Abstract
The heat generated during the machining of titanium alloys accumulates in the cutting area during machining. These high temperatures lead to tool wear, affect the quality of the machined surface, and alter the cutting force. In light of this, a new method for mixing vegetable oil additives is proposed herein, through the addition of graphene nanoparticles and sulfur-based extreme pressure (EP) additives to canola oil to improve the lubrication and cooling performance of the machining area. The optimum results were found for the combination of canola oil + graphene + sulfur-based EP additives, which effectively decreased the temperature of the cutting area and wear of cutting tools. In comparison to canola oil, the flank wear value decreased by 56.4%. Similarly, the surface roughness and cutting force when using the canola oil + graphene + sulfur-based EP additive were the lowest, exhibiting a decrease of 36.1% and 27.0%, respectively, in comparison to simple canola oil. The inorganic film produced by the EP additive molecule helps prevent direct contact between the tool and the workpiece, reducing tool wear and improving surface quality. Furthermore, adhered chips were also observed, with a layered morphology. Graphene shortens the length of the chip-adhesion layer (0.081 mm) and reduces adhesion wear. Elemental testing confirmed that graphene penetrates more easily into the manufacturing area, which is beneficial to reducing abrasive wear and the cutting force. In addition, the higher thermal conductivity of graphene will effectively reduce the temperature of the cutting area, which impedes the agglomeration of these chips. This weakens the adhesion of the chips to the surface of the workpiece.
Similar content being viewed by others
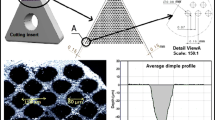
Explore related subjects
Discover the latest articles, news and stories from top researchers in related subjects.Avoid common mistakes on your manuscript.
1 Introduction
As a research hotspot in the field of machining, the minimal quantity of lubricant (MQL) has been extensively applied in the turning of titanium alloy [1]. In the MQL environment, a small amount of cutting fluid (10–100 ml/h) is atomized together with compressed air and sprayed to the cutting area as a lubricating and cooling aerosol [2]. The consumption of mineral oil as the MQL is lower in comparison to water injection machining, but the mineral oil is not recovered during evaporation. Evaporation of mineral oils can be harmful because they are highly toxic, non-renewable, and costly to dispose of. Therefore, a research priority is to make use of vegetable oil in MQL machining [3].
Sankaranarayanan et al. [4] critically analyzed the prospects for sustainable green manufacturing by using ecologically friendly vegetable oil–based cutting fluids. The applicability of several vegetable oils in various metal cutting applications is reviewed and compared. As a potential eco-friendly metal cutting fluid, vegetable oil provides an attractive solution to various health hazards (such as skin irritation, harmful aerosols, ingestion, etc.). Vegetable oil can replace synthetic cutting fluid. This alternative method is effective and economical to realize green manufacturing. In the machining of titanium alloy, vegetable oil–based MQL upgrades surface quality and reduce wear on cutting tools by virtue of its superior cooling and lubricating properties [5]. Rahim and Sasahara [6] studied the life of cutting tools when using palm oil in the course of drilling titanium alloy. The results demonstrate that, in the MQL environment, the lifespan of cutting tools was extended by 306% compared with dry cutting. Khan et al. [7] studied the impact of vegetable oil–based cutting fluid on cutting properties in the MQL turning of low alloy steel (AISI9310). They concluded that, compared with water injection machining, MQL using vegetable oil–based cutting fluid can lower the temperature of the average chip-cutter interface by 10%; and enhance the formation mode of the chip, wear of cutting tools, and surface finish to different degrees. Vegetable oil boasts more superior lubrication and cooling properties, chiefly because oleic acid and ricinoleic acid contained in vegetable oil provide high binding energy and a low coefficient of friction [8]. However, although vegetable oil–based MQL can greatly improve the lubrication performance of the machining area, it is still insufficient for the heat dispersion of the machining area. Therefore, it is necessary to provide additional cooling for the machining area. Khanna et al. [9] discussed the various challenges and future needs associated with cryogenic and hybrid manufacturing technologies. The article pointed out that the further mixing of low temperature conveying technology and minimum quantity lubrication (MQL) is beneficial to improve the machinability of difficult-to-process materials. In the process of turning 316L austenitic steel, Maruda et al. [10] considered three cooling methods: dry machining, MQCL method, and MQCL + EP/AW. It was found that when cooled by the MQCL method with EP/AW, the friction coefficient and chip thickening coefficient on the rake face decreased and the sliding angle increased compared with dry machining and MQCL method. Considering the chip shape, the MQCL method is more advantageous when cutting 316L austenitic steel. When cooled by the MQCL method, the chip shape is in the form of short spiral or very loose form which makes easier to remove it from the cutting area. Krolczyk et al. [11] studied the parametric and non-parametric description of the surface topography after turning under dry cutting and MQCL conditions. The results showed that, compared with dry cutting, the application of MQCL method can lead to the reduction of three-dimensional surface roughness parameters. In addition, the distribution of irregular peaks and pits by MQCL method is better than that by dry cutting, which means that the surface machined by MQCL technology has high wear resistance.
