Abstract
This paper presents thermo-mechanical modeling on multilayered metallic microstructures consisting of two bilayers that enable 3D deployment once being Joule heated. A representative design of such microstructures, as well as their working principle is introduced. A mathematical model is derived using Euler–Bernoulli beam theory, and analytical solutions describing out-of-plane displacement of the multilayered microstructures when uniformly heated, which is validated by finite element analysis. Parametric analysis on thermal load and dimensional change of beam shows a good agreement between the analytical solutions and results given by finite element analysis. The phases of the near-equiatomic NiTi layer are analyzed by EDS and XRD, which prove to be austenite during the Joule heating process. The mechanical properties of austenite NiTi are incorporated into the analytical solutions that provides a good estimation of 3D deployment of microstructures made of NiTi and aluminum. The experimental results provide an approximately 7 µm out-of-plane deployment by applying a uniform temperature increase of 132 K, and parametric analysis on the dimension of top aluminum beam offers another promising approach to larger 3D deployment. The proposed mathematical model provides an efficient tool for predicting the out-of-plane deployment of such multilayered microstructures.
Similar content being viewed by others
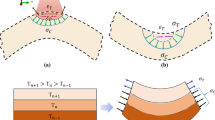
Explore related subjects
Discover the latest articles, news and stories from top researchers in related subjects.Avoid common mistakes on your manuscript.
1 Introduction
Microactuators allowing vertical displacement have been widely used in such applications as micromirror arrays (Song et al. 2018), microgrippers (Shintake et al. 2018; Somà et al. 2018), switches (BARACU et al. 2019), programmable microstructures (Knick et al. 2019b), and soft microrobtics (Hines et al. 2017). Ceramics (Galos et al. 2017; Jafferis et al. 2015), metals (Najafi Sohi and Nieva 2016; Su et al. 2019; Zainal et al. 2015), polymers (Zolfagharian et al. 2016), as well as multiple combinations among them have been chosen for developing such microstructures (Choudhary et al. 2011).
Though many approaches and materials are available for building out-of-plane microactuators (Li et al. 2015), thermal actuators usually show more advantages over the others when it comes to large displacement, cost-effective mass production, and a variety of candidate materials including ceramics, metals and polymers (Ghosh et al. 2017; Knick et al. 2019a). Besides that, lightweight and large areal densities are inherently attributed to electrical thermal actuators consisting of bilayer beams (Ren et al. 2018, 2019). Surface microfabrication offers a mature and efficient approach for bilayer thermal actuators that can be tested and characterized on silicon wafers after released (Knick et al. 2019b). While large displacement of such lightweight microactuators have attracted much attentions to the need of microgrippers and switches, enhaced stiffness and bending strength are basically demanded in many other applications, such as micro clot retriever (Investigators 2009; Vikas Gupta 2004), micro robots (Combes 2003; JianFeng and Cho 2014; Shang et al. 2009), and micro sails for chip scale microsatellites (Atchison and Peck 2011; Macdonald 2014).
Generally, thermal microactuators created by surface microfabrication, also known as 2D microstructures, are basically patterned to various planar geometries with very small thicknesses, which inevitably leads to weak bending strength. There are several representative researchers who have been trying to overcome the restriction through different approaches. Inspired by reconfigurable structures, vertical deployment of multiple microstructures made of bilayer beams were proposed to alleviate this issue (Yan et al. 2017; Yan et al. 2016; Zhang et al. 2017). However, these microstructures cannot be actuated actively, and external bases are necessary to provide prestrain to deform these 2D microstructures to 3D ones. The prestrain bases which help enhance bending stiffness have proven to be an obstacle to active control of the deployed 3D lightweight microstructures for more diverse and complicated surroundings.
