Abstract
Fast-responding pressure-sensitive paint (Fast PSP) and temperature-sensitive paint (TSP) measurements were conducted on two turbocharger compressors using a single-shot lifetime-based technique. The fast PSP and TSP were applied on separate blades of one compressor, and both paints were excited by a pulsed 532 nm Nd:YAG laser. The luminescent decay signals following the laser pulse were recorded by a CCD camera in a double-exposure mode. Instantaneous pressure and temperature fields on compressor blades were obtained simultaneously, for rotation speeds up to 150,000 rpm. The variations in pressure and temperature fields with rotation speed, flow rate and runtime were clearly visualized, showing the advantage of high spatial resolution. Severe image blurring problems and significant temperature-induced errors in the PSP results were found at high rotation speeds. The first issue was addressed by incorporating a deconvolution-based deblurring algorithm to recover the clear image from the blurred image using the combination of luminescent lifetime and rotation speed. The second issue was resolved by applying a pixel-by-pixel temperature correction based on the TSP results. The current technique has shown great capabilities in flow diagnostics of turbomachinery and can serve as a powerful tool for CFD validations and design optimizations.
Similar content being viewed by others
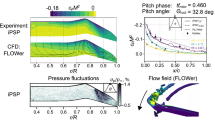
Avoid common mistakes on your manuscript.
1 Introduction
The highly unsteady turbomachinery flows are closely related to the aerodynamic performance and the structural integrity of engine components. Surface pressure and temperature fields with high spatial resolution are strongly desired to understand the complex internal flow, validate the numerical codes and provide basis for design strategies. Unfortunately, such information is usually difficult to obtain on rotating components such as compressor blades, especially at high rotation speeds. Miniature semi-conductor pressure transducers and thin-film sensors have been developed and applied for surface pressure and temperature/heat flux measurements on rotating blades, respectively (Sieverding et al. 2000; Ainsworth et al. 2000). However, those single-point measurement techniques have disadvantages including low spatial resolution and high cost. There are also challenges in signal transmission (either by slip-ring or wireless device) which typically result in reduced signal-to-noise ratio. Alternatively, it is possible to capture the blade temperature fields using infrared thermometry, but both the spatial and temporal resolutions are limited by the long exposure time of an IR camera (Juliano et al. 2012; Pastuhoff et al. 2016). In contrast, pressure- and temperature-sensitive paints have shown excellent capabilities in providing full-field, high spatial resolution data with greatly reduced cost (Liu and Sullivan 2005). Owing to the recent developments in fast-responding PSPs and lifetime-based techniques, PSP and TSP measurements on rotating blades with high-fidelity have been achieved, showing great promises in unsteady flow diagnostics in turbomachinery (Gregory et al. 2008, 2014a).
PSP and TSP measurements on fast rotating surfaces have three major challenges. Firstly, short exposure time must be used to freeze the motion at high rotation speeds, leading to insufficient signal in each exposure and the need of a phase-averaging system to improve signal-to-noise ratio (SNR). This phase-averaging method was adopted by many researchers for different applications including propeller (Burns and Sullivan 1995; Yorita et al. 2012), scale-model fan (Bencic 1998), compressor cascade (Engler et al. 2000), turbocharger compressor (Gregory 2004), helicopter rotor (Wong et al. 2005, 2010; Watkins et al. 2007) and rotating disk (Kameya et al. 2011). However, this method was unable to recognize high-frequency pressure features and cycle-to-cycle variations. To address this issue, a single-shot, lifetime-based technique was proposed by Gregory et al. which adopted a high-energy excitation source such as a pulsed laser to provide high SNR without any phase averaging (Gregory et al. 2009; Juliano et al. 2011). Because the illumination field from a pulsed laser varies from shot to shot, it is necessary to use the lifetime-based method where the reference and pressure-sensitive images come from the same laser pulse. This technique has been shown to be quite effective in capturing instantaneous pressure and temperature fields on helicopter blades, and its fundamentals will be discussed in the next section. The second challenge is image blurring near the edges caused by the finite exposure time and cycle-to-cycle variations in blade position during data acquisition using the phase-averaging method. This issue can be partially resolved if the single-shot method (no phase-averaging) is used, but image blurring still exists at high rotation speed due to the finite luminescent lifetime (usually a few µs). However, it is possible to recover the clear images from the blurred ones using a deconvolution-based deblurring algorithm (Juliano et al. 2012; Gregory et al. 2014b). The third challenge is the temperature-induced errors in PSP measurements, especially at high rotation speed where there is usually a radial temperature gradient on the testing surface due to aerodynamic heating. This error can be corrected using temperature fields obtained from separate temperature measurements (Bencic 1998; Juliano et al. 2012; Klein et al. 2013; Disotell et al. 2014). To avoid problems due to low SNR and image blurring, a laser-scanning method has been developed by several researchers in which a photo-multiplier tube was used to collect the luminescent intensity or decay signal from a single point excited by a focused laser beam (Liu et al. 1997; Engler et al. 2000; Pastuhoff et al. 2016). However, the measurement system for this method was quite complicated and the resulting sampling rate was insufficient for unsteady measurements (each scan required at least 30 s). In addition, the data from each measurement point needed to be averaged within a number for cycles to achieve sufficient SNR.
