Abstract
Carbon fiber–reinforced polymer (CFRP) composites are widely utilized in the aerospace industry due to their exceptional mechanical properties. In this paper, a regular dodecagon trajectory side milling method was employed to investigate the high-speed cutting performance of CFRP, focusing on the impact of fiber cutting angle, up milling and down milling, processing parameters, and cooling conditions on the cutting characteristics. Results indicate that utilizing the Gr-NMQL cutting lubrication method can significantly improve machining surface quality while reducing cutting force by up to 15%. Additionally, using a PCD burr milling cutter, the normal and tangential cutting forces followed a particular trend: 60° > 30° > 90° > 0° > 150° > 120°. Moreover, when the cutting speed exceeded 200m/min, both normal and tangential cutting forces showed a significant decrease. Cutting along the fiber direction yielded superior machining quality compared to it, and the optimal surface roughness was achieved when cutting along the 90° direction. Finally, a comparative study of up milling and down milling revealed that implementing the up milling process improved both cutting force and surface quality. These findings contribute to a deeper understanding of the high-speed milling performance of CFRP and provide insights for optimizing the machining process.
Similar content being viewed by others
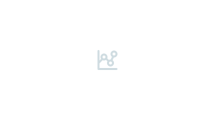
Explore related subjects
Discover the latest articles, news and stories from top researchers in related subjects.Avoid common mistakes on your manuscript.
1 Introduction
CFRP composites are known for their exceptional properties, including high specific strength, high specific modulus, fatigue resistance, and corrosion resistance [1,2,3]. As a result, these composites have found widespread use in various manufacturing fields, such as transportation, aerospace, new types of weapons and equipment, and high-precision machining [4,5,6]. While CFRP components are typically manufactured using “near-net-shape” processes, secondary mechanical processing is often necessary to meet subsequent connection and assembly requirements [7]. Among the commonly used processing methods for CFRP, milling stands out as a popular option [8].
CFRP has gained significant attention as a lightweight and high-strength material in various engineering applications. However, the complex structure of CFRP, which consists of high-strength fiber phase and low-strength resin phase, as well as the interface phase, leads to unfavorable machining characteristics [9,10,11]. During the milling process, the alternating action of the tool and the various phases of the material easily generate machining defects such as burrs, delamination, and pits [12,13,14,15]. These defects directly result in poor machining surface quality, which severely limits the engineering applications of CFRP. Therefore, it is essential to address the urgent tasks of improving machining quality and reducing cutting force, which are the root cause of various physical phenomena in the material cutting process.
In recent years, extensive research has been conducted worldwide to improve the mechanical machining of CFRP. Scholars have carried out experimental studies to analyze the CFRP machining process. Geier [16] studied the impact of fiber cutting angles on cutting forces and developed a multi-order polynomial model to predict cutting forces. Oguz et al. [17] analyzed the cutting force characteristics and machining surface morphology during CFRP milling processes. WU et al. [18] revealed the influence of different fiber orientations on wear mechanisms and tool wear evolution, while Madhavan et al. [19] studied the relationship between cutting forces, chip morphology, fiber cutting angles, and feed rates. Konstantin et al. [20] discussed the impact of cutting edge radius on cutting forces during CFRP cutting processes and proposed a novel method for preparing cutting edges. Wang et al. [21] found that surface pits were the primary machining surface damage in orthogonal milling tests of unidirectional CFRP laminates, and they proposed a milling strategy that considers fiber cutting angles. Nor et al. [22] found that ultrasonic-assisted milling can help reduce cutting forces and machining temperatures but is not conducive to improving surface quality. Mishra et al. [23] deals with hybrid manufacturing of microstructured objects that are first 3D printed, and then, the surface finish is finalized by machining. The orientation of the internal fibers is also important for the machining performance.
