional information flow among the facilities.
The proposed approach is designed for multiple periods, and it assumes that the location and capacity of centers are already known and fixed. Vehicles start their itinerary from the repair centers and travel to the manufacturers to pick up damaged machinery and deliver repaired ones. The cost of carrying spares and machines is determined using Euclidean distance between the centers. Additionally, the same type of machinery is placed at each repair center, and two strategies (active, cold standby) are considered. The components of a subsystem can also be of different types.
To achieve these objectives, the study formulates a four-objective location-routing model and applies two methods to solve it: a heuristics method and Multi-Choice Meta-Goal Programming with Utility Function (MCMGP-UF). One of the key contributions of this study is the introduction of the concept of "eco-friendly" spare parts in both forward and backward flows in the supply network, as well as the consideration of reliability and redundancy strategies for machine repair.
In summary, this study proposes an innovative approach to designing an outsourced maintenance supply network for manufacturing systems. The proposed approach addresses several challenges and includes novel concepts and methods. By providing optimal solutions for the number and location of centers and the flow of machinery and parts, this study can help improve the efficiency and sustainability of manufacturing systems.
In advanced manufacturing systems, the need for an efficient maintenance and repair system is critical to ensure the smooth operation of machines and prevent production downtime. Given the diverse specifications and standards required for repairing different machines, a multi-echelon supply chain is designed. This involves dividing the manufacturing systems, repair centers, and spare part suppliers into different layers based on their performance criteria such as repair capability, proficiency of the repair system, distance to the manufacturing plant, and reliability of the machine after repair. The proposed model then decides on the assignment policy that optimizes these performance criteria.
One unique aspect of the proposed model is the consideration of environmental factors in the selection of spare parts. The model aims to be eco-friendly by choosing spare parts that are most recyclable and environmentally compliant, based on a green supply chain policy. This ensures that the environmental impact of the maintenance and repair system is reduced, making it more sustainable in the long run. It is important to note that this eco-friendly policy focuses on spare parts and not on carbon emissions during transit.
To calculate the environmental compliance of spare part suppliers, various environmental indicators can be considered, such as greenhouse gas emissions, energy consumption, waste generation, water usage, and materials used. The specific indicators and their weights can be determined based on the environmental priorities of the organization and the environmental regulations in the region.
Once the environmental compliance of the spare part suppliers is calculated, it can be integrated into the decision-making process by adding it as an objective or constraint in the optimization model. For example, the model can aim to minimize the total cost while also ensuring that a certain percentage of the spare parts are sourced from environmentally compliant suppliers. Alternatively, the model can aim to maximize the environmental compliance while ensuring that the total cost does not exceed a certain budget. The specific approach will depend on the priorities and goals of the organization.
Overall, the proposed model offers a comprehensive approach to designing an efficient maintenance and repair system for advanced manufacturing systems. By considering multiple performance criteria, including environmental compliance, the model provides a more holistic solution to the problem.
3.1 Model development
3.1.1 Notation
- M :
-
Set of manufacturing centers \(m=1, \dots , M\)
- K :
-
Set of repair centers \(k=1,\dots ,kK\)
- T :
-
Set of time periods \(t= 1, \dots ,\) T
- L :
-
Set of spare part centers \(l=1,\dots ,\) L
- J :
-
Set of spare parts \(j=1,\dots ,\) J
- I :
-
Set of machinery \(i=1,\dots ,\) I
- V :
-
Set of vehicles \(v=1,\dots ,\) V
- F :
-
Set of failure modes \(f=1,\dots ,\) F
- G :
-
Set of centers where the transporting vehicles are stationed \(G\in \{K,L\}\)
- H :
-
Set of items that are transported by vehicles \(H\in \{I,J\}\)
- N :
-
Set of centers that vehicles should visit \(N\in \{M,K\}\)
- Q :
-
Number of failures of the standby components of type \(j\) in subsystem \(i\) \(q=1,\dots ,Q\)
- P :
-
Allocated component types that are on standby \(p=1,\dots ,\) P
- W :
-
Standby component choices used for subsystem \(i w=1,\dots ,\) W
3.1.2 Parameter
- Cx jlt :
-
Cost of purchasing spare part j from place l in period t
- Cr ikt :
-
Cost of repairing machinery i in place l in period t
- \(Cy_{imk}^{vt}\) :
-
Cost of transporting machinery i from manufacturing center m and repairing k with vehicle v in period t
- \(Cb_{jlk}^{vt}\) :
-
Cost of transporting spare part j from spare part center l and repairing k with vehicle v in period t
- \(Ck_{ikm}^{vt}\) :
-
Cost of transporting machinery i from repair center k and manufacturing center m with vehicle v in period t
- E l :
-
Cost of establishing spare part center l
- F k :
-
Cost of establishing repairing center k
- Cap ljt :
-
Capacity of spare parts center l for spare parts j in period t
- Cap kit :
-
Capacity of repairing centers k for machinery i in period t
- \(d_{mk}^\alpha\) :
-
Euclidean distance between manufacturing center m and repair center k
- \(d_{kl}^\beta\) :
-
Euclidean distance between repair center k and spare part center l
- Ed kl :
-
Maximum expected distance between spare part center l and repair center k
- dem imft :
-
Demand level by production center m for repairing machinery i with failure mode f in period t
- dem jfi :
-
Demand level for spare part j for repairing machinery i with failure mode f
- Ql jikt :
-
Spare part j that does not damage environment by repair center k for machinery i in period t
- a kl :
-
Distance control parameter \({a}_{kl}=\left\{\begin{array}{c}1\; if \;{d}_{kl}^{\beta }\le {Ed}_{kl} \\ 0\; otherwise \end{array}\right.\)
- Cavm vi :
-
Capacity of vehicle type v for machinery i
- Cavs vj :
-
Capacity of vehicle type v for spare part j.
