Abstract
Fiber-reinforced composites/fiber-reinforced polymer is excellent material owning the performance of high strength, high toughness, light weight, good fatigue resistance and shock absorption, and strong designability. It has a wide range of application prospects. The reinforcing fiber makes the cutting of the composites far from easy. When machining of FRP, the high tool wear, defects on machined surface, and poor processing efficiency severely restrict its wide application. Exploring the cutting mechanism of FRP has very important practical significance. In recent years, simulation technology based on discrete element and finite element methods has gradually been applied to the research field of material cutting. This paper summarizes the methods, theories, and conclusions in cutting simulation of fiber-reinforced composites in recent years, and finally puts forward the future focus and development direction of fiber reinforced composite cutting simulation research.
Similar content being viewed by others
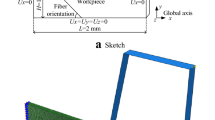
Avoid common mistakes on your manuscript.
1 Introduction
Fiber-reinforced composites/fiber-reinforced polymer (FRP) consists of reinforced fibers, interface phases, and the matrix. The fiber mainly including three shapes including continuous fiber, short fiber, and the whisker, which is the main load-bearing structural unit. The interface is used to change the direction of crack propagation or prevent crack propagation and transfer load as a special buffer area. The matrix is the basic structural unit that forms the shape and rigidity of the composite material, which mainly plays the role of connection and forming [1]. FRP can generally be divided into three categories, carbon fibers, glass fibers, and aramid fibers [2]. This advanced FRP has good physical and mechanical properties with high strength, light weight, shock absorption performance, and large-area integral molding [3], so it has partially replaced metal alloy materials in many fields, especially used widely in aviation, aerospace, and other military fields [4]. Besides, the fields of automobiles, civil construction, medicine, and chemical industry are gradually using FRP as a better substitute [5].
The properties between FRP and most metal materials are mainly different in non-homogeneity and anisotropy. Although FRP can be directly manufactured into complex structural parts by a near-net forming process, however, the secondary machining (e.g., cutting, milling, grinding, drilling) of FRP is employed due to the requirement of geometric dimensions and machined surface quality being high in some sophisticated devices. In view of this, many scholars have made a series of studies on the machining of this kind of composites focusing on the cutting mechanism of FRP.
The cutting force plays an important part in the material cutting process, and it is also the source of various physical phenomena in the cutting process. The cutting heat affects the machined surface quality [6]. In virtue of a large number of experiments, Koplev et al. pointed out that the cutting force is associated with the chip and the tool wear [7]. Hocheng et al. carried out the study of drilling fiber-reinforced thermosets and thermoplastics, and found that one tends to fracture while the other exhibits a lot of plastic deformation. Thermosetting materials are more sensitive to micro-defects, and they also require greater cutting forces [8].
FRP is an anisotropic material, and its cutting forces are related to fiber orientation. Different scholars have studied cutting forces, chip formation modes, and cutting deformation mechanism of fiber direction. Fiber angles are represented by 45° and 135°, and two special dividing lines of 0° and 90°. These 4 different fiber angles are often classified and studied by different scholars. Zhang et al. divided the cutting deformation into three modes: interlayer separation, fiber cutting, and fiber bending [9]. Wern et al. [10] concluded that the cutting force of GFRP (glass fiber-reinforced plastic) is affected by orientation and reinforcement of fiber. Its maximum cutting force occurs at the cutting angle of 90° fiber regardless of the tool geometry [10]. However, Zhang [11] and others believe that the cutting force of unidirectional GFRP materials when the fiber angle being from 0° to 120° increases as the fiber angle increasing but decreases when the fiber angle being from 120° to 180°, which was obtained through orthogonal cutting experiments. For unidirectional graphite/epoxy resin-based layered carbon fiber composites, Wang [12] conducted machining experiments with PCD tool and found that the main cutting force gradually raised as the fiber direction angle increasing until to 90° and then decreased. In cutting process of CFRP, the material deformation mechanism is closely linked with the fiber angle. The shear process inside the interface shear layer has an important influence on the cutting force. The shear deformation and the fracture energy of the interface layer are an important factor of resulting on the workpiece material deformation [13]. For resin-based multidirectional fiber-reinforced composites, the grinding force increases nearly linearly with the increase of the grinding depth [14]. Through the milling experiment of carbon fiber-reinforced composite material, it is concluded that increasing the milling speed, the milling force decreases; when the feed rate increases, the milling force decreases [15]. For surface defects, they always occur at the milling exit. The main reason is tearing, and the tearing area increases as the milling force increases [15]. Different scholars have different opinions on the cutting force behavior of fiber-reinforced composite materials when the fiber angle changes. At present, the change rule of cutting forces in different fiber directions has not yet obtained in a comprehensive and reasonable method.
Cutting heat is also a hot spot in cutting mechanism research. The thermal conductivity of fiber-reinforced composites along the fiber direction is higher than that of vertical direction, so the fiber direction affects the cutting temperature distribution. The cutting heat which was formed by the cutting force and cutting deformation cause deformation of the workpiece and cutting tool. They also change the friction state of the rake face, aggravate the wear of the tool, and affect the machined surface quality.
Temperature also has important influence on the drilling force, and delamination always appears in the area where the cutting heat accumulates, especially at the exit of the machined hole [16]. For machining of CFRP with dry condition at a larger feed rate, when the temperature rises at the interface between the edge and the drilling surface, the friction conditions between the tool and the drilling change significantly [17]. Compared with common structural metal materials such as carbon steel, the overall cutting temperature of CFRP is lower [18], and the maximum machining temperature occurs in the 90° fiber direction. The cutting heat of CFRP is mainly contributed by the frictional heat in the contact area between the workpiece and tool flank face [18]. Brinksmeier et al. [19] used manual thermocouple temperature measurement methods to compare orbital and conventional drilling of CFRP, and according to the hole surface temperature found that the surface quality of the carbon fiber composite material is greatly affected by the cutting temperature. Lower process temperatures can be gained with orbital drilling, while the local temperature peaks damage the surface layer using conventional drilling [19]. In addition to manual thermocouple temperature measurement, infrared fiber optic sensors are also used to measure cutting temperature. The cutting temperature of carbon fiber composite material in the 0° fiber direction is obtained by the optical infrared pyrometer, combined with the calculation of the cutting force, and finally the critical cutting temperature with PCD tools in the 0° direction is obtained [20].
At present, there are few theoretical studies on the cutting temperature in the FRP cutting process. One of the reason is that it is not easy to measure the cutting temperature and there are not many experimental data. The FRP fiber-matrix heat transfer model, the material’s cutting temperature field distribution, and the influence of cutting heat on the machined surface quality and chip morphology are still not satisfactorily answered.