As the most promising method for full-field pressure and temperature measurements on rotating blades, the single-shot, lifetime-based technique with image deblurring and temperature correction capabilities has been successfully applied on helicopter rotor wind tunnel tests. This technique was first demonstrated on a 0.128 m diameter helicopter model operating at 4900 rpm (Disotell et al. 2014), and then applied on a 3.366 m diameter rotor running at 1150 rpm (Watkins et al. 2016). The PSP and TSP were applied on separated blades, and the data were taken separately at repeatable test conditions. The TSP results were then used to apply temperature correction on the PSP results. However, this technique is yet to be applied on fast rotating targets (104–105 rpm) such as compressor blades, which would pose additional challenges. Most importantly, unsteady temperature fields on blade surface are frequently encountered in turbomachinery. Therefore, simultaneous measurements of pressure and temperature are highly desired to ensure that the temperature-induced errors in PSP results are properly removed. Other concerns include paint applications on highly curved surface, the effect of paints on compressor dynamic balancing and strong image blurring.
In the current study, single-shot lifetime-based PSP and TSP measurements were conducted on two turbocharger compressors with rotation speeds up to 150,000 rpm. The PSP and TSP are applied on separate blades of each compressor and excited by a pulsed Nd:YAG laser (532 nm), so that instantaneous pressure and temperature fields on the blades could be obtained simultaneously. Other challenges of testing and data processing have also been identified and addressed, including the paint preparation, the requirement of dynamic balancing and the image processing methods. The current measurement technique provides full-field pressure and temperature fields with high spatial resolution on fast rotating blades, and can serve as a powerful tool for CFD validations and design optimizations of turbomachines.
2 Experiment setup
2.1 Pressure- and temperature-sensitive paints
The PSP consists of a polymer-ceramic (PC) binder and PtTFPP (from Frontier Scientific) as pressure sensor. The PC binder is basically a mixture of high concentration of ceramic particles with a small amount of polymer to physically hold the ceramic particles to the surface. The luminophores are attached onto the porous surface of the binder, which can interact immediately with oxygen, resulting in a frequency response over 6 kHz (Pandey and Gregory 2016). The TSP uses an oxygen-impermeable automobile clearcoat (Dupont ChromClear HC7776S) as the binder and Ru(dpp) (from GFS Chemicals, Inc.) as the temperature sensor. For the PSP, the binder and the luminophore solution were air-sprayed onto the model separately. For the TSP, the binder was mixed with luminophore solution and then the mixture was air-sprayed onto the model surface. The resulting paint thickness was less than 20 µm and the surface roughness was 1–2 µm. Both PSP and TSP were custom made in Shanghai Jiao Tong University.
This combined PSP/TSP system should meet the following two requirements for simultaneous lifetime-based measurements: (1) both coatings can be excited by the same light source; (2) the signal levels and lifetime values of TSP and PSP are comparable under the test condition. Previous study has shown that both paints can be excited by a 532 nm Nd:YAG laser, and their lifetime values are close at the ambient condition (103 kPa and 298 K) (Peng et al. 2016). The intensity levels can be adjusted by varying the luminophore concentration in the solution using methanol as solvent. The PSP and TSP samples prepared using different luminophore concentrations were examined in a custom-built calibration chamber. Considering the test conditions encountered in the turbocharger test stand, the optimum luminophore concentrations were determined to be 0.3 mg/ml for PSP and 1 mg/ml for TSP, which provided best pressure and temperature sensitivity and close signal levels under 532 nm excitation.
Two turbocharger compressors with different size were tested in the current study, which are referred to as “TC1” and “TC2”. Each compressor has a total of six main blades with one blade applied with TSP and two other blades applied with PSP, as shown in Fig. 1. One of the PSP blades served as a backup, since the PSP was more susceptible to mechanical damage and chemical contamination than the TSP. The painted blades were not adjacent to each other to avoid possible interference effects during image deblurring. The compressors were weighed on an analytical balance (Zhuojing BSM2204, 0.0001 g accuracy) before and after the paint application. The added mass from the paints was found to be within 0.5% of the total mass of the compressor. Still, it was important to check the dynamic balance of the compressors to ensure safe operations at high rotation speeds. The dynamic balance tests were performed using a test bench at Wuxi IHI Turbo (WIT). Then, the compressors and other turbocharger parts were assembled and the turbocharger was finally installed on the test facility for experiment.