In a previous research, our group had proposed a promising design of multilayered metallic microstructures made of two materials, NiTi alloys and Aluminum (Ren et al. 2019). Such microstructures can be fabricated and tested easily and effectively after released from substrates (Ren et al. 2018). A representative module of the mentioned microstructures is shown in Fig. 1. Aluminum is chosen for Material 1 (marked as red), while NiTi alloys are chosen for Material 2 (marked as blue). The Al\NiTi bilayer thin film is deposited in sequence on patterned negative photoresist, and then lifted off to get bilayer Al\NiTi beams connected by bonding sites. Prior to the symmetrical deposition of NiTi\Al atop the bottom Al\NiTi bilayer, evaporation of polysilicon as sacrificial layer between the bottom and top bilayers. Polysilicon deposited on bonding sites are etched to expose bottom NiTi layer, which will be bonded the top NiTi layer. Final step of dry etch removes the polysilicon sandwiched by the bilayers, as well as the silicon substrate beneath the bottom Al layer. Released multilayered microstructures could be electro-thermally actuated to deploy from 2 to 3D microstructures due to the mismatch of coefficients of thermal expansion (CTE) between Al and NiTi. It is worth noting that there could be many phases in NiTi layer, and post-annealing process is usually introduced to get uniform phases.
An analytical electro-thermal actuation model have been established to analyze the effect of Joule heating on thermal distribution across the multilayered microstructure in a previous work (See Supplemental Material which had been accepted for publication). However, the corresponding thermo-electrical model remains lacking. It is urgent to develop the analytical thermo-mechanical models to complete the electro-thermo-mechanical analysis of the multilayered metallic microstructures, which lays the consolidated foundation for precise and effective control of the vertical displacement of such microstructures.
The first study on bi-metallic beams could date back to 1925 (Timoshenko 1925) when Timokenko established bending equations for bi-metallic strips with rectangular cross sections by using Euler–Bernoulli beam theory. Both of simply and fixed supporting ends were considered in his research, and the formula for curvature of such bilayer strips are derived. However, the axial load resulting from limiting the thermal expansion of the strips was ignored in the orignial research. More practical models for bilayer beam supported by simply supporting ends was proposed in (Burgreen and Manitt 1969; Burgreen and Regal 1971). A kind of multilayered cantilever microactuator actuated by Joule heating was investigated, and its deflection was described by an electro-thermo-mechanical model validated by finite element analysis and experiments (Jiang et al. 2007). Similar research also includes (Christophersen et al. 2006; Hsueh 2002; Rahaeifard 2016; Yan et al. 2004) where Euler–Bernoulli beam theory is widely used. These research had paid more effort on models for vertical displacement, while the microstructures presented in Fig. 1 could combine the large vertical displacement with enhanced strength by selective bonding the top bilayer beams to the bottom ones. Such a design differs this research from previous ones, and related thermo-mechanical model on the vertical deployment of such multilayered beams are badly needed.
This paper is organized as follows. Firstly, the phase mechanical properties of NiTi layers are characterized and determined after post-annealing process. Then, a mathematical model for thermo-mechanical behaviors is developed for analytical solutions, which is followed by its validation using the finite element analysis. Finally, practical experiments for in-situ electrical characterization of the microstructures are presented.
2 Characterization of the NiTi alloy layers
2.1 NiTi sputtering and compositions
The fabrication started with cleaning (100) p-type silicon wafers. Then, the negative photoresist, ma-N1420, was spin-coated on the wafer after pre-processing in the HMDS oven at 150 °C for 16 min. The HMDS layer helped improve the adhesion between the silicon surface and ma-N1420. The resist was spinning coated on wafers at a rate of 3000 rpm for 30 s, followed by prebake at 110 °C for 2 min on a hotplate. Next, the photoresist was exposed by h-line (405 nm) UV light on a Karl SUSS MA6 Mask Aligner for 35 s with a constant power of 12 mW/cm2, followed by development for 2 min in the metal ion free Tetramethylammonium hydroxide (TMAH) based developer ma-D 533/S. The profile of the developed resist was measured by the Dektak stylus profiler, and the thickness of the coated resist was 2.5 µm, as shown in Fig. 2. The undercut of developed resist was measured to be 1.2 µm by optical microscope, which ensures safe and clean lift-off of 0.6 µm Al\NiTi bilayers.
After deposition of 0.3 µm Al by electron beam evaporation, NiTi thin films were co-sputtered onto the Al layer in a Kurt J. Lesker PVD 75A machine. A Ni-50at%-Ti target was installed on the DC source, while a pure Ti target was fixed on the RF source. The wafer substrate was glued on the plate with a cooling system, which helped keep a constant room temperature of as-deposited thin films during the sputtering process. The base pressure was pumped down to 8e-7 torr, and then the power of turbo pumper was slowed to 50% before the injection of argon gas (5 mtorr). 200 W DC power and 100 W RF power were applied on Ni50Ti50 target and pure Ti target, respectively. The surficial oxidized layers on NiTi and Ti targets were cleaned by argon gas while the shutter for the substrate was kept closed to prevent the sputtered atoms from depositing on the substrate. Then, 0.3 µm NiTi thin film deposited onto Al layer at a constant rate of 1.55 A/s. Finally, 1165 PG remover was used to lift off the Al\NiTi bilayer at 65ºC for 1 h.
