Abstract
Today electronic devices require a power supply without any variation or disturbance. Nevertheless, electrical variations presented in power lines are more frequent and powerful. The consequences of poor power quality are reflected in the lifetime and performance of electronic devices. Thus, in this study, an FMEA is presented to know which electrical variation has more effect on the reliability of electronic devices. The analysis was performed following the classification of electrical disturbances which consider the waveform of the disturbance. The results of the FMEA showed that electrical harmonics have more influence to harm an electronic device. In addition, a reliability analysis is performed in this study to measure the effects of the electrical variation via mean time to failure. The electronic product selected was a laptop computer. The results of the reliability analysis showed that laptop computer reduced its lifetime in around 4800 h under the electrical variation selected.
Similar content being viewed by others
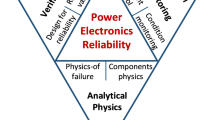
Avoid common mistakes on your manuscript.
1 Introduction
Power quality (PQ) has become an important topic for the industry and consumers. Nowadays, electronic devices (non-linear loads) are more sensitive to electrical variations (EVs) existing in the power line (PL). PQ issues are primarily due to continually increasing sources of disturbances that occur in interconnected power grids, which contain a large number of power sources, transmission lines, transformers, and loads. Such systems are exposed to environmental disturbances such as lightning strikes. Furthermore, non-linear power electronic loads, for example, a converter driver equipment, have become increasingly common in the power system [1]. The lack of PQ is directly reflected in the reliability of the electronic device, which uses the voltage lines for its operation. In consequence, it is necessary to know which disturbance presented in the PL produces the higher damage in the piece to get a better reliability assessment when electronic devices are in real operational environments. PQ issues and PQ classification have been investigated by many authors. Saini [1] made a review of PQ classification via signal processing techniques, such as fuzzy logic, neural network, and genetic algorithm. Dash et al. [2] used a fast Modified recursive Gauss–Newton method for the estimation of PQ indices in distributed generating systems during both islanding and non-islanding conditions. Naik and Kundu [3] established PQ indexes based on discrete wavelet transform (DTW) to determine the amount of deviation from the desired pure signal, and the recommended PQ index is defined as the weighted sum of the percentage energy deviation of the DWT details. Geun-Joon et al. [4] focus on voltage sag phenomena and their impact on customer satisfaction, to derive a unique power quality of service index, information from both the supply network (according to standards in use) and the customer (defined in terms of load sensitivity and interruption cost) are merged. Biswal and Dash [5] proposed a fast adaptive discrete generalized S-transform algorithm based on a new frequency scaling named selective frequency scaling, window cropping, and an adaptive window function. Ozgonenela et al. [6] investigated ensemble empirical mode decomposition performance and compared it with classical empirical mode decomposition for feature vector extraction and selection of power quality disturbances. Another index is proposed by Duarte and Kagan [7] using the voltage and the harmonic distortion. Finally, Dehghania et al. [8] proposed a new classification using the hidden Markov model (HMM) and wavelet transform (WT). In this work, 15 different types of power quality disturbances were considered for training and evaluating the proposed method. The Dempster–Shafer algorithm was employed for improving the accuracy of classification.
The reviewed papers mentioned above only classify the EV. However, those works cannot identify which variation has more probability to damage the device when it is plugged in the PL, in that case, Mendez et al. [9] established the importance to know which EV affects directly the lifetime of electronic devices and the significance to analyze the PQ issues using reliability techniques. The main objective of this study is to obtain the risk priority number (RPN) indexes of PQ variations presented in the PL via failure mode and effect analysis (FMEA); in this case, we consider the classification established by Seymour [10]. With the highest RPN index, we proposed a reliability analysis to measure the effect of the EV into the electronic device. The results presented in this paper offer a better way to understand which EV has more probability to harming the electronic device. Moreover, we proposed a technique to analyze the effect of the EV into electronic products via a reliability analysis.
