Abstract
The cost of low sulfur calcined petroleum coke (LS-CPC) is higher than that of high sulfur (HS-CPC). The trend of increasing CPC cost has been significant in recent years and has independent from metal prices. Since 2004, INALUM has tried to determine the proper blending formula between HS-CPC and LS-CPC to improve production costs, as well as anode performance without disturbing plant operation. INALUM has used various blending ratios for the two types of coke, i.e. 60/40, 85/15 as well as 100/0. The increased presence of sulfur does influence anode quality but through well-managed granulometry and recipe, anode quality is still maintained. By utilizing the 85/15 ratio in coke blending, INALUM has successfully reduced anode production costs by approximately 7%.
Access provided by Autonomous University of Puebla. Download conference paper PDF
Similar content being viewed by others
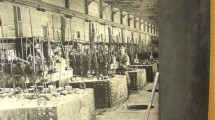
Keywords
Introduction
It is well known that in the Hall–Héroult process that anode quality widely depends on the raw material, which is calcined petroleum coke. In order to classify petroleum coke in anode production, sulfur is used for characterization and becomes the reference for anode production. Sulfur originates as sulfur in the anode carbon plus some sulfur contained in the alumina and in the aluminium fluoride [1]. It has been well documented that the sulfur content in the crude oil that produces petroleum coke tends to increase day by day due to economic reasons in the refining industry and it affects the sulfur presence on the anodes, which will in turn affect air permeability and reactivity. Moreover, the effect caused by the increased presence of sulfur in the anode will influence reduction cell performance including current efficiency and DC power consumption.
Organic sulfur may exist in the coke in many forms, such as thiophenes attached to the aromatic carbon skeleton, as well as attached to side chains of aromatic or naphthenic molecules. Inorganic sulfur compounds are mostly found on the coke surface or in coke pores bounded by capillary condensation, adsorption, or chemisorption. Separation of sulfur can be achieved by calcination at higher temperatures, hydrodesulphurization, or through chemical treatment with different agents.
As the petroleum industry processes crudes of increasing sulfur and trace element content, the industry consensus is that there is an overall quality deterioration. This, combined with increasing pressure for the protection of the environment, requires the development of low-grade petroleum processing technology and the effective removal of sulfur and its trace elements is imperative. In order to maintain anode quality, calcined petroleum coke with higher sulfur contents are usually blended with cokes that contain less sulfur.
Desulfurization Process
Sulfur is released during the baking process of a green anode. This process is known as desulfurization process and its occurrence depends on the peak flue gas temperature. As explained previously, petroleum crudes are getting sour, hence producing a pet coke that has more sulfur and a higher content of metallic impurities. The degree of coke desulfurization and destabilization of carbon to sulfur bonds depends on the level of calcination and the residence time of coke in kiln. The destabilized bonds between carbon and sulfur in CPC are prone to break during the anode baking process thus leading to further desulfurization [2]. According to previous findings for the different sulfur content of petroleum coke calcined at 1100 °C or below, the largest desulfurization rate of petroleum coke is less than 20% and 80% of the sulfur remains in the baked anode [3]. If thermal desulfurization is the objective then it must meet several criteria (specific heating rate, maximum temperature, and residence time) without affecting coke quality [4].
Effect of Sulfur
Currently, a typical specification for sulfur content in CPC used in producing carbon anode is up to 3% and projections may reach 4.5% [5]. The aluminium industry uses blends of high and low sulfur CPC in an effort to balance between minimum production cost while expecting to obtain a suitable sulfur level to produce good anode quality. In the market, LS-CPC has become more expensive and it also becomes one of the many challenges faced by the global aluminium industry.