The composition of Ni and Ti was determined by energy dispersive scattering (EDS) using Analytical SEM JEOL 7600F, as shown in Fig. 3. Fourteen representative spectrums on the as-deposited NiTi layer were sampled for EDS analysis, and the results on atomic ratios of Ni to Ti were listed in Table 1. It could be seen that that the compositions of Ni and Ti at different sites are very close, and the average composition of as-deposited NiTi layer is Ni-50.25at%-Ti. Therefore, the NiTi alloys can be safely considered to be equiatomic.
2.2 Post-annealing on NiTi thin films
Given that the composition of Ni in NiTi has big influence on the transformation temperature, it is necessary to determine what kinds of phases are included in the post-annealing microstructures. Post-annealing process on the NiTi thin films on the substrate is carried out by using Rapid Thermal Processing (RTP, Allwin21).
The NiTi thin films are annealed at 550 °C for 10 min in protective Ar gas. The XRD results of bare wafer, as-deposited NiTi/wafer, and annealed NiTi/wafer are plotted in Fig. 4. It can be seen that the amorphous NiTi thin films are trained to such crystal phases as martensite and austenite. Further intensity counts’ comparasion between the two phases reveals that NiTi alloys mainly exist in austenite. Hence, it can be safely assumed that the NiTi layers remain austenite phase during the thermal actuation between room temperature to higher ones. The mechanical properties of chosen materials, Al (\(i = 1\)) and Ni50Ti50 (\(i = 2\)), are listed in Table 2.
The whole microstructures will be completed after an symmetrical deposition of NiTi\Al top bilayers, followed by XeF2 dry etch process to release the multilayered structures from wafers, as shown in Fig. 5. It could be seen clearly that the edges of the beams are free of beads owe to the good undercut of developed ma-N1420.
3 Thermo-mechanical model
A two-dimensional diagram for the out-of-plane deployment of the 2D multilayered microstructures, as well as the thermal moment when uniformly heated by ΔT across the beams, is given schematically in Fig. 6.
Euler–Bernoulli beam theory is employed for the mathematical thermo-mechanical model. The left bonding site is assumed to be fixed, while the right side is set free. Thermal moment is produced when the top and bottom beams are heated owe to the effect of thermal mismatch. Furtherly, the thermal moment in the bottom bilayer can be given by
where the location of neutral axis of the bottom bilayer from the x-axis shown in Fig. 6 is calculated by
Similarly, the thermal moment in the top bilayer could be expressed as
where \(z_{tc}\) is the location of neutral axis of segment (b) in top bilayer measured from the top edge of the gap, as seen in Fig. 6. Since the width of the top Al layer is narrower than that of the top NiTi, the formula for its neutral axis needs take the effect of widths into consideration, that is,
It is necessary to clearly point out all the typical bending cases in different segments of the multilayered beam, as shown in (a), (b) and (c) in Fig. 6. The flexural rigidity of segment (a) could be directly given by \(E_{2} I_{3}\), where
Moreover, the effective flexural rigidity of segments (b) and (c) can be obtained by
and \(\left( {EI} \right)_{b} = E_{1} b_{b1} \left[ {\frac{{h_{b1}^{3} }}{12} + h_{b1} (z_{bc} - \frac{{h_{b1} }}{2})^{2} } \right] + E_{2} b_{b2} \left[ {\frac{{h_{b2}^{3} }}{12} + h_{b2} (z_{bc} - h_{b1} - \frac{{h_{b2} }}{2})^{2} } \right]\), respectively. As such, the equilibrium bending equations for (a), (b) and (c) can be written as
where \(\rho_{1}\), \(\rho_{2}\) and \(\rho_{3}\) refer to the radius of curvature of segments (a), (b) and (c), respectively.