This study is arranged as follows: the classifications of EV presented in the PL is described in Sect. 2. The FMEA analysis performed to the classification presented by Seymour [10] is presented in Sect. 3. Reliability approach and their procedure are described in Sect. 4. A case of study performed includes a reliability analysis between constant voltage (actual procedure), and the EV with the highest RPN is described in Sect. 5. Section 6 establishes the results and the effects of the EV into the device. Finally, the last section provides the concluding remarks and a future work which can derivate from this paper.
2 Types of electrical variations
There are different classifications for PQ issues; each classification uses a specific property to categorize the problem. Some of them classify the events as “steady state” and ‘non-steady state” phenomena. In some regulations (e.g., ANSI C84.1), the most important factor is the duration of the event, see Table 1. Other guidelines (e.g., IEEE-519) use the wave shape (duration and magnitude) of each event to classify power quality problems. Other standards (e.g., IEC) use the frequency range of the event for the classification.
Seymour [10] has established seven categories of EL based on wave shape form produced by the EL, and these disturbances are described in Table 2.
3 FMEA of electrical variations
The American Society of Quality (ASQ) defines an FMEA as a step-by-step approach for identifying all possible failures in a design, a manufacturing or assembly process, or a product or service. The main objective of FMEA is to assign an RPN; this numerical value is associated with the causing failure, severity, occurrence, and detection.
The RPN value is obtained as follow:
Severity refers to the magnitude of the end effect of a system failure. The more severe of the consequence, the higher value of severity will be assigned to the effect. Occurrence refers to the frequency that a root cause is likely to occur, described in a qualitative way. That is not in the form of a period of time but rather in terms such as remote or occasional. Detection refers to the likelihood of detecting that a root cause before a failure can occur Arabian-Hoseynabadia et al. [11]. For this case, we established a relationship between electrical variations presented in Table 1 and reliability techniques to get the factors described in Eq. (1).
3.1 Preliminary for FMEA
The severity, occurrence, and detection factors are individually rated using a numerical scale, typically ranging are from 1 to 10. These scales, however, can vary in range depending on the FMEA standard being applied. However, for all standards, a high value represents a poor score (for example, catastrophically severe, very regular occurrence or impossible to detect). Once a standard is selected, it must be used throughout the FMEA [11].
In this study, we use the procedure proposed by Arabian-Hoseynabadia et al. [11] and modify the scale of severity, occurrence, and detection to do more appropriated for the application EV shown in Table 2.
The severity modified scale and criteria are shown in Table 3. This table was developed via reliability tools such as mean time to failure (MTTF), which measure the average lifetime, inverse power law (IPL) that is the common model to analyze electronic devices.
The occurrence modified scale and criteria are shown in Table 4. This table was developed via the magnitude of the EL presented by Funch and Mohammad [12] and classification provided by MIL-STD-1629A [13].
The number of detection levels was reduced by removing 1, 6–10, as the presence of the remaining four levels was adequate for this analysis. The modified Detection scale and criteria are shown in Table 5. Table 5 was based on the PQ existing technology and their capacity to detect and suppress the electrical variation when the electronic devices is plugged in PL.
Defining the criteria tables is the first step in performing an FMEA. Arabian-Hoseynabadia et al. [11] mentioned the basic principles of an FMEA using different standards that are similar and simple:
-
The system to be studied must be broken down into its assemblies.
-
For each assembly, all possible failure mode must be determined.
-
The root causes of each failure mode must be determined for each assembly.
-
The end effects of each failure mode must be assigned a level of severity, and every root cause must be assigned a level of occurrence and detection via Tables 3, 4, and 5.
-
The RPN is calculated via Eq. (1).
In the following section, the procedure of the FMEA is established and how the RPN and which electrical variation has more effect into electronic devices.
3.2 FMEA procedure
The first step to develop the FMEA is to define the criteria in the analysis. These criteria were performed in Tables 2, 3, and 4. The second step is making a subdivision of the system; in this case, we perform an FMEA for EV. The EV was classified and described in Table 2.
For each EV, we determinate the possible failure mode produced when an electronic device is plugged on to the PL; for this case, we consider information provided by Seymour [10], Funch and Mohammad [12], Kennedy [14] and Dah and Luc [15].