- Cp ikt :
-
\({Cp}_{ikt}=\left\{\begin{array}{c}1\; if\; repair\; center\; k\; can\; repair\; machine\; i\; in\; period\; t\\ 0\; otherwise \end{array}\right.\)
- TTnn ’ :
-
Travel time from node n to \({n}^{^{\prime}}\)
- RT ifkt :
-
Repair time of machinery i with failure mode f at repair center k in period t
- BigM :
-
A large number
- UW n :
-
Upper bound of time-window for each node n
- T :
-
Total time
- \({n_{max}}_{ijt}\) :
-
Upper bound for \({n}_{ijt}\)
- \({n_{max}}_{it}\) :
-
Upper bound for \({n}_{it}\)
- CC :
-
Total budget
- WW :
-
Weight capacity
- VV :
-
Volume capacity
- C ijt , W ijt , V ijt :
-
Cost, weight and volume for component j for subsystem \(i\) in period t
- rij (t):
-
Reliability of component j for subsystem \(i\) at time t
- ρi (t):
-
Failure-detection/ switching reliability at time t
- \(f_{ijt}^q\) :
-
pdf for \({q}^{th}\) failure of type \(j\) component for subsystem \(i\) at time t
- S n :
-
Random nonnegative numbers, individual terms of this sequence are called renewals
- τ(t):
-
Potential failure rate
- λ ij , k ij :
-
Scale and shape parameters of Erlang distribution
3.1.3 Decision variable
- \(P_{jlk}^{vt}\) :
-
Amount of spare part j moved from spare part center l to repair center k in period t by vehicle v.
- \(H_{ifmk}^{vt}\) :
-
Amount of machinery i with failure mode f transferred from manufacturing center m to repair center k in period t by vehicle v.
- \(Q_{ifkm}^{vt}\) :
-
Amount of machinery i with failure mode f transferred from repair center k to manufacturing center m in period t by vehicle v.
- Nm vikt :
-
Number of vehicles v transferring machinery i from repair center k in period t.
- TL vknit :
-
Total load of vehicles v assigned to repair center k at node n for machinery i in period t.
- Ns vjt :
-
Number of vehicles v transferring spare part j in period t.
- X ijt :
-
Number of active components of type j used in subsystem i in period t.
- Y ijt :
-
Number of standby components of type j used in subsystem i in period t.
- n ijt :
-
Number of type j components used in subsystem i in period t
- n it :
-
Number of components used in subsystem i in period t
- Z k :
-
1, if repair center k is established; \(otherwise\) 0
- W l :
-
1, if spare part center l is established; \(otherwise\) 0
- U jlkt :
-
1, if spare part j of spare part center l is assigned to repair center k in period t; \(otherwise\) 0
- O imkt :
-
1, if machinery i of manufacturing center m is assigned to repair center k in period t;\(otherwise\) 0
- E lnn'vt :
-
1, if in the path of vehicle v assigned to spare parts center l, node \({n}^{^{\prime}}\) is met after node n in period t;\(otherwise\) 0
- E knn'vt :
-
1, if in the path of vehicle v assigned to repair center k, node \({n}^{^{\prime}}\) is met after node n in period t;\(otherwise\) 0
- DT jlkt :
-
Delivery time of spare part j from spare part center l to repair center k in period t.
- DT ikmt :
-
Delivery time of machinery i from repair center k to manufacturing center m in period t.
- LTW nt :
-
Tardiness in node n in period t.
- δ kl :
-
Binary linear variable \({\delta }_{kl}={Z}_{k}*{w}_{l}\)
- N (t):
-
Renewal counting process that tracks the total number of renewals (excluding initial occurrence) to date
3.1.4 Objective function
3.1.5 Constraint
The objective of this optimization model is to manage the flow of spare parts and machines in a repair system. The model has four main objectives: minimize costs, account for environmental concerns, set covering demand, and maximize machine reliability. The constraints of the model ensure that demand, component reliability, and spare part and machine flows are balanced, while also accounting for capacity and time-window limitations.
The first objective function minimizes the total cost; the first and second terms include the cost of establishing repair centers and spare parts, respectively. The third term relates to the cost of purchasing spare parts and the cost of transferring them. Clearly, the transportation costs will depend on the centers, as this allows the decision makers to use vehicles most economical for moving parts and machines. The fourth term presents the transport between the manufacturing and repair centers. The last term is the cost of transferring the machinery for repair from the manufacturing center to repair center. The sixth term covers the cost of transportation between the repair centers. Since environmental issues are a concern, the second objective function is set as such. The third objective function is provided to cover the repair centers by the spare parts and vice versa. The fourth objective is to maximize the reliability of the machines that is based on in active and standby strategies.
Constraints (5) and (6) ensure that spare parts and machines flow according to demand and component reliability. Constraint (7) balances the flow between repair centers and manufacturing centers. Manufacturing centers can only be assigned to repair centers that are open (Constraint 8). Constraints (9) and (10) relate to the flow and allocation variables. Constraints (11) and (12) address the capacity of each center. Constraint (13) requires that each repair center repairs a batch of similar machines. Routing starts from the spare part center to the repair center allocated to it (Constraint 14). The spare part center must be visited if a repair center is dedicated to it in a given period (Constraint 15). Constraints (16) and (17) are similar to Constraints (14) and (15) for the repair centers. Constraint (18) ensures that a route starting from a center returns to it. Constraints (19) and (20) confirm a tour construction. Constraints (21) and (22) represent the overall vehicle load after visiting a node. Constraints (23) and (24) guarantee that the entire load does not exceed the vehicle capacity. Constraints (25) and (26) address the delivery time to each node. Constraint (27) demonstrates the time-window violation. Constraint (28) is the inventory balance equation in the repair centers. Constraints (29) – (31) represent the cost, weight, and volume constraints. Constraints (32) and (33) limit the maximum number of components for a subsystem. Constraints (34) and (35) are the linearization constraints for the third objective function. Constraints (36) – (39) relate to the determination of the renewal process. Finally, Relation (40) displays the type and sign of decision variables.
4 Solution approach
The proposed model is a complex multi-objective optimization model that aims to optimize the reliability, cost, and environmental impact of a supply network for outsourced maintenance. The model includes several constraints related to redundancy, location, and routing, which are important factors for ensuring a robust and efficient network.
To address the complexity of the problem, this study proposes a heuristic solution approach based on an advanced version of the multi-choice goal programming model, as described by Razavi et al. [55] and Nayeri et al. [49]. This approach, called HA-MCMGP-UF, is designed to generate high-quality solutions quickly by iteratively optimizing the conflicting objective functions..