Too high sulfur contents in a carbon anode negatively impacts the performance of reduction cell. The current efficiency will decrease due to increasing of sulfur content in the carbon anode. Other factors that cause the decreasing current efficiency is due to the increased porosity in the higher sulfur anode caused by desulfurization; increased porosity increases carbon dusting, which decreases current efficiency amongst other things. SOx emissions in the baking plant and reduction cell typically increased (if not mitigated) when consuming higher sulfur cokes. Any positive effects of sulfur seem to be much less pronounced. The positive effect of sulfur for anodes in using butts is usually attributed to sulfur neutralizing the negative effect of sodium present in the anode butt [1].
Pilot-Scale/Laboratory Test
Raw Material Preparation
High and low sulfur cokes are selected for the test as shown in Table 1. Coal Tar Pitch (CTP) for this test is shown in Table 2. The selected material are standard raw materials used at INALUM.
After a material analysis was performed, a range of anode blends was selected for the test. As part of the test, the only independent variable was the CPC. Since the sulfur contribution of CTP and anodes butts remains are kept constant (in this test), those contributions are therefore not considered as independent variable although sulfur content in CTP and anode butt were included in the estimation of the sulfur content in the baked pilot anodes as shown in Table 3.
Raw materials used to produce the anodes were prepared using INALUM standards. The materials were divided into particle size fractions coarse-1, coarse-2, medium, and fine. All particle sizes were prepared by using a sieve shaker and a planetary mill to prepare the material composition with a high degree of precision in order to avoid segregation during distribution particle in mechanical conveyors. The pilot test equipment used consisted of a mini kneader, mini shaking table, and mini anode mould to produce mini anode (14 cm × 9 cm × 10 cm) with weight is 2 kg. For each coke recipe, 10 anode samples were produced with total 30 pieces. All anodes were simultaneously placed on the top layer of the anode baking furnace at the baking plant. The aim was to equalize the heat and temperature distribution in the furnace that is caused by the top layer closer to fire burner. A total of 30 test anodes used for electrical resistivity, but half for CO2, air reactivity and air permeability due to limitation number of sample as well as working time.
Pilot Test Result
Desulfurization
Remaining material after analysis anode core of each anode type were analyzed to evaluate desulfurization during baking. In INALUM’s case, a closed top furnace is used for operation and we only have the temperature of flue gas in the top section available. Temperature of flue gas during baking process noted by 1235 °C and the soaking time is 72 h. Our experience from a couple years ago is that flue gas temperatures may be 1250 °C, but actual anode temperature are not always the same in the top, middle, and bottom layers. The top layer anodes temperature is around 1100–1150 °C, while the middle and lower layers have lower temperatures around 1050–1100 °C [6]. The results from our analysis presented in Table 4 indicates that more sulfur content in green anode leads to higher levels of desulfurization.
The green anode %S is the same as Table 3 (theoretically calculation) and the baked anode was measured by X-ray fluorescence. Baked anode was only from one test per coke recipe.
Residual Reactivity
Referring to the test analysis, higher sulphur cokes lead to better CO2 Residual Reactivity (RRCO2) and lower Air Residual Reactivity (RRO2). The sulfur will inhibit the migration to the surface and subsequently produce a loss of sodium by the formation of stable sodium-sulfur species [7].
CO2 reactivity of baked anode material is linked to the most important impurities, namely Calcium, Sodium, and Sulfur. This description is explained in equation below [7]:
where RCO2 = Carboxy reactivity (%) calculated for a known purity.