Thus, in a bid to further enhance cooling and lubrication properties, a range of nanoparticles have been dispersed into vegetable oil, following the heat transfer enhancement theory of solids [12]. Su et al. [13] compared experiments with dry turning and concluded that the addition of graphite nanoparticles under MQL conditions can reduce the cutting force by 26% and the cutting temperature by 21%. Rapeti et al. [14] mixed MoS2 nanoparticles with different vegetable oils in the MQL environment. The results suggested that MQL fluid with nanoparticles can decrease the wear of cutting tools, cutting force, cutting temperature, and surface roughness in comparison with other selected machining environments. For Al2O3nanoparticles, Hadi and Atefi [15] investigated the effect of Al2O3NMQL in the milling processes of AISID3 steel and found that the surface roughness was 25% less than that of pure MQL. Sharma et al. [16] compared the simulation and experiment of nano-additive based on alumina/multi-walled carbon nanotubes in the course of turning. The results indicated that the coefficient of friction on the rake face of cutting tools was decreased and the temperature distribution was uniform.
Apart from that, an extreme pressure (EP) additive provides low viscosity, favorable water solubility, and a high lubricating function. Extreme pressure additive reacts with the surface at high temperature and under high pressure, absorbing the surface and decreasing the shear stress [17]. Ozcelik et al. [18] compared the properties of four vegetable oils in a turning test, including EP additive and two kinds of commercial cutting fluid (semi-synthetic and mineral). They found that EP additive brings out the best in surface roughness, feed force, and wear of cutting tools. Maruda et al. [19] figured out that, in comparison with dry cutting, phosphate-based EP additive decreased friction in the contact zone between the cutting tool and the workpiece, thereby lowering the parameters of selected surface topography by 6–38% and the wear of flank surface by 23%. The reason behind these findings is the high-concentration anti-wear friction film that takes shape on the machined surface. In addition, Maruda et al. [20] also studied the tool wear of P25 carbide inserts under different cooling conditions during AISI 1045 carbon steel finishing: dry cutting, minimum cooling and lubrication, and phosphate-based extreme pressure/AW additives. The results showed that the blade wear of MQCL-EP/AW method is around 40% less than that of dry cutting and around 25% less than that of the MQCL method. This improvement proved to be the result of the formation of a phosphate-based friction film. In addition, scanning electron microscopy analysis showed that the active compound contained in the friction film reduces the adhesion and diffusion rate during tool wear.
Previous studies have shown favorable results by adding a range of additives to vegetable oil, but most of the studies are restricted to one additive, which may make the cutting fluid play an incomplete role in the machining region. Sulfur is extensively applied as an additive in cutting fluid because of its special structure and properties. It also plays a role in reducing friction, compression resistance, and dispersion in the machining region. Similarly, graphene can be used as an additive in cutting fluid to decrease the generation of heat and enhance the heat absorption at the contact interface of the tool-chip and the tool-workpiece [21]. Thus, it may be possible to further enhance the friction performance and heat absorption of the cutting area by taking graphene nanoparticles and sulfur-based EP additive as additives to the cutting fluid. This paper evaluated the influence of graphene nanoparticles and sulfur-based EP additive on turning titanium alloy from four points: wear of cutting tools, cutting temperature, surface roughness, and cutting force.