The surface quality of FRP is associated with the cutting force, cutting heat, and cutting parameters. By orthogonal cutting experiments, Cai et al. [18] concluded that the quality and morphology of the machined surface are anisotropic. Su et al. [21] thought that when orthogonal cutting CFRP, as the cutting speed increases, the fiber deformation area decreases before fiber fracture. A turning experiment on GFRP composite materials was conducted by Palanikumar [22]; the feed rate has the greatest effect on the surface roughness on the machining of GFRP composites and the surface roughness fluctuated in different fiber orientation [22]. Using of K10 solid carbide tool end mill for milling of the GFRP composite, the cutting speed has the greatest influence on the surface roughness, followed by the cutting thickness; while in the use of HSS (high speed steel) end mill and brazed end mill, the cutting thickness has the most significant effect [23]. In contrast to traditional drills, a new multi-groove drill bit was designed to drill CFRP [24]. The thrust force will be reduced by 37.45% compared with the original drill bit, and a better surface quality drilled hole was acquired [24]. The most common surface damage in drilling CFRP mainly reflects in delamination, fiber pull-out and uncut fibers, micro-cracks, inappropriate surface roughness, and substrate burning [25]. The ratio of primary drill bit diameter to secondary drill bit diameter affects the delamination factor of the hole exit [26]. Different fiber orientation angles will cause different material deformation and failure modes, so the machined surface quality has a great relationship with the fiber orientation angle. F. Cepero-Mejías observed that there is a great correlation between fiber angle and workpiece damage [27]. When the fiber angle is changed from 30° to 90°, the damage increases significantly [28]. Subsurface damage is also affected by fiber angle. F. Cepero-Mejias pointed out that at small fiber angle, the sub-damage is mainly fragile chip ruptures; on the contrary, the sub-surface is damaged by ductile chip ruptures [28]. Some observations showed that tool rake angle, tool relief angle, cutting thickness, and fiber direction angle all have varying degrees of influence on the CFRP orthogonal cutting process [29–32]. The fiber direction angle has a large effect on the surface quality after processing.
It can be seen from the literature review above in the machining of FRP, due to FRP’s non-homogenous structure, anisotropic mechanical properties, and difficult-to-cut composition phases, that the machinability of FRP is relatively poor, and the processed surface has many defects (Fig. 1). So, the FRP can also be regarded as a kind of difficult-to-machine material. Under the same cutting edge, the tool alternately interacts with the fiber and the matrix. Due to the difference in the mechanical properties of the fiber and the matrix, they are not removed at the same time, which can easily give rise to serious fiber pull-out, interface peeling, surface tearing, and other defects. Besides, the anisotropy of composite materials mainly affects the material removal mechanism of different fiber layup directions. For CFRPs, the in-plane Young’s modulus parallel to the α-axis is approximately 1000 GPa while the Young’s modulus parallel to the γ-axis normal to the basal planes is only 30 GPa [4]. Under different fiber layer angles, there are big differences in the form of fiber damage. The surface processing quality of FRP laminates has significant directionality, and the surface morphology and contour will change with the fiber cutting angle [37]. In addition, the reinforcement phase and matrix of FRP are usually difficult-to-cut materials. For example, the reinforced phase carbon fiber has high strength, high hardness, and brittleness, and it is easy to produce severe tool wear during the cutting process; the matrix material has the characteristics of soft plastic difficult to process, and the material separation process generally experienced large plastic deformation, and affected by high temperature softening and glass transition, which makes the reinforced material lose its proper protection and support, resulting in defects such as delamination, burrs, and tearing.
Compared with metal materials, the relationship between stress and strain of FRP is more complicated. The processing methods of traditional metal materials are not suitable for FRP. In the FRP machining process, we often see severe tool wear and low machining efficiency. In fact, plastic deformation processes such as slip flow almost do not occur in the deformation process of cutting fiber-reinforced composite. As all we know, a huge difference exits between the cutting damage of fiber reinforced materials and metal materials. This difference forces us to propose and establish new models. Based on the research on plastic processing technology, researchers have conducted more extensive study on the cutting mechanism of fiber-reinforced composite materials.
In summary, the study on cutting mechanism of FRP is mainly by feat of the perspective experiments from the aspects of cutting force, surface finish quality, cutting chips, and cutting temperature and material removal mechanism. The relationship between cutting force, cutting temperature, cutting parameters and material properties, workpiece surface quality, and cutting tools has not yet been resolved. In-depth researches on the cutting mechanism of fiber-reinforced composites have far-reaching practical significance for optimizing tool parameters, ensuring machined quality, improving machining efficiency, and reducing machining costs. Besides, for ultrasonic vibration machining and water jet machining, it requires a lot of time to obtain the required parameters from experiments.
FRP cutting is a brittle machining process with large strain and high strain rate. Many factors can influence the cutting force and degree of machining damage, and there are complex and unknown correlations between the influencing factors. As we want to explore the mechanism of cutting FRP, using experimental method is not enough. When cutting process of composite, the experimental conditions are complicated, the test amount is huge, and the cost is high. Besides, it is difficult to rely entirely on macroscopic experiments methods to quantitatively study the cutting mechanism, especially from the microcosmic view.
As the computer technology grows, the numerical solutions such as discrete element and finite element are gradually applied in cutting of fiber-reinforced material. Computer modeling and simulation technology provides a new effective research method for exploring the cutting mechanism. With the aid of computer simulation, the macro- or micro-cutting mechanism can be truly studied in depth. The machining parameters such as feed rate, cutting depth, and cutting speed can be selected reasonably; the tool structure is also optimized. In view of this, in this paper, the work done in simulation of cutting fiber-reinforced composites by relevant scholars based on the collected literature is summarized; and the simulation methods, theories, and conclusions that scholars have obtained and developed in simulation of cutting fiber-reinforced composites are reviewed, and finally, the future focus and development direction of fiber reinforced composite cutting simulation research are proposed.
2 Cutting simulation of fiber-reinforced composite
2.1 Discrete Element Method
Discrete element method (DEM) was proposed in the 1970s and is often used in rock mass engineering and soil particle engineering. Its basic idea is to separate the discontinuity into a collection of rigid elements which makes each rigid element satisfy the equation of motion. An iterative method can be used to solve the equation of motion of each rigid element, and then the overall motion form of the discontinuity can be gained. The discrete element method allows relative movement between elements without satisfying the conditions of continuous displacement and deformation coordination. Discrete elements are based on the discontinuous state of particles, and particle elements defined by specific parameters are assembled to form bulk materials. Discrete element calculation speed is fast, the storage space required is small, and it is especially suitable for solving large displacement and nonlinear problems [38].
Ismail et al. [39] used discrete elements to simulate the microscopic failure mechanism of unidirectional laminated fiber-reinforced composites. The interface strength has an important effect on the transverse tension in FRP. When the interface strength is high, matrix cracking is its main damage [39]. Iliescu et al. [40] adopted the DEM to establish an orthogonal cutting model of carbon fiber-reinforced composite. The discrete element model includes three steps, namely pre-processing, dynamic calculation, and post-processing; and the material properties are defined by the interaction of micro-machined particles, and the different layered carbon fiber models are established by setting the particle geometry-physical parameters and the particle arrangement direction [40]. Newton’s law and integrated algorithm are used to obtain the velocity, acceleration, and position information of the particle at the next moment [40]. Without considering the tool wear and cutting heat conduction, the cutting force and the resistance of cut depth through the discrete element method were obtained, and based on the simulation results, the fiber deformation failure mode and cutting mechanism under different fiber direction angles were analyzed [40]. In the 0° and 45° fiber directions, the simulated cutting force is in accordance with the experimental value, while the cutting force in the 90° fiber angle is higher than the experimental value [40]. The simulation results also show that in the 45° fiber direction, the tool wear is the most serious due to the generation of small chips [40]. Figure 2 [40] shows the discrete element cutting models of 0°, 45°, 90°, and −45° fiber directions. Through the discrete element method simulation, the high degree of compression, bending, and delamination of the fiber can be seen. The DEM is reasonable and feasible to study the cutting mechanism of composite materials.