In terms of simulation and modeling, Cepero et al. [24] and Song et al. [25] proposed finite element simulation methods and analytical prediction models for CFRP machining processes and chip formation mechanisms, respectively, to investigate the influence of fiber orientation on chip formation. Seeholzer et al. [26] proposed an analytical prediction method for drilling unidirectional CFRP cutting forces by considering material properties, process parameters, and fiber cutting angles. To predict the cutting force in CFRP milling processes, DUAN et al. [27] and Yan et al. [28] studied the effects of cutting speed, feed rate, milling width, and fiber orientation on cutting force through finite element modeling and orthogonal milling tests. Han et al. [29] investigated the material removal mechanism of unidirectional CFRP at different temperatures, while Liu et al. [30] established fracture mechanism evolution models for unidirectional and multidirectional CFRP. Xiao et al. [31] and Ning et al. [32] used analytical methods to establish cutting force prediction models for multidirectional CFRP laminates, and Zhang et al. [33] theoretically analyzed the effect of machining inclination angle on burr damage to improve the surface quality of bent CFRP components.
According to the literature analysis, the fiber cutting angle is a crucial factor affecting machining performance, but there is currently no established systematic theoretical method. Current research has focused mainly on experimental characterization, surface damage analysis, and numerical simulation of CFRP machining processes, with little emphasis on up milling and down milling comparisons. This paper proposes a method of side milling with the PCD burr end mill and a special regular dodecagon trajectory to accurately measure cutting forces during the milling of unidirectional CFRP specimens. A comparative analysis of the factors influencing cutting forces in up milling and down milling processes is conducted to reveal the influence mechanism of cutting forces in high-speed milling of CFRP. Additionally, the impact of cooling methods on cutting forces and tool life is investigated.
2 Experimental principles and testing method
2.1 Materials and specimens for machining experiments
CFRP structures used in the field of aerospace engineering often incorporate complex fiber weaves to meet the unique requirements of engineering mechanics in various directions. The cutting angle of fibers is critical to machining performance, and its effects have been studied by segmenting the cutting angles. Decoupling of the complex fiber weave structure is necessary to investigate the mechanism of the cutting angle’s impact on cutting forces. Unidirectional CFRP materials serve as an ideal composite model for studying the mechanical machining properties of anisotropic materials, as they avoid the problems associated with complex interfaces and fiber directionality in multidirectional weaving.
Carbon fiber is known for its exceptional blend of high tensile strength and lightweight properties, which greatly contribute to aircraft structural lightweighting, and the practical suitability of T300 carbon fiber has been substantiated through empirical validation [34]. This paper presents milling experiments using unidirectional CFRP composite materials (provided by the Beijing Institute of Aeronautical Materials), with carbon fibers (T300-3K) as the reinforcing phase. The mechanical performance parameters of the carbon fibers are shown in Table 1.
Traditional experimental methods typically require the preparation of multiple experimental blocks with varying quantities and fiber angles, which can result in a complex sample preparation process and a tedious experimental process. Moreover, the traditional experimental process involves repeated positioning, clamping, tool setting, and cutting to complete tests at various angles, which can introduce various sources of interference and lead to large human errors and fluctuations in experimental data, making experimental analysis difficult. This paper presents a method for improving the accuracy of multi-angle cutting experiments on carbon fiber composite materials. Figure 1 illustrates the schematic of the side milling test for the regular dodecagonal specimen used in this study.
In the experimental process, the carbon fiber composite material was first machined into a plate-like specimen with a regular dodecagonal cross-section, with a locating hole in the center. The specimen was fixed to the force measuring device of the CNC machine through the locating hole. Next, the machining path and parameters were set in the CNC program. The cutting process was performed along the outline of the plate-like specimen using a milling cutter, and the complete cutting force signals were recorded using the force measuring device during the milling process. Besides, in the milling process, an arc-type tool path method is employed for each cutting path.