2.2 Turbocharger test facility
Figure 2 shows the schematics of the turbocharger test facility at WIT. This facility has been used for performance test of turbocharger products and is typically driven by exhaust gas. During operation, the high pressure air firstly passes through a reducing valve and then through a control valve which sets the flow rate for the turbine inlet. Then the air goes into the combustion chamber through two different pipes which are designed to meet the requirements of different types of turbocharger. The air is mixed with fuel inside the combustion chamber and then ignited to produce the exhaust gas that drives the turbine. It should be note that the turbocharger can also be driven only by the compressed air without combustion. During operation, the compressor draws air from the inlet and the compressed air is transported and finally exhausted outside the room. The facility also has a monitoring system with sensors to measure the inlet and outlet parameters (pressure and temperature), the flow rate, the room temperature and other parameters during operation. The current PSP and TSP measurements were conducted without combustion in the test facility to avoid possible thermal degradation of the paints.
2.3 Single-shot lifetime-based measurement system
The luminescent response I(t) from PSP to a pulsed excitation light can be described by
where τ is the lifetime of the paint and I 0 is the intensity at t = 0 (Liu and Sullivan 2005). The lifetime method for PSP is based on the fact that τ is inversely proportional to the local oxygen concentration, which can be directly related to the air pressure according to Henry’s law. The relation is shown below
where τ ref and p ref are the luminescent intensity and air pressure at a reference condition, respectively. This is similar to the Stern–Volmer equation for intensity-based method.
In single-shot lifetime PSP data acquisition, a single laser pulse provides the illumination for PSP, and a charge-coupled device (CCD) camera is used to take two consecutive images (a pressure-sensitive and a reference image) on the luminescent decay of the paint following the laser pulse. A schematic of the two-gate lifetime approach is shown in Fig. 3 (Juliano et al. 2012). The initial portion of the decay curve (Gate 1) is relatively insensitive to pressure, thus serving as a reference. Gate 2 covers the rest of the luminescent decay which has much higher pressure sensitivity than gate 1. The timing of the gates is selected such that the signal levels in both gates are close. The ratio of the integrated signal from the two gates is computed and calibrated to provide the surface pressure distribution.
Theoretically, assuming the lifetime of the paint at a fixed pressure and temperature is constant over the surface, all pressure information could be obtained from the ratio of two gated signals within a single lifetime decay curve. This would eliminate the need for a wind-off reference. However, it has been shown by Goss et al. that this assumption is invalid due to paint inhomogeneities (Goss et al. 2004, 2005). They also showed that an intensity ratio between two gates at wind-off condition could be used to eliminate the spatial variations in lifetime. The wind-off ratio is mapped to wind-on ratio, resulting in a ratio of ratios. Therefore, the modified Stern–Volmer equation for single-shot, lifetime-based method is
where I 1 and I 2 are intensities from Gate 1 and Gate 2, respectively. This single-shot, lifetime-based method is equally applicable for TSP measurements. The only difference is that the relationship between the intensity ratio of ratios and the temperature ratios is typically nonlinear which requires a polynomial curve fit for calibration.
The measurement system for the turbocharger test is shown in Fig. 4. A laser beam was produced by a 532 nm Nd:YAG laser (Dawa-200, Beamtech, 100 mJ/pulse), which was first expanded by a concave lens and then passed through an optical diffuser to improve the uniformity of the illumination field. The illumination covered the entire compressor disk to provide excitation for both PSP and TSP blades. The luminescent signals were collected by a CCD camera (pco. 1600, pco. imaging) through a long-focus lens (200 mm/f4, Nikon). A 600 nm long-pass filter was installed before the lens to exclude the excitation light. The timing of the system was controlled by a digital pulse/delay generator (BNC-575, Berkeley Nucleonics Corporation). A picture of the TC1 compressor after installation on the test facility is shown on bottom right in Fig. 4.
3 Data acquisition and processing
3.1 Data acquisition
The test conditions in the current study are listed in Table 1. Here, the flow rates have been normalized by one selected case (case 4) of each compressor for proprietary protection reasons. The wind-off images were taken before starting the test facility for each compressor and the room temperature was recorded as T ref. The image size was 800 by 600 with a spatial resolution of 8 pixels per mm. The rotation speed was increased gradually, and wind-on images were taken at four different speeds for each compressor. Three different flow rates at a selected speed (n = 60,000 rpm) were also tested for TC1. A total of 50 images were record at about 4 Hz for each test condition. The maximum speed of TC1 was 80,000 rpm, resulting in a tip speed of 260 m/s. The maximum speed of TC2 reached 150,000 rpm, resulting in a tip speed of 236 m/s. An additional test was performed on TC1 at n = 80,000 rpm to evaluate the effects of runtime, during which the images were taken at 0.5 Hz for a span of 10 min.
