Abstract
This paper presents results of experiments performed to establish effect of controlling magnetic fields on refinement degree of structure of deposited metal and weld. Electric arc surfacing was performed on plates made from steel VMSt3sp without and with action of sign changing longitudinal magnetic field with frequency of 3 Hz. Analysis of microstructures of deposited metal showed that influence of controlling longitudinal magnetic field positively affects its structure. In addition, it also increases toughness of deposited metal. Experiments were carried out on welding butt joint of plates 4 mm thick made of steel 12H18N10T with Sw-06H19N9T wire 3 mm in diameter under influence of sign changing transverse magnetic field with frequency of 5 Hz. Analysis of microstructure of welds showed that effect of controlling transverse magnetic field leads to refinement of weld metal grain by almost twice that should lead to increase of weld metal yield strength and improve service characteristics of weld and welded joint.
Access provided by Autonomous University of Puebla. Download conference paper PDF
Similar content being viewed by others
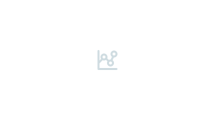
Keywords
- Electric arc welding
- Electric arc surfacing
- Longitudinal magnetic field
- Transverse magnetic field
- Magnetic field induction
- Weld
- Crystallization of weld pool
1 Introduction
Grinding of weld structural components leads to increase of yield strength of weld metal and service characteristics of weld and welded joint. It is perspective to use external (controlling) magnetic fields to control processes of melting of electrode and base metals as well as process of crystallization of weld pool metal. Their usage does not require significant changes of standard equipment and surfacing (welding) techniques. Longitudinal magnetic fields and transverse magnetic fields are used in electric arc welding and surfacing. For the former, induction vector is parallel. For the latter, it is perpendicular to axis of electrode and arc. In this case, it is possible not only to control productivity of electrode melting but also geometric dimensions of rolls in cross section, mix liquid metal in weld pool, refine metal structure and thereby improve service characteristics of parts [1,2,3,4,5,6,7,8,9]. Forced mixing of liquid metal in weld pool occurs when using controlling magnetic fields for submerged arc welding [10,11,12], grinding of structural components of weld metal is often observed [11,12,13]. It has been established that refinement of weld structure during welding with action of magnetic fields occurs during primary crystallization of weld metal [14]. Induction of magnetic fields in bath head part should be within 20…40 mT and frequency of alternating magnetic fields should be within 3…6 Hz [1, 11].
Insufficient knowledge of processes occurring in arc welding with control actions does not allow staff to reasonably choose control tools, to assign optimal parameters of these actions during welding (for example, optimal frequency of magnetic field). In addition, mechanism of weld structure refinement during welding with influence of controlling magnetic fields is not clear.
It is shown that mechanism of weld metal crystallization (accepted in literature on welding and widely covered in educational literature on theory of welding processes) is explained from standpoint of diffusion mechanism. Brief review of such sources is given in [13], mechanism of crystal growth is presented as addition of substance atoms from melt to solid phase (substrate) that is as a diffusion process. But these ideas do not stand up to criticism because rate of crystallization of melt in weld pool during electric arc welding is by 2…3 orders of magnitude higher than rate of diffusion and self-diffusion in molten metals and alloys. The same approach was used in all works that discussed issue of structure refinement of weld metal in arc welding with action of controlling magnetic fields. It should be noted that crystallization of weld metal is similar to crystallization of ingots during processes of casting and metallurgical production. At the same time, cluster mechanism of process of their crystallization is widely used to explain properties of ingots in literature in field of foundry and metallurgical production. It is known that conditions of metal crystallization in weld pool are different from conditions characteristic of ingot crystallization processes. However, there is also significant similarity between processes of crystallization of weld pool and ingots in metallurgical production.
Review of new ideas about mechanism of ingots crystallization in foundry and metallurgical industries is given in works [15, 16]. At present, specialists proceed from model of cluster structure of liquid metals and alloys in all works devoted to consideration of ingots crystallization. There are components similar to crystal known as clusters in metallic liquid. They arise during melting of crystalline bodies (metals and alloys). There is softening zone around clusters, i.e. liquid metal atoms. Volume of softened zone is about 2…5%. This zone is intermediate medium through which atoms from one cluster pass to another. Process of crystallization is presented as process of clusters enlargement that is process of their connection.
However, at present, this approach is not used in relation to processes of electric arc welding and surfacing using controlling magnetic fields. In addition, there are no works that would consider influence of controlling transverse magnetic field on refinement of weld structure in electric arc welding. That is why it is actual to carry out research to establish influence of control magnetic fields on degree of grinding of structural components of weld metal or deposited metal in electric arc welding or surfacing.