In addition, in this case, we consider the effects of EV in the product’s reliability. A summary of failure modes generated by EV into electronic devices is shown in Table 6.
The root cause of each failure mode is established in Table 7; the root cause was related to the sources of the EV presented in the PL.
Based on Tables 2, 6, and 7, we set on the severity, occurrence, and detection ranking following the criteria established in Tables 3, 4, and 5. In this step, is included a liability approach to determinate the ranking of each FMEA criteria for all EV. The reliability approach proposed was established in the failure rate of the electronic device when the EV is submitted into the piece, and this concept is added, as shown in Table 3. In addition, we consider if the EV presented in the power line can be implemented in the reliability models, such as inverse power law (is the common life-stress relationship to describe the performance of electronic devices when the voltage is submitted into the piece), and this concept is applied in the detection rank (presented in Table 4). The severity, occurrence and detection ranking and RPN for EV is shown in Table 8.
The results presented in the Table 8 offer a good perspective to know which EV has the highest probability to damage the electronic device when is plugged on the PL. Based on Table 7, the EV with the highest RPN was electrical harmonics (EH). EH are steady-state phenomena, so they are present all the time in the sinusoidal waveform in the PL. Moreover, in the Table 7, impulsive and oscillatory disturbance has a big change to reduce the reliability of the electronic product. Impulsive and oscillatory disturbances are caused by weather conditions such as thunderstorms.
In the following section, a reliability methodology is applied to measure the performance and the lifetime of electronic products under the EV with the highest RPN. The device selected for the analysis was a commonly residential product (laptop computer).
4 Reliability approach
A reliability prospective is proposed in this section; this approach is to know the effect of the EV into electronic devices and to have a numerical result of the impact. The analysis was performed via EH, which has the highest RPN value in the FMEA made in Sect. 3.
4.1 Preliminary for reliability approach
To know the performance and lifetime of any product in reliability, a life-stress relationship is employed. The life-stress relationship is constituted by these concepts:
-
1.
a physical model that describes the behavior of the product under the stress factor;
-
2.
a probability distribution that describes the behavior of products under applied stress.
Based on the concepts established above, voltage is commonly used as a stress factor to know the performance and lifetime of electronic devices. The physical model, which describes the performance of the electronic product under voltage stress, is inverse power law (IPL), and it is defined as:
The Weibull distribution is commonly used to describe the behavior of failure times of electronic devices [16], so recalling the Weibull distribution and expressed as in Eq. (2), the following is obtained:
where \(\beta \) represents the shape parameter (that involves the Weibull distribution), K is a characteristic parameter for each device under analysis, n expresses the acceleration factor and represents how the applied stress harms the device, and V represents the voltage level submitted into the piece. Other important equations in reliability analysis are reliability function \(\left( {R\left( t\right) } \right) \) which establishes the probability to survive of the product under the stress applied and Hazard Function \(\left( {H\left( t \right) } \right) \). Based on Eq. (3), the \(R\left( t \right) \) and \(H\left( t \right) \) equations are defined as:
The principal assumption in Eq. (3) is that the level of stress V needs to be constant during the experimentation procedure, and that the level of stress V represents an issue in the life-stress relationship presented in Eq. (3), because IPL does not the ability to analyze the EV presented in the PL, that is EV is a time-varying stress. To solve this problem, it is necessary to modify Eq. (2) via the cumulative damage model (CDM). CDM takes into account the cumulative effect of the applied stresses in the piece. Therefore, based on CDM theory and applying it into the IPL model shown in Eq. (2), considering \(\alpha =\frac{1}{k}\) in IPL model and given a time-varying stress \(x\left( t \right) \), the IPL model for CDM is written as:
Rewriting Eq. (6) in terms of Weibull distribution, we have the following:
where
Nevertheless, the model obtained in Eq. (7) does not take in consideration the cumulative damage presented in the piece when it is under the time-varying voltage. Nelson [17] establishes that when the stress \(V\left( t \right) \) is a function of time; the distribution scale parameter \(\beta \left( {V,x} \right) \) is a function of time, namely, \(\beta \left( t \right) =\beta \left( {V\left( t \right) ,x} \right) \). The corresponding cumulative exposure \(\epsilon (t)\) becomes the integral:
Substituting Eq. (8) into Eq. (7), and changing the variable t for v, we obtain:
where
Equations (3) and (8) represent the probability density function (PDF) for constant voltage and time-varying voltage scenario, respectively, and the PDF describes the behavior of the product undervoltage scenario. Examples of reliability testing using Eqs. (2), (3), and (9) can be found in [9, 16–19].