During the experiment, the milling cutter was used to mill each edge of the regular dodecagon specimen. This allowed for the measurement of cutting forces for typical cutting angles with a 30° incremental change, while preserving surface information for accurate surface quality testing in subsequent analyses. Although circular specimens can cover all cutting angles, the sharp change in fiber cutting angles during milling leads to abrupt changes in cutting force signals, which is not conducive to accurate analysis. Compared to circular specimens, the regular dodecagon milling test method maintains a longer stable cutting path for specific angles, generating stable cutting force signals for accurate testing and analysis. Moreover, the implementation of the arc entry and exit tool strategy not only ensures cutting process stability but also results in distinct boundaries for cutting force signals at various fiber cutting angles. This facilitates a more accurate analysis of cutting forces. Furthermore, each milling path of the regular dodecagon in this experiment can be independently programmed with different process parameters such as cutting speed, feed rate, cutting width, and milling style, enabling steady and accurate milling performance testing and comparison analysis.
2.2 Experimental setup
The experimental platform for high-speed milling of CFRP is shown in Fig. 2. The experiments were performed on a CNC machining center (MAKINO-V77) using a side milling process. Firstly, the unidirectional CFRP composite sheet was cut into a rectangular sample with dimensions of 70 mm in length, 70 mm in width, and 8 mm in height. Then, the rectangular sample was machined into a regular dodecagon using the CNC program and was fixed onto the cutting force dynamometer (Kistler9257B) with the aid of locating holes. During the experiments, the milling process was conducted using a PCD burr style end mill. Cutting force signals in various directions were collected by the force dynamometer during the side milling process. These signals were amplified by a charge amplifier and transmitted to the cutting force measurement software (Kistler-DynoWare) through a data acquisition card.
As shown in Table 2, the high-speed milling experiment parameters were designed to investigate the influence of cutting forces on the high-speed milling process of CFRP using a single-factor experimental method. The experiment compared the cutting strategies of up milling and down milling at fiber cutting angles with a 30° increment, aiming to reveal the mechanism behind the effect of cutting forces on the high-speed milling of CFRP. Additionally, the experiment studied the impact of four cooling and lubrication methods on cutting forces, including dry milling, minimum quantity lubrication milling (MQL, castor oil, 50 ml/h), graphene nanoparticle-enhanced minimal quantity lubrication milling (Gr-MQL, 0.5% wt graphene addition in castor oil, 50 ml/h), and traditional cooling by cutting fluid pouring (CEP, 5% emulsion, 60 L/h).
3 Milling test results and discussion
3.1 Cutting force data analysis
As shown in Fig. 3, a typical cutting force signal plot is presented for a regular dodecagon sample. To obtain accurate cutting force signals in all directions, the raw signals need to be filtered. The filtered signal plot displays the cutting force signals along twelve cutting paths. During the side milling process, the cutting force in the vertical direction (Z direction) can be neglected since the cutting depth remains constant. By utilizing this regular polygon testing method, stable cutting force signals can be obtained at fixed increments (30°) of fiber cutting angles. It is worth noting that this method provides sufficient sampling length for each cutting angle and clear boundaries between different cutting angles, effectively avoiding measurement errors commonly associated with traditional testing methods.
In the investigation of cutting mechanisms, the analysis of normal (radial) cutting force and tangential cutting force during milling is essential. During experimental procedures, the cutting forces in the X and Y directions measured by the force sensor need to be computed to determine the normal and tangential cutting forces of the milling cutter. The following equations can be derived based on the decomposition and equivalence relationship of cutting forces:
Here, θ represents the fiber cutting angle, Ft represents the tangential cutting force of the milling cutter, Fn represents the normal cutting force of the milling cutter, and Fx and Fy represent the cutting forces measured along the X and Y directions, respectively, by the force sensor.
3.2 Influence of fiber cutting angle on cutting force
The fiber cutting angle, defined as the angle between the cutting feed direction and the fiber axis in the machining process of unidirectional CFRP, plays a crucial role in determining the strength and stiffness of the CFRP material. Specifically, the fiber cutting angle has a significant impact on the cutting force during the machining process.
As shown in Fig. 4, the experiment results demonstrate that in the milling of CFRP, the normal cutting force surpasses the tangential cutting force, and the cutting force in up milling is substantially lower than that in down milling. Moreover, an increase in fiber cutting angle (0–60°) leads to an increase in cutting force due to the transition from interlaminar delamination to extrusion fracture. Additionally, an increase in frictional force between the tool and the fiber further contributes to the increased cutting force. However, within the fiber cutting angle range of 60 to 90°, the cutting force begins to decrease owing to the lower shear strength of carbon fiber. As the cutting edge angle increases relative to the fiber axis, the tool can more readily sever the fibers, resulting in a reduction of the cutting force. Therefore, the influence of fiber cutting angle on cutting force is not a simple linear relationship, but rather a complex interaction between the angle and the anisotropy of carbon fiber strength and friction performance.