2 Materials and Methods. Results
Initially, influence of longitudinal magnetic field on metal structure was studied in electric arc surfacing with submerged arc wire with direct current of reverse polarity. Scheme of device used to create magnetic field is shown on Fig. 1. Cylindrical core pos. 3 is made of ferromagnetic steel. Multi-layered coil pos. 2 is made of insulated copper cable. Device for inputting longitudinal magnetic field is installed concentrically with electrode pos. 1. Lines of magnetic field created by input device are positioned along axis Z.
Outer diameter of core pos. 3 (made from ferromagnetic steel St 45) was 50 mm, and inner hole diameter was 20 mm. Winding (contained 100 turns) was made of four layers of insulated copper wire with diameter of 2 mm.
Electric arc surfacing was performed on plates (30 mm thick) made from steel VMSt3sp with 4 layers without action and with action of longitudinal magnetic field with frequency of 3 Hz to study structure of deposited metal. Surfacing was carried out by wire Np-30HGSA 5 mm in diameter under layer of flux AN-60 as per mode with following parameters surfacing current (direct current of reverse polarity) is from 650 to 680 A, arc voltage is from 34 to 35 V, surfacing speed is 20 m/h. Level of longitudinal magnetic field induction Bz at surface of workpiece (plate) under electrode was from 25 to 30 mT. Surfacing was carried out with preliminary heating of the metal to temperature of 200 ℃. Deposited samples were cut and subjected to metallographic examination.
Crystal structure of the deposited metal 30HGSA is shown on Fig. 2. Crystallization proceeds with formation of columnar dendritic structure when surfacing without magnetic field. Dendrites formed in this case are elongated, boundaries between them are almost straight. Small zone of equiaxed crystals is formed in central part of roll. Primary structure is finer, interdendritic layers are narrower, and central zone of equiaxed crystals is wider (refer to Fig. 2a) in lower layers. Columnar form of crystallization in upper layer is not completely suppressed (refer to Fig. 2b) when surfacing with magnetic field. However, in the first layer crystallization (refer to Fig. 2c) proceeds with formation of fine misoriented and uniform structure over entire cross section of roll, intergranular interlayers are thinner and boundaries are strongly developed. Finer particles of the second phase are released during crystallization and randomly oriented when surfacing with magnetic field.
Series of tests of deposited metal samples for impact strength was carried out. Standard samples with dimensions of 10x10x55 mm with V-shaped groove were used. It has been established that impact strength of deposited metal after surfacing without magnetic field is КCV = 0.16 MJ/m2 and impact strength of deposited metal after surfacing with magnetic field is КCV = 0.20 MJ/m2.
Increase of impact strength is caused by positive effect of magnetic field on structure of deposited metal and type of its destruction. In the first case, crack spread by mechanism of brittle transcrystalline cleavage. In the second case when surfacing with magnetic field, crack spreads by mixed quasi-brittle mechanism, which is associated with presence of large columnar pearlite grains in its structure. Soft ferrite phase forms skeleton and with such structure it does not have significant effect on fracture mechanism. Pearlite grains have shape close to cells (refer to Fig. 3b) and alternate in structure with ferrite grains during surfacing with magnetic field. Crack spreads by mixed (quasi-brittle) mechanism that is transgranular chip and pit-ductile destruction.
Fracture micromechanism (remaining quasi-brittle) qualitatively changes to mixture of dispersed quasi-chip and pitting ductile destruction type (refer to Fig. 3c) in the inner layers of deposited metal where dendritic form of crystallization degenerates and dispersed carbide phase is formed.
Thus, usage of controlling longitudinal magnetic field with frequency of 3 Hz in electric arc surfacing with wire Np-30HGSA under layer of flux AN-60 positively affects structure of deposited metal and increases impact strength of it.
Automatic submerged arc welding under layer of flux Marathon 431 (Bohler) of plates 4 mm thick from steel 12H18N10T with wire Sw-06H19N9T with diameter of 3 mm was performed to establish positive effect of controlling transverse magnetic field on efficiency of grinding structure of weld metal. ADF-1004 automatic machine and rectifier VDU-1202 were used for welding (falling external characteristic of power source was included). Seam welding modes (on reverse polarity) were welding current 280…320 A, arc voltage 30…32 V, welding speed 30 m/h. Transverse magnetic field input device shown on Fig. 4 was used with location of rods across axis of seam.