To keep the continuity of top and bottom bilayer beams at the bonding sides, the boundary conditions given in Eq. (8) must be satisfied:
The relations between \(\theta_{i}\) (\(i\) = 1, 2, 3) and \(\rho_{i}\)(\(i\) = 1, 2, 3) can be expressed as
Note that the \(\theta_{i}\) and \(\rho_{i}\) could be negative values. Negative \(\theta_{i}\) mean that the included angles between the x-axis and the tangents of beam profiles become smaller as the point moves towards x-axis, while the negative \(\rho_{i}\) mean the corresponding centers of the bending segments locate beneath x-axis. To be more specific, \(\theta_{2}\) and \(\rho_{2}\) are negative, while \(\theta_{1}\), \(\theta_{3}\), \(\rho_{1}\) and \(\rho_{3}\) are positive, as shown in Fig. 6. Substituting Eqs. (1) ~ (7) and Eqs. (9) ~ (11) into Eq. (8), we obtain
To verify the analytical solutions on the 3D deployment of the 2D multilayered beams, Coventorware is chosen for finite element analysis on the deformation under uniform temperature distribution. All the dimensional parameters except the length of the top Al beam \(L_{t1}\) are set as constant. Besides that, thermal load applied by temperature increase \(\Delta T\) is the other factor to be evaluated for the effect of vertical displacement. The effect of 3D deployment is measured by out-of-plane displacement \(\delta\) shown in Fig. 6 and formulated by Eq. (13).
where \(\left| {\overrightarrow {{O_{2} O_{3} }} } \right|\) can be calculated by using the law of cosines:
Following parametric analysis on the thermal load and length of the top Al beam is carried out by the analytical models and the finite element model. The displacements of \(\delta_{t}\) and \(\delta_{t}\) with respect to the top Al beams’ lengths ranging from 1 to 200 µm are plotted at four different temperature loads of 50 K, 100 K, 150 K, 200 K, as seen in Fig. 7.
The continuous curves are results obtained from the analytical model, while the concrete points are corresponding results exported from the Coventorware. It can be seen clearly that there is an excellent agreement between the solutions given by the analytical model and that obtained by finite element analysis. As such, the reliability of the analytical model on thermos-mechanical behaviour of presented multilayered microstructures are validated, which provides a much more effective approach to estimating the deployment of such microstructures than finite element simulation.
4 Experimental validation
To substantiate the thermo-mechanical model presented above, the fabrication and electrical characterization on mentioned multilayered microstructures are completed. A similar experimental setup as shown in the previous research is employed. Four-point resistance measurement using MMR variable temperature probe station on the representative released microstructures after post-annealing is shown in Fig. 5, which is used for four-probe station to calibrate the relation between the equivalent resistance and balanced temperature. After that, the contact pads are connected to a logic PCB using the gold wire bonder, as shown in Fig. 8, followed by the in-situ electrical actuation on the microstructure in the Dual Scanning Electron Microscope (SEM)/Focused Ion Beam (FIB) system (FEI Helios). A functional generator provides a voltage input to the PCB and measures the in-situ resistance of the structures under different voltages. The in-situ temperature could be derived from the resistance by using their calibrated relation by the probe station.
The length of the top Al beam in the experiment is 193 µm, 10 µm shorter than the top NiTi beam. The out-of-plane deployment are defined by \(\delta_{t} + \delta_{b}\) which is measured from SEM imaging in vacuum surroundings. The relation between the measured displacement and in-situ balanced temperature is plotted in the blue line shown in Fig. 9, whereas the red one represents the corresponding analytical solutions.
They appear to be in good agreement with each other. It is worth noting that there is still some residual stress in the microstructures after post-annealing, which contributes the initial deployment shown in Fig. 5. An initial deployment approximately 6.3 µm resulting from residual thermal stress is deducted from the measured displacement obtained from SEM images. The analytical solution reveals a good linear relation between the 3D deployment and thermal load, and an displacement of 7 µm is expected when the microstructure is heated to achieve a temperature increase of 132 K, which is more than 10 times larger than the thickness of bilayer beams. Another effective approach to achieve much larger deployment could be properly modifying the length of the top Al beam, which is already demonstrated by analytical solutions shown in Fig. 7.