3.2 Image processing method
The data processing procedures in the current study are shown in Fig. 5, including four steps: image transformation, image deblurring, image registration and temperature correction. A Cartesian to polar coordinate transformation was performed (see Fig. 6) before implementing image processing techniques (deblurring and registration). Here, the transformation algorithm was developed based on the work by Ribarić et al. (Ribarić et al. 2000). A grid with a radial resolution of 265 pixel/R and 4 pixel/degree was generated in the polar coordinates and the intensity values on the grid were computed using bilinear interpolation based on the original image.
The main merit of the coordinate transformation was that the circumferential blur in the original image became translational blur in the transformed image and could be dealt with conveniently using a deconvolution-based image deblurring technique (Juliano et al. 2012; Gregory et al. 2014b). The blade motion (solid-body rotation) in polar coordinate during image blur is now one-dimensional, as given by
A point-spread function (PSF) was defined based on the lifetime of PSP/TSP and the blade rotation speed. Combining Eqs. (1) and (4), the PSF in polar coordinate could be obtained, as given by
Then, the deblurring operations were performed using a “deconvwnr” function in Matlab based on the above PSF. Sample PSP images of TC1 at 60 k rpm in polar coordinates before and after deblurring are shown in Fig. 7. The image blurring was quite severe under such a high rotation speed (up to 30–40 pixels near blade tip), but the clear image was successfully recovered from the blurred image using the deconvolution-based method. The lifetime values were determined in the following way: τ at the reference condition (10 μs for PSP and 7 μs for TSP) were used initially for deblurring the wind-on images to obtain an estimation of the pressure and temperature fields, and then the τ values of each test condition were updated based on the estimated pressure and temperature fields (using the median value of the corresponding τ field), and the wind-on images were deblurred by the updated τ which yielded the final pressure and temperature results.
Another benefit of the coordinate transformation was that it allowed the implementation of a cross-correlation-based image registration method under polar coordinates (Guizar-Sicairos et al. 2008). This sub-pixel accuracy algorithm was applied on all wind-on images so that they were aligned with the corresponding wind-off images in polar coordinates. An alternative method using projective transformation could be applied directly under Cartesian coordinates based on a set of marker points predefined on the painted blade surface (Disotell et al. 2014). However, it has been shown by Gregory et al. that the deblurring algorithm would produce additional noise near the sharp edges in the image due to the Gibbs effect (Gregory et al. 2014b). Considering the small size of the compressor blades in the current study, the use of marker points was undesirable since it would greatly impair the data quality.
After the image registration was completed, the ratio-and-ratios were computed and the calibration data and temperature correction were applied to yield the pressure and temperature fields. The details of paint calibration and temperature correction are presented in the next subsection. A disk filter (10-pixel size for PSP and 20-pixel size for TSP) was applied to the images before they were transformed back from the polar coordinates to the Cartesian coordinates to produce the final results. Note that all the results presented in the current paper were from single-shot images without any averaging. In addition, it was found in the results that a few pixels at the blade edge showed large fluctuations and unreasonable values. This “edge-pixel anomaly” was attributed to the combination of the Gibbs effect of deblurring algorithm and slight image misalignment caused by blade vibration. Therefore, those pixels were excluded from the final results.
3.3 Paint calibration and temperature correction method
The PSP and TSP calibrations were performed in a custom-built calibration chamber with a pressure range from 0 to 345 kPa and a temperature range from 273 to 323 K. Two 5 mm square paint samples were prepared for PSP and TSP, respectively. The measurement system was similar to the one described in the previous section. The only difference was that a 50 mm lens (50 mm/f1.2, Nikon) was used for calibration, instead of the long-focus lens. The reference pressure and temperature were 103 kPa and 293 K, respectively, and the calibration curves were forced to pass through (1, 1). The pressure calibration results of lifetime-based method are presented in Fig. 8a, showing a linear relation between pressure and intensity for the PSP. In addition, the TSP had very little pressure sensitivity as expected. The temperature calibration results of lifetime-based method are presented in Fig. 8b. The PSP displays significant temperature sensitivity, showing the importance of performing temperature correction using TSP data.
Two different methods for temperature correction were adopted in the current study. At low rotation speeds, it was found that the temperature increased by only a few K on the blade with a relatively uniform distribution and the pressure variations were not significant. Here, the temperature correction was performed on PSP data using the following equation as first suggested by Peng et al. (Peng et al. 2013):
where k was the ratio of temperature sensitivity determined by the calibration results in Fig. 8b. It should be noted that all intensity terms have been replaced by intensity ratios, so that it can be applied to data of the single-shot lifetime-based method. At high rotation speeds (n ≥ 40,000 rpm for TC 1 and n ≥ 100,000 rpm for TC 2), both the pressure and temperature variations were substantial on the compressor blades. As shown in Fig. 9, the temperature calibration varied significantly over a wide range of pressure, which would greatly reduce the accuracy of the previous correction method. However, it was still possible to recover the true pressure using the temperature field obtained from the TSP results. Once the temperature was known, a pressure calibration curve was obtained according to Fig. 9. Then, the pressure was found according to the ratio-of-ratios in the PSP data.