Chip formation in orthogonal cutting by discrete element simulation for different fiber orientations [40]
2.2 Finite Element Method
Finite element method (FEM) is a numerical solution method that has grown up with the development of computer science. In fact, for the problems that are difficult to obtain analytical solutions in engineering, satisfactory numerical solutions can be obtained when certain accuracy requirements are met. The use of finite element analysis of composite cutting processing can save a lot of time for determining experimental processing parameters, and the results obtained can be correlated and compared with the cutting force and chips obtained in the experiment. Finite element modeling can also discuss and analyze the changes of processing parameters with processing conditions.
At present, the solid modeling methods of fiber-reinforced composite using finite elements include macro-mechanical model and micro-mechanical model. The macro-mechanical model is assumed that the material is an equivalent homogeneous material (EHM) often used to research the cutting force changes and macro-destructive models during the cutting process. The macro-mechanical model is difficult to simulate the detailed chip formation process. Therefore, the results accuracy of the macro-mechanical model needs to be improved. The micro-mechanical model considers the actual size of the material from a microscopic point of view, can simulate the removal mechanism of the material on the microscopic size, and can study the damage and destruction process of the fiber and the matrix. The micro-scale cutting simulation can provide a more in-depth, careful, and rigorous explanation of the macroscopic cutting removal mechanism, and obtain the stress, strain, temperature distribution clouds which are difficult to obtain by other methods. However, the micro-mechanical model requires more calculation and longer calculation time.
2.2.1 Macro-mechanical model
The hypothesis of homogenization is applied in the macro-mechanical model. The composite material is assumed to be uniform. At the same time, it does not distinguish internal components and does not consider the interaction between components. The fiber is implicit in the material and its direction is set by defining the material coordinate system. The macro-mechanical model is mainly used to analyze the change of cutting force and the overall deformation and failure mechanism of materials.
Most finite element models are based on material modeling of continuum, while heterogeneous composite materials cannot be accurately modeled [41]. For the macro-mechanical cutting simulation model, the material failure theory affects the accuracy of the simulation results, which is critical to simulation modeling. The failure theory mainly includes the following: maximum stress, Tsai-Hill, Hashin, Hoffman. Table 1 summarizes common failure theories. Hashin damage criteria [42] are the most popular failure theory. Puck failure theory is an emerging failure criterion developed on the basis of Hashin’s quadratic theory, and its matrix failure criterion is currently recognized as the most accurate criterion. The Puck failure theory can better predict the load-displacement curve, strain field, and failure mode of the large thickness composite laminate during the transverse shear failure process [43].
Orthogonal cutting refers to that the main cutting edge is at right angles relative to the cutting speed direction. Most of the cutting conditions are bevel cutting methods, but in theoretical and experimental research, orthogonal cutting is the simplest way to observe and measure cutting behavior. The majority of finite element simulation models are orthogonal cutting, and the rest models are drilling and milling, as shown in Table 2.
Arola and Ramulu [44] conducted a finite element model of FRP, and by setting the maximum stress and Tsai-Hill failure criteria, respectively, the stress distribution contours of the cutting deformation zone were obtained. The subsurface damage caused by matrix cracking, fiber-matrix peeling, and fiber fracture was obtained by setting different failure criteria [45]. Setting different failure criteria (such as using Hashin failure criteria) can also be used to quantitatively analyze the impact of amount of back-cutting on the cutting force, surface processing quality, and cutting topography when machining CFRP.
Due to the anisotropy of materials, different fiber orientation angles are often used as variables to study the damage mechanism of FRP. Lu et al. [47] analyzed the mechanism of matrix damage and sub-surface damage in cutting carbon fiber-reinforced resin matrix composite with fiber angles of 0° and 90°. The direction of matrix cracking is parallel to the fiber direction after entering stable cutting [47]. Relative to the fiber layup angles of 0°, 45°, and 90°, when the fiber layup is 135°, the CFRP material has the highest stress. Comparing with the milling experiment, the surface quality obtained by the ply angle of 135° is the worst, which verifies the correctness of the simulation conclusion [48]. Based on the Hashin criterion, Ref. [49] established a two-dimensional macro-anisotropic CFRP cutting model. Simulation results show that the fiber angle has large influence on the damage of CFRP under the surface [49]. When increasing the fiber angle, the depth and area of the subsurface damage also increase significantly; the main cause of subsurface damage is the failure of the matrix [49].
The Tsai-Hill failure criterion is often adopted by scholars to establish homogeneous and anisotropic two-dimensional [50] or three-dimensional models [51]. Mahdi and Zhang considered chip breakage, optimized the contact model, and established a two-dimensional cutting model that is consistent with the experimental measurement results [50]. By three-dimensional Tsai-Hill failure criterion, the cutting force/depth resistance value obtained by the 3D macro-finite element cutting model simulation is relatively consistent with the experimental value, and the chip formation mechanism obtained is very consistent with the experimental observation results [51].
F. Cepero-Mejia et al. [52] established a finite element model of CFRP laminates in the 45° direction based on the Hashin criteria of and the Puck criteria. The energy-based linear softening damage propagation was used to trace the crack path under different fracture modes [52]. Four different fracture modes such as shear failure, fiber/matrix peeling, matrix fracture, and fiber micro-buckling have been effectively simulated [52]. The crack path propagation methods under other fiber angles should be further studied in order to provide an effective research method for predicting workpiece processing damage. In addition, Cepero-Mejias [53] performed a finite element simulation of the damage caused by cutting the unidirectional GFRP material based on the Hashin and Puck criteria. In the 0° and 45° directions, the two criteria can predict damage better and consistently, while in the 60° to 90° direction, the prediction accuracy is not good. And this difference may come from the peeling of fiber and matrix [53].
The ultrasonic vibration machining of FRP is beneficial to improve the surface quality. Using finite element model can simulate the ultrasonic vibration machining of FRP. Li et al. [54] applied a forced vibration to the tool at reference point on basis of ordinary machining simulation model, so that the tool got a simple harmonic vibration according to the sinusoidal motion path. Combining the movement of the tool and workpiece, the workpiece collides with the tool at a certain speed, and the simulation machining of carbon fiber-reinforced composite with ultrasonic vibration is acquired [54]. It is found that the damage of the matrix is mainly distributed in the area connecting the tool tip; the damage area of the matrix is significantly reduced in ultrasonic vibration cutting compared with ordinary cutting. The author also established ultrasonic vibration cutting models with different amplitudes and vibration frequencies, and found that increasing the amplitude and frequency, the cutting force decreases, and the damage to the substrate also decreases [54].