2 Experimental design
2.1 Workpiece materials and tools
The material used in this study was titanium alloy Ti6Al4V, with a diameter of 30 mm and a length of 200 mm. A carbide blade was used, with the model being DCMT11T304-SMIC907. The machining method was cylindrical turning. The chemical composition of the workpiece is displayed in Table 1, and its main mechanical properties are listed in Table 2.
2.2 Test plan
Three machining conditions were compared as below: (1) canola oil + graphene + sulfur–based EP additive, (2) canola oil + sulfur–based EP additive, and (3) canola oil. The cutting speed was set to 60 m/min and 100 m/min. The feed speed was f = 0.1 mm/rev and the cutting depth was 0.5 mm. Under a range of machining conditions, the turning length was 80 mm. A new blade was applied after turning under each condition.
2.3 Measuring equipment and MQL system
The computer numerical control lathe used in the test was the CAK4085nj, and the temperature of the machining region was measured using a FLIR T630 sc infrared thermal imager. The wear of cutting tools was measured by VMX-2000C ultra-large depth-of-field optical three-dimensional microscope. The microscopic surface morphology of the workpiece was observed using a ZEISS thermal field emission scanning electron microscope and the force during machining was measured with a Kistlter9257b three-dimensional dynamometer. The cutting tool was installed on the dynamometer by a specially designed fixture, and the cutting force in the machining process was measured with a DAQ card and Dynoware software. The test device is displayed in Fig. 1.
The temperature of the processing area is measured by FLIR T630 sc infrared thermal imaging camera. Firstly, connect the thermal imaging camera to the computer and place the thermal imaging camera at a distance of about 1 m from the lathe, so as to obtain temperature data more accurately. Secondly, the contact area between the tool and the workpiece is completely and clearly displayed on the screen of the infrared thermal imager. Finally, the maximum temperature of the contact area between the tool and the workpiece is obtained by computer.
The roughness of the machined surface was measured using a TR240, with a sampling length of 0.8 mm. Measurements were made by dividing the workpiece into four sections on average, randomly selecting six points in each section along the circumferential direction, and then measuring the 24 selected points and calculating an average value. This was done to sample the workpiece area comprehensively and decrease errors.
The outlet temperature of the SUNAIR of MQL equipment was − 10℃, the air pressure of the air compressor was 10 bar, and the liquid flow rate of the nozzle was 70 mL/h. The sprayed liquid formed a complete cone, which was around 15°. The nano nozzle exerted the best effect in the spraying range with a length of 190 mm, as presented in Fig. 2. Therefore, the tool was used within this effective parameter range during the test.
2.4 Preparation of the cutting fluid
Both one-step and two-step approaches are commonly used to disperse nanoparticles into solution [23]. In this study, the two-step approach was chosen. The content of graphene nanoparticles was 0.5%, and the content of sulfur-based EP additive was 12%. The chosen vegetable oil was canola oil with a single layer of graphene applied.
The canola oil, graphene nanoparticles, and sulfur-based EP additive were weighed using a high-precision electronic balance (precision = 0.001 g). The solution was thoroughly stirred with a magnetic stirrer and then dispersed with an ultrasonic disperser. The mixing process is displayed in Fig. 3.
When the machining was finished, the surface of the workpiece was cleaned to prevent the cutting fluid from remaining on the surface of the workpiece and interfering with EDS element testing.