Moreover, the cutting force in the reverse fiber cutting zone (90° < θ < 180°) is noticeably lower than that in the forward fiber cutting zone (0° < θ < 90°). This is attributed to the fact that during reverse fiber cutting, the fiber is more susceptible to bending failure under the tool edge. Conversely, during forward fiber cutting, the composite material primarily experiences interlaminar debonding and fiber compression fracture. The cutting force under different cutting angles follows the pattern: 60° > 30° > 90° > 0° > 150° > 120°.
3.3 Influence of feed rate on milling force
Figure 5a, b illustrates the impact of feed per tooth on the normal cutting force (Fn) and tangential cutting force (Ft), respectively.
The experimental results demonstrate that the cutting forces during down milling exceed those during up milling. As the feed per tooth increases, so do the cutting forces, as they are directly proportional to the cutting area. An elevated feed per tooth corresponds to a higher volume of material being cut per tooth, resulting in an increase in the cutting area, and therefore, an increase in the cutting forces. Furthermore, in cutting processes, an increase in cutting area leads to elevated cutting temperatures, which may cause thermal expansion and softening effects, ultimately impacting the cutting forces. Hence, when milling CFRP, selecting and adjusting the feed per tooth according to the specific circumstances is essential to achieve optimal machining outcomes and regulate the cutting forces.
Moreover, the experimental findings revealed that the normal cutting force surpassed the tangential cutting force significantly in CFRP machining. This outcome can be attributed to the springback effect observed on the CFRP surface, which leads to considerable compression and friction on the tool’s flank face. Additionally, the study results demonstrated that the maximum cutting force emerged at a fiber cutting angle of 60°, whereas the minimum cutting force was recorded at a fiber cutting angle of 120°, representing approximately one-third of the maximum value.
3.4 Influence of cutting width on milling force
Figure 6a, b illustrates the influence of cutting width on the normal force and tangential force, respectively.
As the cutting width increases, both cutting forces in the two directions also increase. This is because the increase in cutting width results in the removal of more material from each cutting edge, requiring greater cutting forces. In addition, the cutting resistance and frictional force also increase due to the increased scale of material removal and the stronger fiber deformation and surface rebound effects on the machined surface.
3.5 Influence of high speed cutting on milling force
Figure 7 illustrates the impact of cutting speed on milling forces in the unidirectional CFRP milling process under both up milling and down milling conditions.
The experimental data reveal that both normal and tangential cutting forces exhibit an increasing trend with the cutting speed when it is below 200 m/min. However, a notable reduction in milling forces is observed when the cutting speed exceeds 200 m/min. These results demonstrate that high-speed milling can not only enhance processing efficiency but also reduce cutting forces for CFRP composites. This phenomenon can be attributed to the increase in strain rate with an increase in cutting speed, which causes the matrix to soften, thereby leading to a reduction in friction and cutting resistance and, in turn, an overall reduction in cutting forces. Additionally, the experimental findings indicate that the normal cutting force is greater than the tangential cutting force, and the cutting force in up milling is smaller than that in down milling, which is consistent with previous research. The results suggest that selecting suitable machining processes and tools and adjusting cutting parameters according to processing requirements can lead to optimal machining results for CFRP composites.
3.6 Effect of cooling conditions on cutting force
Figure 8 illustrates the impact of cooling conditions on cutting forces during CFRP milling.
Among the four cooling methods evaluated, dry milling resulted in the highest normal and tangential cutting forces. Although conventional flood cooling with emulsion can effectively reduce cutting forces, this method is expensive and environmentally unfriendly. In contrast, the use of a castor oil-based minimum quantity lubrication (MQL) method can reduce cutting forces by 10–12% compared to dry milling, while also being environmentally friendly. Additionally, the Gr-NMQL cooling method demonstrated the most significant reduction in cutting forces. Compared to dry milling, the Gr-NMQL method can decrease cutting forces by approximately 12–15%.