5 Conclusions
In summary, a thermo-mechanical model for multilayered microstructures allowing out-of-plane 3D deployment is proposed in this paper, as a necessary and further supplementary research from the electro-thermal modeling. The core microstructures made of two metallic bilayers are separated from the grid microstructures, which simplifies the analytical modeling reasonably. The phases of equiatomic NiTi alloys are determined by EDS and XRD after a rapid thermal annealing process. It turns out to be almost austenite at room temperature, which provides necessary and convincing mechanical properties for the following modeling and varification. The analytical model is derived and solved for analytical solutions based on Euler–Bernoulli beam theory, which is validated by finite element analysis and experiments. The comparison results reveal very good agreements, and thus validate the feasibilitiy of estimating 3D deployment for microstructures based on presented such multilayered beams. In addition to increasing thermal load, the parametric analysis of the effect of length of top Al beams on the out-of-plane displacement provides more promising approach for large deployment. Moreover, proper changes of composition of Ni in NiTi alloy could increase the transformation temperature of NiTi to above room temperature, and the combination of thermal mismatch and shape memory effect could improve the efficiency of deployment and thus bending stiffness dramatically.
References
Atchison JA, Peck MA (2011) Length scaling in spacecraft dynamics. J Guid Control Dyn 34:231–246
Baracu A, Muller R, Voicu R, Tibeica C, Dinescu A, Pustan M, Birleanu C (2019) Microfabrication and experimental characterization of an Out-of-Plane MEMS switch. Sci Technol 22:124–134
Burgreen D, Manitt PJ (1969) Thermal buckling of a bimetallic beams. J Eng Mech Div 95:421–432
Burgreen D, Regal D (1971) Higher mode buckling of bimetallic beam. J Eng Mech Div 97:1045–1056
Choudhary N, Kharat D, Kaur D (2011) Surface modification of NiTi/PZT heterostructure thin films using various protective layers for potential MEMS applications. Surf Coat Technol 206:1735–1743
Christophersen M, Shapiro B, Smela E (2006) Characterization and modeling of PPy bilayer microactuators. Sens Actuators B: Chem 115:596–609. https://doi.org/10.1016/j.snb.2005.10.023
Combes SA (2003) Flexural stiffness in insect wings I. Scaling and the influence of wing venation. J Exp Biol 206:2979–2987. https://doi.org/10.1242/jeb.00523
Galos R, Shi Y, Ren Z, Zhou L, Sun H, Su X, Yuan J (2017) Electrical impedance measurements of PZT nanofiber sensors. J Nanomater. https://doi.org/10.1155/2017/8275139
Ghosh B, Jain R, Majumder S, Roy S, Mukhopadhyay S (2017) Experimental performance evaluation of smart bimorph piezoelectric actuator and its application in micro robotics. Microsyst Technol 23:4619–4635
Hines L, Petersen K, Lum GZ, Sitti M (2017) Soft actuators for small-scale robotics. Adv Mater 29:1603483
Hsueh C (2002) Thermal stresses in elastic multilayer systems. Thin Solid Films 418:182–188
Investigators PPST (2009) The penumbra pivotal stroke trial: safety and effectiveness of a new generation of mechanical devices for clot removal in intracranial large vessel occlusive disease. Stroke 40:2761–2768
Jafferis NT, Smith MJ, Wood RJ (2015) Design and manufacturing rules for maximizing the performance of polycrystalline piezoelectric bending actuators. Smart Mater Struct. https://doi.org/10.1088/0964-1726/24/6/065023
Jian F, Cho S (2014) Mini and micro propulsion for medical swimmers. Micromachines 5:97–113. https://doi.org/10.3390/mi5010097
Jiang J, Hilleringmann U, Shui X (2007) Electro-thermo-mechanical analytical modeling of multilayer cantilever microactuator. Sens Actuators A Phys 137:302–307
Knick CR, Sharar DJ, Wilson AA, Smith GL, Morris CJ, Bruck HA (2019a) High frequency, low power, electrically actuated shape memory alloy MEMS bimorph thermal actuators. J Micromech Microeng 29:075005
Knick CR, Smith GL, Morris CJ, Bruck HA (2019b) Rapid and low power laser actuation of sputter-deposited NiTi shape memory alloy (SMA) MEMS thermal bimorph actuators. Sens Actuators A Phys 291:48–57