4.1 MCMGP-UF
Goal programming (GP) is a widely used method for solving multi-objective programming models. Variants of GP, such as weighted goal programming and multi-choice goal programming, have been developed to address specific challenges and preferences in decision-making.
Multi-Choice Meta-Goal Programming with Utility Function (MCMGP-UF) is an improved version of goal programming methods that allows for more balanced solutions. The MCMGP-UF approach is designed to help decision-makers achieve a balance between competing objectives in a multi-objective programming model. The MCMGP-UF achieves more balanced solutions by allowing decision-makers to specify their preferences and priorities for each objective. By doing so, the model can find solutions that meet the preferences and priorities of the decision-makers as closely as possible, resulting in a more balanced outcome. In practical terms, this means that decision-makers can use MCMGP-UF to find solutions that achieve a balance between multiple objectives, such as minimizing costs while maximizing customer satisfaction. This can help decision-makers make more informed and effective decisions by taking into account multiple factors and balancing competing objectives. Additionally, the use of a utility function in MCMGP-UF allows decision-makers to assign weights to the various objectives, reflecting their relative importance, further enhancing the ability to achieve a more balanced solution.
Recently, Nayeri et al. [49] used an improved form of GP, called the multi-choice meta-goal programming with utility function (MCMGP-UF) method, that offers several advantages over other versions of GP. Firstly, the method yields more balanced solutions by incorporating the preferences of decision-makers. Secondly, the method is flexible and can model the preferences of decision-makers by defining multiple goal levels for each objective function. Thirdly, the method can use a utility function to incorporate the preference values of the decision-makers. To illustrate, the method can be used to solve supply chain optimization problems by considering multiple objectives such as minimizing cost, maximizing reliability, etc. By using the MCMGP-UF method, decision-makers can define different levels of importance for each objective function and generate solutions that satisfy their preferences.
The formulation of the MCMGP-UF method is presented below [49]:
where \({t}_{i}\) denotes the target value for the ith objective function as determined by the DM, \({n}_{i}\) is a negative deviation and \({p}_{i}\) is a positive deviation. \({\alpha }_{j}\mathrm{and}{ \beta }_{j}\) are meta-deviations.\({Q}_{j}\) is the limit for deviation type j, \(Big{M}_{i}\) is a large number, \(Gi\) is a binary variable, and \({\delta }_{i}\) is the importance weight of the ith objective function. \(D\) is also the maximum unwanted deviation. \({F}_{i}^{min}\) is the lower bound of the target range and \({F}_{i}^{max}\) defines the upper bound of the target range. \({U}_{i}\) represents the utility value. \({T}_{i}\) is a continuous variable, and \({\xi }_{i}\) denotes the normalized deviation of \({T}_{i}\) from \({F}_{i}^{min}\). \({f}_{i}\left(x\right)\) is the function of the ith objective and \({b}_{j}\) is the scalar aspiration level of the jth right hand vector of model constraints and \({g}_{j}(x)\) is model constraints. Objective function (1) can be written in the min–max or weighted form. This paper considers the weighted form.
4.2 Heuristic approach
The proposed paper presents a heuristic solution for a multi-objective optimization of redundancy reliability for eco-friendly outsourced maintenance supply networks. The heuristic method is developed by Gholizadeh et al. [18] and Gholizadeh et al. [17] and is combined with LP relaxed to solve the model. The proposed method involves the following steps:
-
Relaxation of binary constraints: The binary constraints related to an open facility (e.g., \({E}_{ln{n}^{^{\prime}}vt},{E}_{kn{n}^{^{\prime}}vt},{O}_{imkt},{U}_{jlkt},{W}_{l},{Z}_{k}, {\delta }_{kl}\)) are relaxed by converting them into positive variables to relax the model.
-
Optimal solution: The relaxed model is solved to obtain the optimal solution.
-
Record non-zero quantities: All non-zero quantities of the relaxed variables obtained from the relaxed model results are recorded.
-
Generate constraints: For each non-zero value of the relaxed variables, it is set to 1 and added as constraints to the main MILP model.
-
Optimal solution: The main MILP model is solved again to obtain the optimal solution.
4.3 Hybrid method
The present study aims to develop a novel hybrid algorithm by integrating the MCMGP-UF method and HA to address the problem of multi-objective optimization of redundancy reliability for eco-friendly outsourced maintenance supply networks. The proposed algorithm builds upon previous work by Gholizadeh et al. [17, 19] and employs a heuristic to relax the binary variable. To handle multi-objectives, we utilize the MOMILP approach in the proposed model. Specifically, we first check that all binary variables have values of either zero or one. We then obtain the values of \({n}_{i},{p}_{i},{\alpha }_{j},{\beta }_{j}\) for each objective by relaxing the binary constraints. Subsequently, we treat the binary variable as a continuous variable and incorporate it into the new model to optimize the solution. Finally, report \({n}_{i},{p}_{i},{\alpha }_{j},{\beta }_{j}\) and the decision variables of the proposed model. The pseudocode for the proposed approach is as follows:

In this code, parameters represent the model parameters including objective functions, decision variables, and binary variables. binary_variables represent the binary variables that need to be relaxed. The relax_binary_constraints function is used to relax binary constraints by converting them into positive variables. The solve_relaxed_problem function is used to solve the relaxed problem. The generate_constraints function is used to generate constraints for each non-zero value of the relaxed variables. The report_variables and report_solution functions are used to report the variables and the solution of objective functions and decision variables, respectively.
Here is an example of the hybrid method to solve a multi-objective problem using the MCMGP-UF and a heuristic to relax binary variables:
Consider a manufacturing company that produces three types of products: A, B, and C. The company has four production lines, each capable of producing one type of product. The objective is to maximize profit and minimize the total number of production lines used. The company also has a constraint on the total production volume, which must be greater than or equal to 100 units.
The decision variables are the number of production lines used for each product type, denoted by Xa, Xb, and Xc. The constraints are:
The profit function for each product type is:
To solve this problem using the MCMGP-UF and a heuristic to relax binary variables, we first define the utility function as:
where λ is a weighting parameter that represents the relative importance of minimizing the number of production lines used.
Next, we define the multi-choice meta-goals as:
We then solve the problem using the following steps:
-
Initialize λ = 0 and solve the problem using a heuristic to relax the binary variables, such as the linear relaxation method. This gives us a non-dominated set of solutions.