CFRP materials exhibit high thermal sensitivity, and high-speed cutting can cause elevated temperatures that alter their structure and mechanical properties, resulting in thermal cracking and delamination. Cutting cooling effectively reduces the temperature in the cutting area, thereby minimizing the thermal impact on the material and lowering cutting forces. Additionally, the use of nano-particle-based minimum quantity lubrication (MQL) generates a lubricating film in the cutting area, reducing friction and cutting forces. Given the high fiber content of CFRP structures, adhesion between the tool and workpiece is a common occurrence during cutting, but the use of Gr-NMQL can effectively decrease adhesion and, consequently, cutting forces. Proper cutting cooling conditions can reduce the thermal impact, adhesion, and cutting forces during high-speed CFRP cutting, improving cutting efficiency and workpiece quality. The Gr-NMQL cutting cooling method shows promising results in reducing cutting forces and represents an environmentally friendly processing option.
3.7 Effect of NMQL cooling method on material removal
Figure 9 shows the schematic of material removal mechanism during Gr-NMQL cutting. In up milling, the thickness of chips increases from zero to the maximum at the end of the cut. The cutting force moves along the tangential direction of the cutter, resulting in an upward cutting force on the CFRP. Compared to down milling, this method facilitates the removal of material with lower cutting forces. During down milling, the chip thickness starts out large and gradually decreases during the cutting process. Under this machining mode, the cutting force is directed towards the interior of the material, requiring greater energy from the tool to remove the material.
When using Gr-NMQL cutting, graphene nanosheets can fill the tiny pits on the surface of the CFRP material, which improves the surface finish and flatness, reduces surface roughness, and consequently decreases cutting forces. Additionally, the nanosheets can form a uniform dispersion of colloids, which adhere to the cutting edge of the tool and form a smooth lubricating film, resulting in significant improvements in lubrication performance and reduced friction coefficient and cutting forces during the cutting process. Furthermore, with Gr-NMQL cutting, the cutting heat is more easily absorbed by the graphene nanosheets and castor oil nanofluids and discharged with the chips, which also reduces cutting forces and improves the machining quality.
3.8 Effect of fiber cutting angle on surface integrity
In contrast to the conventional two-dimensional surface roughness representation (Ra) method, the utilization of three-dimensional surface roughness measurement proves effective in capturing data across all three dimensions of machined surfaces, thereby providing a more comprehensive insight into surface contour information. This study employs the three-dimensional roughness parameter Sa to characterize the surface roughness of CFRP. A typical CFRP milling surface profile is presented in Fig. 10. Figure 11 illustrates the influence of fiber cutting angle on surface roughness in CFRP milling. The study conducted a comparative analysis of the effects of milling methods and cooling lubrication conditions on surface roughness. It was observed that the surface roughness was significantly superior when cutting along the direction of the fiber as compared to cutting against it, and the surface quality was optimal at a 90° cutting angle. Additionally, when using a burr milling cutter, surface roughness was found to be better when fiber cutting angle is 30–90°. Moreover, cutting cooling lubrication was found to significantly improve surface roughness, particularly when using the Gr-NMQL cutting method. The Gr-NMQL cutting lubrication method was found to result in superior surface quality as compared to dry cutting and traditional pouring cooling.

Fig. 10 Typical machined surface profile of CFRP
Different fiber cutting angles cause significant differences in surface microstructure while affecting cutting forces. Figure 12 shows the micro-topography of CFRP surfaces under different fiber cutting angles. When the fiber cutting angle is small, the CFRP material is primarily removed through interlaminar shear. In this case, due to fiber debonding, significant grooves form on the machined surface. As the cutting angle increases, the fibers start to be cut by the tool edge, and the crack propagates along the composite material interface under the action of cutting forces. Under the tool compression, the resin adheres to a small amount of fiber cross-section. When the cutting angle is 60°, the adhesion effect of the resin becomes more prominent, and surface quality is further improved. Due to the different mechanical properties of the resin matrix and fibers, significant microstructures appear on the cutting surface. Unlike metal materials, the randomness of fiber fracture crack propagation during CFRP cutting results in machining surface defects.