3 Results and discussion
3.1 Wear of cutting tools
Regardless of the applied cutting fluid, abrasive and adhesive wear appeared as the dominant wear mechanisms [24]. The wear value Vb of the flank surface of cutting tools directly embodies the service life of the tools. Figure 4 shows the wear length of the flank surface under three machining conditions at 60 m/min and 100 m/min. It can be seen that the order of wear length of the flank surface from small to large was canola oil + graphene + sulfur–based EP additive < canola oil + sulfur-based EP additive < canola oil. The wear on the cutting tools was the most severe with canola oil and the wear length of the flank surface was 0.262 mm (60 m/min) and 0.436 mm (100 m/min). However, after adding sulfur-based EP additive into canola oil, the wear of the flank surface of cutting tools was significantly reduced at 0.206 mm (60 m/min) and 0.247 mm (100 m/min). Most importantly, the cutting tools with canola + graphene + sulfur-based EP additive experienced the smallest wear at 0.132 mm (60 m/min) and 0.190 mm (100 m/min). In comparison with canola oil at cutting speeds of 60 m/min and 100 m/min, the wear length of the flank surface of canola oil + graphene + sulfur-based EP additive was decreased by 49.6% and 56.4%, respectively.
The temperature of the machining region plays a vital role in the wear of cutting tools, as displayed in Fig. 5, which demonstrates the temperature comparison of two cutting speeds under three machining conditions. The temperature was highest with canola oil at 158.3 ℃ (60 m/min) and 177.6 ℃ (100 m/min). Canola oil and sulfur-based EP additive were 132.8 ℃ (60 m/min) and 147.2 ℃ (100 m/min). Canola oil + graphene + sulfur-based EP additive was the lowest temperature at 108.3 ℃ (60 m/min) and 124.5 ℃ (100 m/min). Under the action of vegetable oil, the molecules of sulfur-based EP additive readily react with the surface of cutting tools. The instantaneous high temperature and high pressure on the friction surface resulted in the S–S bond and C-S bond in the molecules of EP additive to break and generate organic iron mercaptide and inorganic films of iron sulfide [25]. This inorganic film hinders the contact between the tool and the workpiece, thereby resisting wear and enduring extreme pressure, reducing the temperature of the cutting area and reducing tool wear. Likewise, after adding graphene nanoparticles into canola oil, the temperature decreased even further. Graphene as an additive also reduces the temperature of the cutting area and the wear of the cutting tools.
In addition, the electron microscope pictures taken on the flank surface of the tool further found the adhered chips, which appeared to be layered. Figure 6 shows the comparison of the chip adhesion layer length under the three processing conditions at 100 m/min. It can be seen from the figure that the order of chip adhesion layer length from small to large is canola oil + graphene + sulfur-based EP additive < canola oil + sulfur-based EP additive < canola oil. The chip adhesion layer is the longest (0.141 mm) without any additives, but the chip adhesion layer is significantly reduced (0.086 mm) after adding graphene nanoparticles. However, the change of the chip adhesion layer is not obvious (0.081 mm) after adding sulfur-based EP additive on the basis of graphene nanoparticles. This shows that the sulfur-based EP additive is not as effective as graphene in reducing chip adhesion. In addition, C, N, Co, and W elements were found through EDS element detection, as shown in Fig. 7. Co and W elements are the main components of the carbide tool matrix, indicating that the coating of the tool has been destroyed. However, this damage is most likely due to abrasive wear caused by stiff points in the workpiece material [26].
In addition, the content of C element is as high as 12.38%, which proves that graphene can penetrate into the machining area. Canola oil can form a lubricant film on the tool-workpiece contact surface [27]. This lubricant film can not only effectively inhibit the adhesion of chips to the surface of the tool, but also prevent the stiff points in the material from contacting the surface of the tool, thereby reducing adhesion and abrasive wear. However, graphene can further enhance the lubricity of the lubricating oil film [28]. Graphene nanoparticles are small in size and under the strong pressure of the nozzle, they will be transported to the microscopic surface where the tool and the workpiece contact, playing a role of lubrication and cooling [29], effectively weakening the affinity between the workpiece material and the tool surface, thus further inhibiting chip adhesion and hard point scratching, and reducing adhesion and abrasive wear.