-
For each solution in the non-dominated set, compute the values of G1 and G2.
-
Solve the MCMGP-UF problem using the values of G1 and G2 as the meta-objectives, and Xa, Xb, and Xc as the decision variables. This gives us the optimal solution that balances the two meta-objectives.
-
If the optimal solution is not feasible, increase λ and repeat steps 2–3 until a feasible solution is found.
For example, let's say we use the linear relaxation method to obtain the following non-dominated set of solutions:
-
Solution 1: Xa = 2, Xb = 1, Xc = 1, Profit = 32.5, Lines used = 4
-
Solution 2: Xa = 1.5, Xb = 1.5, Xc = 1, Profit = 34.25, Lines used = 4
-
Solution 3: Xa = 1, Xb = 2, Xc = 1, Profit = 33, Lines used = 4
-
Solution 4: Xa = 1, Xb = 1, Xc = 2, Profit = 32, Lines used = 4
Next, we compute the values of G1 and G2 for each solution:
-
Solution 1: G1 = -10.75, G2 = 3.25
-
Solution 2: G1 = -8.5, G2 = 4.75
-
Solution 3: G1 = -9.25, G2 = 4
-
Solution 4: G1 = -9, G2 = 3.75
5 Numerical study
The objective of this research is to evaluate the behavior and solution of a maintenance supply chain network using a multi-objective mixed integer programming (MOMIP) model. The case study involves an automobile parts manufacturer located in Amol, Iran, which produces a variety of steel and cast iron products. The maintenance of machinery is critical for the firm, and timely delivery of spare parts for machine repairs is crucial for assessing the reliability of the firm. Furthermore, the government regulations and economic benefits necessitate the use of environmentally friendly spare parts.
The MOMIP model is implemented using GUROBI and executed within the GAMS environment on a computer system with a dual-core Pentium processor 1.40 GHz and 3 GB of RAM. The machine under study is the multi-axis and multifunction CNC: GS-200/L CNC turning machine, as shown in Fig. 2. The spare parts for the machine are listed in Table 1.
The results of the analysis are obtained using GAMS and Matlab, and the model's performance is evaluated and analyzed. The numerical experimentation is conducted to evaluate the model's behavior and solution. The results of this analysis could provide insights into the benefits of using environmentally friendly spare parts, and the importance of timely delivery in enhancing the reliability of the firm's machinery. The study's methodology and results could have significant implications for the maintenance supply chain network of similar manufacturing firms.
To evaluate the effectiveness of our proposed approach, we designed and implemented ten test problems that cover a range of indices, as shown in Table 2. These problems were carefully selected to represent a variety of scenarios that are commonly encountered in the field. By testing our approach on these problems, we can assess its ability to handle a diverse range of optimization challenges.
The values of the parameters used in the model are randomly generated using the uniform probability distribution as shown in Table 3.
5.1 Validation
Next, we validate the model according to Table 2 for various model sizes. The optimal results are shown in Table 4. Note that the objective function values are given separately for each test problem.
The results on the fourth objective function, which is maximizing reliability, are shown in Table 5 with respect to the redundancy allocation and the various strategies.
From Table 5, for 10 problems of various specifications, the optimal reliability value is obtained based on the stated criteria. For example, in Problem 8, the maximum system reliability is 0.99940314. It is related to a system with a weight of 220, cost of 120, and a volume of 300. The criteria used are the scale and shape parameters for the Erlang distribution. The number of components used in subsystem i and the reliability of each subsystem and its component are given. It is expected that there is no limitation in the number of active and standby components in the selection of the component in each subsystem (as in an active strategy, no component can be in standby mode or only an active component in the standalone strategy). There is also no limitation in choosing the type of components in each subsystem (i.e., in each subsystem, any number of a component can be selected). A higher level of system reliability is achieved using a stand-by strategy, which can significantly improve the reliability levels of the subsystems based the criteria compared to an active standby strategy.
5.2 Case study results
Figure 3 presents the results of the hybrid method used in the case example, with the weight of each objective set at 0.3, 0.2, 0.2, and 0.3, respectively.
5.3 Sensitivity analysis
Next, the sensitivity analysis of the objective function is compared based on some of the model parameters to determine the effect of a change in the value of the objective function. The sensitivity of the objective function is checked against the demand, failure rate, and reliability of the components.
5.3.1 Demand
In this study, we conducted a sensitivity analysis to investigate the effect of demand on the objective function of a selected test problem. All parameters, except demand, were kept constant to isolate the effect of demand on the system's performance. The experiment was conducted using a well-defined problem and model, which are described in detail in the previous sections.
The results of the sensitivity analysis are presented in Fig. 4. As shown in the figure, an increase in demand leads to a linear increase in the value of objective function #1. This suggests that marketing and advertisement efforts that lead to increased demand can result in higher gains for the system. However, it is important to note that the analysis was conducted under specific assumptions and conditions, and the results may not generalize to other situations or models.
Figure 5 shows the sensitivity analysis of objective function #2 with respect to demand. As the demand increases, the value of objective function #2 decreases linearly. This indicates that an increase in demand leads to more transportation and higher environmental hazards associated with finding the most appropriate spare part supplier. Therefore, managers should develop a strategy to balance the demand in the planning horizon to address environmental concerns. On the other hand, demand changes do not have any effect on the values of objective functions #3 and #4.
5.3.2 Component reliability
The effect of component reliability on the objective functions is investigated next. We conduct sensitivity analysis to determine how the objective functions change with respect to the reliability values of the components. To this end, we fix all parameters except the component reliability and solve the problem for different reliability values. The results are shown in Figs. 6, 7, and 8.
Figure 6 illustrates that increasing the reliability value leads to an increase in objective functions #1 and #4, while objective function #2 decreases and objective function #3 remains unchanged. Specifically, increasing the reliability of the components can lead to a higher system availability, which in turn leads to higher profit and lower failure-related costs.
Furthermore, Fig. 7 shows that improving component reliability increases the value of objective function #4, indicating that better reliability can reduce the environmental impact of the system. This is because more reliable components require less maintenance, resulting in less waste and pollution.
On the other hand, Fig. 8 demonstrates that increasing the reliability of the components reduces the value of objective function #2. This is due to the fact that more reliable components can be more expensive and may require more complex supply chains, resulting in higher procurement and transportation costs.