When the fiber cutting angle is around 90°, the fibers on the CFRP surface are easily cut, resulting in smaller fiber cross-sections and an optimal surface roughness. As the fiber cutting angle continues to increase, the surface quality deteriorates sharply in the reverse fiber cutting region (90–180°). In this region, fibers are mainly removed by bending failure under the combined effect of tool edge extrusion and cutting, resulting in low cutting forces. However, this removal method leads to poor surface quality and high surface roughness, as the fiber breakage caused by bending failure usually occurs below the machined surface, forming obvious surface depressions. Moreover, due to the randomness of the fracture position, the machined surface presents uneven pits. Although using a burr style end mill can reduce cutting forces and improve the machining quality, it still cannot achieve an optimal surface in the reverse fiber cutting region.
3.9 Effect of cooling method on tool wear
Figure 13 shows the influence of cutting length on tool wear. High-speed milling was used to compare and analyze the tool wear performance of different milling methods and lubrication cooling conditions. Using a burr end mill, the tool wear during down milling was found to be greater than that during up milling under dry cutting conditions. Therefore, in high-speed machining of CFRP, up milling can improve tool life. In addition, tool wear was improved under three different cutting lubrication cooling conditions, among which the Gr-NMQL cutting method showed the best durability of the tool.
4 Conclusion
This paper employs the burr style end mill high-speed milling process and experiments with a specially designed regular dodecagon cutting trajectory to investigate the high-speed machining performance of unidirectional CFRP. The influence of machining parameters (feed per tooth, cutting width, and cutting speed) and fiber cutting angle on cutting force and surface quality during high-speed milling of unidirectional CFRP is elucidated. The effects of up milling, down milling, and cooling lubrication conditions on cutting force and surface quality are compared, and the SEM characterization of the machined surface under typical cutting angles is conducted to reveal the underlying mechanisms affecting cutting force and surface quality during high-speed milling of unidirectional CFRP. The following conclusions can be drawn.
Using the regular dodecagon cutting path method, it is possible to efficiently and accurately measure the cutting force at different fiber cutting angles. By selecting different regular polygon paths according to the research requirements for cutting angles, cutting tests can be combined to improve the testing accuracy. This is of great significance for the study of cutting performance of anisotropic materials.
Using the Gr-NMQL cutting and lubrication method can improve cutting force and surface quality and has a positive effect on tool wear. Compared to dry cutting, the maximum cutting force can be reduced by about 15%. Gr-NMQL cutting has better surface quality than emulsion pouring cutting and has application prospects.
In the high-speed milling experiment of unidirectional CFRP with a 30° angle increment, it was found that the fiber cutting angle has a significant influence on the cutting force and surface integrity of CFRP. The experimental results showed that using a PCD tool, the normal cutting force is greater than the tangential cutting force, and both forces follow the pattern of 60° > 30° > 90° > 0° > 150° > 120°. Due to different fiber fracture and failure mechanisms, the machining quality in the forward fiber cutting region is better than that in the reverse fiber cutting region, and the surface roughness is optimal when cutting along the 90° direction. However, processing composite materials with curved surface presents a complex coupled process. The test results obtained from planar machining of composite materials may exhibit variations when applied to curved surface machining.
A comparative study was performed to evaluate and compare the cutting force and surface quality between up milling and down milling. High-speed milling was conducted using a PCD burr style end mill, and the results indicated that the utilization of up milling led to significant improvements in both cutting force and surface quality. Specifically, when the cutting speed exceeded 200 m/min, improvements in both normal and tangential cutting forces were observed. These findings suggest that up milling can serve as an effective strategy to enhance the performance of CFRP high-speed milling processes.