Figure 1 shows higher sulfur coke prebaked anode RRCO2 was higher than lower Sulfur. According to the equation, residual reactivity resulting from pilot test is in line with the literature that states that sulfur will increase RRCO2 due to sulfur serving as an inhibitor for other impurities that serve as catalyst. This would be beneficial for a prebaked anode in order to decrease carbon dust in a reduction cell. On the other hand, Fig. 1 indicates that high sulfur has no advantage in terms of RRO2, which was lower than high sulfur. With regards to Table 1, the content of trace elements in high sulfur coke, especially metal elements (Ni, Fe, Si), were slightly lower than low sulfur coke. The contribution of high sulfur to air reactivity is not yet well known, and if we refer to the metal element content in low sulfur and high sulfur as provided on Table 1, prebaked anodes with lower sulfur ratio should have lower RRO2 because metal elements such as nickel and iron are more present in low sulfur. Both elements could drive change of amphoteric reaction to form metal-superoxo. Nevertheless, lower RRO2 was observed when using higher sulfur ratios in prebaked anode. Higher vanadium content in higher sulfur coke may play a role in lowering RRO2. According to Lossius et al. [8] higher vandium levels will increase desulfurization rate and at lower temperature to create significant desulfurization. It can be assumed to be a result of high desulfurization rates, which leads to increased anode porosity and increased surface area that accelerates the reaction rate. Refer to analysis of variance, P-value RRCO2 is 0.013 and RRO2 is 0.000 that is smaller than 0.05 that indicates the analyst rejects null hypothesis or there is significant variance of anode ratio 60/40, 85/15, and 100/0.
Specific Electrical Resistance (SER)
As depicted on Fig. 2, specific electrical resistance of the anode ratio 85/15 and 100/0 are higher than the anode ratio 60/40. The level of resistance obtained may be related to the final baking temperature. In normal practice, increasing resistivities increase the anode voltage drop and DC power consumption. Refer to analysis of variance, P-value SER is 0.136 bigger than 0.05 that indicates the analyst accept null hypothesis or there is no significant variance of anode ratio 60/40, 85/15, and 100/0.
Air Permeability (AP)
As depicted on Fig. 3, air permeability is increased by higher sulfur content. This was caused by increasing desulfurization during the baking process, thus increased air permeability. Any loss of sulfur from the anode structure creates an additional surface area, thereby creating more air permeability. It then helps CO2 react with a larger number of anode carbon. Refer to the analysis of variance, P-value AP is 0.006 smaller than 0.05 that indicates the analyst rejects null hypothesis or there is significant variance of anode ratio 60/40, 85/15, and 100/0.
Net Carbon Consumption
All properties, both mechanical and chemical, will ultimately contribute to carbon consumption in anodes. In order to determine the best anode, it will be considered/analyzed by estimated net anode consumption below equation [9]:
where
NC: Net Anode Consumption.
C: Cell Factor.
CE: Current Efficiency.
BT: Bath Temperature.
CRR: CO2 Residual Reactivity
ARR: O2 Residual Reactivity
AP: Air Permeability
TC: Thermal Conductivity.
Assuming the variables associated with reduction cell parameters such as cell factor, current efficiency, and bath temperature are constant hence from the equation is obtained estimated net anode consumption as depicted on Fig. 4. According to Fig. 4, the trend that is observed shows that the Sulfur content influences anode consumption. A parameter that plays a role in increasing anode consumption is the increased air permeability. Higher sulfur creates more porosity in the anode caused by increased desulfurization rate during baking process.
Test in Reduction Cell
In order to verify the anode performance impact from a higher sulfur ratio in coke blending, a test in the reduction cell was undertaken (Table 5)
Test was performed in two separate blocks, the first block was set up as cell reference, which consumed full of anode 60/40. The other block was set up as pots test consisting of 11 pots consumed anode 85/15 and 11 other cells consumed anode 100/0.
Raw Material
Consumed raw material during the application test in reduction cell is in line with the pilot test as described on Tables 1 and 2 (Table 6).
Anode Quality
All anode key properties fulfill the standard overall though air permeability was not in accordance with literature reported that higher sulfur will make higher air permeability. The anode residual reactivity, as shown in Table 9, provides a satisfactory result considering that a higher sulfur content does influence residual reactivity as shown on chart 1. However, any deviation between the anode quality in the pilot test and the test in reduction cell may be disputed due to a high variability process control (such as ball mill speed is not always the same every time and certainly depends on particle size of ball mill feed, weight of anode, position of anode in baking furnace) during production of anodes in the industrial plant, and those parameters become larger variability during this test. As explained in Table 10 that variability in industrial test is of wide range and temperature of flue gas in baking plant was varied because all anodes were spread out across all layers in section and pit. Meantime, temperature of flue gas for each layer is different and thermocouples in middle and bottom layers were not yet installed. Besides, anode temperature cannot be obtained because there are no facilities installed to measure this. However, our experience is anode temperature was definitely different in every layer [6]. Therefore, the only data available is the temperature of flue gas in top layer.