3.2 Surface roughness
Surface roughness exerts an enormous influence on parts. The smaller the surface roughness, the more complete the contact between mating surfaces and the smaller the wear. It also influences the fatigue strength of the workpiece. A workpiece with large surface roughness is uneven and the stress is concentrated on the raised sections. Figure 8 lists the average surface roughness of each machining environment at two different cutting speeds. It shows that the order of surface roughness from small to large was canola oil + graphene + sulfur-based EP additive < canola oil + sulfur-based EP additive < canola oil. Compared with canola oil alone, oil + graphene + sulfur-based EP additive decreased the surface roughness by 30.6% at 60 m/min and 36.1% at 100 m/min. The lowest surface roughness was found for canola oil + graphene + sulfur-based EP additive.
Chips stuck on the workpiece surface, along with scratches on the workpiece surface caused by chips stuck on the cutting tool, can decrease the surface roughness of a workpiece. For comparison, electron microscope pictures were taken at the same position on the surface of the workpiece under different processing conditions (Fig. 9). The results from this study showed that larger and a higher number of chips adhered to canola oil, and the adhesion was more severe, as displayed in Fig. 9a (red region). However, chip adhesion was lower in canola oil with sulfur-based EP additive, as shown in Fig. 9b (red region), although irregular scratches were discovered on the surface of the workpiece, as indicated in Fig. 9b (yellow region). Under the machining conditions of canola oil + graphene + sulfur-based EP additive, the volume of adhered chips became smaller, as displayed in Fig. 9c (red region).
The reason behind these findings is that as there is no additive in the canola oil, the blade is tightly attached to the workpiece, which results in increased friction force and an inability to disperse heat. This results in the chips clumping together and adhering to the surface of the workpiece, as presented in Fig. 10a. The direct contact between the cutting tool and the workpiece can be alleviated by adding sulfur-based EP additive to canola oil [30]. Sulfur-based EP additive decreases friction and pressure on the surface of the cutting tool-workpiece and then lowers the cutting temperature. Low temperature is not favorable for the aggregation of chips and may inhibit their adhesion. In addition, low temperatures can inhibit the peeling of chips on the cutting tool more easily, which leads to increased hardness of the cutting tool and helps the tool to form scratches on the surface of the workpiece, as shown in Fig. 10b. However, the heat absorption and lubrication of the cutting fluid can be increased considerably by adding graphene nanoparticles into canola oil [31]. The heat in the cutting area was dispersed to a greater extent, which effectively inhibits the agglomeration of chips, decreases the adhesion of chips to the surface of the workpiece, and causes the surface roughness to decrease further, as demonstrated in Fig. 10c.
3.3 Cutting force
Figure 11 shows that the order of cutting force from small to large was canola oil + graphene + sulfur-based EP additive < canola oil + sulfur-based EP additive < canola oil at two cutting speeds of 60 m/min and 100 m/min. The figure reveals that the cutting force does not decrease distinctly after adding sulfur-based EP additive to vegetable oil, particularly at the cutting speed of 100 m/min, from 98.21 N to 94.97 N. This may be because sulfur-based EP additive is not effective enough in reducing cutting forces. However, after graphene was added, the cutting force distinctly decreased, and the cutting force achieved a minimum value of 73.17 N at a cutting speed of 100 m/min. In comparison with canola oil, the cutting force of canola oil + graphene + sulfur-based EP additive decreased by 27.7% and 27.0% at the two cutting speeds of 60 m/min and 100 m/min, respectively.