References
Zhang L, Ren C, Zhou C, Xu H, Jin X (2015) Single fiber push-out characterization of interfacial mechanical properties in unidirectional CVI-C/SiC composites by the nano-indentation technique. Appl Surf Sci 357:1427–1433
Zhang L, Ren C, Ji C, Wang Z, Chen G (2016) Effect of fiber orientations on surface grinding process of unidirectional C/SiC composites. Appl Surf Sci 366:424–431
Zou F, Dang J, Wang X, Zhang H, Sun X, An Q, Chen M (2021) Performance and mechanism evaluation during milling of CFRP laminates under cryogenic-based conditions. Compos Struct 277:114578
Kesarwani S, Verma RK, Jayswal SC (2023) Evaluation of the cutting force, burr formation, and surface quality during the machining of carbon nanoparticle modified polymer composites for structural applications. Mater Today Commun 34:105375
Aamir M, Tolouei-Rad M, Giasin K, Nosrati A (2019) Recent advances in drilling of carbon fiber-reinforced polymers for aerospace applications: a review. Int J Adv Manuf Technol 105:2289–2308
Chen L, Huang Y, Li W, Yang R, Chen X, Zhang G, Rong Y (2023) Acoustic emission monitoring and heat-affected zone evaluation of CFRP laser cutting. Compos Struct 304:116419
He Y, Sheikh-Ahmad J, Zhu S, Zhao C (2020) Cutting force analysis considering edge effects in the milling of carbon fiber reinforced polymer composite. J Mater Process Technol 279:116541
Kumar D, Gururaja S (2020) Machining damage and surface integrity evaluation during milling of UD-CFRP laminates: dry vs. cryogenic. Compos Struct 247:112504
Zheng H, Zhang W, Li B, Zhu J, Wang C, Song G, Wu G, Yang X, Huang Y, Ma L (2022) Recent advances of interphases in carbon fiber-reinforced polymer composites: a review. Compos Pt B-Eng 233:109639
Voss R, Seeholzer L (2018) Analytical force model for orthogonal machining of unidirectional carbon fibre reinforced polymers (CFRP) as a function of the fibre orientation. J Mater Process Technol 263:440–469
Song Y, Cao H, Zheng W, Qu D, Liu L, Yan C (2022) Cutting force modeling of machining carbon fiber reinforced polymer (CFRP) composites: a review. Compos Struct 299:116096
Chen X, Li W, Rong Y, Zhang G, Chen L, Huang Y (2022) Dimethicone-assisted laser cutting of CFRP hole. Archiv Civ Mech Eng 22(4):182
Han L, Zhang J, Sun T (2022) Tailoring fiber arrangement in subsurface damage layer of unidirectional CFRP composites by reverse multi-pass cutting. Compos Sci Technol 227:109571
Wang X, Song C, Li L, Jiao F (2022) Study on the influence of fiber cutting angle on cutting force in ultrasonic assisted cutting CFRP disc. Int J Adv Manuf Technol 121(5-6):3989–3997
Ashworth S, Fairclough JPA, Meredith J, Takikawa Y, Kerrigan K (2022) Effects of tool coating and tool wear on the surface quality and flexural strength of slotted CFRP. Wear 498:204340
Geier N (2020) Influence of fibre orientation on cutting force in up and down milling of UD-CFRP composites. Int J Adv Manuf Technol 111(3-4):881–893
Çolak O, Sunar T (2016) Cutting forces and 3D surface analysis of CFRP milling with PCD cutting tools. Procedia CIRP 45:75–78
Wu W, Li S, Qin X, Liu W, Cui X, Li H, Shi M, Liu H (2022) Effects of fiber orientation on tool wear evolution and wear mechanism when cutting carbon fiber reinforced plastics. Chin J Aeronaut 36(5):549–565
Madhavan V, Lipczynski G, Lane B, Whitenton E (2015) Fiber orientation angle effects in machining of unidirectional CFRP laminated composites. J Manuf Process 20:431–442
Sauer K, Witt M, Putz M (2019) Influence of cutting edge radius on process forces in orthogonal machining of carbon fibre reinforced plastics (CFRP). Procedia CIRP 85:218–223
Wang C, Ming W, An Q, Chen M (2017) Machinability characteristics evolution of CFRP in a continuum of fiber orientation angles. Mater Manuf Process 32(9):1041–1050