4 Results and discussion
4.1 The TC1 compressor
The instantaneous Temperature fields (presented in normalized value ΔT/T ref) on the TC1 compressor blade at four different rotation speeds are shown in Fig. 10. It is clear that the temperature generally increased during the tests, and the amount of temperature rise increased with rotation speed. At the lowest speed (n = 20,000 rpm), the temperature distribution was fairly uniform with an average ΔT = 7.4 K (see Fig. 10a). At higher speeds, the temperature field was showing a streamwise temperature gradient (increasing in downstream direction) and a radial temperature gradient (increasing from the root to the tip). As a result, the minimum ΔT was located near the root on the leading edge, and the maximum ΔT was found at the tip in downstream region. Both gradients were growing as the rotation speed increased, which are clearly visualized in Fig. 10b–d. The maximum ΔT measured on the blade was about 27 K for the highest speed (n = 80,000 rpm). The streamwise and radial gradients were probably related to the compression effect and the aerodynamic heating, respectively. However, the effect of metal heat transfer from other components (shaft, housing, etc.) could not be neglected. Therefore, more detailed temperature measurements on multiple components of the turbocharger are necessary to fully understand the thermal mechanism. Obviously, for such strong and complex temperature variations on the blade, a pixel-by-pixel temperature correction on the PSP data was definitely necessary to obtain reasonable pressure results. The corresponding pressure fields (presented in pressure ratio P/P ref) measured by PSP after temperature correction are shown in Fig. 11. Generally, a streamwise pressure gradient existed on the blade with reduced pressure near the leading edge and increased pressure downstream due to compression. This streamwise pressure gradient increased with rotation speed, as expected. Also, a radial pressure gradient can be observed in all cases near the leading edge with the minimum pressure appeared at the tip. This is also reasonable considering that the relative flow velocity reached the maximum at the tip.
The instantaneous temperature fields on the TC1 compressor blade at n = 60,000 rpm with different flow rates are shown in Fig. 12. Significant variations in temperature field were observed as the flow rate was reduced from Q/Q ref = 1.44–0.59. The overall ΔT increased at lower Q probably because there was less fluid available to provide cooling for the blade. It was also interesting to find the competition between the compression effects and the aerodynamic heating effects. At the maximum flow rate (Q/Q ref = 1.44), the temperature field was dominated by the streamwise gradient and the radial gradient was only visible near the tip as shown in Fig. 12a. As the flow rate decreased, the radial gradient became stronger and was finally dominant at the minimum flow rate (Q/Q ref = 0.59). The corresponding pressure fields measured by PSP after temperature correction are shown in Fig. 13. The streamwise pressure gradients decreased slightly with the flow rate, which was consistent with the variation in total pressure ratio measured by the pressure sensors located at the inlet and the outlet of the compressor. The streamwise pressure distributions at the blade mid-span are also compared in Fig. 14a, b for different rotation speeds and flow rates, respectively. The results have basically confirmed the observations from the pressure contours as previously discussed.
4.2 The TC2 compressor
The instantaneous temperature fields on the TC2 compressor blade at three different rotation speeds are shown in Fig. 15. Note that the results of the minimum rotation speed were not included since both the temperature and pressure variations were rather indistinct. The general trend was very similar to the results of TC1 compressor but with less amount of temperature rise. At n = 60,000 rpm, the temperature field was fairly uniform with an overall ΔT of only 2.2 K. Both the streamwise and radial gradients started to show at higher speeds, but with less strength compared with TC1 compressor which was likely related to reduced compression/pressure ratio and aerodynamic heating. The maximum ΔT found on the blade at the highest speed (n = 150,000 rpm) was about 15 K. As shown in Fig. 16, the pressure fields also displayed similar trend as observed from the results of TC1. The streamwise pressure gradients increased with rotation speed, and the minimum pressure was again found near the tip at the leading edge.
4.3 Time-dependent temperature variations on the blade
The TC1 compressor was operated continuously for 10 min at n = 80,000 rpm and the blade temperature fields at the beginning and the end of the operation were compared in Fig. 17. The two contours show similar trends in both radial and streamwise directions, but there was a clear reduction in the overall temperature rise at the end of operation. The maximum ΔT on the blade dropped by as much as 4 K. The reason for this time-dependent temperature variation was currently unclear, which would be clarified by future studies including other components of the turbocharger. Unlike the temperature fields, the blade pressure fields at the beginning and the end of the operation were quite similar, as shown in Fig. 18. This is reasonable since both the rotation speed and the flow rate were kept constant. The time-dependent temperature field on the blade showed the importance of simultaneous PSP and TSP measurements. Due to the large temperature rise on the blade, any flow unsteadiness would cause temperature changes that could potentially lead to significant pressure errors if simultaneous measurements were unavailable. The PSP results in this case could also serve as validation for the temperature correction scheme.