Some researchers also have applied finite element to study the drilling this composites. Virtual crack extension (VCE) method [55, 56] and cohesive zone elements (CZE) [57] are often used in layered modeling. The disadvantage of these two methods is that they cannot simulate the progressive destruction of characteristics within and between layers. Zitoune [56] proposed a numerical model considering the tool point geometry calculating thrust forces when drilling unidirectional CFRP, and the numerical results can better inflect the experimental values. Durao et al. [57] established a finite element model for simulating the layered initiation and cutting force in drilling carbon/epoxy composites, and pointed that a linear relationship exists between the stress and relative displacement of the interface element homology point before the damage starts to grow [57]. Combining the feed rate and cutting speed experiments, a 3D cutting simulation model of carbon fiber composite was developed to obtain the drilling force change trend, so the model can be used to predict the cutting force and torque, and also be optimized the process parameters [58]. Based on the response surface method, An et al. [59] used the Hashin failure criterion and took the cutting speed, feed rate, and drill tip angle as design variables, and established a prediction model for the axial force of carbon fiber composite drilling. The effects of three variables on the axial force were comprehensively analyzed based on the high-line diagram, and a theoretical basis for the reasonable formulation of drilling processing parameters in actual production provides was provided [59]. Yang et al. [60] analyzed the cutting force by establishing a two-dimensional finite element simulation model in milling CFRP. When the fiber angle is between 0° and 90°, the cutting force shows a decreasing trend; while the fiber direction angle increases from 90° to 180°, an increasing trend is found [60]. The cutting force increases as the milling speed and feed per tooth increase, and decreases with the increase of tool rake angle [60].
In summary, the macro-mechanical model can simulate cutting behavior. The damage of the matrix and fiber can also be obtained. The tendency of cutting force which obtained by the macro-mechanical model is consistent with the experiment, but the accuracy of cutting force prediction needs to be improved. The current failure theories rarely consider the effect of cutting heat, and most of models do not take the interface layer into its model, so the prediction accuracy of the macro-mechanical model can be further improved.
2.2.2 Micro-mechanical model
Nayak et al. [61] proposed a microscopic modeling method and applied it to cutting simulation research of UD-GFRP. In this model, in the direction of fiber longitudinal axis occurs the maximum-in-plane principal stress. In Ref. [62], a finite element cutting simulation model was established for glass fiber and carbon fiber-reinforced composite materials. The fiber reinforcement and the matrix were separately modeled and assigned with their respective material properties. The interface phase was simulated by cohesive elements, and successfully predicted the damage during processing. Comparison of experimental and simulation results, the depth of debonding and fiber damage decreased as the fiber orientation increases [62].
Based on the same modeling mind, a three-dimensional orthogonal cutting finite element model was developed [63]. Under the condition of a rake angle of 20°, comparing numerical simulations results and experimental data at different fiber angles to obtain cutting force, it is found that they have good consistency. The relationship between the fiber angle and the delamination length at different rake angles of 5°, 10°, 15°, and 20° is obtained through simulation method, and the mechanism of material removal and fiber destruction in different fiber directions can be explained satisfactorily to a certain extent through micro-mechanical models [63]. A cutting model for CFRP established by Calzada et al. can accurately predict fiber failure [64]. Rentsch et al. [65] established a micro-process modeling based on implicitly defined anisotropic continuous fibers and an explicit micro-cutting model of fiber matrix (Fig. 3 [65]). The simulated results are consistent with the cutting removal mechanism from experiment. The trend of the simulated cutting force in the fiber direction at 0° and 45° fiber direction is correct, but the cutting force and thrust force are lower than experimental values (Fig. 4 [65]). By feat of the maximum principal stress criterion to simulate fiber failure, Ref. [66] established orthogonal cutting models for unidirectional CFRP and GFRP composites. The simulation results can more accurately predict the cutting force during the cutting process, and the failure of the fiber is a combination of extrusion and bending [66]. As the direction angle of the fiber decreases, the effect of bending becomes more significant [66]. In Ref. [67], a micro-cutting finite element model was performed though setting different material constitutive and material failure criteria in four different fiber angles. The CFRP failure in the 0° fiber direction is mainly interface cracking and fiber breaking; the failure in the cutting 45° and 90° fiber directions is mainly the intrusion of the tool, and a large number of fiber bundles are broken; the 135° fiber direction causes fiber fracture and cracks along the fiber direction. The fiber fracture point is below the blade; the damage of the matrix comes from the cutting of the tool and the deformation and extrusion of the fiber bundle [67].
Implicit macro-cutting model and explicit micro-cutting model [65]
Comparison of cutting force and thrust force in 0 ° and 90 ° fiber angles [65]
The micro-mechanical model can simulate the process of fiber-matrix fracture, interface cracking and evolution during FRP cutting under different fiber angles at the micro-level, and can also analyze and study the cutting force. Based on orthogonal cutting model of CFRP laminate, the main cutting force first increases and then decreases when the fiber angle increases, and reaches the maximum at 90° [68]. The chip formation mechanism, the cutting damage, and the effect of the machining parameters on cutting force are obtained by the two-dimensional finite element cutting model of FRP [69]. The chip morphology, damage mode, and cutting force of fiber-reinforced composites have obvious anisotropy [69]. The main cutting force increases as the cutting speed, cutting depth, tool rake angle, tool tip radius, and fiber diameter increase, and decreases as the tool clearance angle increase [69]. J. de Freese et al. [70] established a two-dimensional orthogonal unidirectional CFRP micro-cutting model, and used the Johnson-Cook failure criteria to compare the deformation and damage mechanisms of the workpiece at different cutting speeds (1.25m/s and 5m/s). At a cutting speed of 1.25m/s, small cracks appear in the matrix, while at a cutting speed of 5m/s, long cracks appear in the interface layer between the fiber and the matrix. Comparing the scanning electron microscope (SEM) images, the simulation results are consistent with the real microstructure [70]. The changing of cutting force and its influence on the machining process by setting different cutting speeds and axial depth of cut as variables was studied in Ref. [71], and it is found that the cutting force increased with the cutting speed increasing and the overall fluctuation ranges of the cutting force showed a small increasement [71]. In the cutting process of different fiber directions, the fiber deformation, fiber stress transfer, matrix stress transfer, and cohesive failure at 90° cutting are medium compared with the fiber direction of 45° and 135° [71].
A three-dimensional finite element micro-cutting model for CFRP was built as shown in Fig. 5 [72].
CFRP cutting process. Cut-in (a), cutting process (b), and cut-out (c) [72]
Comparing different cutting speeds, increasing the cutting speed can improve the quality of the machined surface. The reason is that at lower speeds, the matrix will produce more damage (Fig. 6 [72]), and some fibers are compressed by the cutter and nearby fibers, causing bending deformation, and breaking below the processed surface [72]. Increasing the speed can reduce the contact time, more fibers are directly broken by shear, and the surface quality after processing is better. It is also concluded through simulation that the processing quality in the 135° direction is the worst, with more defects such as fiber exposure and interface cracking. The processing quality of 0° and 90° fiber direction is better [72].