R(t) and h(t) for Eq. (8) is defined as:
4.2 Selection of time-varying equation
For the time-varying scenario, it is necessary to find an equation, which describes this scenario. EH are expressed by the Fourier series and is defined by:
By setting
Substituting Eq. (13) in Eq. (12), we obtain:
In Eq. (13), \(C_0 \) represents the amplitude of the fundamental signal. \(C_n \) is the amplitude of the harmonic. \(\omega _n \) is the frequency of the harmonic. \(\theta _n \) is the phase of the harmonic. Eq. (13) represents the compact form of Fourier series; this representation is widely used to know the magnitude and the phase of the harmonics into a power line.
Since Eq. (14) represents an infinite term, it is necessary to know which EH appears frequently, and Schneider Electrics [17] established that harmonics 3, 5, 7, 11, and 13 have a negative impact into any electrical and electronic device. Therefore, if the Eq. (13) is established in terms of the harmonics 3, 5, 7, 11, and 13, and their frequencies (\(\omega _n\)) (Consider a fundamental frequency as 60 Hz, so the harmonics will be in multiples of 60 Hz). In addition, as established, only single-phase loads were considered that means the term \(\theta _n =0\) Eq. (14) is now written as:
Equation (14) represents the equation that defines the EV in the time, and that can be used in the reliability analysis performed by Eq. (9).
5 Illustrative example
To obtain the lifetime of the laptop computer under constant stress and time-varying stress scenario, an accelerated life testing (ALT) was performed. The procedure of ALT experiment was as follows:
-
1.
Devices under analysis are single-phase loads.
-
2.
The technical specifications of the laptop computer were 15.6\(\mathrm {''}\) of screen, 120 VAC, 60 Hz, 2.5 GB of Processor. 750 GB of HD.
-
3.
Two different reliability analyses were performed in this example with different voltage scenarios. In the first experiment, the voltage levels remain constant in the ALT. The second scenario was performed with time-varying voltage induced by EH, the EH were submitted in the ALT via the Eq. (15)
-
4.
For both voltage scenarios, 20 pieces were under analysis. In addition, three levels of voltage stress for constant voltage scenario were selected. The stress levels were established via Optimum Test Plans for ALT proposed by Nelson [17]. The levels selected for both experiments were 150, 185, and 210 VAC, and the distribution of the pieces under each stress was 12 pieces under 150 VAC, 5 pieces under 180 VAC, and 3 pieces under 210 VAC. In the scenario of time-varying voltage, the value of the term in Eq. (15) \(C_0 \) took the value of the level stress established on constant scenario (150, 185, and 210). The value of \(C_n \) was selected randomly via a Monte Carlo algorithm and following the IEEE-519 (1992). The IEEE norm establishes that harmonics cannot exceed 20 % of \(C_0 \).
-
5.
To obtain the lifetime of each laptop computer, we use a National Instruments DAQ NI 6343 and Labview\(^\mathrm{TM}\) to control each experiment and to record the lifetime of each device under experiment.
-
6.
All parameter estimation for both scenarios were performed via maximum likelihood estimator (MLE).
-
7.
No censored data were obtained in both voltage scenarios.
5.1 Case of study for constant voltage scenario
The results of the failure time obtained from the ALT performed to the laptop computer under constant voltage stress can be seen in Table 9. In addition, Fig. 1 shows a diagram of the experiment made in this case of study to obtain the lifetime of Table 9. Failures considered in the device were the following: AC/DC conversion fault, malfunction in the motherboard, failure of cooling system, hard drive failure (loss of data), and processor breakdown.