4.4 Evaluation of measurement uncertainties
A major source of measurement uncertainty was the assumption of a constant lifetime for PSP and TSP during image deblurring. The spatial variations of lifetime were not considered in the current study, which could lead to measurement errors at high rotation speeds due to the significant variations of lifetime from strong pressure and temperature gradients on blade surface. For example, the lifetime values of TC1 at n = 60,000 rpm varied from 5 to 8 μs for PSP and from 5.6 to 6.2 μs for TSP. The ratio of ratios obtained using different lifetime values is compared in Fig. 19 to investigate this effect. The results are streamwise distributions taken from the blade mid-span and θ 0 indicates the angular range of one blade. The effect of lifetime variation is almost negligible except for the PSP case near the end of the blade (θ/θ 0 = 1) where a large gradient exits. However, this error increased significantly at higher rotation speed due to larger variation in lifetime values. At n = 80,000 rpm, τ varied from 3 to 7 μs for PSP and from 4.6 to 5.9 μs for TSP. Again, the ratio of ratios obtained using different lifetime values is compared in Fig. 20. Clear differences in the deblurred PSP and TSP results caused by lifetime variations are observed for over 20% of the blade near the end. This is actually not surprising considering the strong temperature and pressure gradients located in this region as shown in Figs. 10d and 11d, respectively. The errors in PSP are more significant due to larger variations in τ. According to the above evaluations, the accuracy of the current deblurring method is generally acceptable for rotation speed no more than 60,000 rpm. For higher rotation speeds, a more precise deblurring algorithm taking account of the lifetime variation effect is desired for improving the measurement accuracy.
Another possible error source was the non-uniform temperature distribution on the compressor, meaning that the temperature on each blade might not be exactly identical. This effect would generate pressure measurement errors since the temperature field used for correction of PSP data was not obtained from the same blade. In the current study, the temperature non-uniformity could not be examined directly since only one blade was painted with TSP. However, it is possible to evaluate this effect by comparing the measured pressure from two separate blades painted with PSP. The differences in pressure (averaged in spanwise) between separate blades of TC1 are shown in Fig. 21 for all four rotation speeds. The agreement between two blades is generally good for most part of the blade (first 80% from leading edge) where the differences are within 5% (within 3% for n ≤ 60,000 rpm). For the last 20% of the blade near the end, the pressure difference increases rapidly with rotation speeds, which is up to 10–20% at the maximum speed (n = 80,000 rpm). The large overall temperature rise (near 30 K) near the blade end at n = 80,000 rpm could potentially have temperature variations of a few Kelvin between different blades and lead to significant pressure errors in PSP measurement. This issue could be resolved with a hybrid PSP/TSP system that allows simultaneous measurement of pressure and temperature on the same blade (Peng et al. 2016).
5 Conclusions
The instantaneous pressure and temperature fields with high spatial resolution have been obtained using PSP and TSP on turbocharger compressor blades with rotation speeds up to 150,000 rpm. The current work is built on the existing single-shot lifetime-based technique and has successfully extended its applications to real turbomachinery experiments. The primary challenge here is the unsteady temperature fields which results in unpredictable temperature-induced errors in the PSP results. A combined PSP/TSP system has been developed which is able to perform simultaneous PSP and TSP measurement so that real-time temperature correction can be applied to the PSP results. A set of data processing procedures has also been developed to deal with other challenges such as the rotational image blur and large temperature variation/gradient. According to the PSP and TSP results, the pressure and temperature fields are quite complex with gradients in both streamwise and radial directions. The effects of rotation speed, flow rate and runtime on the pressure and temperature fields are clearly identified:
-
1.
the amount of temperature rise and the temperature gradients (both streamwise and radial) increases with rotation speed;
-
2.
both the streamwise and radial pressure gradients increase with rotation speed;
-
3.
the amount of temperature rise increases as flow rate reduces, the streamwise temperature gradient is dominant at high flow rates, and the radial gradient is dominant at low flow rates;
-
4.
the streamwise pressure gradient increases as flow rate reduces due to stronger compression (higher pressure ratio);
-
5.
the amount of temperature rise decreases with runtime, while the temperature and pressure gradients do not change with runtime.
In addition, the simultaneous measurements of PSP and TSP have been proved to be necessary due to the time-dependent variations in temperature field.