Matrix deformations at different cutting speeds: 1047.2 mm/s (a) and 4188.8 mm/s (b) [72]
Qi deeply studied the three-dimensional multiphase micro-drilling behavior of CFRP [73]. Different fiber angles lead to different deformation and failure modes of the material, resulting in different chip formation processes and forms, cutting forces, and surface quality; the fiber direction angle has a qualitative effect on the cutting behavior [73].
The comparison between the micro-topography image of the experimental workpiece by SEM (scanning electron microscope) and the simulation result shows that the micro-mechanical model can better reveal the mesoscopic cutting behavior [74]. When the fiber angle θ is 0°, the micro units that do not participate in bending fracture are rolled and crushed by the flank surface, thereby causing incomplete damage to the matrix and fibers; when the fiber angle θ is 45°, a larger area of the matrix will be destroyed during cutting; thus, a relatively tidy surface is formed and the surface quality is better after processing; when the fiber angle θ is 90°, the rounded corners of the tool tip first squeeze the CFRP, causing the matrix to fail, and then partial fiber compression failure occurs; when the fiber angle θ is 135°, the rake face first contacts the CFRP, and the unit is contacted and squeezed by the rake face and then bends to break, and finally forms chips [74]. This model can make reasonable analysis, prediction, and interpretation of the surface quality of the workpiece after machining, and provide guidance for improving tool geometric parameters and cutting process optimization.
The heat transfer mechanism in cutting FRP is currently unclear. Scholars have explored and researched cutting heat by establishing finite element models. By defining the fiber, interface phase, matrix material model, and damage evolution, Xiao et al. [75] developed a CFRP micro-finite element model, and simulated the material removal process under the coupled thermal and mechanical effects. Through the simulation, the change of cutting temperature of CFRP is mainly concentrated at the position where the cutting edge of the tool contacts the material, and part of the cutting heat is taken away with the chip flow [75]. The peak cutting temperature appears in the 90° fiber direction. This is because the complicated material fracture is most likely to occur at the 90° fiber direction, which is affected by both bending and shearing [75]. In the 0° fiber direction, there produces the lowest cutting temperature because the material mainly undergoes compression and bending fracture, and the fiber peels off from the resin surface, which results in taking away most of the heat. Besides, the surface fiber is exposed after machining, and the heat is easily dispersed, so the thermal stress under the surface is not deep [75]. The simulation results were compared and verified with the chip morphology and the micro-morphology of the machined surface, and the chip morphology, surface quality, and cutting temperature of the CFRP material are obviously affected by the fiber angle [75].
Xu et al. [76] established a thermal-mechanical coupled microstructure model to study the orthogonal cutting process of FRP with ultrasonic vibration. The model is composed of a three-phase microscopic layer of matrix, fiber, and interface, and an isotropic material layer (Fig. 7 [76]). The cutting temperature has a small contribution to the cutting force, but it has an important influence on the material removal process [76]. Cutting heat is always spread along the front of the tool. High-frequency vibration not only reduces the contact time between the workpiece and the tool, but also speeds up the removal of chips, thereby reducing heat generation and accumulation. Therefore, ultrasonic vibration machining can keep the temperature of the tool and workpiece below the glass transition temperature of matrix material. However, if the feed speed is higher than the maximum vibration speed, the function of ultrasonic vibration-assisted machining becomes limited [76].
The micro-finite element model of cutting FRPs [76]
In addition to general cutting simulation, scholars applied finite element technology to analyze other machining and cutting behaviors of FRP. Li et al. [77] established a 3D finite element modeling for multiple-pass cutting of CFRP (Fig. 8 [77]), and studied their effects on the surface quality. Compared with a single pass processing, multiple passes cutting can significantly improve the quality of the machined surface; and the cutting force of multiple passes is significantly lower than that of a single pass [77]. The fiber fracture length obtained by cutting is increased by 40% compared with a single pass, and the fiber pull-out depth is also increased by 63% [77]. Process parameters can be optimized through multiple cutting simulations to ensure the best surface quality of the workpiece. Multi-pass cutting provides a new focus for people to study the cutting mechanism of CFRP, and it also provides meaningful guidance for industrial CFRP machining.
a The 3D multiple-pass cutting model of CFRP. b The fiber, the interface, and the matrix element. c The distribution of fiber. d The micro-structure of CFRP observed in experiments [77]
In addition to the finite element model, a 3D micro-mechanical model using SPH (smoothed particle hydrodynamics) method was established. SPH can better predict the value of cutting force, where in the 0° fiber angle, its predicted cutting force is 30% more accurate than finite element [78]. Compared with high-speed camera images, SPH can also observe the peeling behavior at the boundary of the fiber matrix.
Based on the references used in this paper, there also exits some problems in the process of cutting simulation of fiber-reinforced polymer, the most pivotal of which is the FRP cutting simulation model being difficult to well simulate the cutting process in the real machining environment. On the one hand, the tool is often set as a rigid body in the model and does not wear out in most conditions, which is different from the real situations. In fact, the rake angle of the tool and the blunt radius of the cutting edge of the tool have an important influence on the removal mechanism of FRP materials. On the other hand, composite material simulation models should more consider the influence of thermal effects on cutting process, while a few models have relatively simple research on thermal-mechanical coupling models. Future research work needs to reconstruct and optimize the existing material constitutive based on stress failure, and incorporate the fiber-matrix anisotropic heat transfer characteristics and thermal diffusion, thermal softening, and thermal degradation effects inside the constitutive equation. In addition, mass scaling is often used in micro-mechanical models to speed up calculations and save calculation costs. However, with the enrichment of the FRP constitutive equations, this puts higher requirements on the calculation capabilities of computers, which also requires the improvement of the theory and the algorithm.
3 Conclusions and prospects
-
(1)
The cutting simulation of fiber-reinforced composites has made great progress in the past 20 years. Discrete element and finite element methods are effective, simple, economical, and feasible methods to explore the cutting mechanism of composite materials. The prediction of cutting force, mechanism of material deformation, damage of fibers and matrix, and the surface quality after machining can be obtained through both methods in a certain accuracy and reasonable explanation.
-
(2)
The cutting simulation model changes from two-dimensional to three-dimensional, which can provide more accurate material and tool information. The three-dimensional model provides the possibility to observe and study the wearing of the tool, the generation, and flow of chip. With the continuous advancement of computer technology, there will be more 3D simulation-based cutting models in the future; more parameters or conclusions and even new discoveries should be observed.
-
(3)
In the cutting simulation model, the material failure model and friction model need to be further improved. The material model should be more accurate. At the same time, the friction situation during processing is extremely complicated. How to accurately express the friction situation during processing through the model is still a difficult problem.
-
(4)
FRP cutting simulation is very insufficient in the research on cutting heat. In-depth study of cutting heat can be of great significance for optimizing processing procedures, increasing tool life and increasing cutting speed. In addition, exploring the cutting simulation of special machining such as high-pressure water jet machining and electrical discharge machining is the focus of future research.