Based on Table 9, the parameters \(\left( {\beta , K~\mathrm{and}~n} \right) \) established on Eq. (3) can be estimated via MLE. To do that, it is necessary to obtain the log-likelihood function. Therefore, based on Eq. (4), the log-likelihood function is obtained as follows:
where \(F_e \) is the number of the groups of exact time to failure data points. \(N_i \) is the number of the times to failure in the \(i{\mathrm{th}}\) time to failure group data. \(V_i \) is the stress level of the \(i{\mathrm{th}}\) group. \(\beta \), K, and n are the IPL-Weibull parameters to be estimated. \(T_i \) is the exact failure time of the \(i^{th}\) group.
Therefore, based on Eq. (16) and Table 9, the estimation of parameters \(\beta \), K and n via Newton-Raphson approximation were:
With values obtained in (17), it is possible to describe performance and calculate the mean time between failures (MTBF). To calculate the performance, it is necessary to drawn by setting the time “t” from 0 to infinity in \(R\left( t \right) \) and \(H\left( t \right) \) obtained from Eq. (3) and by setting the results obtained in (17). The results can be appreciated in Fig. 2.
The MTTF, which determine the mean life of the device. Based on Reliasoft [18], \(\mathrm{MTTF}=\frac{1}{KV^{n}}\cdot \Gamma \left( {\frac{1}{\beta }+1} \right) \). Thus, using the result obtained in (17), the MTTF of the laptop computer under constant voltage for this experiment and the 95 % confidence bounds are:
5.2 Case of study with EH submitted
In this experiment, a time-varying voltage was submitted into the laptop computer to know the effects of harmonics in the device. As established in Sect. 4.2, the amplitude of each harmonic was determined via Monte Carlo algorithm. The experiment followed the IEEE-519 (1992) standard and only the harmonics in order of 3, 5, 7, 11, and 13 (see Eq. 15) were considered, that harmonics were added to the fundamental signal, and the values of fundamental signal were 150 VAC, 180 VAC, and 210 VAC. To produce the EV, we used the CE-Test system. The values generated of each harmonic via Monte Carlo algorithm and the CE-Test system can be seen in Table 10. In addition, Fig. 3 shows show a diagram of the experimental procedure when are submitted in the laptop computer.
In Table 11, the failure time of the device under the EH submitted is presented, and in parenthesis, is the calculated percentage of total harmonic distortion (THD) for each piece under analysis is presented. Failures considered in the device were the following: AC/DC conversion fault, malfunction in the motherboard, software boot loader, failure of cooler system, hard drive failure (loss of data), and processor breakdown.
To calculate the behavior of the laptop computer under EH, we use Eq. (9), and as the same procedure that constant voltage scenario, to calculate the parameters \(\beta \), a, and k it is necessary to obtain the log-likelihood function. Therefore, based on Eq. (9), the log-likelihood function is obtained as follows:
where \(F_e \) is the number of the groups of exact time to failure data points. \(x\left( t \right) \) is the stress profile function. \(\beta \), a and k are the IPL-Weibull in time-varying voltage parameters to be estimated. \(T_i\) is the exact failure time of the \(i{\mathrm{th}}\) group.
Therefore, based on Eq. (19) and Table 11, the estimation of parameters \(\beta \), K, and n via Newton-Raphson approximation was:
Using the same procedure established in Sect. 5.1, the performance of the device under analysis can be found via \(R\left( t \right) \) and \(H\left( t \right) \). To draw the performance of reliability and failure rate, it is necessary to determine the values of EH of Eq. (15) when the device is under normal operation environment. To obtain the EH under normal environment, we perform that a serial of 1000 measurements with FLUKE\({{\circledR }}\) 43B and the average magnitude of harmonics 3, 5, 7, 11 and 13 were recorded, and the results are shown in Table 12.
By subtitling the values obtained in Table 12 in Eq. (15), and by setting the values obtained in 20 in the Eqs. (10) and (11), the performance of the piece can be drawn, and the results can be appreciated in Fig. 4.