Device contains two rods pos. 2 made of ferromagnetic steel which are connected by bridge pos. 3. Coils pos. 4 are placed on rods. This device was attached to welding machine through insulator pos. 3. The automatic welding machine allows adjusting distance from rods ends to the surface of plate pos. 5 that is parameter h as well as stick-out distance of the electrode that is parameter H. Electrode wire pos. 1 passes through contact tube of the automatic welding machine pos. 6.
Angle of the rods inclination to axis of the electrode was α = 30…45º, distance was h = 10…15 mm, parameter a was within range a = 40…45 mm. Magnitude of transverse component of magnetic field induction in zone of weld metal was 25…30 mT, value of longitudinal component of induction was insignificant and equal to 2…3 mT with current in windings of 20 A. Alternating magnetic field with frequency of 5 Hz was used during welding. High stability of parameters of welding process mode was observed at magnetic field frequency of 5 Hz. Transverse templates were cut to study microstructure of seams. Then after polishing cross-sections of the samples they were etched via chemical reagent with following composition that is 200 g of HCl with 300 ml of HNO3 with 300 ml of H2O.
Analysis of welds microstructures has shown that effect of transverse magnetic field on arc and liquid metal of weld pool leads to almost twice refinement of weld metal grain (refer to Fig. 5).
Thus, usage of controlling longitudinal magnetic field with frequency of 3 Hz in arc surfacing with Np-30HGSA wire under layer of flux AN-60 positively affects structure and impact strength of deposited metal. Grain of weld metal is almost twice finer when welding butt joint of plates 4 mm thick from steel 12H18N10T with wire Sw-06H19N9T with action of transverse magnetic field with frequency of 5 Hz that should lead to increase of yield strength of weld metal and improve service characteristics of welded joint.
3 Discussion
Performed experimental studies have shown that effect of longitudinal magnetic field during arc surfacing and transverse magnetic field during submerged arc welding of plates from austenitic (non-magnetic) steel confirmed literature data on optimal parameters of controlling magnetic fields for processes of electric arc surfacing and submerged arc welding and it should increase service characteristics of deposited parts or welds.
Calculations performed in works [1, 11, 12] showed that following parameters of alternating magnetic fields are optimal for electric arc welding and surfacing, namely, induction in head part of pool is around 20…40 mT, frequency is equal to 3…6 Hz. Performed experiments confirm literature data on optimal parameters of alternating control longitudinal and transverse magnetic fields. In electric arc welding or surfacing with action of longitudinal or transverse magnetic field induction of these magnetic fields will affect welding arc and liquid metal of weld pool that will lead to refinement of grain of weld metal (deposited metal) and increase service characteristics of welded structures (deposited parts).
Cluster mechanism of castings crystallization is used in foundry and metallurgical production to explain many properties of castings. In this case it is assumed that liquid metal already contains clusters (analogues of crystals, nanostructures, crystallization centers) surrounded by structureless formations of atoms. Process of melts crystallization is presented as addition of smaller crystals to larger crystals [15,16,17,18,19,20].
For process of arc welding and surfacing of metals and alloys it is advisable to proceed from cluster mechanism of metal crystallization in weld pool but it requires additional research.
4 Conclusions
Optimal parameters of alternating magnetic fields have been established on the basis of performed experiments that make it possible to obtain finer structural components in weld metal.
Performed studies have shown that usage of alternating magnetic fields with induction in head part of weld pool with welding wire of 20…40 mT and frequency of 3…6 Hz is optimal for electric arc welding and surfacing.
For the process of arc welding and surfacing of metals and alloys it is advisable to proceed from cluster mechanism of metal crystallization in weld pool.