-
(5)
The tool wear, cutting parameters, and the distribution of rough and finishing allowances should be simulated at the same time, and the optimized processing technology under different optimization goals can be obtained. An optimized cutting parameter database should be established by the target optimization algorithm.
Change history
08 September 2021
A Correction to this paper has been published: https://doi.org/10.1007/s00170-021-07952-0
References
Cheng LF, Zhang LT, Mei H (2019) Strengthening and toughening of ceramic matrix composites and application basis. Chemical Industry Press, Beijing
Zhang H, Jin X (2017) Research and application of fiber reinforced composite (FRP). China Water & Power Press, Beijing, p 4
Xin ZJ (2015) Advanced composite material processing technology and examples. Chemical Industry Press, Beijing, pp 4–5
Soutis C (2005) Fibre reinforced composites in aircraft construction. Prog Aerosp Sci 41(2):143–151. https://doi.org/10.1016/j.paerosci.2005.02.004
Ye LP, Feng P (2005) Applications and development of fiber-reinforced polymer in engineering structures. Chin Civil Eng J 03:24–36. https://doi.org/10.3321/j.issn:1000-131X.2006.03.004
Chen M, Xu JY, An QL (2019) Machining theory and application techniques for CFRP composites and multilayer stacks. Shanghai Scientific & Technical Publishers, Shanghai, pp 1–8
Koplev A, Aa L, Vorm T (1983) The cutting process, chips, and cutting forces in machining CFRP. Composites 14(4):371–376. https://doi.org/10.1016/0010-4361(83)90157-X
Hocheng H, Puw HY (1992) On drilling characteristics of fiber-reinforced thermoset and thermoplastics. Int J Mach Tools Manuf 32(4):583–592. https://doi.org/10.1016/0890-6955(92)90047-K
Zhang HJ, Chen WY, Chen DC (2014) Study on cutting mechanism of carbon fiber reinforced plastics. Aeronaut Manuf Technol 7:58–60. https://doi.org/10.3969/j.issn.1671-833X.2004.07.009
Wern CW, Ramulu M (1997) Influence of fibre on the cutting stress state in machining idealized glass fibre composite. J Strain Anal Eng Des 32(1):19–27. https://doi.org/10.1243/0309324971513184
Zhang XL, Yan L, He HM, Luo YH, Zhang H (2011) Study on the orthogonal cutting technologies of GFRP. Mater Rev 25(10):59–61
Wang DH, Ramula M, Arola D (1995) Orthogonal cutting mechanism of graphite/epoxy composite, part1: unidirectional laminate. Int J Mach Tools Manuf 35(12):1623–1368. https://doi.org/10.1016/0890-6955(95)00015-P
Song CL, Jin XL (2020) Shearing-buckling mechanism in orthogonal cutting of unidirectional carbon fiber reinforced polymer. J Mater Process Technol 280:116612. https://doi.org/10.1016/j.jmatprotec.2020.116612
Hu NS, Zhang LC (2003) A study on the grindability of multidirectional carbon fibre reinforced plastics. J Mater Process Technol 140(1-3):152–156. https://doi.org/10.1016/S0924-0136(03)00704-0
Liu HW, Cheng Y, Su F (2014) Experimental research on milling forming slot of CFRP. Mach Tool Hydraul 42(19):38–41. https://doi.org/10.3969/j.issn.1001-3881.2014.19.010
Jia ZY, Chen C, Wang FJ, Zhang C (2020) Analytical study of delamination damage and delamination free drilling method of CFRP composite. J Mater Process Technol 282:116665. https://doi.org/10.1016/j.jmatprotec.2020.116665
Karpat Y, Karagüzel U, Bahtiyar O (2020) A thermo-mechanical model of drill margin-borehole surface interface contact conditions in dry drilling of thick CFRP laminates. Int J Mach Tools Manuf 154:103565. https://doi.org/10.1016/j.ijmachtools.2020.103565
Cai XJ, Qiu KX, Wang CD, Ming WW, An QL, Chen M (2014) Study on anisotropic behaviors in cutting of aviation high-strength CFRP materials with unidirectional laminate structure. J Nanjing U Aeronaut Astronautics 46(5):684–693. https://doi.org/10.3969/j.issn.1005-2615.2014.05.004\
Brinksmeier E, Fangmann S, Rentsch R (2011) Drilling of composites and resulting surface integrity. CIRP Ann Manuf Technol 60(1):57–60. https://doi.org/10.1016/j.cirp.2011.03.077
Sreejith PS, Krishnamurthy R, Malhotra SK, Narayanasamy K (2000) Evaluation of PCD tool performance during machining of carbon/phenolic ablative composites. J Mater Process Technol 104(1-2):53–58. https://doi.org/10.1016/S0924-0136(00)00549-5
Su YL (2019) Effect of the cutting speed on the cutting mechanism in machining CFRP. Compos Struct 220:662–676. https://doi.org/10.1016/j.compstruct.2019.04.052
Palanikumar K, Karunamoorthy L, Karthikeyan R (2006) Assessment of factors influencing surface roughness on the machining of glass fiber-reinforced polymer composites. Mater Des 27(10):862–871. https://doi.org/10.1016/j.matdes.2005.03.011
Prashanth ISNVR, Ravi Shankar DV, Manjoor Hussain M, Ramana Reddy D (2017) Performances of different mill cutters in machining of GFRP Composite Laminates. Mater Today: Proc 4(2):2800–2805. https://doi.org/10.1016/j.matpr.2017.02.159
Zhen Y, Li CP, Qiu XY, Park KM, Ko TJ (2020) Study on damage in carbon fiber reinforced plastic drilling using step cutting mechanism drill. J Alloys Compd 826:154058. https://doi.org/10.1016/j.jallcom.2020.154058
Geier N, Davim JP, Szalay T (2019) Advanced cutting tools and technologies for drilling carbon fibre reinforced polymer (CFRP) composites: a review, Composites Part A. Compos A: Appl Sci Manuf 125:105552. https://doi.org/10.1016/j.compositesa.2019.105552
Qiu XY, Li PN, Li CP, Niu QN, Chen AH, Ouyang PR, Ko TJ (2018) Study on chisel edge drilling behavior and step drill structure on delamination in drilling CFRP. Compos Struct 203:404–413. https://doi.org/10.1016/j.compstruct.2018.07.007
Cepero-Mejías F, Curiel-Sosa JL, Blázquez A, Yu TT, Kerrigan K, Phadnis VA (2020) Review of recent developments and induced damage assessment in the modelling of the machining of long fibre reinforced polymer composites. Compos Struct 240:112006. https://doi.org/10.1016/j.compstruct.2020.112006
Cepero-Mejías F, Curiel-Sosa JL, Zhang C, Phadnis VA (2019) Effect of cutter geometry on machining induced damage in orthogonal cutting of UD polymer composites: FE study. Compos Struct 214:439–450. https://doi.org/10.1016/j.compstruct.2019.02.012
Karpat Y, Bahtiyar O, Değer B (2012) Mechanistic force modeling for milling of unidirectional carbon fiber reinforced polymer laminates. Int J Mach Tools Manuf 56:79–93. https://doi.org/10.1016/j.ijmachtools.2012.01.001