The effect of graphene as an additive that reduces cutting force is better than the sulfur-based EP additive due to the good dispersion ability of graphene nanoparticles in the tool-workpiece contact area [32]. As revealed in Fig. 12, important elements of C and O were found in the EDS element of the chips adhered to the surface of the workpiece, but there was no element of S. This suggests that graphene can penetrate into the machining region and burn at high temperature instantaneously, thereby adhering to the chips. This may be because the single-layer graphene is characterized by ultra-thin layered structure and large specific surface area, and thus it can readily penetrate into the contact area of the cutting tool-workpiece. Graphene nanoparticles have strong intermolecular forces. The intermolecular force makes it easier to fix small-weight nanoparticles and vegetable oil molecules together, which is beneficial to inhibit the separation of graphene nanoparticles by external forces, and can effectively promote graphene nanoparticles to play a lubricating and cooling role in the tool-workpiece contact area [33]. In addition, graphene nanoparticles have excellent viscosity and dispersibility, so it has excellent anti-friction properties at the tool-workpiece interface [34]. They can exist as a lubricant at this oil film interface, and will maintain good lubrication performance under high temperature and high pressure, which is more conducive to inhibiting the direct contact between the tool and the workpiece, improving the lubrication effect and reducing the cutting force.
4 Summary
This article provides a new method of mixing vegetable oil additives, adding graphene nanoparticles and sulfur-based EP additive to canola oil to promote the lubrication and cooling performance of the processing area. Respectively, canola oil + graphene + sulfur-based EP additive, canola oil + sulfur-based EP additive, and canola oil, were chosen for comparison. The machining effect was assessed from four perspectives: wear of cutting tools, cutting temperature, surface roughness, and cutting force. The conclusions were specifically outlined below:
-
1.
The least wear of cutting tool occurred with the canola oil + graphene + sulfur-based EP additive. When compared with canola oil, the wear of the flank surface was lowered by 49.6% and 56.4% at cutting speeds of 60 m/min and 100 m/min, respectively. The inorganic film produced by the sulfur polar pressure molecule helps to prevent the direct contact between the tool and the workpiece and reduce tool wear. In addition, graphene shortens the length of the chip adhesion layer (0.081 mm) and reduces adhesion wear. However, the effect of sulfur-based EP additive in reducing adhesion is not very obvious. Element detection proves that graphene nanoparticles can penetrate into the machining area, which is beneficial to reduce abrasive wear.
-
2.
The cutting temperature of canola oil + graphene + sulfur-based EP additive is the lowest. When compared with canola oil, the surface roughness decreased by 30.6% and 36.1% at cutting speeds of 60 m/min and 100 m/min, respectively. The high thermal conductivity of graphene and the wear resistance of the sulfur-based EP additive are the main factors to reduce the temperature of the cutting zone. Low temperature is beneficial to prevent chip agglomeration, reduce the volume of chip adhesion, and improve the surface quality of the workpiece.
-
3.
The cutting force was the smallest with the canola oil + graphene + sulfur-based EP additive. When compared with canola oil, the cutting force decreased by 27.7% and 27.0% at cutting speeds of 60 m/min and 100 m/min, respectively. Elemental testing demonstrated that graphene nanoparticles penetrate into the machining area more easily than sulfur-based EP additive, which helps to enhance the stability of lubricating oil film, thus providing lubrication cooling and reducing cutting force.