It is important to note that increasing component reliability can result in higher maintenance costs, as more resources and tasks are needed to maintain the level of reliability. Therefore, managers should carefully balance the costs and benefits of improving component reliability to maximize the overall performance of the system.
5.3.3 Failure rate
The reliability of a system is influenced by its failure rate, which in turn impacts the cost of purchase and repair. While the failure rate does not have a direct effect on objective functions #1 and #2, increasing it leads to higher costs. Therefore, we focus only on objective function #4 to investigate the effect of failure rate on the system. From Fig. 9, it is evident that increasing the failure rate results in lower system reliability. A higher failure rate also increases the risk of machine breakdown, resulting in reduced machine availability. One possible way to address this issue is to store critical spare parts, which assures system performance continuity. However, this approach incurs high operating costs. Therefore, it is crucial to strike a balance between cost and reliability to optimize system performance.
5.4 Sensitivity analysis of MCMGP-UF and normalized objective function gap
The Multi-Criteria Maintenance and Replacement Model with MCMGP-UF is analyzed for sensitivity. First, we investigate the effect of parameter changes on the model. Then, we compare the deviation of each objective function from its lower limit.
5.4.1 Demand
Regarding the effect of demand changes on the objective function, Fig. 10 shows that an increase in demand results in a higher objective function.
5.4.2 Component reliability
Figure 11 demonstrates the sensitivity of the ideal objective function to changes in component reliability. The figure shows that increasing the reliability of components has a positive effect on the ideal objective function.
5.4.3 Sensitivity analysis normalized distance of objective functions
We now review the impact of changes in the parameters on the normalized distances of the objective functions. The normalized gaps of the objective functions for each parameter at various levels are shown in Table 6. The results indicate that an increase in demand and component reliability leads to a decrease in βi and an increase in αi, which is consistent with the objectives of the optimization model.
5.5 Managerial implications
We offer some managerial insights. The moving parts of a machine usually need repairs or be replaced. Implementing the proposed objectives and constraints can help managers to reduce the cost of maintenance while maintaining or improving the reliability of the maintenance supply network. By optimizing for both redundancy and reliability, managers can ensure that maintenance activities are performed efficiently and effectively, which can lead to cost savings in the long run. The focus on eco-friendliness in the maintenance supply chain is becoming increasingly important for companies. Implementing multi-objective optimization techniques can help managers to identify ways to reduce the environmental impact of maintenance activities, such as by optimizing the routing of maintenance vehicles or reducing energy consumption during maintenance activities.
Reliability and redundancy are critical factors for customer satisfaction in the maintenance supply chain. By optimizing for both factors, managers can ensure that maintenance activities are performed in a timely and effective manner, which can lead to improved customer satisfaction and loyalty. Outsourced maintenance supply networks often rely on the performance of third-party suppliers. By implementing the proposed approach, managers can identify the most reliable and cost-effective suppliers, which can lead to improved supplier performance and reduced downtime. Maintenance activities can be subject to various risks, such as equipment failure or workforce shortages. Multi-objective optimization techniques can help managers to identify and mitigate these risks, such as by increasing redundancy in critical areas or developing contingency plans for unexpected events. Overall, multi-objective optimization of redundancy reliability for eco-friendly outsourced maintenance supply networks can help managers to balance competing objectives and achieve better performance, cost-effectiveness, sustainability, customer satisfaction, supplier performance, and risk management.
Firstly, managers should prioritize maintenance on parts with higher failure rates or face more demand. Specifically, the chuck cylinder, spindle motor, chuck, coolant pump, conveyor chip, and hydraulic unit have higher failure rates than other parts, so investing in better maintenance for these parts can reduce downtime and improve overall system reliability. Secondly, managers should invest more in certain categories of spare parts, beyond their mean time between failures (MTBFs). By taking into account the sensitivity of the objective functions to changes in component reliability and demand, managers can optimize their inventory and ensure that they have the right spare parts available when needed. Thirdly, some spare parts tend to last longer than others, such as tailstock or sub-spindle, spindle head stock, and saddle. These parts should be inventoried accordingly, with a focus on ensuring that they are available when needed for repairs.
Finally, by using the MCMGP-UF model, managers can plan for quicker scheduling of spare parts needed for repair, which can help to minimize downtime and ensure timely delivery. Overall, the insights offered by the model can help managers to optimize their maintenance and spare parts inventory, reduce costs, and improve system reliability. Overall, the findings suggest that managers can achieve higher levels of system reliability by prioritizing the selection of components and subsystems with higher reliability values and implementing a standby strategy where appropriate. The results of Table 5 can provide guidance for managers in making decisions related to the design and maintenance of complex systems.
6 Concluding remarks
This paper proposes a novel environmentally friendly maintenance supply network for industrial machinery that integrates multi-objective mixed integer programming to minimize total costs while addressing environmental concerns and maximizing network coverage and reliability. The proposed network incorporates production centers, repairs, and spare parts, with an active and cold standby strategy to ensure the reliability of the repaired parts. The testing of a multi-choice goal programming using a case firm from Iran demonstrates the applicability of the model and offers insights for optimized spare-part supply for maintenance and delivery. The proposed model has the potential to optimize machine availability, reduce the cost of spares in the network, and ensure a stable line of spares re-supply. Future work can explore the issue of uncertainty in the parameters and develop an integrated policy for managing returns and repairs. This model presents a promising approach towards building sustainable and reliable maintenance supply networks for industrial machinery.
The design of environmentally friendly supply chain networks for advanced manufacturing systems is of critical importance for society and policymakers. The implementation of sustainable and socially responsible supply chains can help reduce the environmental impact of industrial machinery and promote more sustainable practices. The proposed framework for designing a closed-loop green supply chain network (CLGSCN) under a redundancy strategy provides a valuable tool for managers to optimize machine availability, reduce costs, and ensure a stable line of spare parts re-supply while taking into account environmental considerations.
The findings of this study have practical implications for policymakers, as they can help promote the development of sustainable and socially responsible manufacturing practices. Policymakers can use the proposed model and optimization techniques to encourage businesses to adopt more sustainable practices by providing incentives for the implementation of closed-loop green supply chain networks.