Halim NFHA, Ascroft H, Barnes S (2017) Analysis of tool wear, cutting force, surface roughness and machining temperature during finishing operation of ultrasonic assisted milling (UAM) of carbon fibre reinforced plastic (CFRP). Procedia Eng 184:185–191
Mishra SK, Gómez-Escudero G, González-Barrio H, Calleja-Ochoa A, Martinez S, Barton M, de Lacalle LNL (2022) Machining-induced characteristics of microstructure-supported LPBF-IN718 curved thin walls. Procedia CIRP 108:176–181
Cepero-Mejías F, Phadnis VA, Kerrigan K, Curiel-Sosa JL (2021) A finite element assessment of chip formation mechanisms in the machining of CFRP laminates with different fibre orientations. Compos Struct 268:113966
Song C, Jin X (2022) Analytical modeling of chip formation mechanism in cutting unidirectional carbon fiber reinforced polymer. Compos Pt B-Eng 239:109983
Seeholzer L, Scheuner D, Wegener K (2020) Analytical force model for drilling out unidirectional carbon fibre reinforced polymers (CFRP). J Mater Process Tech. 278:116489
Duan Z, Liu G, Fan X, Chen T (2021) Study on cutting force performance and cutting mechanism of carbon fiber reinforced polymer (CFRP) composites. J Adv Mech Des Syst Manuf 15(3):M37
Yan X, Reiner J, Bacca M, Altintas Y, Vaziri R (2019) A study of energy dissipating mechanisms in orthogonal cutting of UD-CFRP composites. Compos Struct 220:460–472
Han L, Zhang J, Liu Y, Gu Q, Li Z (2021) Finite element investigation on pretreatment temperature-dependent orthogonal cutting of unidirectional CFRP. Compos Struct 278:114678
Liu C, Ren J, Shi K, Zhang Y (2023) Investigation of fracture mechanism evolution model for UD-CFRP and MD-CFRP during the milling process. Compos Struct 306:116585
Xiao J, Gao C, Ke Y (2018) An analytical approach to cutting force prediction in milling of carbon fiber reinforced polymer laminates. Mach Sci Technol 22(6):1012–1028
Ning H, Zheng H, Yuan X (2021) Establishment of instantaneous milling force prediction model for multi-directional CFRP laminate. Adv Mech Eng 13(6):2072279365
Zhang B, Li Y, Wang F, Yang L, Deng J, Lin Y, He Q (2023) Machining inclination selection method for surface milling of CFRP workpieces with low cutting-induced damage. Compos Struct 304:116495
Skoczylas J, Samborski S, Kłonica M (2019) The application of composite materials in the aerospace industry. J Technol Expl Mech Eng 5(1):1–6
Funding
This work was supported by the Tianjin Education Commission Research Project (2021KJ039).
Author information
Authors and Affiliations
Contributions
LZ: methodology, resources, investigation, validation, formal analysis, writing—review and editing, and visualization. XZ: conceptualization, methodology, formal analysis, data curation, validation, and writing—original draft.
Corresponding author
Ethics declarations
Competing interests
The authors declare no competing interests.
Additional information
Publisher’s Note
Springer Nature remains neutral with regard to jurisdictional claims in published maps and institutional affiliations.
Rights and permissions
Springer Nature or its licensor (e.g. a society or other partner) holds exclusive rights to this article under a publishing agreement with the author(s) or other rightsholder(s); author self-archiving of the accepted manuscript version of this article is solely governed by the terms of such publishing agreement and applicable law.
About this article
Cite this article
Zhang, L., Zhang, X. Effect of milling type and cooling mode on cutting characteristics during CFRP milling using a PCD burr end mill. Int J Adv Manuf Technol 129, 2735–2745 (2023). https://doi.org/10.1007/s00170-023-12488-6
Received:
Accepted:
Published:
Issue Date:
DOI: https://doi.org/10.1007/s00170-023-12488-6