References
Benjamin DM, Sabarish VN, Hariharan M, Samuel RD (2018) On the benefits of sub-zero air supplemented minimum quantity lubrication systems: an experimental and mechanistic investigation on end milling of Ti-6-Al-4-V alloy. Tribol Int 119:464–473
Revuru RS, Posinasetti NR, Ramana V, Amrita M (2017) Application of cutting fluids in machining of titanium alloys—a review. Int J Adv Manuf Technol 91(5–8):2477–2498
Gaurav G, Sharma A, Dangayach GS, Meena ML (2020) Assessment of jojoba as a pure and nano-fluid base oil in minimum quantity lubrication (MQL) hard-turning of Ti-6Al-4V: a step towards sustainable machining. J Clean Prod 272:122553
Sankaranarayanan R, Hynes NRJ, Kumar JS, Krolczyk GM (2021) A comprehensive review on research developments of vegetable-oil based cutting fluids for sustainable machining challenge. J Manuf Process 67:286–313
Rahim EA, Sasahara H (2011) A study of the effect of palm oil as MQL lubricant on high speed drilling of titanium alloy. Tribol Int 44(3):309–317
Rahim EA, Sasahara H (2011) Investigation of tool wear and surface integrity on MQL machining of Ti-6AL-4V using biodegradable oil. Proc Inst Mech Eng B J Eng Manuf 225(9):1505–1511
Khan M, Mithu M, Dhar NR (2009) Effects of minimum quantity lubrication on turning AISI9310 alloy steel using vegetable oil-based cutting fluid. J Mater Process Technol 209(15–16):5573–5583
Wang Y, Li C, Zhang Y, Li B, Yang M, Zhang XP, Guo S, Liu G (2016) Experimental evaluation of the lubrication properties of the wheel/workpiece interface in MQL grinding with different nanofluids. Tribol Int 99:198–210
Khanna N, Agrawal C, Pimenov DY, Singla AK, Machado AR, Silva LRR, Gupta MK, Sarikaya M, Krolczyk GM (2021) Review on design and development of cryogenic machining setups for heat resistant alloys and composites. J Manuf Process 68:398–422
Maruda RW, Krolczyk GM, Niesłony P, Krolczyk JB, Legutko S (2016) Chip formation zone analysis during the turning of austenitic stainless steel 316L under MQCL cooling condition. Procedia Eng 149:297–304
Krolczyk GM, Maruda RW, Krolczyk JB, Niesłony P, Wojciechowskic S, Legutko S (2018) Parametric and nonparametric description of the surface topography in the dry and MQCL cutting conditions. Measurement 121:225–239
Eltaggaz A, Hegab H, Deiab I, Kishawy HA (2018) Hybrid nano-fluid-minimum quantity lubrication strategy for machining austempered ductile iron (ADI). Int J Interact Des Manuf 12(4):1273–1281
Su Y, Gong L, Li B, Liu ZQ, Chen DD (2016) Performance evaluation of nanofluid MQL with vegetable-based oil and ester oil as base fluids in turning. Int J Adv Manuf Technol 83(9–12):2083–2089
Rapeti P, Pasam VK, Gurram K, Revuru RS (2018) Performance evaluation of vegetable oil based nano cutting fluids in machining using grey relational analysis—a step towards sustainable manufacturing. J Clean Prod 172(3):2862–2875
Hadi M, Atefi R (2015) Effect of minimum quantity lubrication with gamma-Al2O3 nanoparticles on surface roughness in milling AISID3 steel. Indian J Sci Technol 8:296–300
Sharma N, Syed NA, Ray BC, Yadav S, Biswas K (2019) Wear behaviour of silica and alumina-based nanocomposites reinforced with multi walled carbon nanotubes and graphene nanoplatelets. Wear 418–419:290–304
Denver, CO, US (2004) Experimental comparison of vegetable and petroleum base oils in metalworking fluids using the tapping torque test. Japan-USA Symposium on Flexible Automation; JUSFA
Ozcelik B, Kuram E, Cetin MH, Demirbas E (2011) Experimental investigations of vegetable based cutting fluids with extreme pressure during turning of AISI 304L. Tribol Int 44(12):1864–1871
Maruda RW, Krolczyk GM, Wojciechowski S, Zak K, Habrat W, Nieslony P (2018) Effects of extreme pressure and anti-wear additives on surface topography and tool wear during MQCL turning of AISI 1045 steel. J Mech Sci Technol 32(4):1585–1591
Maruda RW, Krolczyk GM, Feldshtein E, Nieslony P, Tyliszczak B, Pusavec F (2016) Tool wear characterizations in finish turning of AISI 1045 carbon steel for MQCL conditions. Wear 372–373:54–67