Based on this, the pilot test results can be used as a reference for demonstrating the influence of the sulfur content causes in the pilot test that was conducted with intensity in order to maintain a degree of variability in the process (Table 7).
Reduction Cell Performance
See Table 8.
According to Stanislaw Pietrzyk [1], the increase in anode sulfur content leads to a decrease in Current Efficiency (CE) and the correlation between CE in relation to the sulfur content are
Sulfur content also has a negative effect on gas generated on electrochemical reactivity expressed as carbon consumption. Increasing sulfur leads to increasing Boudouard reaction which produces CO, while an electrochemical reaction produces CO2 with sulfur mainly bound as COS. Both generated gases may be expected and most importantly drive DC power consumption. However, independent checks on the application tests in the reduction cell are not possibly due to various variables influencing CE and DC Consumption.
Table 11 shows that either DC consumption or CE are getting higher and lower, respectively, while using higher Sulfur cokes (linearly correlation) as well as a potential for energy loss due to the increase in sulfur content.
Anode Performance
See Table 9.
Carbon dust was quantified based on the total weight of carbon dust generating from carbon dust discharged from process in a certain period and divided by the total of aluminium production during in same period. The same thing was also performed in broken anode condition where the broken anode parts had fallen down into reduction cells was recovered, weighed, and quantified.
SO 2 Generation
Due to the presence higher sulfur in CPC, the effect of desulfurization in the anode baking plant and reduction plant was monitored as potential risk. It can result in higher SO2 concentrations thus polluting the environment. The threshold limit for gas emissions follows the Ministry of Environment regulation (Table 10).
The sampling was executed in exhaust gas cleaning facilities at the blower fan (equipment which distribute from wet scrubber into Gas Stack). Each bake furnace has one ring main which allows the flow of gas into the wet scrubber. Based on Table 10, desulfurization effects during baking anode were examined and the results exhibit no concerns about polluting environment cause SO2 far below threshold value. At the baking furnace, it is not possible to use only for certain anode test because in the same time the existing anode (outside anode test) must be produced to fulfill other reduction cells. Due to this condition, the baking furnace was also used to produce baked anode for existing requirement at the same time and therefore the trends of SO2 emission did not line up with the sulfur content of the test anodes.
Sampling was executed on gas duct of respective sampling pot cell. All pots are still below threshold value which means no concerns about polluting environment due to higher sulfur content on cokes Table 11.
Economical Analysis
Based on the test results, it was identified that there is a potential to reduce anode production costs by 15 USD/tonne Al with coke blends 85/15, or in other words, 7% reduction of anode production costs. If the aluminium production is 250 ktpy, total potential cost savings will be around USD 3,750,000/year. Nevertheless, it needs to compensate or doing more effort to avoid metal losses due to decreasing of CE which is caused by higher sulfur level. Refer to test result, there will be 10,400 tonne of metal lost each year and if assumed net profit margin around 100 USD/tonne this adds up to a total opportunity loss of USD 1,040,000 per year.
Conclusion
The effects of sulfur level in the prebaked anode can be divided into positive and negative aspects. The sulfur content in the anode demonstrates that the residual reactivity of anode (RRO2 and RRCO2) is strongly influenced by the sulfur content. The increase of sulfur will increase RRCO2 but it is inversely proportional to RRO2 where there is a decrease if the sulfur content increases in the anode. Moreover, prebaked anodes with a higher sulfur content have a higher air permeability, which is caused by a higher desulfurization rate, which creates porosity during the sulfur removal process at the bake plant. The higher air permeability will impact anode consumption in the reduction cell. Meanwhile, the effects of increased sulfur content in the anode leads to increased DC Consumption and decreasing CE in the reduction cell. Through the improvement of coke blending ratio, INALUM has successfully reduced anode production costs by approximately 7% by using the ratio 85/15.