Li X, Zhao Y, Hu T, Xu W, Zhao Y, Bai Y, Ren W (2015) Design of a large displacement thermal actuator with a cascaded V-beam amplification for MEMS safety-and-arming devices. Microsyst Technol 21:2367–2374. https://doi.org/10.1007/s00542-015-2447-1
Macdonald M (2014) Advances in solar sailing. Springer Science and Business Media, Berlin
Najafi Sohi A, Nieva PM (2016) Frequency response of curved bilayer microcantilevers with applications to surface stress measurement. J Appl Phys 119:044503
Rahaeifard M (2016) Static behavior of bilayer microcantilevers under thermal actuation. Int J Eng Sci 107:28–35
Ren Z et al (2019) Vertical deployment of multilayered metallic microstructures with high area-to-mass ratios by thermal actuation. J Micro Nano-Manuf. https://doi.org/10.1115/1.4043987
Ren Z, Yuan J, Su X, Sun H, Galos R, Shi Y (2018) A new fabrication process for microstructures with high area-to-mass ratios by stiffness enhancement. In: ASME 2018 international design engineering technical conferences and computers and information in engineering conference, 2018. American society of mechanical engineers, pp V004T008A034-V004T008A034
Shang JK, Combes SA, Finio BM, Wood RJ (2009) Artificial insect wings of diverse morphology for flapping-wing micro air vehicles. Bioinspir Biomim 4:036002. https://doi.org/10.1088/1748-3182/4/3/036002
Shintake J, Cacucciolo V, Floreano D, Shea H (2018) Soft robotic grippers. Adv Mater 2018:e1707035. https://doi.org/10.1002/adma.201707035
Somà A, Iamoni S, Voicu R, Müller R, Al-Zandi MH, Wang C (2018) Design and experimental testing of an electro-thermal microgripper for cell manipulation. Microsyst Technol 24:1053–1060
Song Y, Panas RM, Hopkins JB (2018) A review of micromirror arrays. Precis Eng 51:729–761
Su X, Ren Z, Yan J, Shi Y, Pan Q (2019) Microstructure and twisting ability of an adjusted antisymmetric angle ply laminate. Appl Phys Lett 114:211902
Timoshenko S (1925) Analysis of bi-metal thermostats. JOSA 11:233–255
Vikas GADJ, Martynov V, Menchaca L (2004) Nitinol thin film three-dimensional devices-fabrication and applications.pdf
Yan D, Khajepour A, Mansour R (2004) Design and modeling of a MEMS bidirectional vertical thermal actuator. J Micromech Microeng 14:841
Yan Z et al (2016) Mechanical assembly of complex, 3D mesostructures from releasable multilayers of advanced materials Science advances 2:e1601014
Yan Z et al (2017) Three-dimensional mesostructures as high-temperature growth templates, electronic cellular scaffolds, and self-propelled microrobots. Proc Natl Acad Sci USA 114:E9455–E9464. https://doi.org/10.1073/pnas.1713805114
Zainal MA, Sahlan S, Ali MSM (2015) Micromachined shape-memory-alloy microactuators and their application in biomedical devices. Micromachines 6:879–901
Zhang Y, Zhang F, Yan Z, Ma Q, Li X, Huang Y, Rogers JA (2017) Printing, folding and assembly methods for forming 3D mesostructures in advanced materials. Nat Rev Mater. https://doi.org/10.1038/natrevmats.2017.19
Zolfagharian A, Kouzani AZ, Khoo SY, Moghadam AAA, Gibson I, Kaynak A (2016) Evolution of 3D printed soft actuators. Sens Actuators A: Phys 250:258–272. https://doi.org/10.1016/j.sna.2016.09.028
Acknowledgements
The National Natural Science Foundation of China (No. 11572248) and China Scholarship Council have in part supported the research. The research was in part carried out at the Center for Functional Nanomaterials (CFN), Brookhaven National Laboratory (BNL), which is supported by the US Department of Energy, Office of Basic Energy Sciences, under Contract No. DE-SC0012704.
Author information
Authors and Affiliations
Corresponding authors
Additional information
Publisher's Note
Springer Nature remains neutral with regard to jurisdictional claims in published maps and institutional affiliations.
Electronic supplementary material
Below is the link to the electronic supplementary material.
Rights and permissions
About this article
Cite this article
Ren, Z., Yuan, J., Su, X. et al. Thermo-mechanical modeling and experimental validation for multilayered metallic microstructures. Microsyst Technol 27, 2579–2587 (2021). https://doi.org/10.1007/s00542-020-04988-2
Received:
Accepted:
Published:
Issue Date:
DOI: https://doi.org/10.1007/s00542-020-04988-2