Bai X, Li C, Dong L, Yin Q (2019) Experimental evaluation of the lubrication performances of different nanofluids for minimum quantity lubrication (MQL) in milling Ti-6Al-4V. The International Journal of Advanced Manufacturing Technology 101:1–15
Gajrani KK (2020) Assessment of cryo-MQL environment for machining of Ti-6Al-4V. J Manuf Process 60:494–502
Gaurav G, Sharma A, Dangayach G S, Meena ML (2020) Assessment of jojoba as a pure and nano-fluid base oil in minimum quantity lubrication (MQL) hard-turning of Ti-6Al-4V: a step towards sustainable machining. J Clean Prod 272:122553
Bertolini R, Ghiotti A, Bruschi S (2021) Graphene nanoplatelets as additives to MQL for improving tool life in machining Inconel 718 alloy. Wear 1:203656
Li C (2019) Summary of sulfurized additives Synthetic lubricants 46(3):23–26
Bermingham MJ, Kirsch J, Sun S, Palanisamy S, Dargusch MS (2011) New observations on tool life, cutting forces and chip morphology in cryogenic machining Ti-6Al-4V. Int J Mach Tools Manuf 51(6):500–511
Debnath S, Reddy MM, Yi QS (2014) Environmental friendly cutting fluids and cooling techniques in machining: a review. J Clean Prod 15(83):33–47
Li M, Yu TB, Zhang RC, Yang L, Li H, Wang WS (2018) MQL milling of TC4 alloy by dispersing graphene into vegetable oil-based cutting fluid. The International Journal of Advanced Manufacturing Technology 99(5–8):1735–1753
Singh R, Dureja JS, Dogra M, Gupta MK, Mia M, Song QH (2020) Wear behavior of textured tools under graphene-assisted minimum quantity lubrication system in machining Ti-6Al-4V Alloy. Tribol Int 145:106183
Fabrice D, Guillemet F (2002) New water soluble EP additive for environment friendly fluids. Industrial Lubrication & Tribology 54(6):285–290
Singh R, Dureja JS, Dogra M, Gupta MK, Mia M (2019) Influence of graphene-enriched nanofluids and textured tool on machining behavior of Ti-6Al-4V alloy. The International Journal of Advanced Manufacturing Technology 105(1):1685–1697
Babu MN, Anandan V, Muthukrishnan N, Arivalagar AA, Babu MD (2019) Evaluation of graphene based nano fluids with minimum quantity lubrication in turning of AISI D3 steel. SN Appl Sci 1(10):1–15
Cui X, Li CH, Zhang YB, Jia DZ, Zhao YJ (2019) Tribological properties under the grinding wheel and workpiece interface by using graphene nanofluid lubricant. Int J Adv Manuf Technol 104(9–12):3943–3958
Amrita M, Srikant RR, Sitaramaraju AV (2014) Performance evaluation of nanographite-based cutting fluid in machining process. Mater Manuf Processes 29:600–605
Funding
This study was financially supported by the National Natural Science Foundation of China (NSFC) (Grant NO. 51875367), LiaoNing Revitalization Talents Prograrn (Grant NO. XLYC2007011), Natural Science Foundation of Liaoning Province (Grant No. 2020-MS-234), Foundation of Liaoning Educational Committee (Grant No. JYT2020004), China Postdoctoral Science Foundation (Grant No. 2020M670790) and Shenyang Youth Science and technology innovation project (Grant No. RC190072).
Author information
Authors and Affiliations
Contributions
Ben Wang: Conceptualization, Methodology, Writing—Review & Editing. Quanwei Yang: Formal analysis, Writing—Original Draft. Jiawei Deng: Investigation. Ning Hou: Data curation. Xuezhi Wang: Supervision. Minghai Wang: Validation.
Corresponding author
Ethics declarations
Competing interests
The authors declare no competing interests.
Additional information
Publisher's Note
Springer Nature remains neutral with regard to jurisdictional claims in published maps and institutional affiliations.
Rights and permissions
About this article
Cite this article
Wang, B., Yang, Q., Deng, J. et al. Effect of graphene nanoparticles and sulfurized additives to MQL for the machining of Ti-6Al-4 V. Int J Adv Manuf Technol 119, 2911–2921 (2022). https://doi.org/10.1007/s00170-021-08348-w
Received:
Accepted:
Published:
Issue Date:
DOI: https://doi.org/10.1007/s00170-021-08348-w