To determine the MTTF of the laptop computer under EH can be calculated as \(\mathrm{MTTF}\left( {x\left( t \right) } \right) =\mathop \smallint \nolimits _0^t t\cdot \left[ \left\{ E\left( {t,x} \right) \cdot \right. \right. \left. \left. \left[ {I\left( {t,x} \right) } \right] ^{\beta -1} \right\} e^{-I\left( {t,x} \right) } \right] dt\). Thus, using Eq. (15) for \(x\left( t \right) \) and the values obtained in Table 12, and the results obtained in (20), the MTTF of laptop computer under electrical harmonics with 95 % confidence bounds is:
6 Discussion
The results acquired in Sects. 5.1 and 5.2 can be explained in two parts. The first part is related to values obtained for the parameters of models presented in Eq. (3) and Eq. (9). The physical interpretation of each parameter is the following: Beta (\(\upbeta \)) describes the behavior of failure times; in both cases, the failure rate increases with time and is exhibiting a wear-out type failure. In Figs. 2b and 4b, the wear-out process for each process can be appreciated. In the case of constant voltage (Fig. 2b) reached a maximum failure rate when the piece has around 48,000 h, when electrical harmonics are submitted in the piece, the maximum failure rate is reached when the piece has worked 19,800 h, which means that the wear-out process under electrical harmonics is more accelerated than constant voltage.
Parameters “K” and “\(\alpha \)” are related to IPL model, and both parameters are allied to internal components of the electronic device. In this case, the elements, such as hard drive (HD), AC power converter, and motherboard, are related to the parameters “K” and “\(\alpha \)”. When “K” or “\(\alpha \)” have a high value in the model means a high probability to harm the internal component of the device. Hence, the components of laptop have more damage when are submitted in time-varying scenario produced by electrical harmonics (\(\alpha =1303.808\)) in comparison of constant voltage where parameter (\({K}=5.182\,E{-}12\)).
Parameter “n” measures the effect of the voltage into the piece, for the electrical harmonics case \({n}=4.2553\) and for constant voltage is \({n}=3.252\), which means that the electrical harmonics have more effect in the laptop when harmonics are presented in PL.
Differences among parameters (\(\upbeta , a, k\), and n) affect directly the life estimation and guarantee time. In the case of the laptop computer and based on MTFF (values obtained in (18) and (21)), the lifetime of the laptop computer under electrical harmonics is reduced in over 4800 h in comparison to constant voltage. Figure 5 shows the location of the failures presented in the laptop computer on constant voltage and time-varying voltage produced by electrical harmonics
Based on Fig. 5, both voltage scenarios AC/DC transformer have the major effect of the voltage, and that issue is transferred to the performance of laptop computer. Another important topic is the temperature generated by the laptop, when the laptop is operated under ALT with EH, the temperature in its motherboard increased because the failures in the cooling system increased in comparison of constant voltage that also, reduced the performance, and affected directly the HD and the software system.
7 Concluding remarks and future scope
In this study, an FMEA was performed to know which EV presented in the PL affects directly the lifetime and performance of electronic devices. The classification of EV employed in this study was the waveform produced by the EV in the lines. The FMEA scale of severity, occurrence, and detection was modified to make it suitable for EV presented in Table 2. The results of the FMEA showed that electrical harmonics have more probability to damage the electronic devices, reduce their lifetime, and affects directly the performance. In addition, the FMEA offers a new perspective to know which electrical variation has the biggest probability to damage the electronic device.
A reliability approach was performed to measure the effects of the EV with the highest RPN; the device selected for this analysis was a laptop computer. The study compares the MTTF when the voltage is constant, and time-varying voltage produced by the electrical harmonics. The models employed in reliability analysis were the IPL for constant voltage scenario and CDM for electrical harmonics scenario. The results of the study showed that laptop computers reduce their lifetime in around 4800 h based on MTTF when electrical harmonics is presented in the PL.