Karpat Y, Bahtiyar O, Değer B, Kaftanoğlu K (2014) A mechanistic approach to investigate drilling of UD-CFRP laminates with PCD drills. CIRP Ann Manuf Technol 63(1):81–84. https://doi.org/10.1016/j.cirp.2014.03.077
Che DM, Saxena I, Han PD, Guo P, Ehmann KF (2014) Machining of carbon fiber reinforced plastics/polymers: a literature review. J Manuf Sci Eng 136(3):034001. https://doi.org/10.1115/1.4026526
Soussia AB, Mkaddem A, El Mansori M (2014) Rigorous treatment of dry cutting of FRP-Interface consumption concept: a review. Int J Mech Sci 83:1–29. https://doi.org/10.1016/j.ijmecsci.2014.03.017
Mortell DJ, Tanner DA, McCarthy CT (2016) An experimental investigation into multi-scale damage progression in laminated composites in bending. Compos Struct 149:33–40. https://doi.org/10.1016/j.compstruct.2016.03.054
Pinho ST, Robinson P, Iannucci L (2006) Fracture toughness of the tensile and compressive fibre failure modes in laminated composites. Compos Sci Technol 66(13):2069–2079. https://doi.org/10.1016/j.compscitech.2005.12.023
Faraz A, Biermann D, Weinert K (2009) Cutting edge rounding: an innovative tool wear criterion in drilling CFRP composite laminates. Int J Mach Tools Manuf 49(15):1185–1196. https://doi.org/10.1016/j.ijmachtools.2009.08.002
Dong DJL, Pomarède P, Chehami L, Locquet A, Meraghni F, Declercq NF, Citrin DS (2018) Visualization of subsurface damage in woven carbon fiber-reinforced composites using polarization-sensitive terahertz imaging. NDT E Int 99:72–79. https://doi.org/10.1016/j.ndteint.2018.07.001
Wang CY, Wen L, Ming WW, An QL, Chen M, Zhang HZ (2015) Research progress in milling of carbon fiber reinforced polymer. Aeronaut Manuf Technol (14):76–80. https://doi.org/10.16080/j.issn1671-833x.2015.14.076.html
Liu KX, Gao LT (2003) A review on the discrete element method. Adv Mech 33(4):483–490. https://doi.org/10.3321/j.issn:1000-0992.2003.04.005
Ismail Y, Sheng Y, Yang D, Ye J (2015) Discrete element modelling of unidirectional fibre reinforced polymers under transverse tension. Compos Part B 73:118–125. https://doi.org/10.1016/j.compositesb.2014.12.024
Iliescu D, Gehin D, Iordanoff I, Girot F, Gutiérrez ME (2010) A discrete element method for the simulation of CFRP cutting. Compos Sci Technol 70(1):73–80. https://doi.org/10.1016/j.compscitech.2009.09.007
Wang DZ, Wan L, Wu SJ (2018) Research on Metal Cutting Mechanism Based on Finite Element Method. Publishing House of Electronics Industry, Beijing, p 9
Hashin Z (1981) Fatigue failure criteria for unidirectional fiber composites. ASME J Appl Mech 48(4):846–852. https://doi.org/10.1115/1.3157744
Jia LY, Liao BB, Yu L, Jia YM, Li M (2019) Failure analysis of composite laminates with Puck’s theory under transverse shear load. Acta Mater Compos Sin 36(10):2286–2293. https://doi.org/10.13801/j.cnki.fhclxb.20190226.002
Arola D, Ramulu M (1997) Orthogonal cutting of fiber-reinforced composites: a finite element analysis. Int J Mech Sci 39(5):597–613. https://doi.org/10.1016/S0020-7403(96)00061-6
Lasri L, Nouari M, El Mansori M (2009) Modelling of chip separation in machining unidirectional FRP composites by stiffness degradation concept. Compos Sci Technol 69(5):684–692. https://doi.org/10.1016/j.compscitech.2009.01.004
Xiong WL, Dai BY, Shang JL, Wang WW (2014) Finite element simulations on cutting process for carbon fiber composite. Ordnance Mater Sci Eng 37(1):86–89. https://doi.org/10.14024/j.cnki.1004-244x.2014.01.009
Lu D, Li ZK, Rong YM, Shu R (2014) Cutting simulation of carbon fiber reinforced resin matrix composite material based on macroscopic anisotropy. Acta Mater Compos Sin 31(3):584–590. https://doi.org/10.13801/j.cnki.fhclxb.2014.03.008
Qin XD, Li YH, Wang B, Ji CH, Guo CY, Wang H, Xin HG (2016) Simulation of effect of fiber direction on cutting process of CFRP. Mech Sci Technol Aerosp Eng 35(3):472–476. https://doi.org/10.13433/j.cnki.1003-8728.2016.0326
Yin JW, Jia ZY, Wang FJ, Chen C, Zhang BY (2016) FEM Simulation analysis of subsurface damage formation based on continuously cutting process of CFRP. J Mech Eng 52(17):58–64. https://doi.org/10.3901/JME.2016.17.058
Mahdi M, Zhang LC (2001) A finite element model for the orthogonal cutting of fiber-reinforced composite materials. J Mater Process Technol 113(1–3):373–377. https://doi.org/10.1016/S0924-0136(01)00675-6
Venu Gopala Rao G, Mahajan P, Bhatnagar N (2008) Three-dimensional macro-mechanical finite element model for machining of unidirectional-fiber reinforced polymer composites. Mater Sci Eng A 498(1):142–149. https://doi.org/10.1016/j.msea.2007.11.157
Cepero-Mejias F, Curiel-Sosa JL, Kerrigan K, Phadnis VA (2019) Chip formation in machining of unidirectional carbon fibre reinforced polymer laminates: FEM based assessment. Procedia CIRP 85:302–307. https://doi.org/10.1016/j.procir.2019.09.005
Cepero-Mejias F, Phadnis VA, Curiel-Sosa JL (2019) Machining induced damage in orthogonal cutting of UD composites: FEA based assessment of Hashin and Puck criteria. Procedia CIRP 82:332–337. https://doi.org/10.1016/j.procir.2019.04.241
Li ZK (2014) Study of cutting experiment and simulation of carbon fiber reinforced composites. Nanchang Hangkong University, Nanchang
Zitoune R, Collombet F, Lachaud F, Piquet R, Pasquet P (2005) Experiment–calculation comparison of the cutting conditions representative of the long fiber composite drilling phase. Compos Sci Technol 65(3-4):455–466. https://doi.org/10.1016/j.compscitech.2004.09.028
Zitoune R, Collombet F (2007) Numerical prediction of the thrust force responsible of delamination during the drilling of the long-fibre composite structures. Compos A: Appl Sci Manuf 38(3):858–866. https://doi.org/10.1016/j.compositesa.2006.07.009
Durã LMP, de Moura MFSF, Marques AT (2008) Numerical prediction of delamination onset in carbon/epoxy composites drilling. Eng Fract Mech 75(9):2767–2778. https://doi.org/10.1016/j.engfracmech.2007.03.009
Phadnisl VA, Roy A, Silberschmidt VV (2012) Finite element analysis of drilling in carbon fiber reinforced polymer composites. J Phys Conf Ser 382:1–7. https://doi.org/10.1088/1742-6596/382/1/012014