References
Ahieieva, M.V., Razmyshlyaev, A.D.: About mixing a liquid metal of a welding pool in arc surfacing with a transverse magnetic field effect. Problèmes et perspectives d'introduction de la recherche scientifique innovante. In: Problèmes et perspectives d'introduction de la recherche scientifique innovante. La conférence scientifique et pratique internationale, Brussels, November 2019. Collection de papiers scientifiques «ΛΌГOΣ», vol 2. Plateforme scientifique européenne, Brussels, pp. 56–57 (2019). https://doi.org/10.36074/29.11.2019.v2.05
Mazur, V., Artiukh, V., Matarneh, M.I.: Horizontal force during rolling as indicator of rolling technology and technical conditions of main rolling equipment. Procedia Eng. 165, 1722–1730 (2016). https://doi.org/10.1016/j.proeng.2016.11.915
Boldyrev, A.M., Birzhev, V.A., Martynenko, A.I.: Investigation of influence of alternating axial magnetic field on process of electrode wire fusion. Weld. Prod. 2, 6–8 (2008)
Gharaibeh, N.S., Matarneh, M.I., Artyukh, V.G.: Loading decrease in metallurgical machines. Res. J. Appl. Sci. Eng. Technol. 8(12), 1461–1464 (2014)
Hua, A., Yin, S., Chen, S., et al.: Behavior of arc and drop transfer of mag welding controlled by longitudinal magnetic field. J. Mech. Eng. 46(14), 95–100 (2010)
Marukovich, E.I., Stetsenko, V.Y.: Solidification of metals and alloys. Probl. Solutions Founday Prod. Metall. 3(92), 22–25 (2018)
Radkevich, I.A., Shvab, S.L., Prilutskii, V.P., et al.: Features of arc control by external magnetic field (review). Autom. Weld. Sci. Tech. Sect. 10, 14–17 (2010)
Razmyshlyaev, A.D., Ageeva, M.V.: Primary solidificetion of metal during arc surfacing under the impact of longitudinal magnetic field. Weld. Prod. 3, 9–13 (2020)
Razmyshlyaev, A.D., Ageeva, M.V.: On the mechanism of grinding the structure of the weld metal in arc welding under the influence of magnetic fields (review). Autom. Weld. 3, 29–33 (2018)
Razmyshlyaev, A.D., Ageeva, M.V.: On the cluster mechanism of weld solidification in arc welding with the influence of controlling magnetic fields. Autom. Weld. 1, 1–4 (2019)
Razmyshlyaev, A.D., Delhi, A.A., Mironova, M.V.: Influence of longitudinal magnetic field on the productivity of wire fusion during submerged electric arc surfacing. Autom. Weld. 6, 31–35 (2007)
Razmyshlyaev, A.D., Mironova, M.V., Yarmonov, S.V., et al.: The speed of flows in the pool in arc welding in a transverse magnetic field. Weld. Int. 29(4), 296–300 (2015)
Razmyshlyaev, A.D., Yarmonov, S.V., Vydmysh, P.A., et al.: Modeling the transverse magnetic field generated by equipment in arc welding. Weld. Int. 30(6), 463–466 (2016)
Razmyshlyaev, A.D., Vydmysh, P.A., Ageeva, M.V.: Automatic Submerged Arc Welding with the Influence of External Magnetic Field, p. 245. Priazovsky State Technical University, Mariupol (2017)
Razmyshlyaev, A.D., Ahieieva, M.V.: Features of metal crystallization in arc surfacing and welding with a longitudinal magnetic field action. Collection of Scientific Papers ΛΌГOΣ 21–22 (2020). https://doi.org/10.36074/24.04.2020.v2.07
Razmyshlyaev, A.D., Ahieieva, M.V.: TMF Influence on weld structure at the welding of 12X18H9T. Mater. Sci. Forum 927, 1–5 (2018)
Razmyshlyaev, A.D., Ahieieva, M.V.: Optimal parameters of longitudinal magnetic field that provide mixing of molten metal in a weld pool during electric arc surfacing. Tech. Sci. Technol. 2(16), 7 (2019)
Razmyshlyaev, A.D., Mironova, M.V.: Efficiency of the process of penetration of the parent metal in submerged-arc surfacing. Weld. Int. 26(11), 862–866 (2019)
Al-Quran, F.M.F., Matarneh, M.E., Artukh, V.G.: Choice of elastomeric material for buffer devices of metallurgical equipment. Res. J. Appl. Sci. Eng. Technol. 4(11), 1585–1589 (2012)
Yin X., Gou J., Ma, N.: Numerical simulation of arc and weld pool for GTAW in external axial magnetic fields. Trans. JWRI Spec. Issue WSE. 17–27 (2011)
Author information
Authors and Affiliations
Corresponding author
Editor information
Editors and Affiliations
Rights and permissions
Copyright information
© 2023 The Author(s), under exclusive license to Springer Nature Switzerland AG
About this paper
Cite this paper
Matarneh, M.E., Artiukh, V. (2023). Influence of Controlling Magnetic Fields on Metal Structure at Electric Arc Welding and Surfacing. In: Beskopylny, A., Shamtsyan, M., Artiukh, V. (eds) XV International Scientific Conference “INTERAGROMASH 2022”. INTERAGROMASH 2022. Lecture Notes in Networks and Systems, vol 574. Springer, Cham. https://doi.org/10.1007/978-3-031-21432-5_296
Download citation
DOI: https://doi.org/10.1007/978-3-031-21432-5_296
Published:
Publisher Name: Springer, Cham
Print ISBN: 978-3-031-21431-8
Online ISBN: 978-3-031-21432-5
eBook Packages: EngineeringEngineering (R0)