The proposed method offers a better way to understand the electronic device’s behavior exposed under real voltage environments and to know which EV has a more probability to damage the device. Time-varying scenarios (such as electrical harmonics) into the reliability analysis can offer better information than traditional models, and this information could be useful to improve the quality of the electronic device.
A future work in this field is analyzing the classification presented in Table 2 using techniques, such as root cause analysis (RCA) and hazard and operability study (HAZOP), even a comparative study between techniques can be do to get more accuracy in the calculation of which EV can be more probable to damage an electronic device.
References
Saini MK (2012) Classification of power quality events—a review. Int J Electr Power Energy Syst 43(1):1–19
Dasha PK, Padheea M, Barikb SK (2012) Estimation of power quality indices in distributed generation systems during power islanding conditions. Int J Electr Power Energy Syst 36(1):18–30
Naik CA, Kundu P (2013) Power quality index based on discrete wavelet transform. Int J Electr Power Energy Syst 43:994–1002
Lee G-J, Albu MM (2004) A power quality index based on equipment sensitivity, cost, and network vulnerability. IEEE Trans Power Deliv 19(3):1504–1510
Biswal M, Dash PK (2012) Estimation of time-varying power quality indices with an adaptive window-based fast generalised S-transform. Sci Meas. Technol IET 6(4):189–197
Okan O, Turgay Y, Irfan G, Unal K (2013) A new classification for power quality events in distribution systems. Electric Power Syst Res 95:192–199
Duarte SX, Kagan N (2010) A power-quality index to assess the impact of voltage harmonic distortions and unbalance to three-phase induction motors. IEEE Trans Power Deliv 25(3):1846–1854
Dehghania H, Vahidia B, Naghizadehb RA, Hosseiniana SH (2013) Power quality disturbance classification using a statistical and wavelet-based Hidden Markov Model with Dempster-Shafer algorithm. Int J Electr Power Energy Syst 47(1):368–377
Mendez-Gonzalez LC, Rodríguez-Borbón MI, Piña-Monarrez MR, Ambrosio R, del Valle A (2016) Reliability analysis for laptop computer under electrical harmonics. Qual. Reliab. Eng. Int. doi:10.1002/qre.1979
Seymour J (2006) The seven types of power problems. Schneider Electric-Data Cencer Science Center, Rueil-Malmaison, France
Arabian-Hoseynabadia H, Oraeea H, Tavnerb PJ (2010) Failure Modes and Effects Analysis (FMEA) for wind turbines. Int J Electr Power Energy Syst 32(7):817–824
Fuchs EF, Masoum MAS (2008) Power quality in power systems and electrical machines. Associate Press, Perth
MIL-STD-1629A. Procedures for performing a failure mode, effects and criticality analysis. Department of Defense, USA (24 Nov 1980)
Kennedy B (2000) Power quality primer. McGraw-Hill Companies, New York. doi:10.1036/0071344160
Dah D, Lu C (2013) An update on power quality. Croatia. doi:10.5772/51135 (InTech)
Meeker W, Escobar L (1998) Statistical method for reliability data. John Wiley & Sons, Inc., New York
Nelson W (1990) Accelerated testing: statistical models, test plans and data analysis, vol 507. John Wiley & Sons, inc., publication, New York
Reliasoft (2013) Accelerated life testing reference, chap 12. Reliasoft Publishing, Tucson, p 266
Méndez González LC, Rodríguez Borbón MI, Valles-Rosales DJ, Del Valle A, Rodriguez A (2016) Reliability model for electronic devices under time varying voltage. Qual. Reliab. Eng. Int. 32:1295–1306. doi:10.1002/qre.1867
Author information
Authors and Affiliations
Corresponding author
Rights and permissions
About this article
Cite this article
Méndez-González, L.C., Ambrosio-Lazaro, R., Rodríguez-Borbon, I. et al. Failure mode and effects analysis of power quality issues and their influence in the reliability of electronic products. Electr Eng 99, 93–105 (2017). https://doi.org/10.1007/s00202-016-0399-9
Received:
Accepted:
Published:
Issue Date:
DOI: https://doi.org/10.1007/s00202-016-0399-9