An LB, Zhang YX (2018) Simulation and prediction of thrust force for drilling process of CFRP. Mech Sci Technol Aerosp Eng 37(10):1551–1558. https://doi.org/10.13433/j.cnki.1003-8728.20180078
Yang ZC, Yang FJ, Xiao JM, Yuan ZY, Li Y (2019) Establishment of finite element model for milling CFRP and simulation analysis of cutting forces. Aerosp Mater Technol 49(03):36–40. https://doi.org/10.12044/j.issn.1007-2330.2019.03.007
Nayak D, Bhatnagar N, Mahajan P (2005) Machining studies of UD-FRP composites part 2: Finite element analysis. Mach Sci Technol 9(4):503–528. https://doi.org/10.1080/10910340500398183
Dandekar CR, Shin YC (2008) Multiphase finite element modeling of machining unidirectional composites: prediction of debonding and fiber Damage. J Manuf Sci Eng 130. https://doi.org/10.1115/1.2976146
Ganesh C (2010) Orthogonal machining of uni-directional carbon fiber reinforced polymer composites. Wichita State University, Wichita
Calzada KA, Kapoor SG, DeVor RE, Samuel J, Srivastava AK (2012) Modeling and interpretation of fiber orientation-based failure mechanisms in machining of carbon fiber-reinforced polymer composites. J Manuf Process 14(2):141–149. https://doi.org/10.1016/j.jmapro.2011.09.005
Rentsch R, Pecat O, Brinksmeier E (2011) Macro and micro process modeling of the cutting of carbon fiber reinforced plastics using FEM. Procedia Eng 10:1823–1828. https://doi.org/10.1016/j.proeng.2011.04.303
Venu Gopala Rao G, Mahajan P, Bhatnagar N (2007) Micro-mechanical modeling of machining of FRP composites–cutting force analysis. Compos Sci Technol 67(3-4):579–593. https://doi.org/10.1016/j.compscitech.2006.08.010
Liu XP, Li PN, Li SJ, Niu QL, Qiu XY (2019) Microscopic cutting mechanism of unidirectional carbon fiber reinforced plastics based on zero thickness cohesive element. Aerosp Mater Technol 49(5):22–26. https://doi.org/10.12044/j.issn.1007-2330.2019.05.005
Gao HQ, Jia ZY, Wang FJ, Su YL, Zhu HJ (2016) Mesoscopic failure of CFRP based on mesoscopic simulation modeling. Acta Mater Compos Sin 33(4):758–767. https://doi.org/10.13801/j.cnki.fhclxb.20150907.003
Guo FF, Xiao JZ (2017) Study on cutting simulation of fiber reinforced composite materials based on three phase microstructure. Tool Eng 51(6):26–30
De Freese J, Holtmannspötter J, Höfer P (2019) End milling as a surface pretreatment for adhesive bonding of CFRP – new approaches for root cause identification of reduced bond line performance. Procedia CIRP 85:230–236. https://doi.org/10.1016/j.procir.2019.09.037
Chen N (2015) Study on simulation and experiment of micro cutting of micro cutting of fiber reinforced plastics composites. Harbin Institute of Technology, Harbin
Liu HT, Xie WK, Sun YZ, Zhang JY, Chen N (2018) Investigations on micro-cutting mechanism and surface quality of carbon fiber-reinforced plastic composites. Int J Adv Manuf Technol 94:3655–3664. https://doi.org/10.1007/s00170-017-1110-7
Qi ZC (2015) Drilling force modeling and delamination suppression strategy analysis of CFRP-metal stacks. Northwestern Polytechnical University, Xi’an
Qi ZC, Liu SN, Cheng H, Meng QX, Li Y (2016) Research on the mesoscopic cutting mechanism of CFRP based on three-dimensional multiphase finite element models. J Mech Eng 52(15):170–176. https://doi.org/10.3901/JME.2016.15.170
Xiao JZ (2018) Mechanics modelling and optimization of technological parameters for cutting process of CFRP composites. Zhejiang University, Hangzhou
Xu WX, Zhang LC (2019) Heat effect on the material removal in the machining of fibre-reinforced polymer composites. Int J Mach Tools Manuf 140:1–11. https://doi.org/10.1016/j.ijmachtools.2019.01.005
Li HN, Wang JP, Wu CQ, Zhao YJ, Xu J, Liu XL, Zhu WQ (2020) Damage behaviors of unidirectional CFRP in orthogonal cutting: a comparison between single- and multiple-pass strategies. Compos Part B 185:107774. https://doi.org/10.1016/j.compositesb.2020.107774
Abena A, Essa K (2019) 3D micro-mechanical modelling of orthogonal cutting of UD-CFRP using smoothed particle hydrodynamics and finite element methods. Compos Struct 218:174–192. https://doi.org/10.1016/j.compstruct.2019.03.037
Funding
This study was funded by the National Natural ScienceFoundation of China (grant numbers 51505434), Scientific and Technological Project of Henan Province (grant number 202102210275); the Young Backbone Teacher Cultivation Plan for Higher Education of Henan University (grant number 2020GGJS129); the Young Talents Lifting Project of Henan Province (2019HYTP034); and the Scientific and Technological Innovation Team of Colleges and Universities in Henan Province in 2020 (grant number 20IRTSTHN015).
Author information
Authors and Affiliations
Contributions
Jinguang Du: writing original draft. Miao Geng: writing original draft and editing.
Wuyi Ming: writing guidance. Wenbin He: guiding framework of paper and check original draft. Jun Ma: check original draft.
Corresponding author
Ethics declarations
Ethics approval
Not applicable.
Consent to participate
Not applicable.
Consent for publication
Not applicable.
Competing interests
The authors declare no competing interests.
Additional information
Publisher’s note
Springer Nature remains neutral with regard to jurisdictional claims in published maps and institutional affiliations.
The original online version of this article was revised: There are two more text marks in Fig.1(d) compared with the original Fig.9 in Ref. [36], but themselves are essentially the same. Because the Fig.1(d) is obtained from other article in which the Fig.1(d) is also cited from Fig.9 in Ref. [36]. We had to obtain copyright of Fig.9 from the original Ref. [36], but we omit to replace the Fig.1(d) with the original and unmarked Fig.9 in Ref. [36]. The Fig.1(d) in this article should be Fig.9 cited the original Ref. [36], not the current one.
Rights and permissions
About this article
Cite this article
Du, J., Geng, M., Ming, W. et al. Simulation machining of fiber-reinforced composites: A review. Int J Adv Manuf Technol 117, 1–15 (2021). https://doi.org/10.1007/s00170-021-07531-3
Received:
Accepted:
Published:
Issue Date:
DOI: https://doi.org/10.1007/s00170-021-07531-3