This lifetime-based PSP/TSP system has shown great potential for unsteady flow diagnostics in turbomachinery. However, the following two issues are to be resolved for improvement. The first issue is the thermal stability of both PSP and TSP in extreme test conditions. For example, the temperature within the turbocharger can easily reach 400 K if the combustion chamber is in operation for higher rotation speeds. Similar test conditions are also regularly encountered in other turbomachinary test facilities. It is currently unclear that if the paints (especially the PSP) can remain functional at such a high temperature. More work is required to study the paint performance at higher temperatures, and attempts should be made to further extend the temperature limit of both PSP and TSP. The second issue is the measurement errors caused by the assumption of constant lifetime during image deblurring. Since the lifetime variations are significant at sufficiently high rotation speeds due to large pressure and temperature gradients, a deblurring algorithm with spatial variant lifetime values is desired to improve the accuracy. In addition, CFD simulations will be performed on selected cases for validation of the experimental results and assessment of the performance of data processing algorithms.
Abbreviations
- I :
-
Intensity
- I 0 :
-
Intensity at the beginning of luminescent decay
- I 1 :
-
Intensity of gate 1
- I 2 :
-
Intensity of gate 2
- I PSP :
-
Intensity of PSP
- I PSP_ref :
-
Intensity of PSP at reference condition
- I TSP :
-
Intensity of TSP
- I TSP_ref :
-
Intensity of TSP at reference condition
- I ref :
-
Intensity at reference condition
- k :
-
Ratio of temperature sensitivity between PSP and TSP
- n :
-
Rotation speed
- P :
-
Pressure
- P ref :
-
Pressure at reference condition
- Q :
-
Flow rate
- Q ref :
-
Flow rate at reference condition
- T :
-
Temperature
- T ref :
-
Temperature at reference condition
- t :
-
Time
- V tip :
-
Compressor tip speed
- x :
-
Coordinate in streamwise direction
- ΔP :
-
Pressure difference on separate blades measured by PSP
- ΔT :
-
Temperature change
- Δt :
-
Time duration of image blur
- Δθ :
-
Angular displacement during image blur
- θ :
-
Circumferential angle
- θ 0 :
-
Circumferential angle range occupied by one blade
- τ :
-
Luminescent lifetime
- τ ref :
-
Luminescent lifetime at reference condition
- ω :
-
Angular velocity
References
Ainsworth RW, Miller RJ, Moss RW, Thorpe SJ (2000) Unsteady pressure measurement. Meas Sci Technol 11:1055–1076. doi:10.1088/0957-0233/11/7/319
Bencic TJ (1998) Rotating pressure and temperature measurements on scale-model fans using luminescent paints. In: 34th AIAA/ASME/SAE/ASEE joint propulsion conference and exhibit, AIAA 1998-3452
Burns S, Sullivan JP (1995) The use of pressure sensitive paints on rotating machinery. In: 16th international congress on instrumentation in aerospace simulation facilities
Disotell KJ, Peng D, Juliano TJ, Gregory JW, Crafton JW, Komerath NM (2014) Single-shot temperature- and pressure-sensitive paint measurements on an unsteady helicopter blade. Exp Fluids 55:1671. doi:10.1007/s00348-014-1671-2
Engler RH, Klein C, Trinks O (2000) Pressure sensitive paint systems for pressure distribution measurements in wind tunnels and turbomachines. Meas Sci Technol 11:1077–1085. doi:10.1088/0957-0233/11/7/320
Goss L, Jones G, Crafton J, Fonov S (2004) Temperature compensation in time-resolved pressure measurments. In: International symposium of flow visualization
Goss L, Jones G, Crafton J, Fonov S (2005) Temperature compensation for temporal (lifetime) pressure sensitive paint measurements. In: 43rd AIAA aerospace sciences meeting and exhibit, AIAA-2005-1027
Gregory JW (2004) Porous pressure-sensitive paint for measurement of unsteady pressures in turbomachinery. In: 42nd AIAA aerospace sciences meeting and exhibit, AIAA 2004-0294
Gregory JW, Asai K, Kameda M, Liu T, Sullivan JP (2008) A review of pressure-sensitive paint for high-speed and unsteady aerodynamics. Proc Inst Mech Eng G J Aerosp 222:249–290. doi:10.1243/09544100JAERO243
Gregory JW, Kumar P, Peng D, Fonov S, Crafton J, Liu T (2009) Integrated optical measurement techniques for investigations of fluid-structure interactions. In: 39th AIAA fluid dynamics conference, AIAA 2009-4044
Gregory JW, Sakaue H, Liu T, Sullivan JP (2014a) Fast pressure-sensitive paint for flow and acoustic diagnostics. Ann Rev Fluid Mech 56:303–330. doi:10.1146/annurev-fluid-010313-141304