Furthermore, this study contributes to the literature on supply chain management for advanced manufacturing systems, providing new insights into the challenges of maintaining such systems and proposing a novel design for an outsourced maintenance supply network. The results of this study can be used to inform future research and guide the development of more advanced and sustainable supply chain management practices.
In conclusion, the proposed framework for designing a closed-loop green supply chain network has the potential to make a significant impact on society by promoting more sustainable manufacturing practices, reducing the environmental impact of industrial machinery, and providing valuable insights for policymakers and managers seeking to optimize supply chain networks for advanced manufacturing systems.
Some future research is proposed in the following.
-
Investigating the impact of uncertainty on the closed-loop green outsourced maintenance supply chain network design, particularly in terms of demand and lead time variability. This research could explore the use of stochastic programming techniques, such as robust optimization, to design a network that is robust to uncertainty.
-
Evaluating the effectiveness of column generation and Benders decomposition techniques for solving large-scale closed-loop green outsourced maintenance supply chain network design problems. This research could compare the performance of these two methods and identify which method is more suitable for different types of problem instances.
-
Incorporating the concept of circular economy into the closed-loop green outsourced maintenance supply chain network design. This research could explore the benefits of adopting circular economy principles, such as reducing waste and improving resource efficiency, and how they can be integrated into the network design.
-
Exploring the impact of government policies and regulations on the closed-loop green outsourced maintenance supply chain network design. This research could investigate the effect of policies such as carbon taxes, subsidies, and emissions regulations on the design of the network, and how companies can adapt to these policies to improve their environmental performance.
-
Investigating the role of information technology in the closed-loop green outsourced maintenance supply chain network design. This research could explore how technologies such as the Internet of Things, blockchain, and artificial intelligence can be used to improve the efficiency, sustainability, and resilience of the network.
Data availability
The related data have been presented in the manuscript.
References
AboueiArdakan M, Hamadani AZ (2014) Reliability–redundancy allocation problem with cold-standby redundancy strategy. Simul Model Pract Theory 42:107–118
AboueiArdakan M, Sima M, ZeinalHamadani A, Coit DW (2016) A novel strategy for redundant components in reliability-redundancy allocation problems. IIE Trans 48(11):1043–1057
Ahmadizar F, Soltanpanah H (2011) Reliability optimization of a series system with multiple-choice and budget constraints using an efficient ant colony approach. Expert Syst Appl 38(4):3640–3646
Ahmed MN (2019) The use of performance-based contracting in managing the outsourcing of a reliability-centered maintenance program: A case study. J Qual Maint Eng 26(4):526–554
Amari SV, Dill G (2009) A new method for reliability analysis of standby systems. In Reliability and Maintainability Symposium, 2009. RAMS 2009. Annual (pp. 417–422). IEEE
Bhattacharya D, Roychowdhury S (2014) A constrained cost minimizing redundancy allocation problem in coherent systems with non-overlapping subsystems. Adv Ind Eng Manag 3(3):1–6
Cai W, Liu C, Jia S, Chan FT, Ma M, Ma X (2020) An energy-based sustainability evaluation method for outsourcing machining resources. J Clean Prod 245:118849
Chambari A, Najafi AA, Rahmati SHA, Karimi A (2013) An efficient simulated annealing algorithm for the redundancy allocation problem with a choice of redundancy strategies. Reliab Eng Syst Saf 119:158–164
Chaleshigar Kordasiabi M, Gholizadeh H, Khakifirooz M, Fathi M (2023) Robust-heuristic-based optimisation for an engine oil sustainable supply chain network under uncertainty. Int J Prod Res 61(4):1313–1340
Chen TC (2006) IAs based approach for reliability redundancy allocation problems. Appl Math Comput 182(2):1556–1567
Ebrahimi M, Tavakkoli-Moghaddam R (2020) Benders decomposition algorithm for a green closed-loop supply chain under a build-to-order environment. J Ind Syst Eng 13:102–111
Feizollahi MJ, Soltani R, Feyzollahi H (2015) The robust cold standby redundancy allocation in series-parallel systems with budgeted uncertainty. IEEE Trans Reliab 64(2):799–806
Garg HARISH, Sharma SP (2013) Reliability-redundancy allocation problem of pharmaceutical plant. J Eng Sci Technol 8(2):190–198
Garg H, Rani M, Sharma SP, Vishwakarma Y (2014) Bi-objective optimization of the reliability-redundancy allocation problem for series-parallel system. J Manuf Syst 33(3):335–347
Ghahremani-Nahr J, Kian R, Sabet E (2019) A robust fuzzy mathematical programming model for the closed-loop supply chain network design and a whale optimization solution algorithm. Expert Syst Appl 116:454–471
Ghomi-Avili M, Naeini SGJ, Tavakkoli-Moghaddam R, Jabbarzadeh A (2018) A fuzzy pricing model for a green competitive closed-loop supply chain network design in the presence of disruptions. J Clean Prod 188:425–442
Gholizadeh H, Jahani H, Abareshi A, Goh M (2021) Sustainable closed-loop supply chain for dairy industry with robust and heuristic optimization. Comput Ind Eng 157:107324
Gholizadeh H, Fazlollahtabar H (2020) Robust optimization and modified genetic algorithm for a closed loop green supply chain under uncertainty: Case study in melting industry. Comput Ind Eng 147:106653
Gholizadeh H, Goh M, Fazlollahtabar H, Mamashli Z (2022) Modelling uncertainty in sustainable-green integrated reverse logistics network using metaheuristics optimization. Comput Ind Eng 163:107828
Ghasemi P, Goodarzian F, Abraham A (2022) A new humanitarian relief logistic network for multi-objective optimization under stochastic programming. Appl Intell 52(12):13729–13762