References
S. Pietrzyk and J. Thonstad (2012) Influence of The Sulphur Content in The Carbon Anodes in Aluminium Electrolysis – A Laboratory Study. Light Metals 2012. The Minerals, Metals & Materials Society, p 659–664.
K. Khaji and M. Al Qassemi (2016) The Role of Anode Manufacturing Processes in Net Carbon Consumption. Metals 2016, 6, 128; doi:https://doi.org/10.3390/met6060128.
Shoulei Gao, et.al. (2018) Study on the Property and Desulfurization Mechanisms of Petroleum Cokes with Different Sulfur Contents from 1200 to 2800 °C. Light Metals 2018. The Minerals, Metals & Materials Society, Springer, p 1303–1313.
S.L. Kilic (2016) Experimental Study of the Combined Calcination and Hydrodesulfurization of High-Sulfur Green Petroleum Coke. thesis, University of Quebec.
J. Baker, et al (2010) Quality Analysis of Petroleum Cokes and Coals for Export Specifications Required in Use of Specialty Products and Utility Fuels.
S.S. Sijabat, et al (2019) The Optimization of Soaking Time to Reduce Fuel Consumption while Keeping Good Baked Anode Quality. Light Metals 2019. The Minerals, Metals & Materials Society, Springer; p 1275–1280.
Sheralyn M. Hume (1999) Anode Properties: Influence of Raw Material Properties. 2nd Edition 1999. R&D Carbon Ltd, Switzerland.
L.P. Lossius, et al (2008) Coke and Anode Desulfurization Studies. Light Metals 2008. The Minerals, Metals, & Material Society, p 881–886.
Liu Fengqin (2000) Chinese Raw Materials for Anode Manufacturing. R&D Carbon Ltd, Switzerland.
S. Birghila and I.C.Popovici (2013) Evaluation of the Physical-Chemical Properties in Petroleum Coke. Advances in Petroleum Exploration and Development Vol.6, No.2, 2013, pp. 28–31. doi: https://doi.org/10.3968/.aped.1925543820130602.1758.
Hai-Tao Jiang, et al. (2018) Effects of High-Sulfur Coke on Physicochemical Properties of Prebaked Anodes in Aluminium Electrolysis. Light Metals 2018. The Minerals, Metals & Materials Society, Springer, p 1197–1202.
Muniyandi Sankaralingman, et al. (2018) Amphoteric Reactivity of Metal-Oxygen Complexes in Oxidation Reactions. Coordination Chemistry Reviews 365, 2018, p 41–59. doi:https://doi.org/10.1016/j.ccr.2018.03.003.
Author information
Authors and Affiliations
Corresponding author
Editor information
Editors and Affiliations
Rights and permissions
Copyright information
© 2022 The Minerals, Metals & Materials Society
About this paper
Cite this paper
Sinaga, D.A., Harahap, R., Mugiono, E., Ammar, E.E., Sodikin, A.R. (2022). Higher CPC High Sulfur in Coke Blending Ratio to Optimize Production Cost Without Lowering Standard Anode Quality. In: Eskin, D. (eds) Light Metals 2022. The Minerals, Metals & Materials Series. Springer, Cham. https://doi.org/10.1007/978-3-030-92529-1_109
Download citation
DOI: https://doi.org/10.1007/978-3-030-92529-1_109
Published:
Publisher Name: Springer, Cham
Print ISBN: 978-3-030-92528-4
Online ISBN: 978-3-030-92529-1
eBook Packages: Chemistry and Materials ScienceChemistry and Material Science (R0)