Gregory JW, Disotell KJ, Peng D, Juliano TJ, Crafton J, Komerath NM (2014b) Inverse methods for deblurring pressure-sensitive paint images of rotating surfaces. AIAA J 52(9):2045–2061
Guizar-Sicairos M, Thurman ST, Fienup JR (2008) Efficient subpixel image registration algorithms. Opt Lett 33:156–158
Juliano TJ, Kumar P, Peng D, Gregory JW, Crafton J, Fonov S (2011) Single-shot, lifetime-based pressure-sensitive paint for rotating blades. Meas Sci Tech 22:085403. doi:10.1088/0957-0233/22/8/085403
Juliano TJ, Disotell KJ, Gregory JW, Crafton JW, Fonov SD (2012) Motion-deblurred, fast-response pressure-sensitive paint on a rotor in forward flight. Meas Sci Tech 23:045303. doi:10.1088/0957-0233/23/4/045303
Kameya T, Matsuda Y, Yamaguchi H, Egami Y, Niimi T (2011) Pressure-sensitive paint measurement on co-rotating disks in a hard disk drive. Opt Laser Eng. doi:10.1016/j.optlaseng.2011.06.022
Klein C, Henne U, Sachs W, Hock S, Falk N, Beifuss U, Ondrus V, Schaber S (2013) Pressure measurement on rotating propeller blades by means of the pressure-sensitive paint lifetime method. In: 51st AIAA aerospace sciences meeting, AIAA 2013-0483
Liu T, Sullivan JP (2005) Pressure and temperature sensitive paints. Springer, New York
Liu T, Torgerson S, Sullivan JP, Johnston R, Fleet S (1997) Rotor blade pressure measurement in a high speed axial compressor using pressure and temperature sensitive paints. In: 35th AIAA aerospace sciences meeting & exhibit, AIAA 1997-0162
Pandey A, Gregory JW (2016) Frequency-response characteristics of polymer/ceramic pressure-sensitive paint. AIAA J 54:174–185. doi:10.2514/1.J054166
Pastuhoff M, Tillmark N, Alfredsson PH (2016) Measuring surface pressure on rotating compressor blades using pressure sensitive paint. Sensors 16:344. doi:10.3390/s16030344
Peng D, Jensen CD, Juliano TJ, Gregory JW, Crafton J, Palluconi S, Liu T (2013) Temperature-compensated fast pressure-sensitive paint. AIAA J 51:2420–2431. doi:10.2514/1.J052318
Peng D, Jiao L, Liu Y (2016) Development of a grid PSP/TSP system for unsteady measurements on rotating surfaces. In: 32nd AIAA aerodynamic measurement technology and ground testing conference, AIAA 2016-3405
Ribarić S, Milani M, and Kalafatić Z (2000) Restoration of images blurred by circular motion. In: Proceedings of the 1st international workshop on image and signal processing and analysis
Sieverding CH, Arts T, Denos R, Brouckaert JF (2000) Measurement techniques for unsteady flows in turbomachines. Exp Fluids 28:285–321. doi:10.1007/s003480050390
Watkins AN, Leighty BD, Lipford WE, Wong OD, Oglesby DM, Ingram JL (2007) Development of a pressure sensitive paint system for measuring global surface pressures on rotorcraft blades. In: 22nd international congress on instrumentation in aerospace simulation facilities. doi:10.1109/ICIASF.2007.4380888
Watkins AN, Leighty BD, Lipford WE, Goodman KZ, Crafton J, Gregory JW (2016) Measuring surface pressures on rotor blades using pressure-sensitive paint. AIAA J 54:206–215. doi:10.2514/1.J054191
Wong OD, Watkins AN, Ingram JL (2005) Pressure-sensitive paint measurements on 15% scale rotor blades in Hover. In: 35th AIAA fluid dynamics conference and exhibit, AIAA 2005-5008
Wong OD, Noonan KW, Watkins AN, Jenkins LN, Yao C (2010) Non-intrusive measurements of a four-bladed rotor in hover—a first look. In: American helicopter society aeromechanics specialists’ conference
Yorita D, Asai K, Klein C, Henne U, Shaber S (2012) Transition detection on rotating propeller blades by means of temperature-sensitive paint. In: 50th AIAA aerospace sciences meeting, AIAA 2012-1187
Acknowledgements
This work was supported by funding from the IHI Corporation, the National Natural Science Foundation of China (NSFC No. 11502144) and the Gas Turbine Research Institute of Shanghai Jiao Tong University. The authors greatly appreciate the assistance from Mr. Chunhua Cao, Mr. Xinhua Cao and other staff members of WIT during the turbocharger tests.
Author information
Authors and Affiliations
Corresponding author
Rights and permissions
About this article
Cite this article
Peng, D., Jiao, L., Yu, Y. et al. Single-shot lifetime-based PSP and TSP measurements on turbocharger compressor blades. Exp Fluids 58, 127 (2017). https://doi.org/10.1007/s00348-017-2416-9
Received:
Revised:
Accepted:
Published:
DOI: https://doi.org/10.1007/s00348-017-2416-9