Geng D, Innes J, Wu W, Wang G (2021) Impacts of COVID-19 pandemic on urban park visitation: a global analysis. J For Res 32:553–567
Guilani PP, Azimi P, Niaki STA, Niaki SAA (2016) Redundancy allocation problem of a system with increasing failure rates of components based on Weibull distribution: A simulation-based optimization approach. Reliab Eng Syst Saf 152:187–196
Guo B, Gunn SR, Damper RI, Nelson JD (2006) Band selection for hyperspectral image classification using mutual information. IEEE Geoscience and Remote Sensing Letters 3(4):522–526
Guo J, Wang Z, Zheng M, Wang Y (2014) Uncertain multiobjective redundancy allocation problem of repairable systems based on artificial bee colony algorithm. Chin J Aeronaut 27(6):1477–1487
Ha C, Kuo W (2006) Reliability redundancy allocation: An improved realization for nonconvex nonlinear programming problems. Eur J Oper Res 171(1):24–38
Hadipour H, Amiri M, Sharifi M (2019) Redundancy allocation in series-parallel systems under warm standby and active components in repairable subsystems. Reliab Eng Syst Saf 192:106048
Haoues M, Dahane M, Mouss KN (2021) Capacity planning with outsourcing opportunities under reliability and maintenance constraints. Int J Ind Syst Eng 37(3):382–409
He Q, Hu X, Ren H, Zhang H (2015) A novel artificial fish swarm algorithm for solving large-scale reliability–redundancy application problem. ISA Trans 59:105–113
Huang CL (2015) A particle-based simplified swarm optimization algorithm for reliability redundancy allocation problems. Reliab Eng Syst Saf 142:221–230
Hsieh TJ (2022) A simple hybrid redundancy strategy accompanied by simplified swarm optimization for the reliability–redundancy allocation problem. Eng Optim 54(3):369–386
Hsieh TJ, Yeh WC (2012) Penalty guided bees search for redundancy allocation problems with a mix of components in series–parallel systems. Comput Oper Res 39(11):2688–2704
Hsieh YC, You PS (2011) An effective immune based two-phase approach for the optimal reliability–redundancy allocation problem. Appl Math Comput 218(4):1297–1307
Juybari MN, AboueiArdakan M, Davari-Ardakani H (2019) A penalty-guided fractal search algorithm for reliability–redundancy allocation problems with cold-standby strategy. Proc Inst Mech Eng, Part O: J Risk Reliab 233(5):775–790
Ji Y, Li H, Zhang H (2022) Risk-averse two-stage stochastic minimum cost consensus models with asymmetric adjustment cost. Group Decis Negot 31:261–291
Jahani H, Gholizadeh H (2022) A flexible closed loop supply chain design considering multi-stage manufacturing and queuing based inventory optimization. IFAC-PapersOnLine 55(10):1325–1330
Kafiabad ST, Zanjani MK, Nourelfath M (2020) Integrated planning of operations and on-job training in maintenance logistics networks. Reliab Eng Syst Saf 199:106922
Kanagaraj G, Ponnambalam SG, Jawahar N (2013) A hybrid cuckoo search and genetic algorithm for reliability–redundancy allocation problems. Comput Ind Eng 66(4):1115–1124
Kayedpour F, Amiri M, Rafizadeh M, Nia AS (2017) Multi-objective redundancy allocation problem for a system with repairable components considering instantaneous availability and strategy selection. Reliab Eng Syst Saf 160:11–20
Khoei MA, Aria SS, Gholizadeh H, Goh M, Cheikhrouhou N (2023) Big data-driven optimization for sustainable reverse logistics network design. J Ambient Intell Humaniz Comput 14(8):10867–10882
Khalili-Damghani K, Abtahi AR, Tavana M (2013) A new multi-objective particle swarm optimization method for solving reliability redundancy allocation problems. Reliab Eng Syst Saf 111:58–75
Kim H, Kim P (2017) Reliability–redundancy allocation problem considering optimal redundancy strategy using parallel genetic algorithm. Reliab Eng Syst Saf 159:153–160
Kim HS, Jeon GW (2012) A reliability optimization problem of system with mixed redundancy strategies. IE Interfaces 25(2):153–162
Levitin G, Xing L, Ben-Haim H, Dai Y (2013) Reliability of series-parallel systems with random failure propagation time. IEEE Trans Reliab 62(3):637–647
Liang YC, Lo MH (2010) Multi-objective redundancy allocation optimization using a variable neighborhood search algorithm. J Heuristics 16(3):511–535
Liu Y (2016) Improved bat algorithm for reliability-redundancy allocation problems. Int J Secur Appl 10(2):1–12
Mellal MA, Zio E (2020) System reliability-redundancy optimization with cold-standby strategy by an enhanced nest cuckoo optimization algorithm. Reliab Eng Syst Saf 201:106973
Mendoza CD, Penati V (2020) Joint evaluation of lateral transshipment policies, inventory control policies and maintenance strategies in the spare parts supply chain network: a simulation-based study. http://hdl.handle.net/10589/153752
Nahas N, Nourelfath M, Ait-Kadi D (2007) Coupling ant colony and the degraded ceiling algorithm for the redundancy allocation problem of series–parallel systems. Reliab Eng Syst Saf 92(2):211–222
Nayeri S, Torabi SA, Tavakoli M, Sazvar Z (2021) A multi-objective fuzzy robust stochastic model for designing a sustainable-resilient-responsive supply chain network. J Clean Prod 311:127691
Özçelik G, Faruk Yılmaz Ö, BetülYeni F (2021) Robust optimisation for ripple effect on reverse supply chain: an industrial case study. Int J Prod Res 59(1):245–264
Pourdarvish A, Ramezani Z (2013) Cold standby redundancy allocation in a multi-level series system by memetic algorithm. Int J Reliab Qual Saf Eng 20(03):1340007
Pourkarim Guilani P, Azimi P, Sharifi M, Amiri M (2019) Redundancy allocation problem with a mixed strategy for a system with k-out-of-n subsystems and time-dependent failure rates based on Weibull distribution: An optimization via simulation approach. Sci Iran 26(2):1023–1038
Pietrzykowski M, Woś B, Tylek P, Kwaśniewski D, Juliszewski T, Walczyk J, ... Tabor S (2021). Carbon sink potential and allocation in above-and below-ground biomass in willow coppice. J For Res, 32, 349–354
Qu S, Wei J, Wang Q, Li Y, Jin X, Chaib L (2023) Robust minimum cost consensus models with various individual preference scenarios under unit adjustment cost uncertainty. Inf Fusion 89:510–526
Razavi N, Gholizadeh H, Nayeri S, Ashrafi TA (2021) A robust optimization model of the field hospitals in the sustainable blood supply chain in crisis logistics. J Oper Res Soc 72(12):2804–2828
Roy P, Mahapatra BS, Mahapatra GS, Roy PK (2014) Entropy based region reducing genetic algorithm for reliability redundancy allocation in interval environment. Expert Syst Appl 41(14):6147–6160
Raeisi D, JafarzadehGhoushchi S (2022) A robust fuzzy multi-objective location-routing problem for hazardous waste under uncertain conditions. Appl Intell 52(12):13435–13455
Sadjadi SJ, Soltani R (2015) Minimum–maximum regret redundancy allocation with the choice of redundancy strategy and multiple choice of component type under uncertainty. Comput Ind Eng 79:204–213
Saghih AMF, Modares A (2022) A new dynamic model to optimize the reliability of the series-parallel systems under warm standby components. J Ind Manag Optim 19(1):376–401
Sahebjamnia N, Fathollahi-Fard AM, Hajiaghaei-Keshteli M (2018) Sustainable tire closed-loop supply chain network design: Hybrid metaheuristic algorithms for large-scale networks. J Clean Prod 196:273–296
Samuel CN, Venkatadri U, Diallo C, Khatab A (2020) Robust closed-loop supply chain design with presorting, return quality and carbon emission considerations. J Clean Prod 247:119086
Sarkar A, Panja SC, Sarkar B (2011) Survey of maintenance policies for the last 50 years. Int J Softw Eng Appl 2(3):130–148
Sarada Y, Sangeetha S (2022) A δ-shock model for reengineering of a repairable supply chain using quasi renewal process. Communications in Statistics-Theory and Methods 51(18):6476-6501
Sazvar Z, Zokaee M, Tavakkoli-Moghaddam R, Salari SAS, Nayeri S (2021) Designing a sustainable closed-loop pharmaceutical supply chain in a competitive market considering demand uncertainty, manufacturer’s brand and waste management. Ann Oper Res 315:2057–2088
Sharifi M, Shahriyari M, Khajepour A, Mirtaheri SA (2021) Reliability optimization of a k-out-of-n series-parallel system with warm standby components. Scientia Iranica. https://doi.org/10.24200/sci.2021.56113.4591
Talafuse TP, Pohl EA (2015) A bat algorithm for the redundancy allocation problem. Eng Optim, 1–11. https://doi.org/10.1080/0305215X.2015.1076402
Valaei MR, Behnamian J (2017) Allocation and sequencing in 1-out-of-N heterogeneous cold-standby systems: multi-objective harmony search with dynamic parameters tuning. Reliab Eng Syst Saf 157:78–86
Wang L, Li LP (2012) A co-evolutionary differential evolution with harmony search for reliability–redundancy optimization. Expert Syst Appl 39(5):5271–5278
Wang W, Wu Z, Xiong J, Xu Y (2018) Redundancy optimization of cold-standby systems under periodic inspection and maintenance. Reliab Eng Syst Saf 180:394–402
Wang W, Xiong J, Xie M (2015) Cold-standby redundancy allocation problem with degrading components. Int J Gen Syst 44(7–8):876–888
Wu P, Gao L, Zou D, Li S (2011) An improved particle swarm optimization algorithm for reliability problems. ISA Trans 50(1):71–81
Xu Y, Liao H (2015) Reliability analysis and redundancy allocation for a one-shot system containing multifunctional components. IEEE Trans Reliab 65(2):1045–1057
Yılmaz ÖF (2020) Examining additive manufacturing in supply chain context through an optimization model. Comput Ind Eng 142:106335
Yilmaz OF, Durmusoglu MB (2019) Multi-objective scheduling problem for hybrid manufacturing systems with walking workers. Int J Ind Eng 26(5):625–650
Yılmaz ÖF, Özçelik G, Yeni FB (2021) Ensuring sustainability in the reverse supply chain in case of the ripple effect: A two-stage stochastic optimization model. J Clean Prod 282:124548
Yeh WC, Hsieh TJ (2011) Solving reliability redundancy allocation problems using an artificial bee colony algorithm. Comput Oper Res 38(11):1465–1473
Zhang E, Chen Q (2016) Multi-objective reliability redundancy allocation in an interval environment using particle swarm optimization. Reliab Eng Syst Saf 145:83–92
Zhang E, Wu Y, Chen Q (2014) A practical approach for solving multi-objective reliability redundancy allocation problems using extended bare-bones particle swarm optimization. Reliab Eng Syst Saf 127:65–76
Zoulfaghari H, Hamadani AZ, AboueiArdakan M (2014) Bi-objective redundancy allocation problem for a system with mixed repairable and non-repairable components. ISA Trans 53(1):17–24
Zoulfaghari H, Hamadani A, AboueiArdakan M (2015) Multi-objective availability-redundancy allocation problem for a system with repairable and non-repairable components. Decis Sci Lett 4(3):289–302
Author information
Authors and Affiliations
Contributions
Hadi Gholizadeh: Conceptualization, Methodology, Soft-ware, Validation, Formal analysis, Investigation, Data curation, Writing – original draft.
Ali Falahati Taft: Methodology, Formal analysis, Project administration.
Farid Taheri: Visualization, Software.
Hamed Fazlollahtabar: Writing – review & editing, Supervision, Investigation.
Mark Goh: Writing – review & editing, Visualization, Supervision.
Zohreh Molaee: Formal analysis, Methodology.
Corresponding author
Ethics declarations
Ethics approval and consent to participate
Not applicable.
Consent for publication
Not applicable.
Conflicts of interest/Competing interests
The authors declare that there is no Conflicts of interest/Competing interests.
Additional information
Publisher's note
Springer Nature remains neutral with regard to jurisdictional claims in published maps and institutional affiliations.
Rights and permissions
Springer Nature or its licensor (e.g. a society or other partner) holds exclusive rights to this article under a publishing agreement with the author(s) or other rightsholder(s); author self-archiving of the accepted manuscript version of this article is solely governed by the terms of such publishing agreement and applicable law.
About this article
Cite this article
Gholizadeh, H., Taft, A.F., Taheri, F. et al. Designing a closed-loop green outsourced maintenance supply chain network for advanced manufacturing systems with redundancy strategy and eco-friendly parts. Appl Intell 53, 23905–23928 (2023). https://doi.org/10.1007/s10489-023-04821-z
Accepted:
Published:
Issue Date:
DOI: https://doi.org/10.1007/s10489-023-04821-z